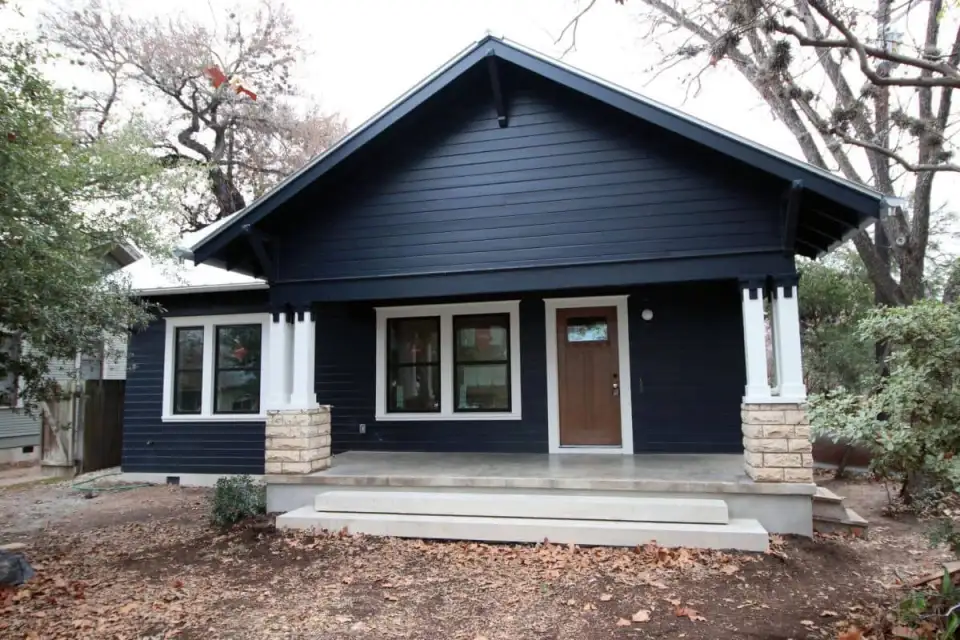
Architect Trey Farmer and his gradually growing family lived for seven years in a 100-year-old Craftsman-style house that never quite attained the moniker of comfortable. That’s unsurprising: The prerenovation blower door test came in at 16 ACH50—definitely drafty, although at least the holes weren’t big enough for mosquitoes to fly through. “A good chunk of the time we’ve lived here we’ve been designing its remodel,” says Farmer, who works with Forge Craft Architecture + Design in Austin, Texas. He and his wife, Adrienne Farmer, a designer with Studio Ferme and a part-time personal chef, designed the final remodel together.
Farmer’s home is just a few blocks from downtown Austin. The neighborhood is designated as a national historic district, although the original 1,400-ft2house hadn’t garnered any particular recognition. The neighborhood status, along with the existing home’s nonconforming setbacks, limited his redesign options. The single-story home remains single story; an addition to accommodate more bedrooms has resulted in a 2,100-ft2 home featuring three bedrooms, two and a half baths, and a large open-plan kitchen, dining, and living room. At first designed with the 2015 PHIUS standard in mind, the home is now a pilot case for the 2018 PHIUS standard in a hot-humid climate.
Part of Farmer’s intent with this remodel is to set an example for the local building industry that is practical to imitate. The changes to the PHIUS standard in 2018 have helped in this regard, according to Farmer, because the newer standard is more attainable and more attractive from a cost standpoint than the 2015 standard was. To further increase this project’s attractiveness in the eyes of local builders, “I’ve been trying to use products and methods that are commonly used in the speculative and custom home industry in Austin,” he explains.
Although the project started as a remodel plus addition, it became closer to entirely new construction once the existing house was taken down to the studs. Extensive termite damage was found. The big advantage to this setback was that Farmer was able to rebuild mostly with 2 x 6 walls, rather than having to work with the old 2 x 4 ones, and could fit more insulation into the wall assemblies. Within the wall, Farmer installed mineral wool batts. For a continuous thermal break, he opted for an insulated exterior sheathing that includes a 1‑inch layer of rigid foam along with a water-resistant facer. He chose this product partly because its uninsulated version is familiar to the building community there.
The question of how best to insulate at the roofline was one of the rabbit holes that Farmer fell into, as he describes it. Local code requires encapsulation of insulation installed at the roofline unless it’s part of a cathedral ceiling, which was only the case for 30% of the ceiling. After debating the merits of sprayed foam—a common approach locally—Farmer chose two layers of mineral wool batts stacked on top of each other, yielding an R‑value of 38.
