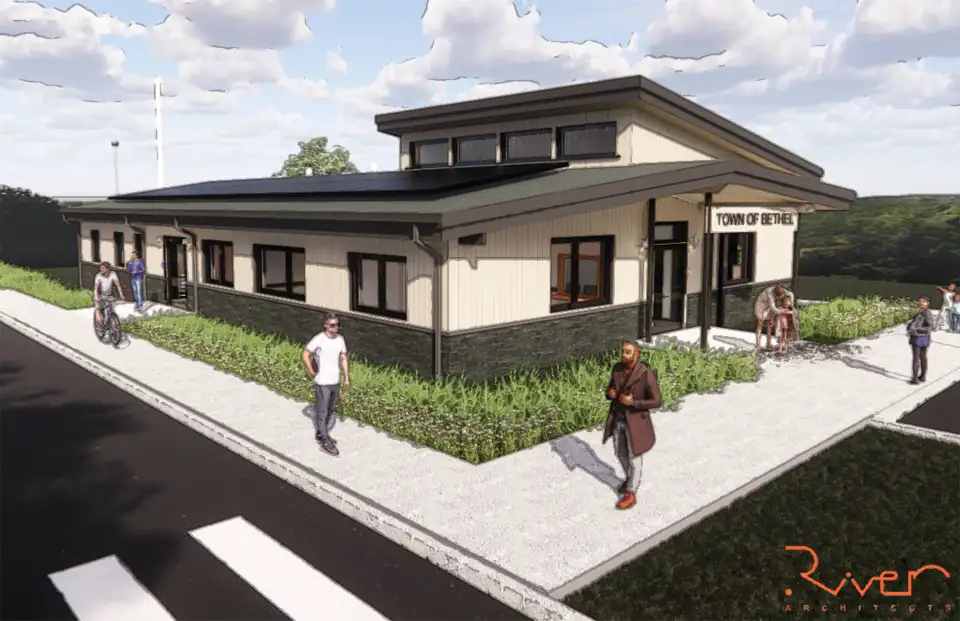
The town of Bethel, New York became famous overnight in 1969 as the site of the original Woodstock music festival. Today, the town still attracts pilgrims and concertgoers, especially to the 16,000-seat Bethel Woods Center for the Arts amphitheater sitting just south of where the festival took place over 50 years ago, but Bethel mostly continues to be a quiet rural community in the Catskills about midway between Poughkeepsie and Scranton. Much of the area consists of farmland or forests with a few hamlets featuring generally older detached houses, as well as a few standalone commercial structures.
These commercial buildings typically were constructed in the middle of the 20th century and should be familiar to anyone who has traveled off the beaten path in rural America, as they dot the landscapes from Maine to California and house everything from ice cream shops to dentists’ offices. They are unapologetically utilitarian, and often are still satisfying the existing needs of the community—be it for dishing out soft-serve or filling a cavity. If one were to describe their general aesthetic, they would sit somewhere between inoffensive and nondescript.
Bethel’s Town Hall is one such building. Originally constructed in the 1960s, it was used as a doctor’s office before becoming the town’s administrative center. Currently, all 11 of the town’s administrative employees work in the building, but conditions are less than ideal. It is less than 3,000 square feet and not compliant with the Americans with Disabilities Act. The corridor between the offices on the ground floor is bereft of natural light, the town clerk’s office has no windows, and the basement feels like a crypt. Juhee Lee-Hartford, founding and managing principal of River Architects, the firm behind the retrofit, describes it graciously as “rather difficult to use and limited.” Beyond being cramped, it also suffers from a lack of insulation and uncontrolled air leakage, as the acoustic ceiling tiles are currently the only layer separating the rafters from the office, according to James Hartford, a principal with River Architects. These conditions have translated into sky-high energy bills and a lack of comfort for those who work in the building. It’s the worst of both worlds.
