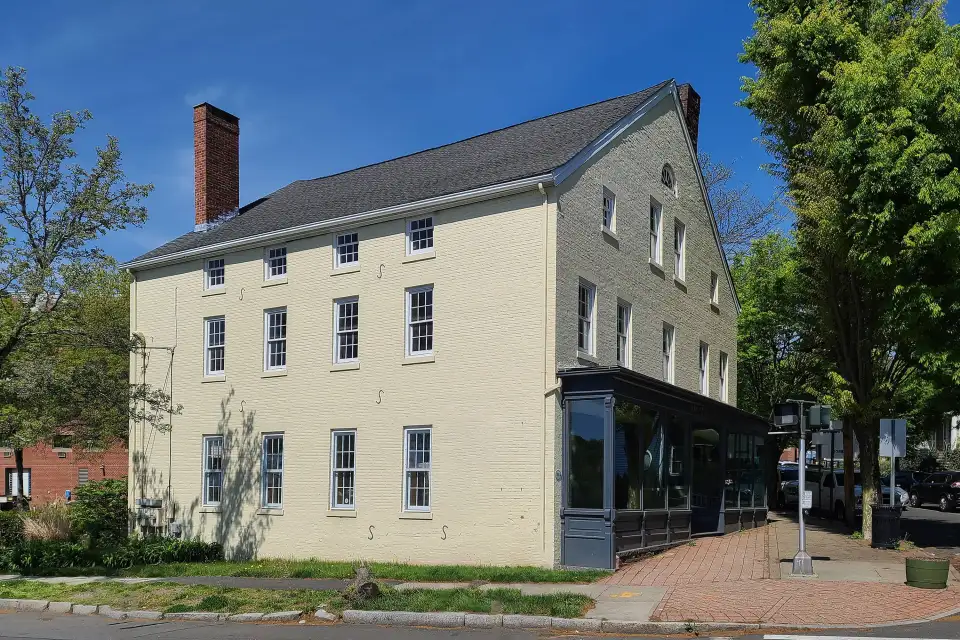
Patriquin Architects, based in New Haven, Connecticut, has occupied our historic office building for five years. During that time we have experienced firsthand its leaky envelope, poor air quality, and the inefficient mechanical systems that are housed within this beautiful three-story historic shell. Finally, we became determined to undertake a Passive House retrofit. We knew the retrofit would be full of unusual challenges, and we haven’t been disappointed in that regard.
The 1816 “King’s Block” building is the oldest remaining Federalist-style commercial building in our southern Connecticut area and has great historic significance to its neighborhood; the local Historic District Commission places strict regulations on exterior changes. In order to extend the lifespan of the 200-year-old building, minimize our energy impact, and improve our own interior environmental quality, we are pursuing PHIUS certification as part of our deep energy retrofit.
We knew from the outset that the retrofit would need to be carried out primarily on the interior of the existing brick envelope. Subject as this building is to the Historic District Commission’s restrictions, the only adjustments we are making to the exterior are four new penetrations for our ERV’s intake and exhaust. We are also replacing our front door and first-floor storefront glazing, switching to a highly-insulated door and triple-pane glazing units that very precisely match the design of the existing door and glazing.

Otherwise, the retrofit essentially builds a new envelope—walls, roof, and insulated first floor— within the existing one. Even the existing single-pane, double-hung windows will remain in the brick wall, acting as a sort of rainscreen for the triple-pane Alpen windows installed within our new inner envelope walls. The intensive interior work to the building required that it be vacant. We coordinated the retrofit with the remote work circumstances made necessary by the COVID-19 pandemic.
Partitioning the Building
A key early decision involved which elements of the building were to remain within the interior conditioned area, versus outside of it. The first decision was to leave the basement outside of the equation. Excluding it from the conditioned envelope makes sense, as the basement is characteristically damp for its age and its location, which is adjacent to a river, and there is no vapor barrier below its rat slab floor. The basement will house only large storage items, including the main electrical panel and a new heat pump water heater, which is expected to provide some key dehumidification. The basement ceiling will be insulated with 9 inches of dense-pack cellulose, installed above a new vapor-permeable air barrier.
