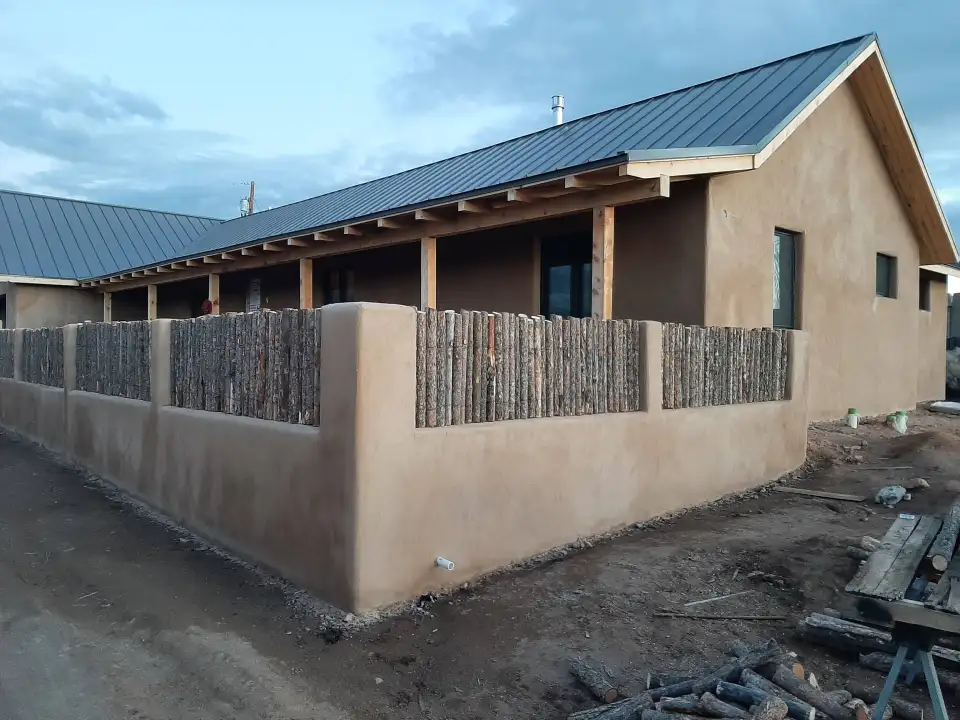
As was true for so many people, 2020 was a pivotal year for Kyle Siler-Evans and Alexandra Burke, and they began to take stock of the lives they had built in the Pittsburgh area. As the COVID-19 pandemic swept across the country that spring, they were lucky enough to remain in their homes, and they had the time to think about what was really keeping them in Pennsylvania. “Lots of people have this story, right? I was working two miles away from my office, but I hadn't been in in six or nine months,” he says. “I realized it didn't matter if I was two miles away or 2,000 miles away.”
Within that 2,000-mile radius was the city of Santa Fe, New Mexico, which is where the young married couple were both born and raised. As they could both work remotely and had talked about one day returning to the Southwest, they decided now was the right time to buy land within the city limits of Santa Fe and build on the site.
Though Siler-Evans is not a professional contractor, he spent several years remodeling and performing repairs on a few homes in Pittsburgh that he rented out prior to moving to New Mexico. The rental homes were just a source of extra money rather than a career path, but he’d gradually acquired more and more skills and had also learned about best practices and some building science to better understand how to improve the performance of his properties. Over time, he became a subscriber to Fine Homebuilding and Green Building Advisor and learned about building standards like Passive House. Even before buying the property in Santa Fe, he recognized that building his own home from the ground up was not a distant, bucket list item, but a practical plan.
Moreover, he knew that it needed to follow the principles of Passive House design. “I figured we’ll probably do this once in our lives, so let’s do it right.”
In the first half of 2020, Siler-Evans discovered Colorado-based Emu Passive and took an online training course to become a certified Passive House tradesperson. After purchasing the property, he then traveled to Colorado to participate in a workshop with Emu co-founder Enrico Bonilauri, who helped him with the PHPP modeling for the house that Siler-Evans and his wife had designed together, and they decided to build to PHI’s Low Energy Building standard.