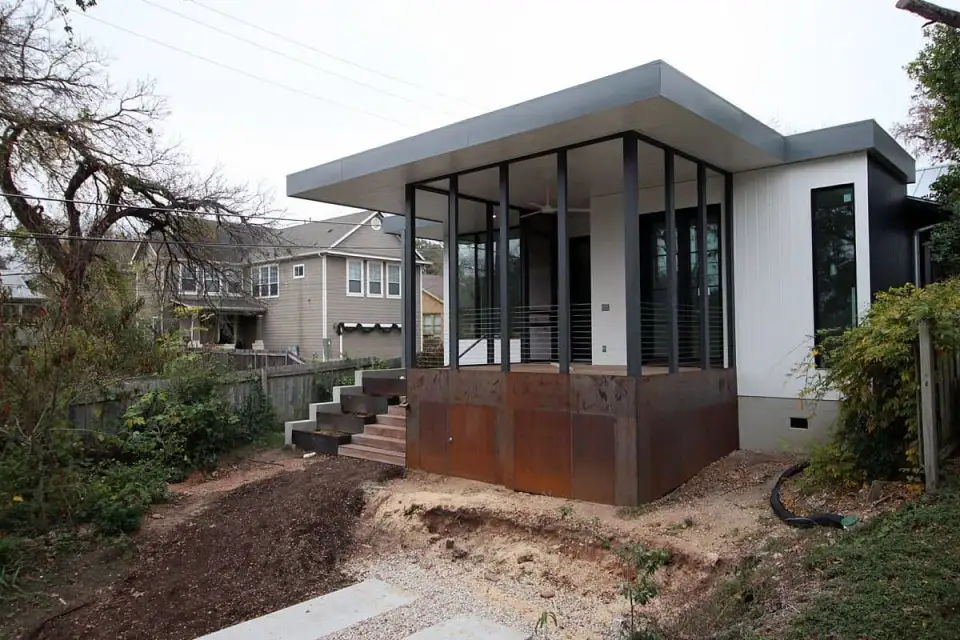
Below the house, the crawl space was insulated using a sprayed foam product—not Farmer’s favorite aspect of the project from a carbon viewpoint. He had explored creating a conditioned crawl space but got scared away by a friend’s experience with that approach, who found it to be expensive and a headache. “Working under a 100-year-old house, there aren’t a lot of options,” he says.
Windows were another rabbit hole for Farmer, as he worked to balance cost and optimal performance for specific façades, along with his ever-present concern for sticking with typical brands. At various points in the design process, Farmer had consulted with another architect whose specialty is historic remodels, and this architect helped preserve the cottage feel in front while ensuring that the views of downtown Austin from the rear addition weren’t sacrificed for slightly better performance. Ultimately Farmer ended up with three types of window from the same manufacturer. In the front of the house, to preserve the original look, he selected triple-pane wood-clad faux double-hungs, most of which are fixed with strategically placed casements. Other walls feature triple-pane windows, and the addition boasts larger, modern-looking windows with a U‑factor of 0.17.
The east-facing modern windows are shaded by a screened porch, which gets extensive use in three, and sometimes four, seasons. A panel of vines filters out the summer sun on the southern façade. The west side gets shading from a front porch and extensive tree canopy—a benefit of being in a well-established neighborhood. According to Farmer, the most recent WUFI version can accommodate shading geometries generated by certain BIM programs, which he found helpful when it came to estimating the impact of these different shading components.