The three main floors are laid out as separate tenancies, with two fire stairs connecting them that are tied into the existing exterior walls. In order to avoid complicated air sealing around this stair structure and minimize the interior conditioned area, we opted to leave these stairs outside of the conditioned envelope. Instead, the air barrier will run straight up the interior side of the newly insulated stairwell walls, behind a new insulated 2x6 wall cavity.
Refining the Ideal Wall and Roof Assemblies
Treating the existing roof and brick exterior walls as a shell, we have focused on creating thermally-robust assemblies on the interior. For the exterior walls, addressing the brick was the first challenge. After patching and filling areas that were structurally compromised, the contractors applied Sto Gold Coat, a fluid-applied air barrier, to the interior surface. This coating will act as the first line of defense against air leakage, while—given its vapor permeability—allowing the bricks to still dry out as part of our vapor-open wall assembly. The R-38 assembly includes a 2x4 framed wall held 3.5 inches off of the existing brick, with the resulting 7-inch cavity to be filled with dense-pack cellulose. A vapor-variable SIGA air barrier is located in between this 2x4 framed wall and a 2x3 service cavity wall, which will be filled with additional mineral wool insulation. This assembly will accommodate shifting electrical and data services in the exterior walls, as occupants and building use change over time, without sacrificing the air barrier.
After much back and forth with the contractor, PHIUS verifier, WUFI modeler, PHIUS technical team, and our staff, we opted for a vapor-closed roof assembly below our existing roof. This will include 3.5 inches of closed-cell spray foam below the existing roof sheathing and between the existing 5x5 rafters, with an additional 9.5 inches of dense-pack cellulose below, and a small insulated service cavity for wiring. The entire assembly will achieve a total R-value of approximately 60. We have also added closed-cell spray foam at the tops of the brick walls, where large gaps existed between the wall and roof eaves. While we would have ideally pursued a vapor-open and foam-free roof assembly, it became clear that given the inconsistencies with the roof framing and materials, that approach would have left us too vulnerable to water penetration. The additional R-value offered by the spray foam is also quite valuable, given the limited space at the eaves.
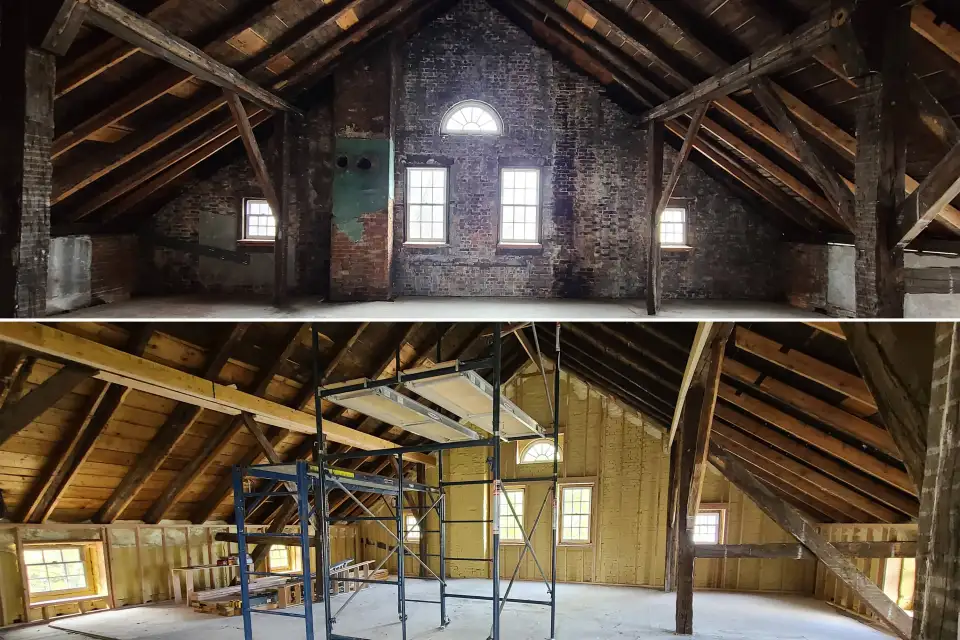
Mechanicals—fossil fuel-free and small
New Minotair Pentacare V12 units serve each of the three conditioned floors for ventilation, heating, cooling, and dehumidification. Given the building’s commercial status and evolving nature, a distinct unit for each floor offered the best strategy. These will stack in a series of small mechanical closets at the back of the building. In order to minimize exterior penetrations for intake and exhaust, the first and second floor share exterior louvers, requiring careful choreography of ductwork traveling vertically through tight existing spaces.
