Sometimes great ideas take years–or decades—to actualize. Roger Meager first came up with the idea of building a very low-energy home roughly 30 years ago. Life intervened. His children were born; he switched jobs; and he and his wife, Mary Thomson, changed cities several times, moving at last to Ottawa, Ontario. Finally, he and Thomson, who were empty nesters by now, got fed up with renting and started shopping for a house or apartment that they could settle in for the long haul. Their search turned into a full-on Goldilocks experience. Nothing seemed that desirable or worth the asking price. Ultimately, it was the undesirable house that led to their happy ending: a certified, infill Passive House that is just the right size.

A Just-Right Passive Home
“It was plainly obvious that this house wasn't good,” notes Meager, speaking of the property they eventually purchased. The house was falling apart in multiple ways and clearly would need a drastic overhaul, if only there was anything worth overhauling. And, the street it was on has strip-mall stretches, albeit in a different section. “Nobody wanted to buy it, because the address just put people off,” he explains. Meager didn’t want to knock the house down, because of the waste that would generate, but a building inspector concluded that the property was essentially a vacant lot in the making. “So, in the end, we said, well, we'll build. Let's build this Passive House.”
To minimize the waste associated with demolishing the existing building, he contacted Habitat for Humanity to come and strip the house. However, he bought the property in 2020, and because of Covid, Habitat had stopped providing that service. Instead, he posted notices that the house would be demolished and all the fittings could go. People came and took everything. “They took the windows, the toilets, the baths, the showers, the chimney, the fireplace, and even all of the newer electrical outlets went,” he recalls. Finally, a demolition company was hired who promised to separate the salvageable wood.
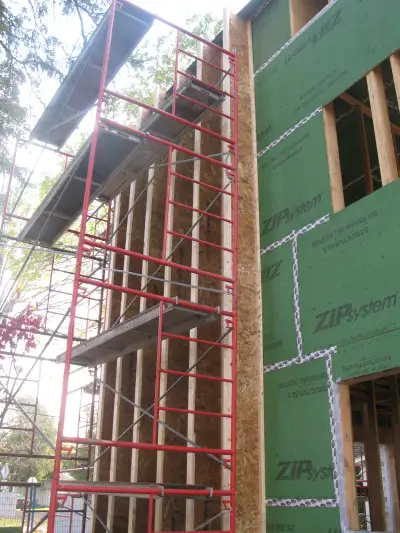
In Ontario, before you can get a permit to take down a building, you have to submit a plan for what will take its place. So, Meager and Thomson were simultaneously planning for destruction and construction. They were both intrigued by the promise of prefabrication, due to its quality, predictability, and minimizing of construction waste. At first, they were drawn to a modular solution, but that got overly complicated. They wanted a fairly simple house with two bedrooms and one-and-a half bathrooms. Their research eventually led them to EkoBuilt, based nearby in Ottawa, which offers a range of options from a materials package to prefabricated wall panels to full house plans. Meager and Thomson were impressed by the knowledge and enthusiasm for Passive Houses of EkoBuilt’s founder, Paul Kealey, and found the firm’s designs and concepts to be innovative and “future proof”.
“We're not concerned about fancy Italian tiling,” explains Meager, “but we are concerned about the structure of the building, and the way the building operates. That is the most important thing.” Meager and Thomson chose an EkoBuilt materials package designed to construct a saltbox-style house with two floors and a total square footage of roughly 1,200. The home has two bedrooms, an office, a full bath, plus a half bath squeezed into a utility room that also manages to include the ERV and the water heater. A Mitsubishi heat pump with one indoor head on each level provides heating and cooling.
