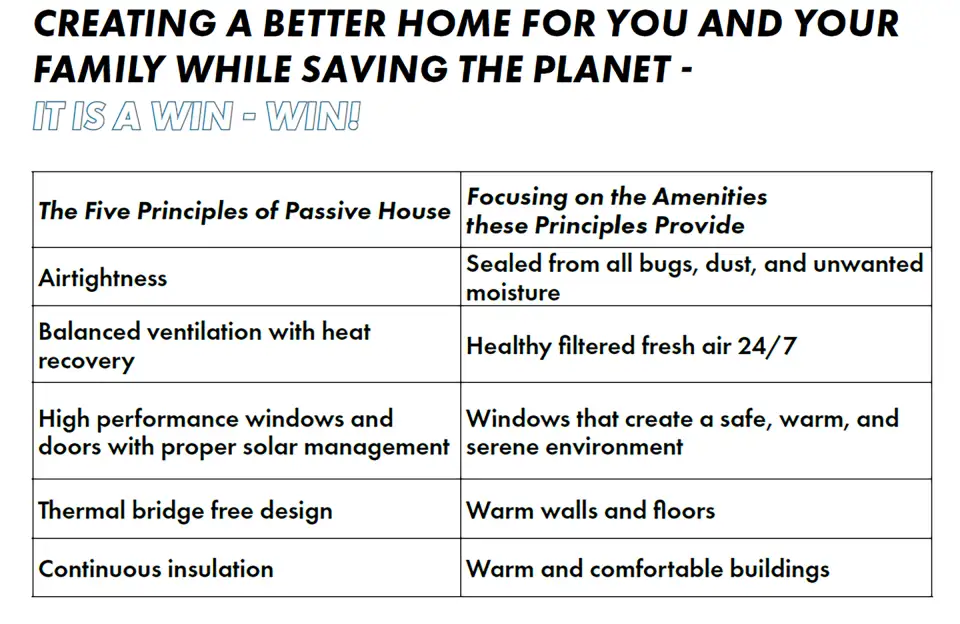
Often, the largest hurdle to embarking on your first Passive House is knowing where to start.
The answers to the question of “Why should I build a Passive House?” seem obvious once you hear them: Passive Houses are simply better, healthier buildings. High-performance envelopes and ventilation strategies that lower the energy demand of a building lead to low-usage, well-sealed buildings. These same strategies provide building occupants with a host of benefits, including quiet, temperate, comfortable, and healthy indoor environments with filtered, fresh air 24/7. Thoughtful design and construction of building envelopes increase building longevity. Lower mechanical loads lead to smaller mechanical systems, and insulation plus high-performing windows and doors mean that heating strategies do not need to focus on the outer perimeter of the building. High-performance building envelopes free the designer to include dramatic expanses of glass and other design elements that would not otherwise be possible.
This all sounds, and is, great, but the question remains: How do you embark on a Passive House project in a way that maximizes your chances of success, client satisfaction, and certification? Over the last decade, Baxt Ingui Architects has honed a repeatable, systematic approach to Passive House design and building. I recently contacted more than 20 people that I admire in the Passive House community to see what they felt were the most important ten steps to creating a first Passive House. I was not surprised with the in-depth and incredibly open responses I received, because the Passive House and high-performance building community is known to openly share their knowledge. Here they are.
Tip 1: Get the client on board.
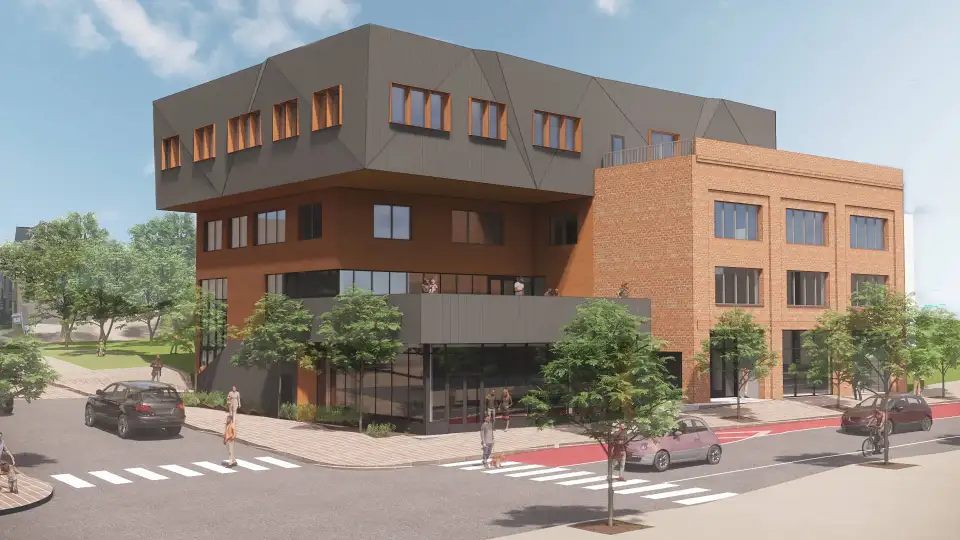
Passive House is a game changer for affordable housing due to its tremendous economic and health benefits. It is also a competitive advantage for anyone building market rate, residential, or commercial projects. Derrick L. Tillman, Bridging the Gap LLC
Clients always want a better building. Focusing on the amenities of a Passive House building rather than the energy savings and building performance is essential. Focusing on how it will benefit them once they occupy the space, instead of describing in detail how you achieve these results, is essential. Otherwise, you may be saying important words, but clients may only hear that they will be missing out on something or are sacrificing for the greater good, when in fact they are getting more. They are having their cake and eating it too.