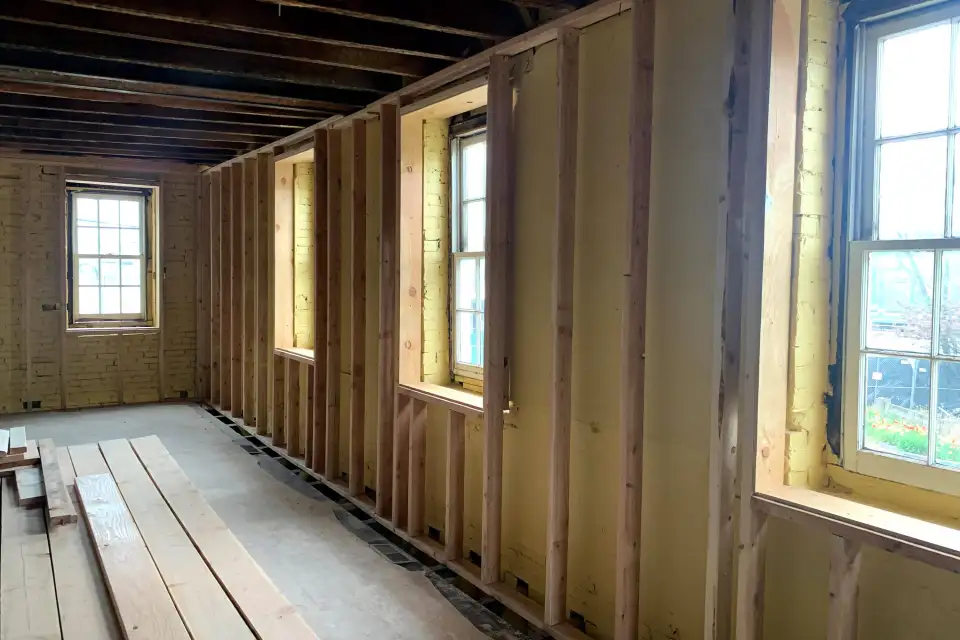
Electrical loads—reducing and supplementing
In order to meet our PHIUS source energy requirements—including balancing out the many computers and other office equipment installed in our space—we are expecting to install a 4-kW PV array as a canopy above the south entrance of our building. We are also replacing the existing lighting throughout with high-efficiency fixtures (targeting an installed LPD of 0.65 W/ft²), upgrading to Energy Star appliances, and considering new automatic shut-off procedures for our office equipment.
Demolition Yields Structural Issues
Demolition of the existing building interiors began in December 2020, following approval for the project by the local Historic District Commission. Demo involved the removal of existing interior furring and partition walls, a dropped ceiling below the roof, flooring throughout, plumbing fixtures, three large and inefficient gas-fired furnaces, and seemingly endless lengths of associated, and oversized, ductwork. Luckily, the ample holes between floors left behind by the ductwork will serve as key floor-to-floor connections during our whole-building blower door test. Also left behind was the beautiful heavy timber framing that runs through the building, which will remain largely exposed following the retrofit.
One of the joys of retrofitting a historic building is contending with the many structural irregularities that accumulate over the years. As the new envelope we are constructing will make the structure inaccessible for many decades to come, addressing any and all structural issues at this stage is critical. This work has included: removing and partially reconstructing a main brick chimney that was peeling away from the exterior wall under its own weight; fixing deteriorating masonry piers throughout; patching many openings in the masonry exterior that had contained doors or windows in a previous life; reinforcing our new 2x4 stud walls to accommodate bowing brick walls on the first floor; and cleaning up and reinforcing erratic structural framing in the basement ceiling and roof structure.
We hope that our new “interior exterior envelope”, combined with the extra attention being given to thorough structural repairs now, will help further lengthen the life of a beautiful historic building and provide resilient, comfortable spaces for future generations of inhabitants.