Bonilauri notes the project is part of Emu’s North American Passive House Pilot Program. The projects that take part in the firm’s Pilot Program provide data to Emu and in return receive assistance in navigating the certification process and access to resources that include construction details, specs, reviews of Passive House-related quotes, support during construction, and dedicated pricing from participating manufacturers. As Bonilauri notes, many single-family projects have details that are very similar, and it is not an efficient use of resources to have the architect to treat common iterations as unique design challenges. By providing standardized, pre-vetted Passive House details for more familiar features, Emu’s Pilot Program reduces time and costs for modeling, and shifts the focus to supporting the builders during construction.
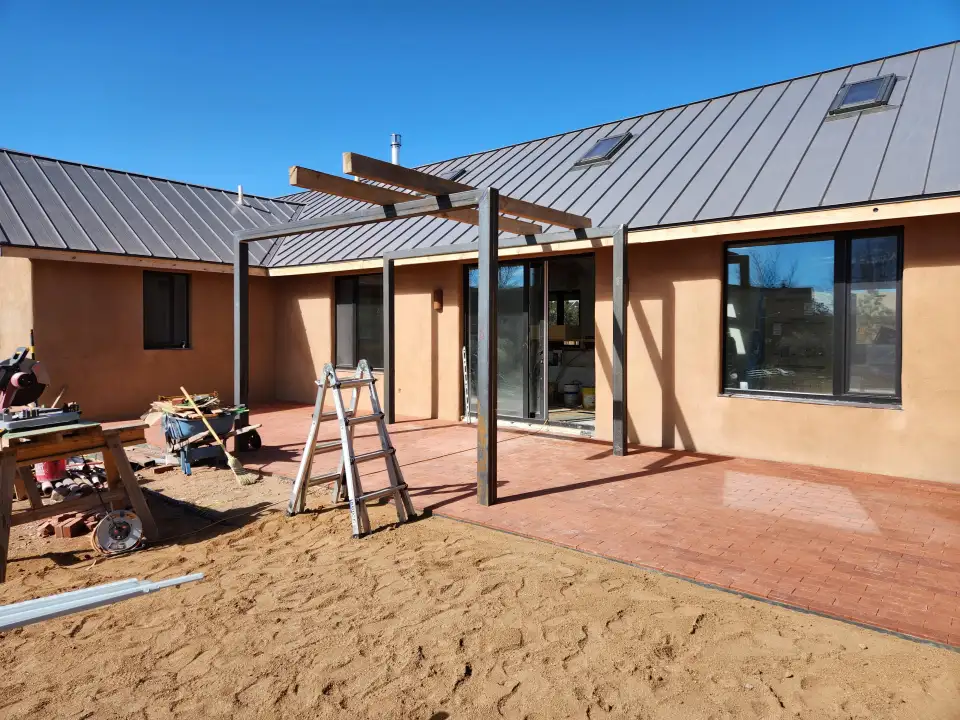
Designing for Santa Fe
Though located in the Cactus State, Santa Fe is in climate zone 5B, and its climate is more similar to Denver than nearby Albuquerque. This disparity is largely because of the approximately 2,000 feet in elevation separating the two New Mexico cities, with Santa Fe being perched approximately 7,200 feet above sea level. Though it sees significant snowfall in the winter and remains a heating-dominant climate, air conditioning has become increasingly necessary, because summer’s average highs regularly exceed 90°F. Consequently, they had to design for a home that could handle both extremes.
Furthermore, air quality is an issue in Santa Fe. Though wildfires are not as large a concern as in many other parts of the Southwest, smoke from both small, nearby fires and larger fires from as far away as Arizona and California can impact air quality. Similarly, juniper pollen in the spring leaves causes allergies for many people within the city, including Burke. “Fingers crossed, having a nice airtight house and a whole-house air filtration system will really help with that,” Siler-Evans says.
