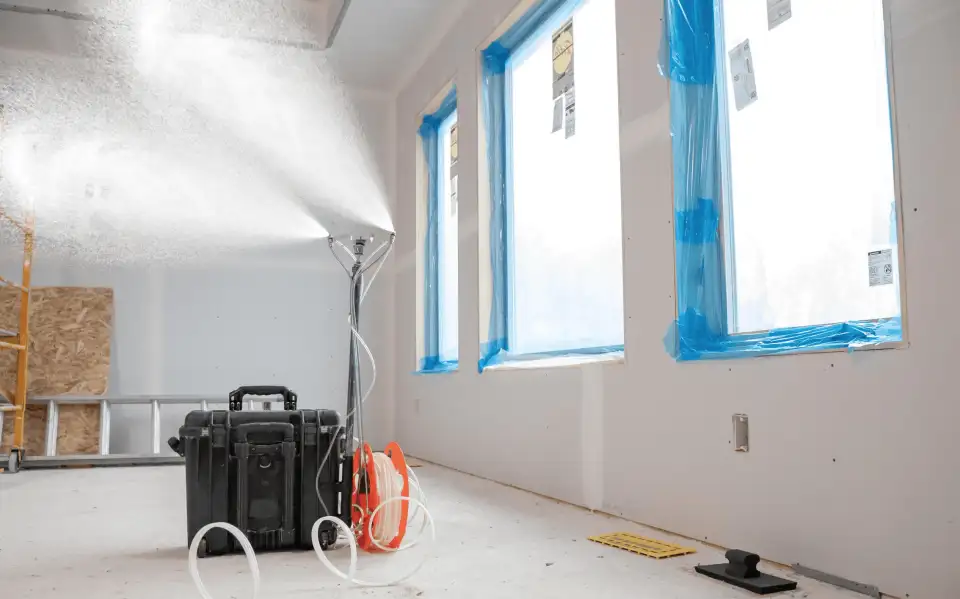
Air sealing is absolutely vital to high-performance and Passive House construction. No surprise, developing novel technologies and products that create airtight barriers are in high demand.
One of the most innovative products in air sealing today is AeroBarrier, which can achieve previously unheard-of levels of airtightness by pressurizing the conditioned space with a blower door, and then aerosolizing AeroBarrier’s non-toxic and GREENGUARD Gold certified sealant. The pressurization guides the sealant into every gap in the air barrier up to half an inch in diameter and as thin as a single strand of hair. The entire operation is overseen by certified technicians, who prep the building for pressurization, control the release of the aerosolized sealant, monitor the air leakage figures in real time, and run a final blower door test before cleaning up the space. The entire process is completed in a single day.
We recently had the opportunity to speak with someone who has experience using the AeroBarrier system, Lawrence Linder. Linder, a Passive House certified tradesperson and GC based in north Jersey, founded PH Airseal in late 2022. Since then, he has helped dozens of commercial, single-family, and multifamily buildings projects throughout the New York metropolitan area meet their airtightness goals with the assistance of AeroBarrier technology.