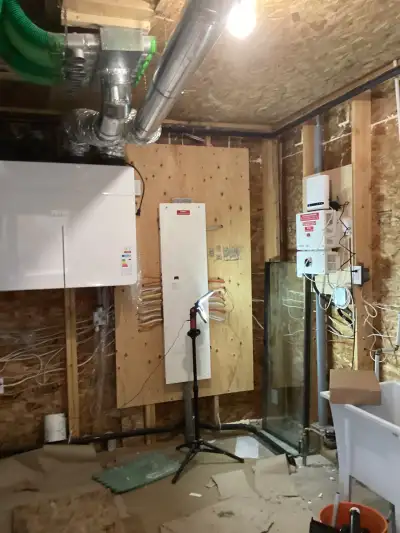
“Roger and Mary have one of the most efficient domestic hot water systems I have ever seen with a shower drain water heat recycler for the only shower in the home, as well as a tankless electric resistance heater,” says Tad Everhart of Certiphiers Cooperative, who helped manage the certification process, along with Susan Stocker. The home achieved the Passive House Institute’s Low-Energy Building certification rather than Passive House Classic, due to shading by surrounding homes that limited the wintertime solar gains and thus increased the space heating demand. The house easily meets the other main criteria—cooling and primary energy renewable demand—and achieved a final airtightness of 0.4 ACH50.
There is no question that Meager and Thomson love their home; they gush about its comfort, performance, and the fresh air delivered by their Jablotron ERV. “We're living well,” says Meager, adding, “You know, it's fantastic.” After installing a PV system designed to produce 4.5 MWh annually, they paid only about $300 Canadian for their electricity use over an entire year.