Despite the pollen and occasional smoke, one of the major benefits of living in Santa Fe is that it has close to 300 sunny days per year, while the average in the United States is only 205. That’s a nice change of pace from Pittsburgh, which has an inverted ratio of sunny to cloudy days (59:306). Santa Fe’s sunniness means that PV systems on homes there will generate more energy than a comparably sized system in a place like Pittsburgh. However, Siler-Evans was quick to point out that there are health benefits to installing a PV system in places around the Rust Belt, even if they are cloudier than the national average. In fact, a PV system in a place like Pittsburgh or New York actually generates 15 times the health and environmental benefits of one in places like Santa Fe or elsewhere in Arizona. “They’re primarily displacing an old, dirty, coal-fired power plant that’s upwind of major population centers,” Siler-Evans explains. “So, even though you get less energy out of that panel, it displaces more harmful emissions.”
This was not a casual tidbit of information he picked up after reading an article online. This was the central thesis of his PhD dissertation. As it turns out, Siler-Evans is a research engineer for the RAND Corporation, a non-profit nonpartisan policy analysis think tank, and he has published numerous papers on civil engineering, education, and labor markets. “Most of my days are spent thinking about big, world problems and helping government and other entities figure out how to tackle them,” he says, noting that energy policy and climate change are two of those big, world problems.
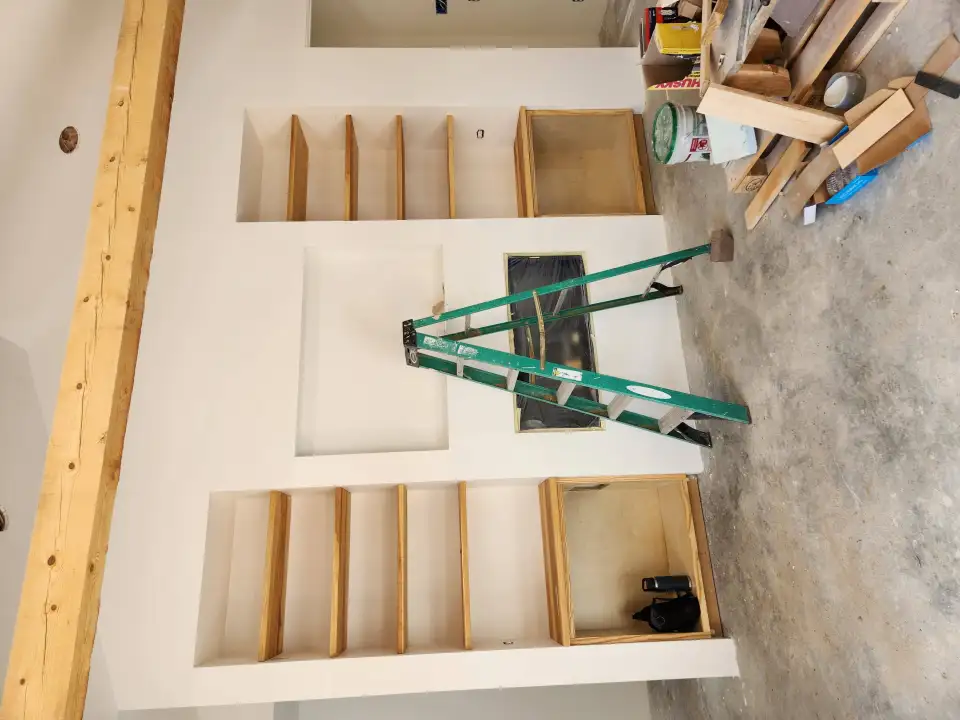
Building in Santa Fe
Construction on the home began in March 2022 and is scheduled to end in March 2023. Despite considering himself only “reasonably skilled”, Siler-Evans has managed to do the lion’s share of the work on the home with just two other people. This work has included framing the exterior wall construction and windows; doing masonry work; installing the electrical, plumbing, and flooring; and even building the cabinets and the front door from scratch. His skeleton crew also installed just about all the Passive House elements of the home, including the Zehnder ERV system and the components that make up the exterior wall assembly. He only subbed out for the pouring and forming of the foundation and the installation of the Mitsubishi mini splits.