Baxt Ingui does a lot of historic masonry retrofits in New York City. During initial walkthroughs with potential clients, I inform them that, should we build a Passive House, we could create a relatively bug-free building, safe from outside air infiltration. If they want fresh filtered air 24/7, we should do a Passive House. If they want incredibly secure windows and doors that remove most of the street noise, we can use Passive House products. Often, I do not even have a chance to mention that they may never need to heat their home and that cooling can be significantly reduced, or the significant energy cost savings and benefits to the environment as a whole. As we continue our initial walk through of the houses and discuss bedrooms and bathrooms, I am often interrupted with questions about how we achieve the amenities of a Passive House—it sticks with them—and they are hooked. Clients want good buildings. They just did not know there was an option for something better, and once they do, they cannot unlearn it. They want a Passive House.
For multi-family developers and building owners, Passive House can make a significant difference to the bottom line—both in selling these amenities or in significantly reducing their operating costs once the building is occupied. There are very few things that can do this.
Tip 2: Involve Passive House consultants and certifying bodies early. Use them as a tool to create better designs that meet Passive House standards.
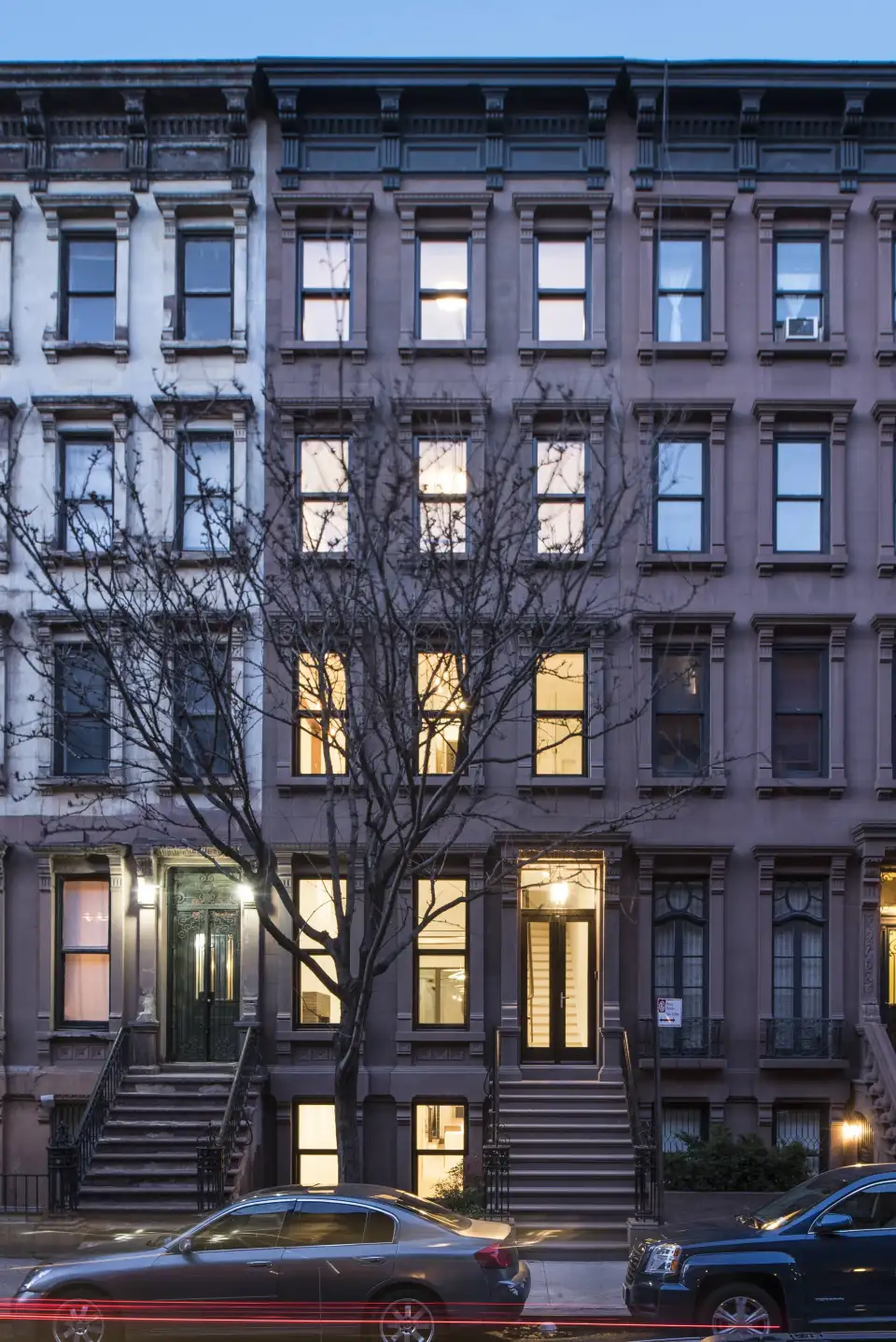
Detail early in the process. This is especially key if any sub (or designer) is a first timer. Marc Fabris, Baxt Ingui Architects
We have found that bringing on the Passive House consultant early in the process helps to de-risk our design and specification process. They can run the buildings through programs such as WUFI or PHPP, removing a lot of the guesswork. In schematic design and design development, this early involvement ensures that we consider key factors like orientation and are not forced to go backwards. In the construction drawing and specification phase, it ensures we put the right insulation where needed, consider all of the potential thermal bridges, and specify shading and correct windows. Passive House is simply better for building and detailing.
Tip 3: Involve the contractor as early as possible, and make sure that they have Passive House tradesperson training.