However, the path to getting their fantastic home was not exactly smooth. While EkoBuilt delivered and contracted with a crew to assemble the materials package required for their airtight and weathertight shell, Meager assumed the role of project manager for the rest of the build. He had had some construction experience in his younger days, but still this task he had set for himself was not made easier when another builder that Meager hired to install the board and batten siding told him that several of the Munster Joinery windows, which had been included with the EkoBuilt package, had not been installed correctly. Asked why he didn’t reach out to EkoBuilt to address these issues, he says, “The problem was we had no faith.” When contacted, EkoBuilt was surprised to have not heard from Meager on this item, since they have had active communication with Meager on other items.
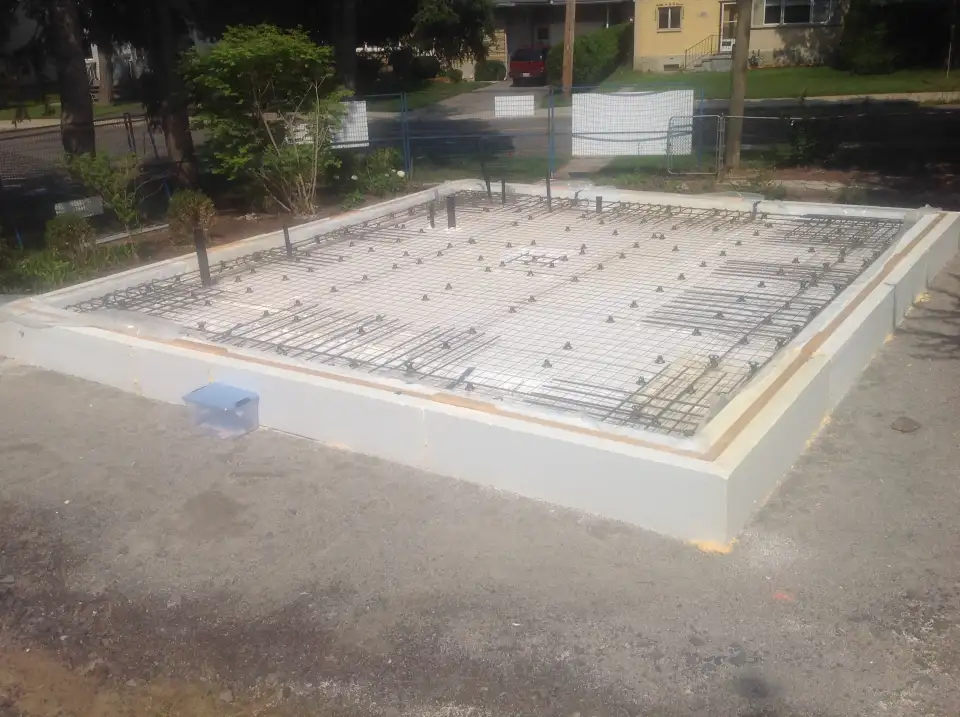
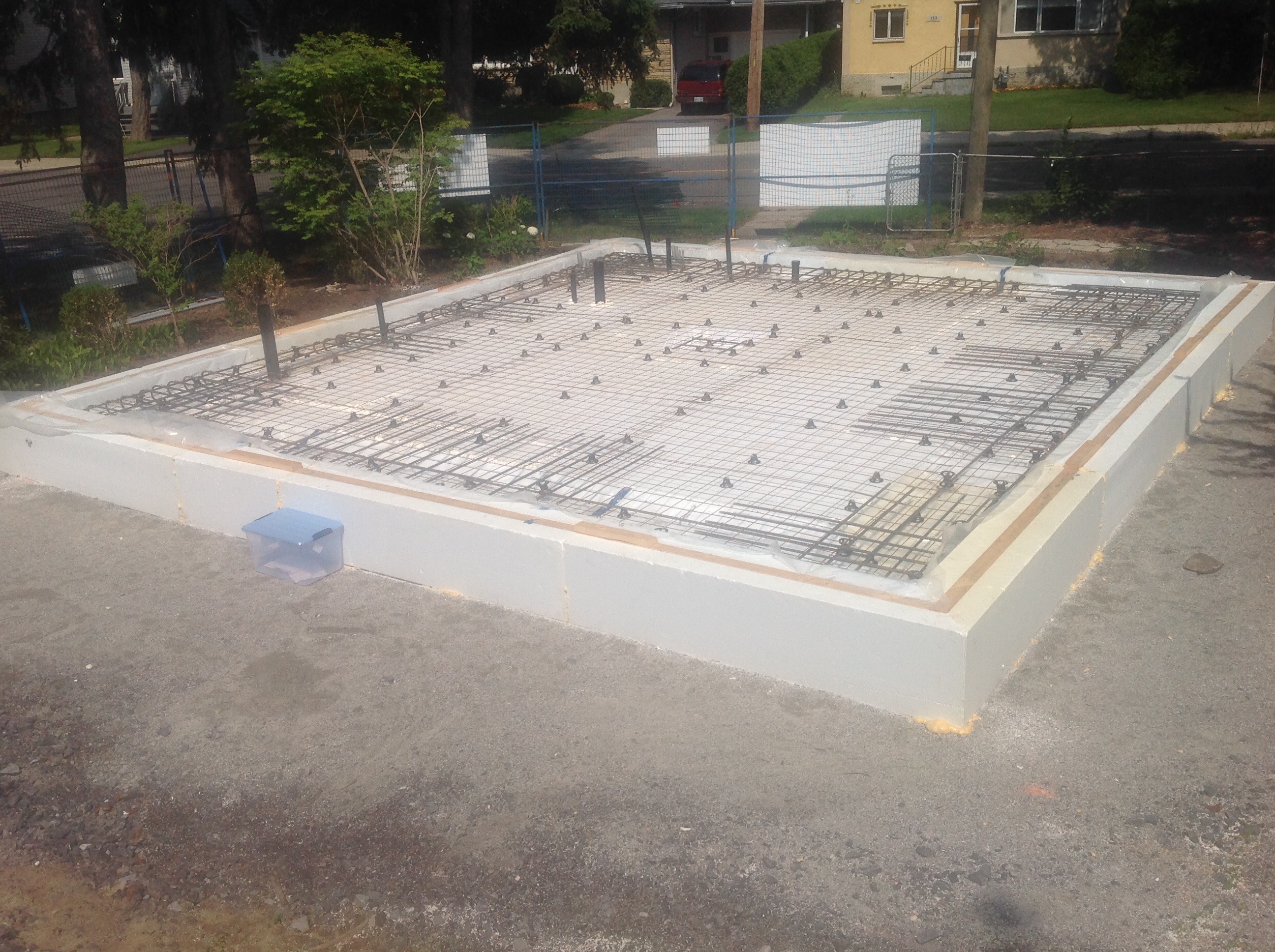
The foundation displays the modest footprint of Meager's home.