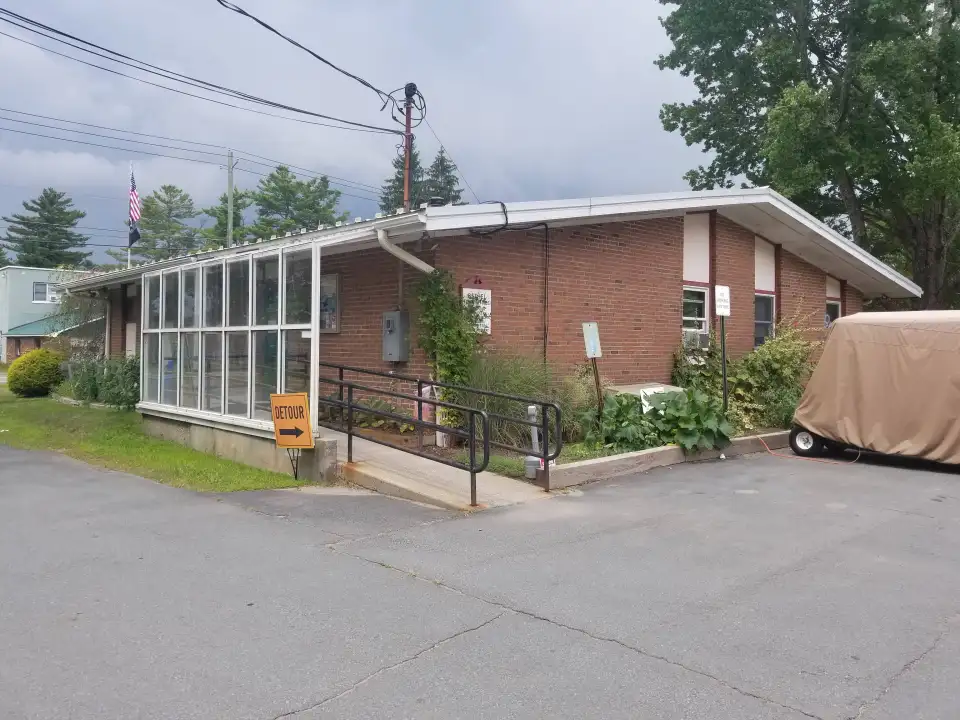
Building Community Resilience
As the home of the original Woodstock, it should come as no surprise that Bethel is a progressive town that is making a push to move the community toward greater sustainability. Sustainable Bethel Committee, a group of volunteers and Town Board members appointed by the Town Supervisor, has been particularly active in pursuing these goals. According to the group’s website, they “research opportunities and advises the Town Board on initiatives to conserve energy, move to renewable energy, reduce greenhouse gas emissions and otherwise make the Town of Bethel a more environmentally sustainable community.”
These efforts have paid off. In 2018, the town was recognized as “Bronze Certified” by Climate Smart Communities, a program that awards points to communities that incorporate concrete actions to make them more resilient and sustainable and is jointly sponsored by several New York State agencies. Among these agencies are the New York State Energy Research and Development Authority (NYSERDA), the New York Power Authority, and the Department of Environmental Conservation. Bethel is currently working towards silver certification, and some of the initiatives they are pursuing to achieve this feat include constructing a community solar project, converting the town’s streetlights to LED, and adopting a green building standard for new or renovated government buildings.
As there was a clear need to renovate and expand the Town Hall to meet the needs of Bethel and its employees, as well as a desire to create a more rigorous building standard, the town decided to pursue a high-performance retrofit of the building and to use it as a model for the new standard. The committee also recognized that NYSERDA was offering incentives to support projects within New York that are regionally significant, carbon neutral, and capable of achieving net-zero energy performance, and that they could obtain additional funding if the retrofit obtained Passive House certification.
Ultimately, these stars all aligned. NYSERDA has offered to provide 85% of the project’s funding through a combination of the Carbon Neutral Economic Development Program and the Clean Energy Communities Program. The Town Hall will serve as a model for Bethel’s Green Building Standard, and the building will pursue PHIUS+ 2018 certification on top of being fully electric. When completed, modeling predicts it will use approximately 85% less energy than the existing Town Hall. It will also be the first municipal building to receive Passive House certification of any kind in the state of New York.
Construction is set to begin in the first half of 2022 and should be completed by spring of 2023.