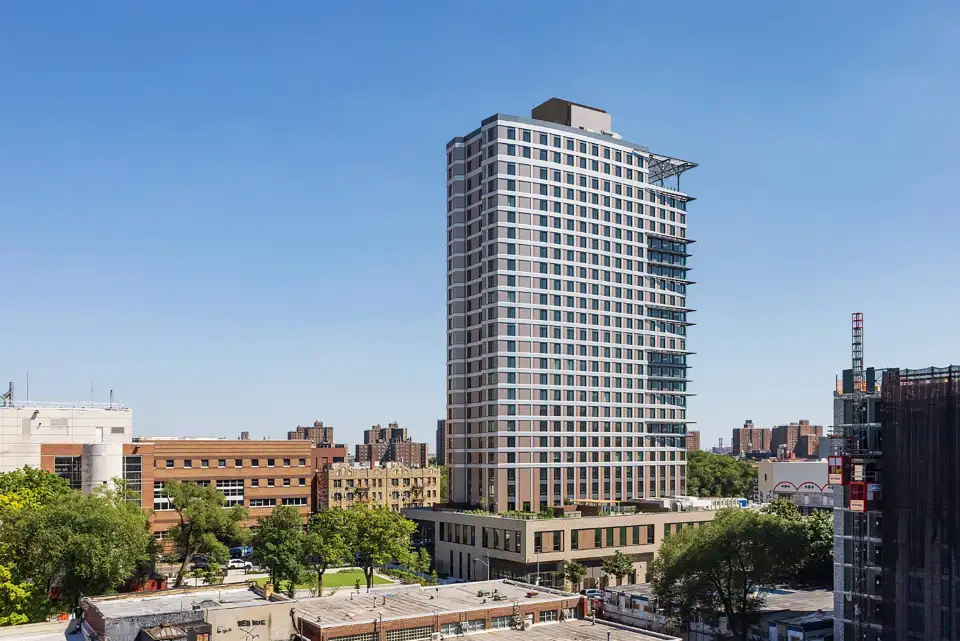
Getting a builder on board early can be very beneficial. Vet details for efficiency and cost considerations prior to final bid docs being prepared. Evaluate construction sequencing with a primary focus on air barrier and insulation continuity. John Woelfling, Dattner Architects
Bringing on the contractor as early as possible allows you to detail and design the way your contractor prefers to build. Their years of experience are essential to the detailing and specification process, and as with the Passive House consultant, early communication with your contractor prevents you from having to go backwards. You can also design towards the builder’s preferences with regards to materials and sequencing. People are more excited to be a part of something they helped create. This is not exclusive to Passive Houses; our best projects were those where the atmosphere was collaborative.
Tip 4: Create air sealing, mechanical, ventilation, and hot water strategies. Clearly identify these strategies in your construction documents.
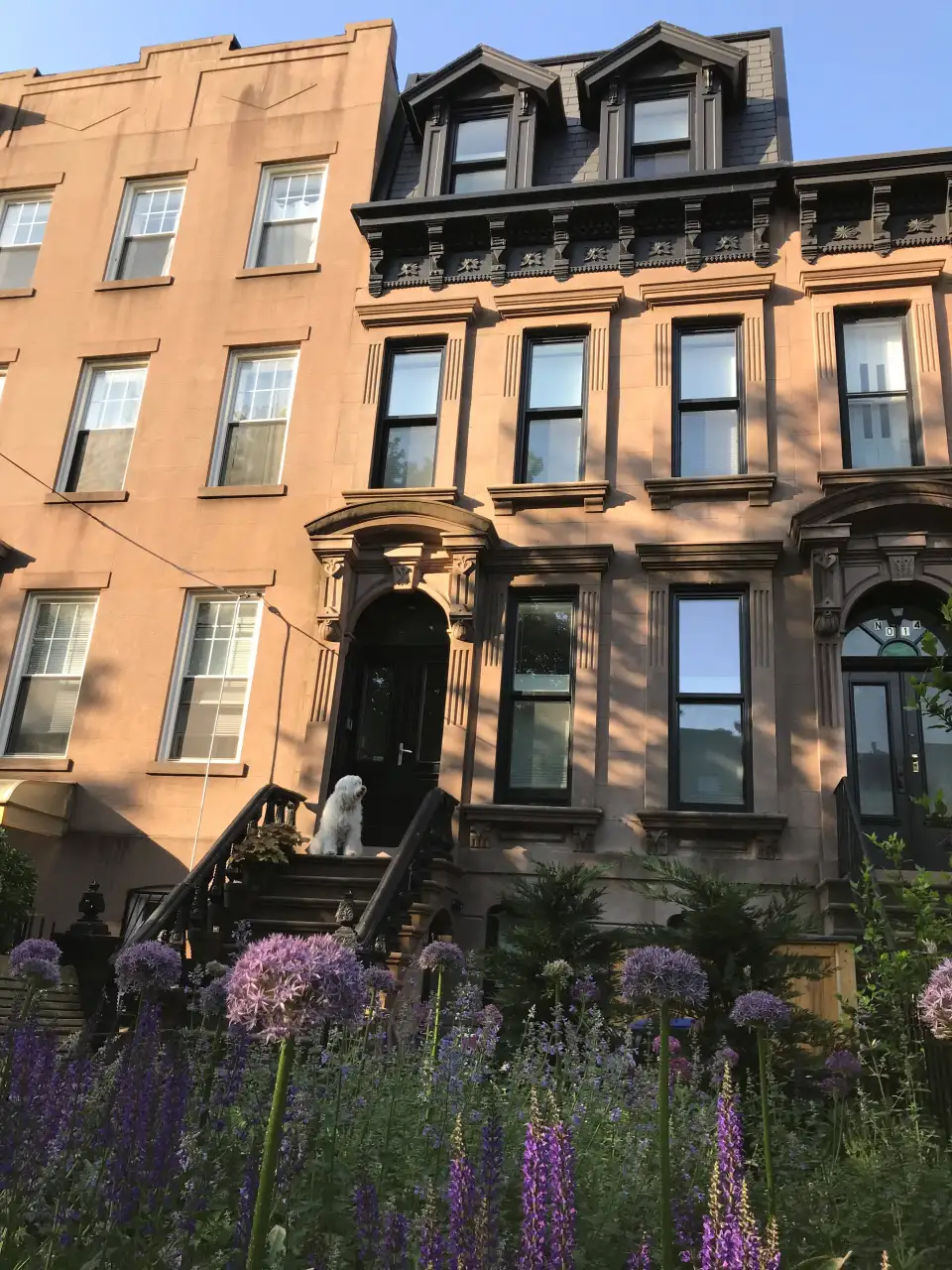
It helps to use one brand or system for air sealing. The cross compatibility between products (tapes to different membranes, different materials, etc.) is much easier, and the technical support from the manufacturer is invaluable. This is especially useful when retrofitting an existing building as opposed to new construction. Max Michel, M2 Finishworks
Start with ventilation. Everyone screws up ventilation. Figure it out early. Passive House requires more drawings. Be prepared for that. Include mechanical systems in design and conversations with clients early. Ed May and John Mitchell, bldgtyp
Plan for mechanicals EARLY: heat pumps, ERVs, range hoods and makeup air, dehumidifiers, humidifiers, water heaters, laundry, and all the associated ductwork, piping, etc. Do a proper heating and load calculation. Cramer Silkworth, Baukraft Engineering
Craig Stevenson, president at the Auros Group, once gave a talk where he described starting by determining how your clients will use their building or home, so that you get it right in design. This, again, is not exclusive to Passive House design, but it is a fantastic tip #4. How cold do they like it; how many thermostats do they want to see; do they want to have remote access; how many take showers at the same time and for what duration; how often do they cook? These are just some of the questions you can ask your client at the beginning of a project to ensure that they are happy at the end.