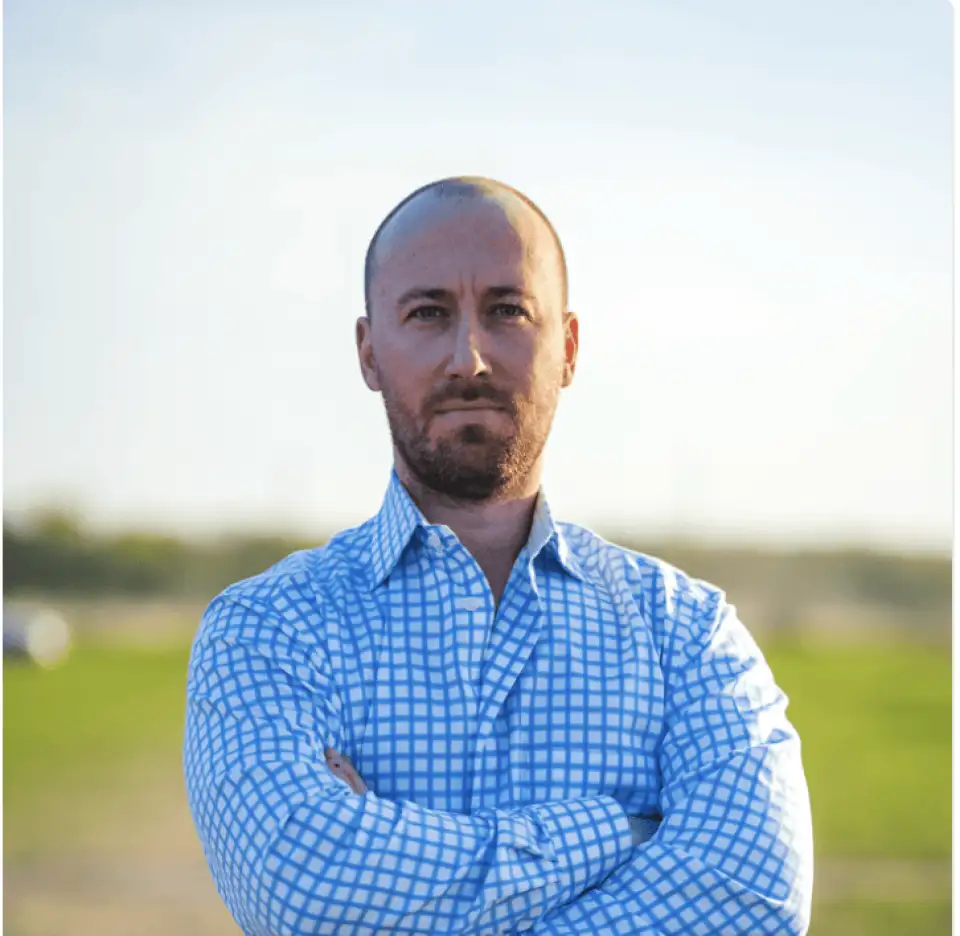
Passive House Accelerator: Thanks for taking the time to speak. To start, what drew you to the architecture, engineering, and construction industry?
Lawrence Lindner: I feel like it initially came from when I was a child just wanting to build things. As I got older, I would work over the summers painting with my father, and then moved into rough framing homes. I was always affected by old homes or older structures. I would get a literal feeling in my gut when looking at the details in the millwork and the exterior facades. I didn’t always know what I was looking at, but knew I liked it.
Fast forward a few years later and I’m living in New York City. Walking the streets was mind-blowing. There were all of the hidden details, like corbels made from gargoyles sticking their tongue out. They were Useful pieces but done with style and a sense of humor that you just don’t see that often anymore. At times it absolutely racks my brain thinking of all of those elements that came together to make these historic buildings.
PHA: What drew you to high-performance buildings?
Linder: I think it’s an appreciation of buildings in general. I simply wanted to build a better product. Building is really personal for me, and I don’t want to build everything that comes across my desk. I want to believe in the product that we’re putting out. That’s just how I’m wired. It’s a challenge to myself and my subcontractors from a GC point of view, but I want to be able to build something that has more thought than other buildings. I want to build something that is going to live longer, and that will allow those inside of it to live better—in this case healthier—lives.
PHA: How did your experience as a GC shape your understanding of the needs of the industry, especially with respect to improved means of air sealing?
Lindner: As a GC, I’m always attempting to get better. It doesn’t matter if it’s continuing education credits through classes and webinars, or just listening to podcasts. Collectively, you will always hear the two most important attributes for a high-performance home, or a well performing home, are they keep water out and they have a high level of air sealing. With that knowledge, being introduced to AeroBarrier products and seeing the direction of code changes, I feel being able to offer this service to my area is immensely valuable.
PHA: How were you first introduced to AeroBarrier?
Lindner: I saw AeroBarrier at the International Builders’ Show in Las Vegas. After speaking to the company and seeing the presentation, I was blown away.
PHA: How does it work?
