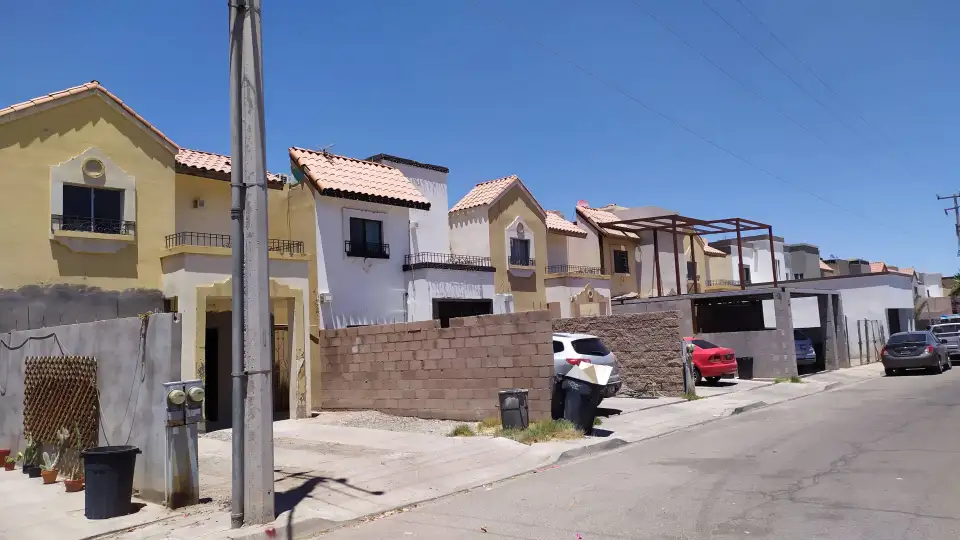
Mexicali and Hermosillo, two cities in northern Mexico, share a hot dry climate with temperatures that reach up to 52°C (125°F) during the summer. They are also home to large social housing developments, some of them recently built, of up to 10,000 single-family homes constructed typically of concrete blocks or reinforced concrete slabs, with single-pane aluminum-framed windows—and no insulation whatsoever. Indeed, the majority of Mexico’s housing stock—currently about 35 million houses—do not meet all the federal building code requirements and were built with no attention to energy efficiency.
As residents in Mexicali and Hermosillo are forced to suffer with life-threatening indoor temperatures, homeowners buy and install second-hand air-conditioning systems to cope with the high temperatures, leading to high energy bills and energy poverty.
A pilot project was implemented to retrofit 30 houses in the social housing parks of Hermosillo and Mexicali, through the Trust for Thermal Insulation, FIPATERM, a branch of the state-owned electricity company, CFE. The project was conducted as part of the Energy Efficiency and Renewable Energy in Existing Social Housing in Mexico Program, commissioned by the German Federal Ministry for Economic Cooperation and Development (BMZ) and implemented by the German Agency for International Cooperation (GIZ). GOPA Infra, on behalf of GIZ, provided technical assistance in the conceptualization and implementation of the pilot project.