Sharing client preferences via clear specifications with descriptions, diagrams, planned mechanical and ventilation routes, or any other way that allows the entire team to be successful is essential.
Tip 5: Create a clear drawing and specifications package.
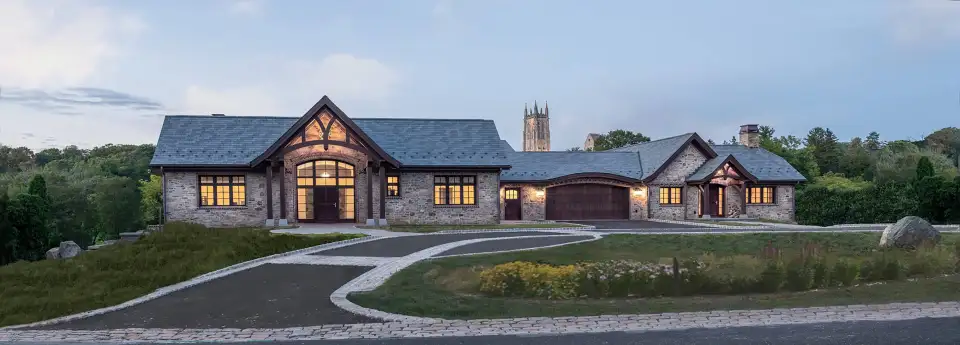
Pay close attention to window design, orientation, sizes, and especially the control of solar radiation and ability to naturally cool the building. Get it right, and your HVAC system can be much smaller and less expensive. Get it wrong, and your mechanical system is more expensive, as is your envelope, and the overall building cost will be much higher than a ‘conventional’ building. Stuart Hood, Introba
Verify structural strategies, thermal bridge-free connections. Define materials performance: air, water, vapor, fire, toxicity, compatibility, origin, and longevity. Create a base energy model; iterate design options and ballpark energy use. Set a renewable energy strategy, including ballpark ROI and load shifting strategy. Set envelope and systems strategy, including decoupling systems from the envelope. Shannon Pendleton, Sanderson Sustainable Design
Completing a red line air sealing diagram, a ventilation diagram showing routes, and a mechanical diagram showing unit locations with filters and equipment that are truly accessible are essential. The same is true for detailed building sections showing the structure, waterproofing, thermal bridge, and other solutions, shading, and more. The better your drawing and specification package is, the better chances you have identifying conflicts before a hammer is even swung. Sharing the package with the entire build team can foster suggestions and substitutions even before final pricing, allowing for a smoother project both physically and financially.
The Reimagine Buildings Collective brings together building professionals stepping up to tackle climate change.
No project is perfect, and there are often physical or financial limitations. Pre-planning and proper detailing ensure that everyone understands and agrees with the final game plan. Sometimes, you cannot get everything you want or need—you must make sure your client is aware of and on board with this. At the end of the day, it is their building and must be their decision.
Tip 6: Hold a kick-off meeting with your Passive House contractor and the entire crew.