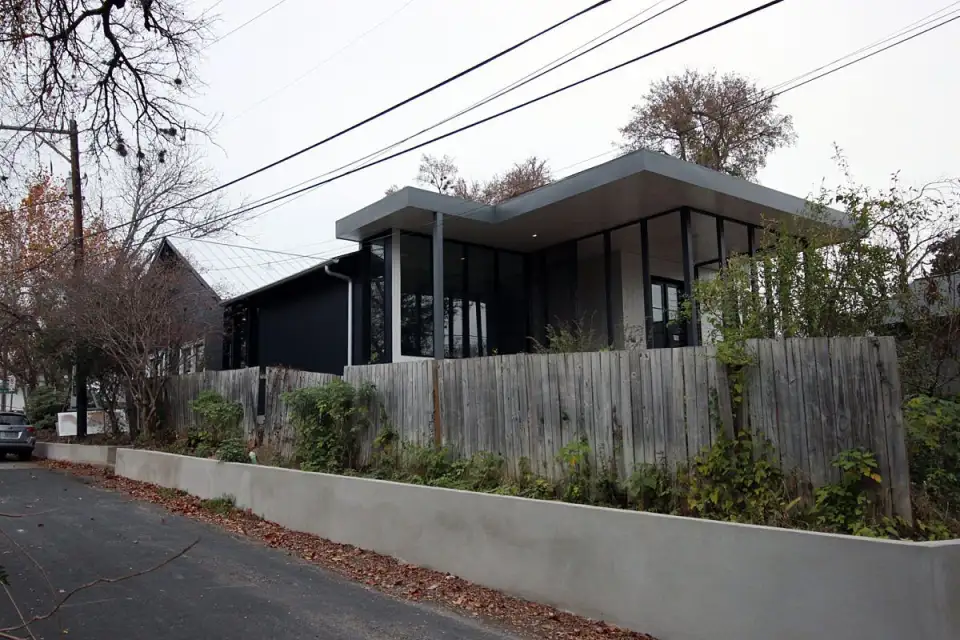
Humidity is a major concern in this climate. An ERV helps with screening out moisture, aided by a dehumidifier programmed to run when the interior relative humidity hits 55% on the indoor air quality monitor. A separately ducted variable refrigerant flow heat pump provides heating and cooling. Even with this equipment, the local green building group expressed concerns that the ERV would not be able to sufficiently exhaust the bathrooms during showers, and indeed might be triggered into conserving the indoor moisture and redistributing it. To avoid that possibility, in each of the two full baths Farmer had dedicated exhaust fans installed that are controlled by in-line humidistats. Damper systems keep these vents sealed when not in use to minimize their potential leakiness.
The home is all-electric, with a heat pump water heater supplying the domestic hot water. The induction cooktop has been a pleasant adaptation, especially for the trained chef of the family. “We love cooking on induction and try to put it in all our projects,” says Farmer. “Once you see how responsive and powerful it is, it’s hard to go back to anything else.”
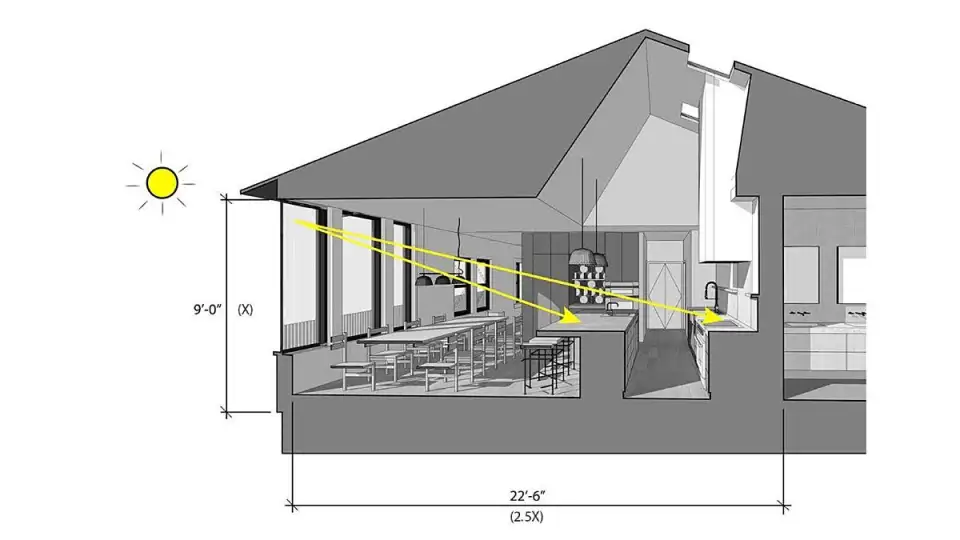
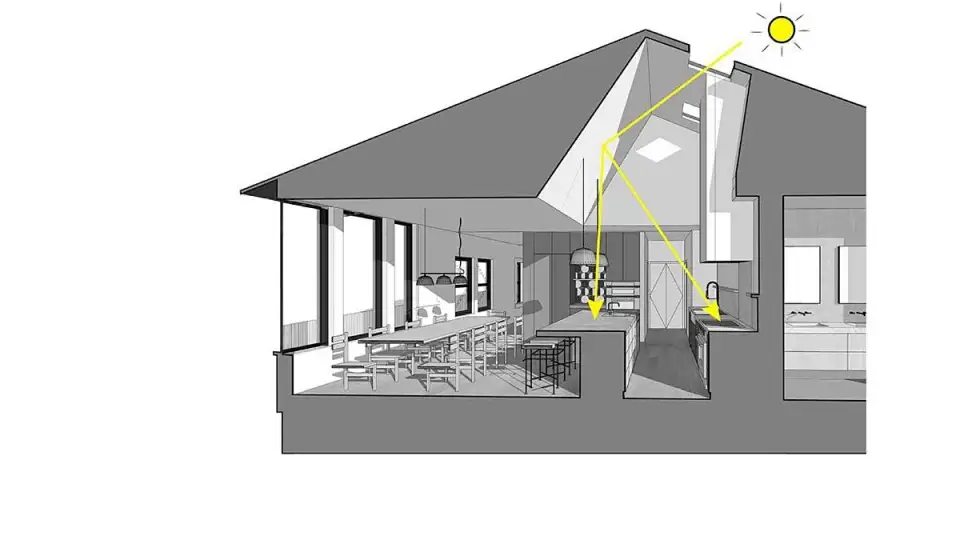