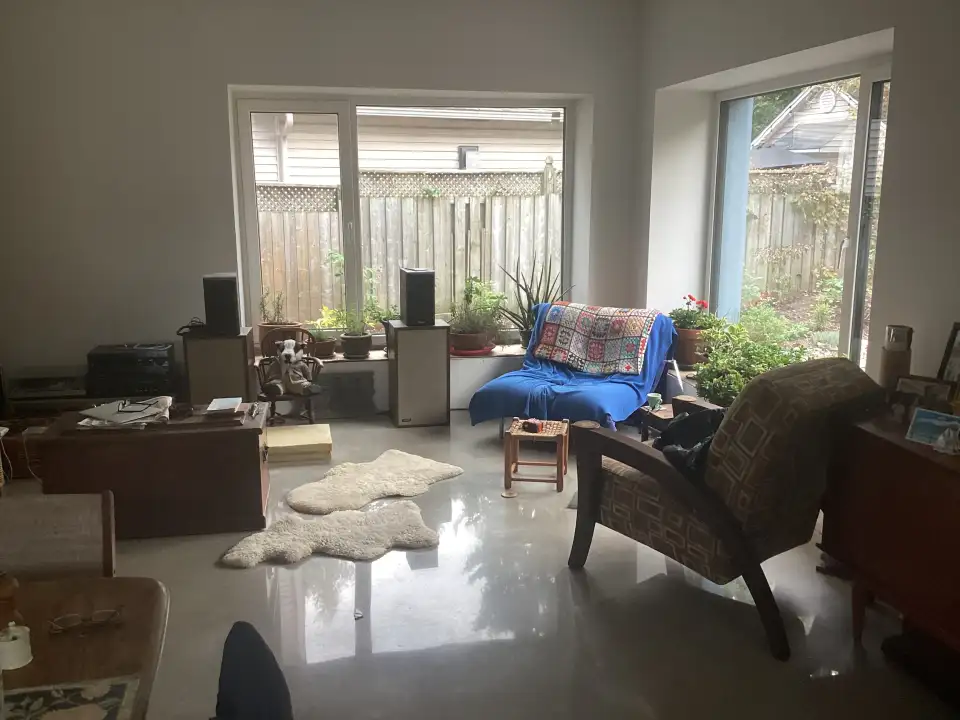
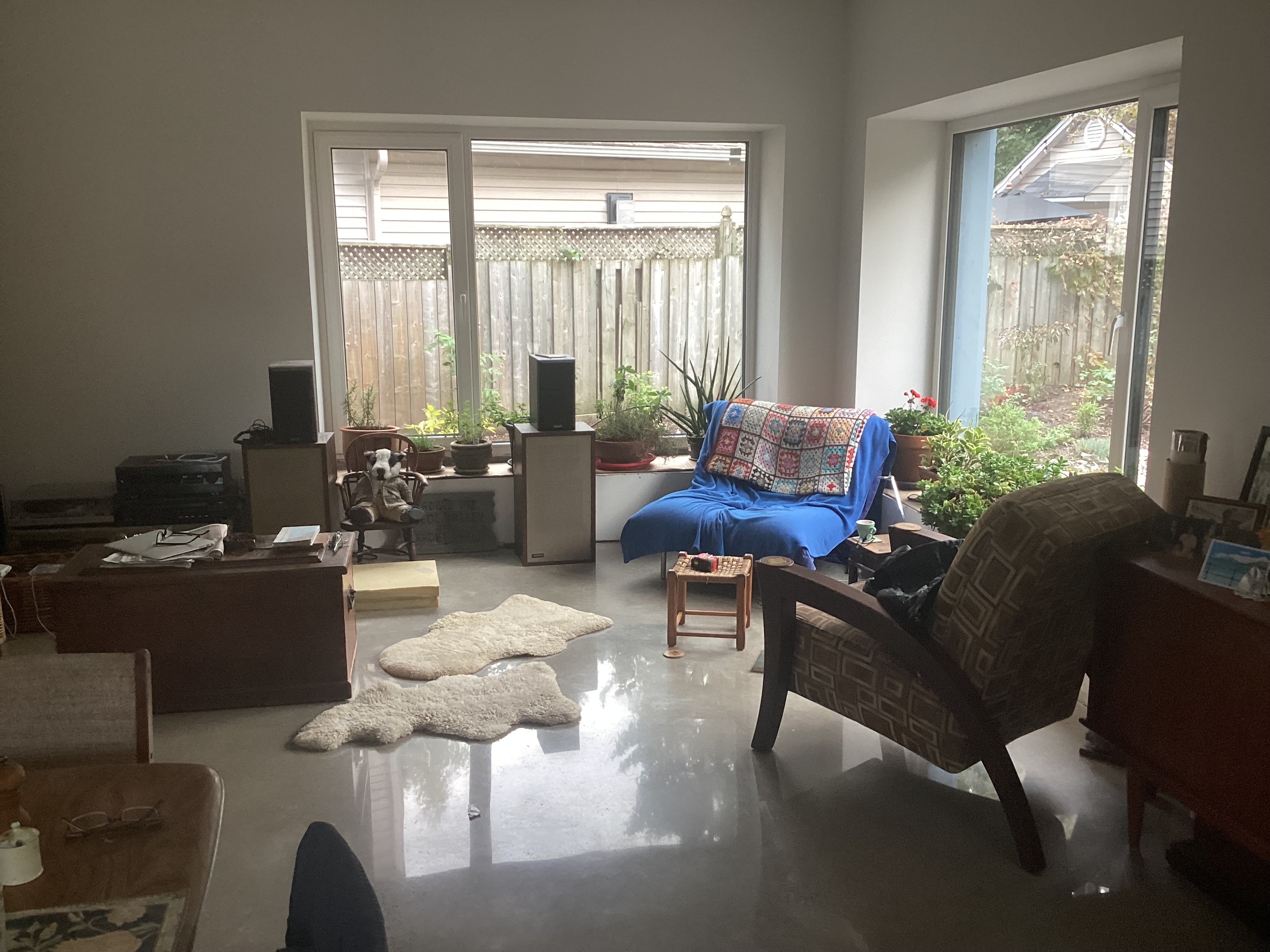
The living room