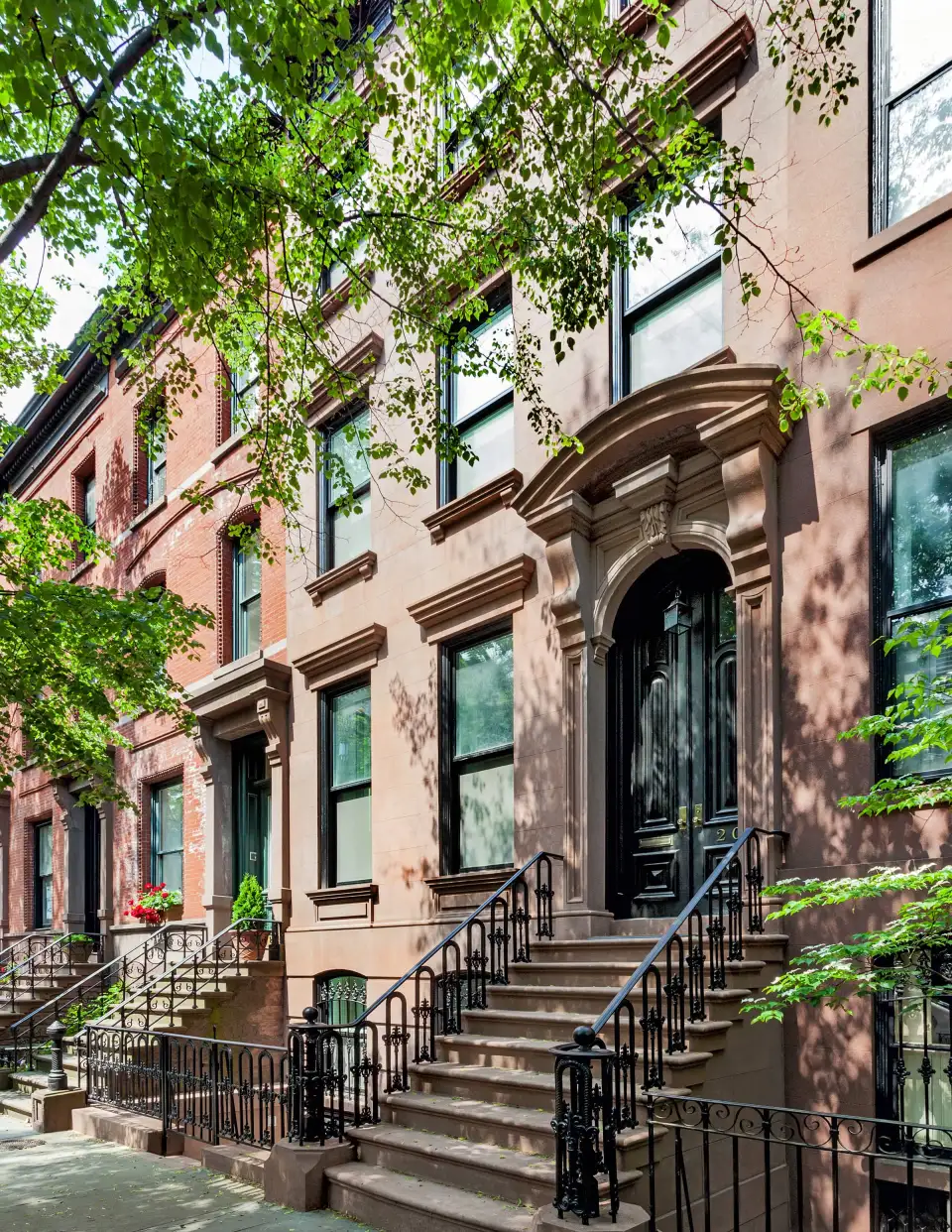
If it is the first Passive House for an architect or contractor, it is important to set up a kick-off meeting with everybody there, including subcontractors. It is more important to stress that it is not a complicated process, but everybody has to understand that it is a collective effort. Eoin Killeen, Kleen Construction
I am often asked how we find Passive House certified contractors. Often, the answer is that we do not—we make them. We love the contractors we have worked with over the years, and any contractor with a love of building and skilled builders is perfect for Passive House. We ask that the person who will be on site all day take a Passive House builders training course prior to construction, and that they hold a kick-off meeting for the entire crew.
One of my favorite things about high-performance and Passive House building design is the new details and techniques our contractors teach us, which have changed the way I think about design and building. That same feeling can be seen on the faces of the builders and subcontractors at the kick-off meetings. This level of knowledge and teamwork is essential.
Tip 7: Hold weekly meetings with the team.
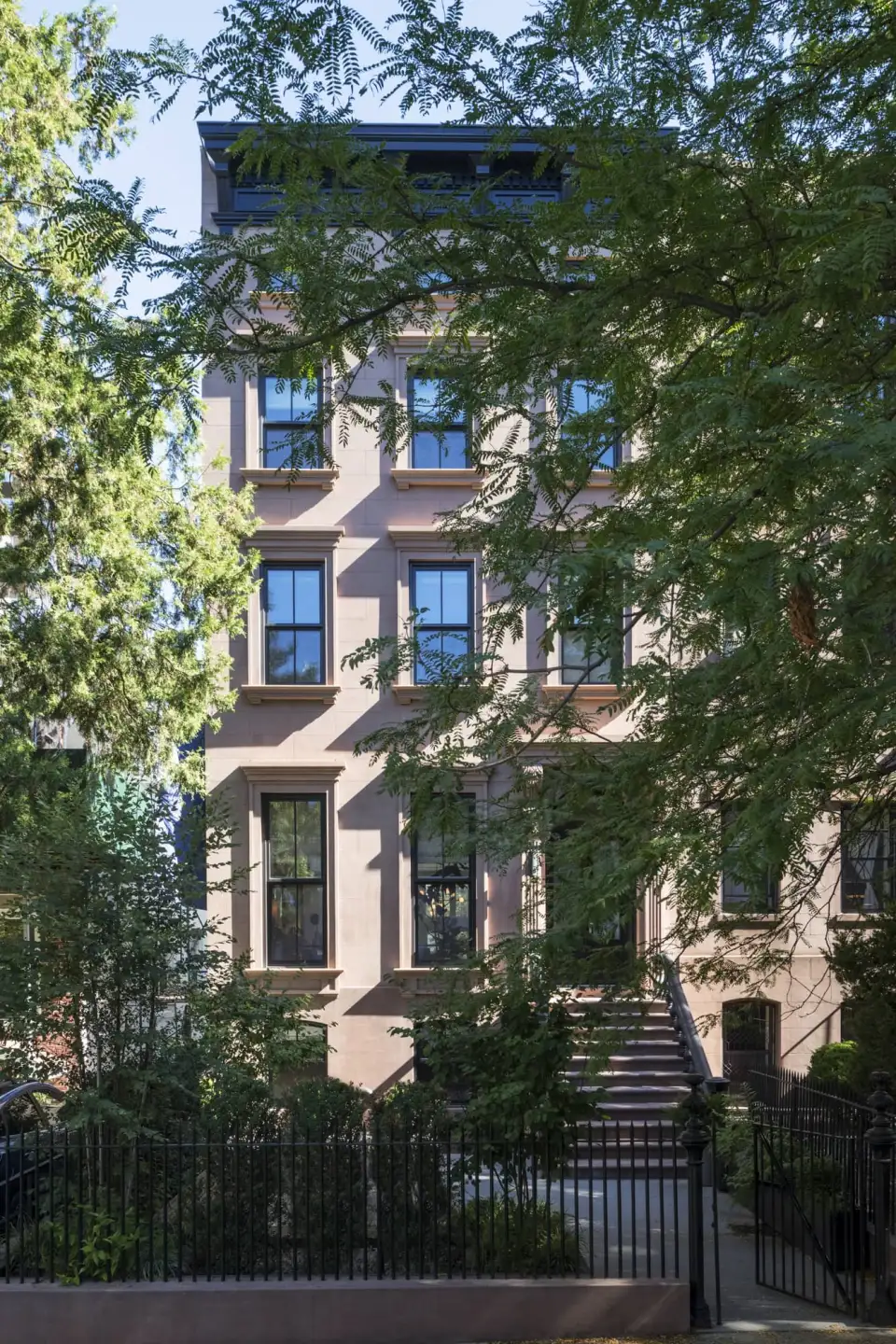
The importance of a weekly site meeting with owner, architect, and contractor cannot be understated—for all projects, not just Passive Houses. This allows the owner to see the house coming together and digest the intricacies involved in the envelope and systems firsthand, and review in real time. The contractor can review aspects of construction they are either currently working on or will be soon. For the architect, the cadence of the meetings allows them to prioritize critical path items effectively and maintain a consistent line of communication with the builder. It also helps to set up a level of accountability for all three, so as a team you are working to meet milestones and keep the project moving forward. Will Conner, Baxt Ingui Architects