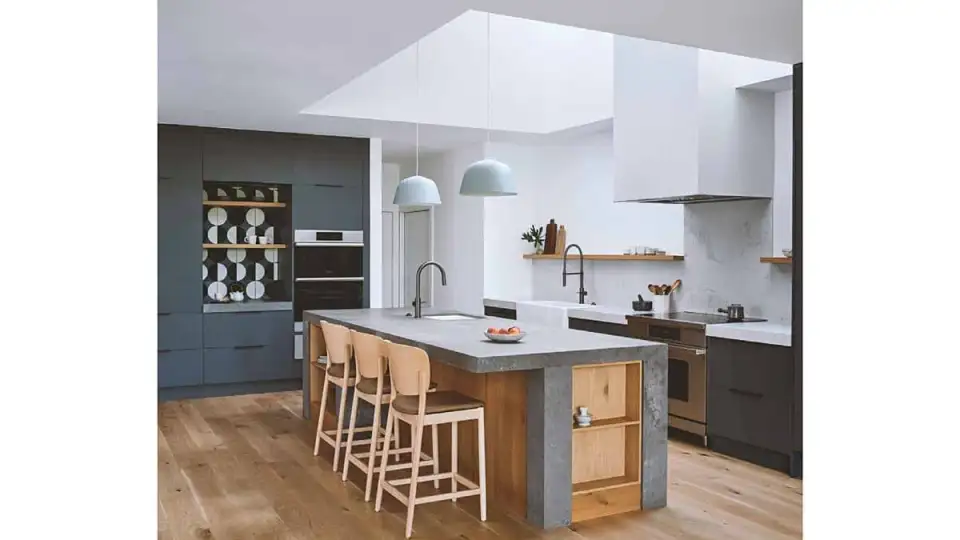
A rooftop 7‑kW PV system is expected to keep the house net positive on an annual basis, producing more energy than the family is expected to consume, which is why the site energy use shows up as a negative: ‑1.33 kBtu /ft2/yr. The PV array was sized to power an electric vehicle as well as the house, and Farmer also felt the oversizing was important to make a statement about trying to be a net positive contributor in a broader sense.
According to Farmer, the 2018 PHIUS standards reduced the required amount of insulation, cutting his project costs significantly compared to what would have been required under the old standard. He is tracking his home’s energy use and working with other experts to better understand the carbon impacts of all the decisions made in this project and how to optimally balance embodied and operational carbon in Austin’s climate.
This article was originally published in the Spring/Summer 2020 issue of Passive House Buildings.
Passive House Metrics
Heating Energy |
Cooling Energy |
Site Energy |
Air Leakage |
|
---|---|---|---|---|
kBtu/ft²/yr |
3.1 |
12.8 |
-1.33 |
0.025 CFM/ft² at 50 Pa |
kWh/ft²/yr |
0.91 |
3.75 |
-0.39 |
|
kWh/m²/yr |
9.72 |
40.14 |
-4.17 |