on the ground floor.
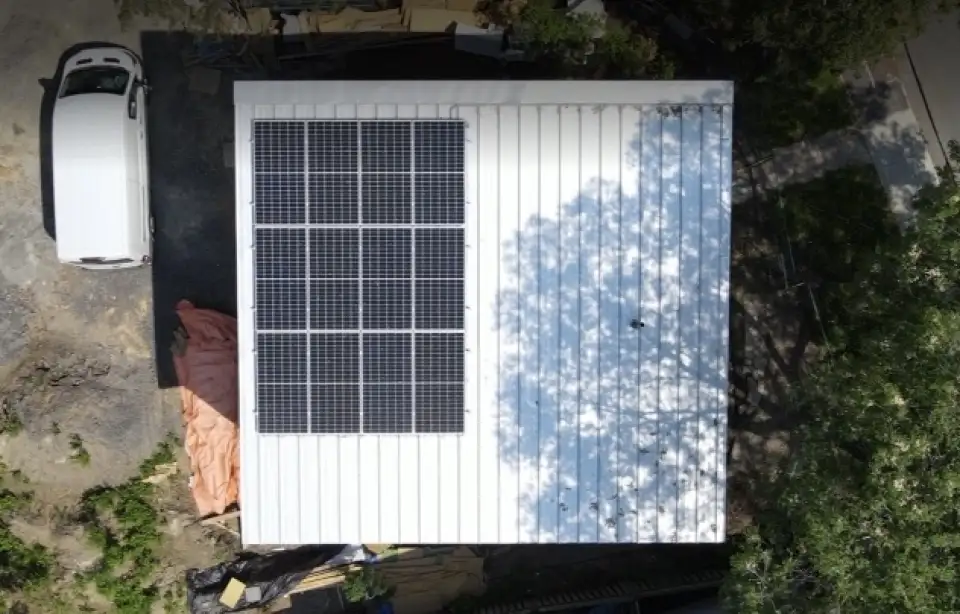

The view of the PV array from above.