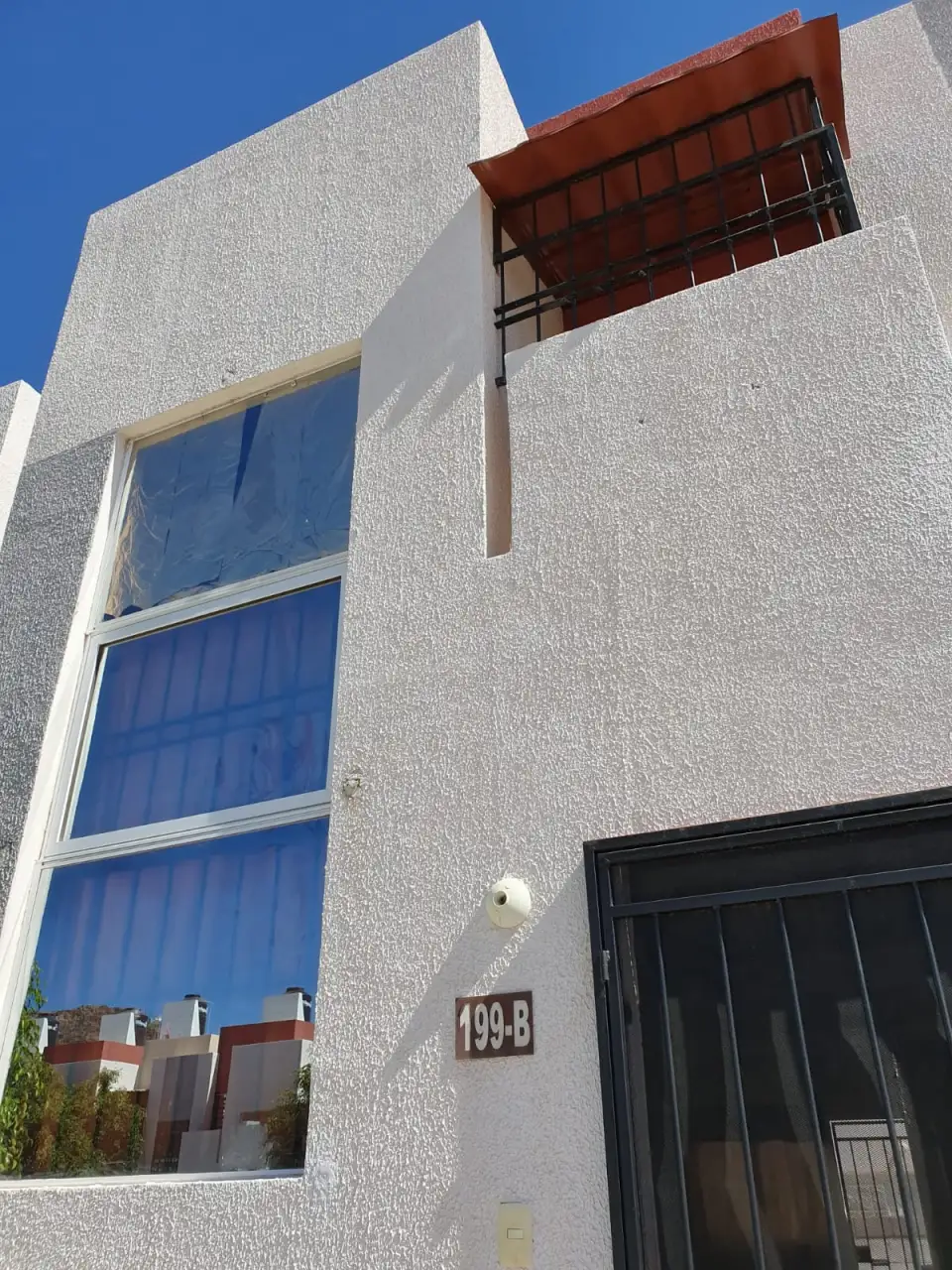
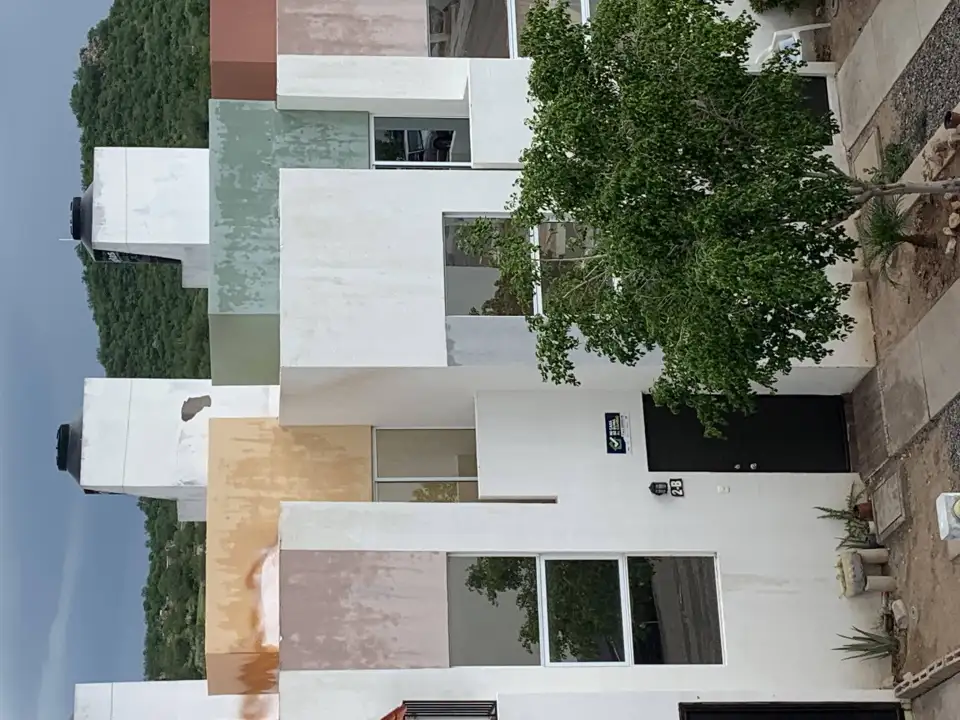
The pilot’s objective was to develop energy retrofit packages, evaluate their technical and financial feasibility, and identify the most suitable mass-scale bundle of energy efficiency and renewable energy measures that would achieve the optimal energy performance for these social housing developments. The homeowners that participated in the project were offered a subsidy to cover some of the retrofit costs, coupled with a 5-year loan that had an annual interest rate of 13%.
Three retrofit packages were designed and implemented, ranging from a low investment scale (Step 1), to intermediate (Step 2), to a more ambitious level of investment and energy performance (Step 3). These packages were conceived as steps towards an EnerPHit, with the Step 3 bundle the closest one to achieving an EnerPHit level of energy savings and thermal comfort.
Step 1 included exterior thermal insulation on the roof (λ 0.028, 1.25 inches) installed in combination with white elastomeric paint on the roof’s surface, an energy-efficient air-conditioning system, energy-efficient appliances, and water-saving fixtures. Step 2 added exterior thermal insulation, along with reflective paint, on the walls (λ 0.038, 1.5 inches); in addition, the participants selected a package of an induction cooktop, an electric boiler, and a PV system to replace the gas-consuming devices, testing the concept of a home with a 100% solar electricity supply. Step 3 further included a heat-recovery ventilation unit, low-e double-glazed PVC windows, and the application of airtight sealing tapes.
Airtightness control was implemented through these sealing tapes, along with attention to sealing of penetrations and adhesive mortar for sealing surfaces. Such airtightness measures have proven to be low cost and, in the pilot, showed excellent results on the pressurization test. A post-retrofit blower door test conducted by Micheel Wassouf of Energiehaus on the one house where all the Step 3 measures were installed showed the house had achieved an airtightness of 0.91 ACH50, complying with the requirement of the EnerPHit standard. Continuity of thermal insulation at the junctions of the walls and slab assured control of the existing thermal bridges.
Table 1 shows the implemented bundles for each step, with the total energy demand for cooling and heating, non-renewable primary energy demand, CO2 savings, and U-values for thermal insulation and windows, compared to the houses before the retrofit intervention (Baseline) and also to both the EnerPHit energy demand criteria and the EnerPHit component criteria. All the retrofit solutions were modeled using PHPP and DEEVI, an energy balance tool developed in conjunction with PHI specifically for social housing typologies and the climates of Mexico.