“I was fortunate enough that my company let me kind of step back from work for a year,” he says with a laugh, “so I'm swinging a hammer six days a week.”
The house is a single-story, with 2,200 ft2 of heated space and a 500-ft2 garage that sits outside of the passive envelope. It is slab-on-grade construction with 8 inches of rigid foam beneath the slab, giving the foundation an R-value of 28. The wall assembly is 2x6 construction with blown-in fiberglass insulation, ZIP sheathing, and then an additional 4 inches of rigid foam insulation beneath a stucco finish that is approximately ¾ of an inch thick. The R-value of the wall is 27, which is modest compared to the vented roof, which has an R-value of 80. That assembly includes 20 inches of blown-in cellulose sitting atop an INTELLO membrane, and beneath that is a 2x4 service cavity with fiberglass batts.
As Siler-Evans notes, their property is ideal for Passive House design. “It’s a perfect north-south orientation,” he says, adding that they have designed the house so that its back faces south and includes the home’s largest windows, which are shaded by a two-foot roof overhang. The protrusion is long enough to block the higher summer sun and avoid excessive thermal gains, but short enough to allow passive solar heating when the winter sun is lower in the sky. Siler-Evans says that modeling performed by Emu as part of the Project Boost allowed them to find the sweet spot for the length of the overhang.
Once construction is completed, Siler-Evans hopes to have enough in his budget to install a PV system for which the standing seam metal roofing is readymade. The angle of the pitch is ideal for solar, and Siler-Evans notes that there are brackets that can be effectively clipped on to the ribs of the seams without the need for any penetration.
Of course, not everything has fallen into place throughout the construction process. Sourcing for some of the more specialized components was difficult, but Siler-Evans avoided any bottlenecking by ordering them well in advance. “I think we got most of what we wanted,” he says. This supply wish list included the triple-pane windows from Alpen and Fakro skylights, which he ordered before the project even broke ground.
He also says that pricing, while still erratic, has not left him with the disheartened sense of shock and awe that plagued the construction industry during the early days of the pandemic. Surprisingly, he notes, the pricing for the Alpen windows was not more expensive than even conventional windows despite having twice the performance, a better warranty, and similar lead times. “We didn’t pay any more to get Passive House-grade windows.”
This nonexistent cost premium was certainly not true across the board, and seeing the inflated prices for materials—whether high-performance or not—quickly dashed any illusions of finishing under budget. “Almost everything was more expensive,” he laughs. “Like, we definitely blew the budget.”
Despite the costs, Siler-Evans sees his Passive House project as more than just a healthier home for him and his wife or a line item on his bucket list, but as a clear counterexample to policies that have fueled climate change and energy insecurity. “We want to make sure we're not contributing to furthering those problems. We're finding the solution here.”
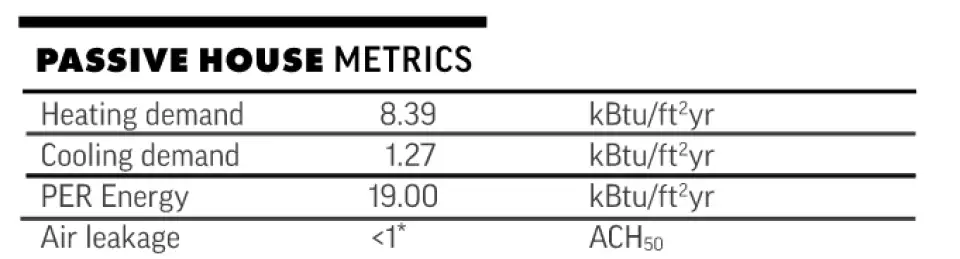