Meager ended up investing a lot more money and his own labor into getting the windows installed correctly, the house properly air sealed, and generally finishing the project. He gasketed, he taped, he foamed, and he oversaw the dense-packing of cellulose into the walls’ I-joists, along with thorny questions about where exactly the mechanical and plumbing runs would go. In the process he came to fully understand the sort of detail that is required to hit the Passive House performance targets, especially the airtightness number. “In these sorts of buildings—obviously in any building, in any construction—the devil's in the detail. And, it's the detail that you don't see, which is really important,” he notes.
Meager is enthusiastic about certification as a process that forces all concerned to stick to achieving the set goals. “Without Tad, I would have probably lost faith, but he was evangelical for me,” he explains, “and that was very good.”
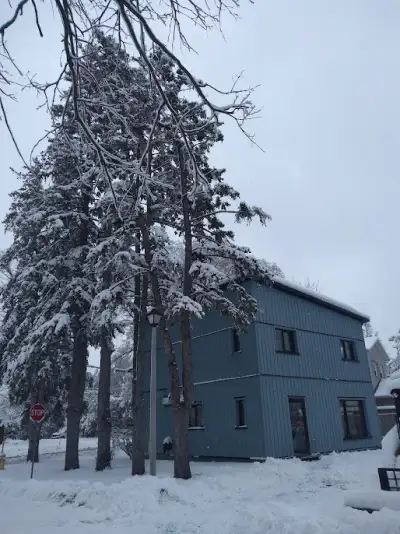
Perhaps not surprisingly for a first-time project, building a small Passive House turned out to be more expensive than Meager had expected. For that and a host of reasons, he is really happy that he built exactly the size house that he needed and no bigger. He was quite surprised—and not happily so—to find that his is one of the smallest on PHI’s database. In his view, a big single-family Passive House defeats the purpose of living more sustainably. “We all grew up in small houses,” he points out, adding, “We've got to stop building big houses, right?”
He also wonders how to make Passive Houses more achievable for more people. “Everybody who comes to our house is amazed by it, which is flattering, but how can we get that to be normal,” he ponders.
One aspect of achieving a certified single-family home has gotten easier. PHI recently introduced a more streamlined process for certifying single-family homes, easyPH, that simplifies the inputs needed for the energy balance calculation, reducing the total number of worksheets to just eight.
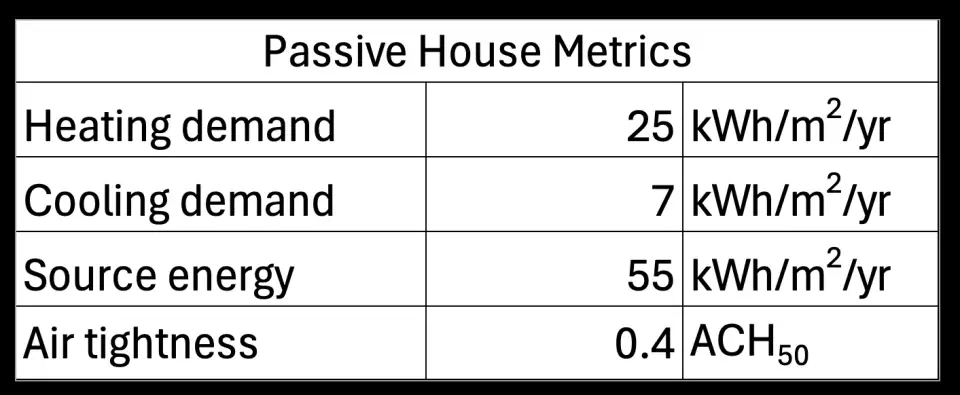