Lindner: In short, our sealant fills all the gaps and cracks where there is air leakage. In order to do this, we first pressurize the home with 100 pascals. We then start to spray our sealant. The sealant is only attracted to the spots where there is air leakage. At that point, it starts to seal and continues to fill in any gaps until we bring the reading down to the desired ACH50 or CFM.
PHA: What’s the biggest change in ACH50 you’ve seen in score before and after using AeroBarrier?
Lindner: We saw one ACH50 drop by 10, from 11.5 to 1.5.
PHA: What’s the best ACH50 score you’ve ever seen?
Lindner: PH Airseal’s current best is a 1.3 ACH50. That said, we haven’t had anyone say, “Get this as low as you can.” [If there are any takers on this, please contact both Lawrence and someone from the Accelerator, because we want to be there to see the results.]
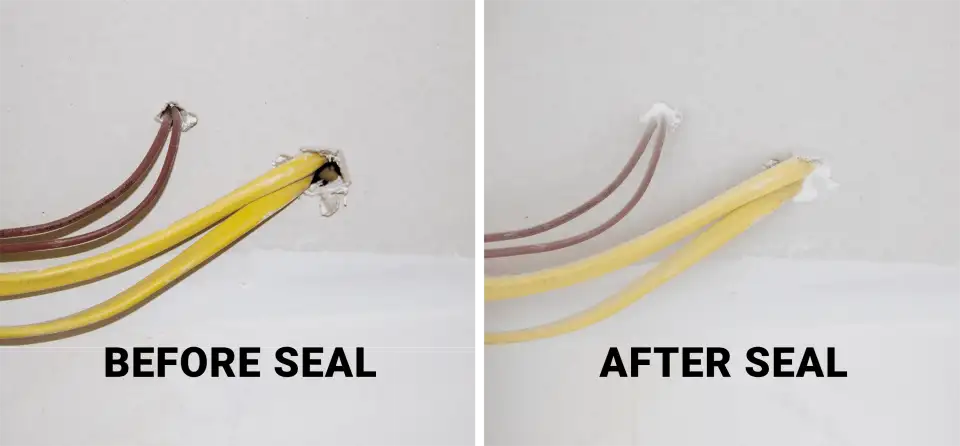
PHA: How many square feet of space can you typically seal within a day?
Lindner: It depends on the initial amount of air leakage and the desired final reading. As a rough estimate, I’d say code compliant projects would be between 10,000 and 20,000 square feet per day. For high-performance projects, it would be between 7,000 and 14,000 square feet per day.
PHA: How quickly does it usually take to seal a single-family home? A multifamily or commercial space?
Lindner: Again, it depends on initial reading and target number. That said, a single-family project is usually going to need 4 hours of spray time. For a multifamily compartmentalized unit, it will likely need 1 hour of spray time. There are just too many variables for a commercial space, so I can’t say.
PHA: Are there steps that crews can take to help your team get the job done quicker?
Lindner: Yes. For new construction, stay on top of the drywallers and the tapers, and keep the cuts close to the electrical boxes or penetrations. Have the worksite clean and free of debris and dust as much as possible. Do a good job on the building envelope.
PHA: Building codes are getting stricter in places like New York City. Do you think other parts of the country will follow suit?
Lindner: This is a whole can of worms here, but building codes have to get stricter. This isn’t as simple as code changing on the local level. In my opinion, it needs to be first done at a federal level to set a simple minimum code standard for all new construction at 2021 IECC [International Energy Conservation Code] levels. For me, that’s the first thing. We should also make it a standard to get a builder’s license where you have to pass a basic knowledge test—not just show insurance and pay a license fee.
Beyond these very simple ideas, the INSPECTORS NEED TO INSPECT! There is so much that goes into construction, but at the end of the day, it doesn’t matter what the code is—it matters what is being actually inspected. Architects can specify everything on the plans all day long, but if builders are not being inspected, none of it matters.
To contact PH Airseal, you can visit their site (here), call (845) 416-4933, or contact Lindner by email ([email protected]).