For our firm, the projects that go well, stay closer to budget and time, and have a happier team and client, are the projects with weekly meetings. The meeting can sometimes be virtual and can sometimes be quick. Each should start the same way: here is what we did last week, here is what we plan to do this week, and this is what we need from you within the next two weeks.
The benefits to weekly meetings are not exclusive to Passive Houses but do become that much more important on Passive projects, especially for retrofits or when a contractor is new to a Passive House. As Kevin Brennan often says, “Passive House is a team sport.”
Tip 8: Use the blower door as a tool during and after construction.
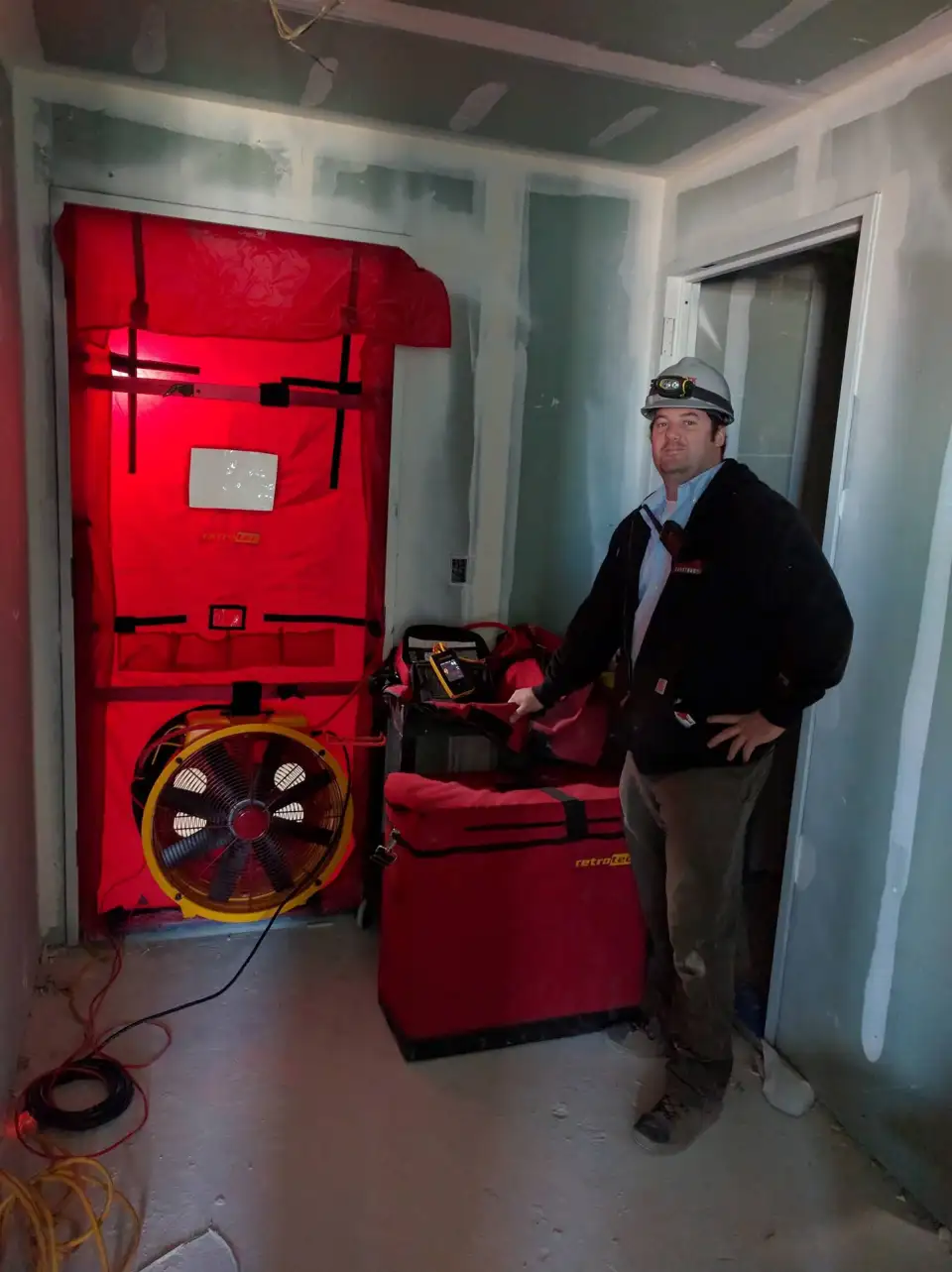
Check the layers as they are going in. Test early, and test often. Kevin Brennan, Brennan Brennan Airtightness and Insulation
Performing a blower door test as early as possible has been one of the secrets of success for our projects. It lets you find air leaks or issues while everything is accessible and easy to fix, allowing continuous building with confidence and ensuring you do not have to go backwards. Some of our contractors will mask the window openings (sometimes running the membrane or plywood right over the windows), so that a blower door test can be performed prior to window install. As windows get installed, the blower door can be used to test for leaks. This prevents you from looking for a needle in the haystack at the end.