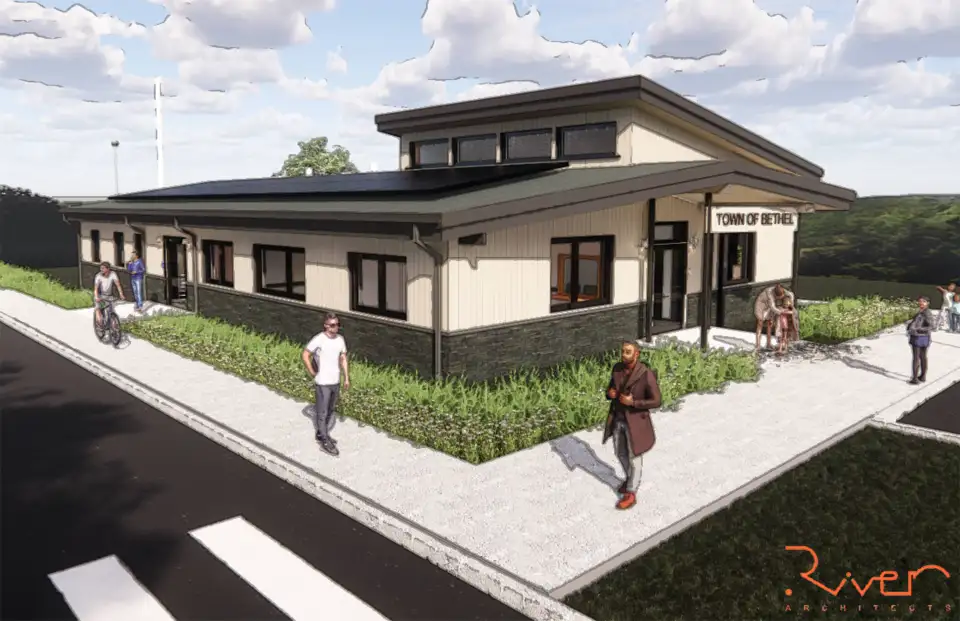
Reimagining Town Hall
Lee-Hartford and Hartford are anticipating a gut renovation of the existing building, and then plan to expand the square footage by approximately 50%, to 4,775 ft2. “We’re reusing the existing structure and frame as a means to provide a service cavity and HVAC interstitial space above that ceiling in the truss space,” Lee-Hartford says. The renovation will also include a complete overhaul of the basement area into a finished space that will house the town’s archives, an additional restroom, and an auxiliary workspace or meeting space for employees. The basement will also be home to an energy storage system for the onsite solar system on the roof of the property. Though the storage system has not been fully designed yet, the team hopes that it will be large enough to keep the building’s HVAC system and lighting operational during a nighttime emergency or severe weather event, and then transfer back to solar once the sun is shining again.
The thermal performance of the foundation will be enhanced by a layer of foam glass insulation that will be installed beneath the slab-on-grade foundation, resulting in an R-value of 21.6 (see detail), and the team hopes to reduce hydrostatic pressure around the foundation by incorporating sub-slab perimeter drainage and a robust vapor barrier using Stego wrap. Given the building’s proximity to White Lake and anticipated increases in rainfall in the Northeast due to climate change, the need for flood resiliency is of critical importance.
For the wall construction, Hartford is planning is to use structurally insulated panels that will have an R-value of 37, while the roof will consist of a 16-inch SIP panel with an R-value of 72. The panelized approach is a technique that Hartford says he learned while working on a design for the Troy Housing Authority with RetrofitNY, a NYSERDA-backed program that was heavily influenced by the Dutch Energiesprong program. Energiesprong has attracted worldwide attention because it has already resulted in the successful retrofit of over 5,700 homes, relying on digital scanning, offsite fabrication, and panelization to quickly retrofit buildings of similar typologies. While working on the program, Hartford was given the opportunity to visit the Netherlands to observe the implementation of the program firsthand.
The facade of the building will be embellished with local bluestone as a nod to the Catskills being one of the largest sources of the material in the United States, while the windows will be made of fiberglass and manufactured by Cascadia. The team ultimately landed on this decision because they were urged by the town to use materials not included on the Living Building Challenge's Red List. Materials placed on the Red List are known to pollute the environment, bioaccumulate in the food chain, and harm construction or factory workers. This extra step of consideration is indicative of both the amount of care that River Architects has dedicated to repurposing the existing structure and Bethel’s efforts to embrace local solutions for climate action.
As the existing Bethel Town Hall represents such a common building typology, this project could serve as a template for thousands of other buildings in New York. “That panelized approach is something that is readily applicable here,” Hartford notes.
For other communities and owners embracing climate smart strategies, this is certainly a project to keep an eye on.
To see details of the new town hall, check out the latest edition of Passive House Accelerator magazine here (pages 74-75).
Metrics
Heating Demand: 7.3 kBtu/ft2/yr
Cooling Demand: 4.4 kBtu/ft2/yr
Source Energy: 24.5 kBtu/ft2/yr
Air Leakage: 0.8 ACH50