Tip 9: Commission the house.
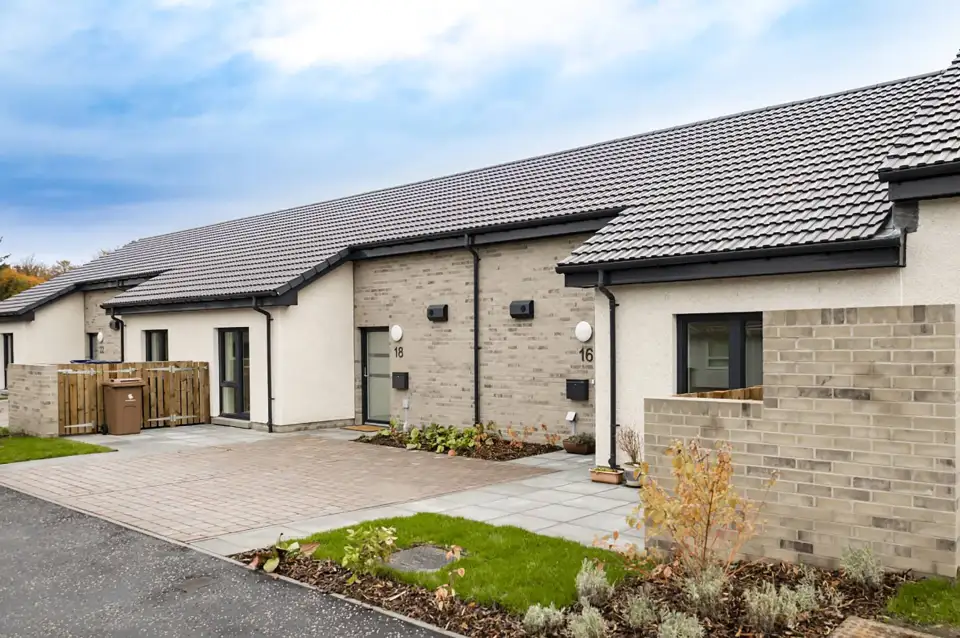
Allow additional time for commissioning—testing and adjusting installed systems—and handover. Handover should be done by the team involved in the commissioning. Having a third party, do the handover for you can lead to details being lost in translation, causing confusion. James Traynor, ECD Architects
Commissioning the house allows for all of the systems to be tested and balanced to ensure that they are working the way you intended. I have learned firsthand in my own Passive House how much better my ERV works post-conditioning and balancing. This is also a great opportunity to describe the system to your clients, show where filters need to be changed, how the thermostats work, and other aspects of their house.
Tip 10: Certify the project.
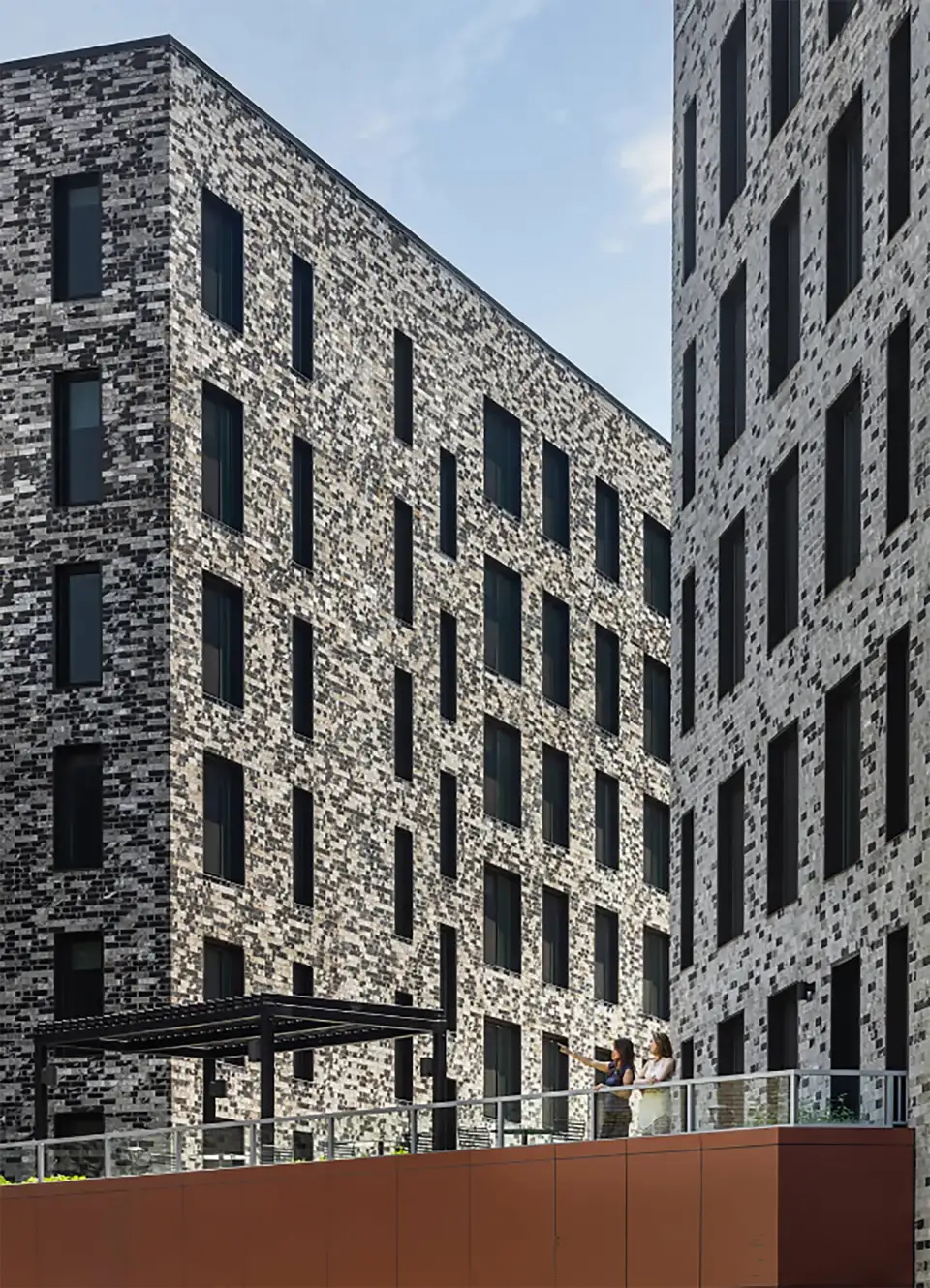
Without the rigor that comes from a third-party evaluation and certification, it might be too seductive to compromise on aspects of a project’s Passive House strategy during the heat of the moment in construction. John Woelfling, Dattner Architects
Take lots of photos and other types of documentation. Require contractors to do the same. Marc Fabris, Baxt Ingui Architects
Certifying the project helps to de-risk the entire project for the owner and team. It ensures that you take the time to get everything right, document correctly, and test at the end to ensure the building performs as designed.
Final Thoughts
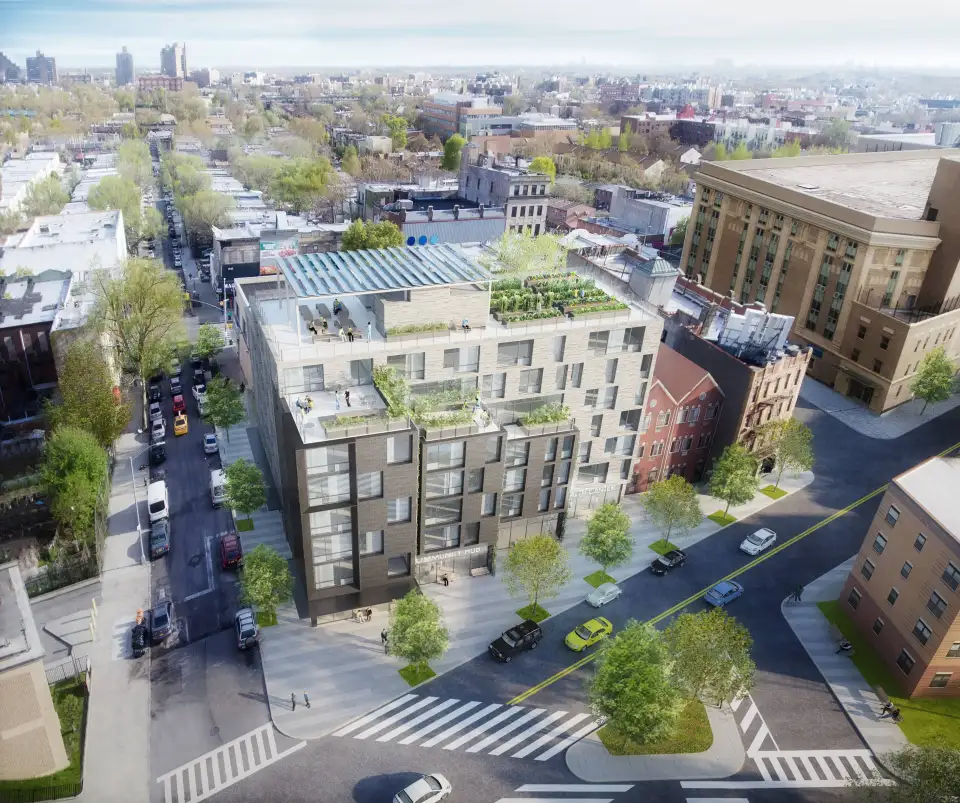
Make it an exciting and positive process for people that they can feel proud of. Celebrate when you can! Sara Bayer, Magnusson Architecture and Planning
Commit yourself to being a changemaker and to designing and building better, more sustainable communities. It will not be easy, so get ready now by understanding the process and the numbers, and always remember that it is worth it! Derrick L. Tillman, Bridging the Gap LLC
One of my favorite parts of the responses I received is that many added extra items, words of encouragement, things to remember, and more. The Passive House community is a collaborative, open, and accepting group, and it’s fun to be a part of it.