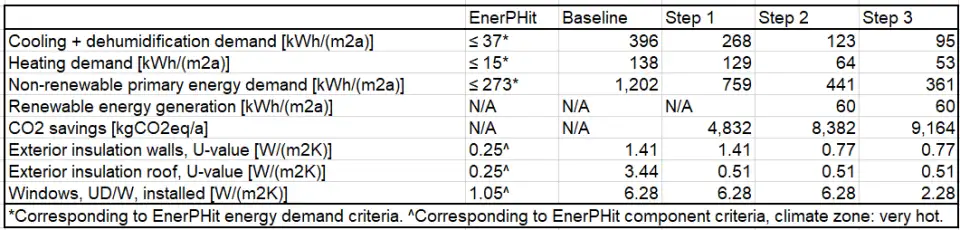
The electricity bills of four houses were monitored for the period of July to December 2022. As shown in Table 2, energy reductions of 1,912 kWh (Step 1 Hermosillo), 1,928 kWh (Step 1 Mexicali), 4,236 kWh (Step 2 Mexicali), and 6,828 kWh (Step 3 Mexicali) compared to the same month of the previous year were achieved for these houses. Step 1 led to energy cost savings of 45%, while Steps 2 and 3 saved up to 45% to 82%, correspondingly, of the energy bill.
Furthermore, the Step 3 house showed excellent levels of indoor air quality. In addition to significant energy savings, those homeowners are experiencing the added benefits of comfort and health associated with having a well-insulated airtight building.
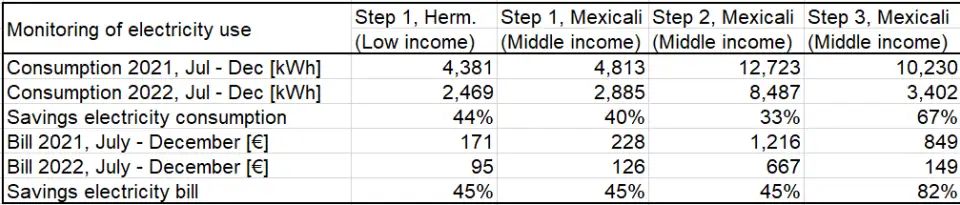
A cost study was performed to examine the financial feasibility of implementing a step-by-step energy retrofit (see Table 3). Regarding the Step 3 house, the intention was to study the technical and financial feasibility of achieving a fully retrofitted house that complied with the EnerPHit standard. The five Passive House principles—airtightness, thermal insulation, thermal bridges, efficient windows, and controlled ventilation with heat recovery—guided the optimization concept, while still taking into account the project’s boundary conditions.

The goal of implementing the five principles ran up against significant barriers in Mexico regarding two of the components needed to comply with the EnerPHit standard: triple-glazed certified windows and mechanical ventilation units with heat recovery, which were simply not locally available. As this pilot was being conducted during 2021-2022, there were also significant delays in the production and shipping of international products—not to mention important incremental costs—due to the Covid-19 crisis and the war in Ukraine. Therefore, for the windows, the best locally available products were selected, which consisted of tilt-and-turn windows with three-chamber PVC frames and low-E double-glazing. Eventually, it was feasible to import from Germany a PHI-certified heat recovery ventilation unit to be able to include proper airtightness control and the ventilation concept.
As for thermal insulation, the economic analysis, considering the current electricity tariffs, favored 2 inches of XPS exterior roof insulation (U-value 0.35 W/(m2K)) over 3 inches of XPS exterior roof insulation (U-value 0.25 W/(m2K)). However, due to the financial objectives that FIPATERM had to achieve, and the terms of the grant agreement, the system offered by FIPATERM-accredited providers of 1.25 inches of sprayed polyurethane (PU) (U-value 0.51 W/(m2K)) had to be used instead of the modeled XPS solution. As for the floor slab, it was not technically feasible to insulate the floor slabs, which are in contact with the ground.
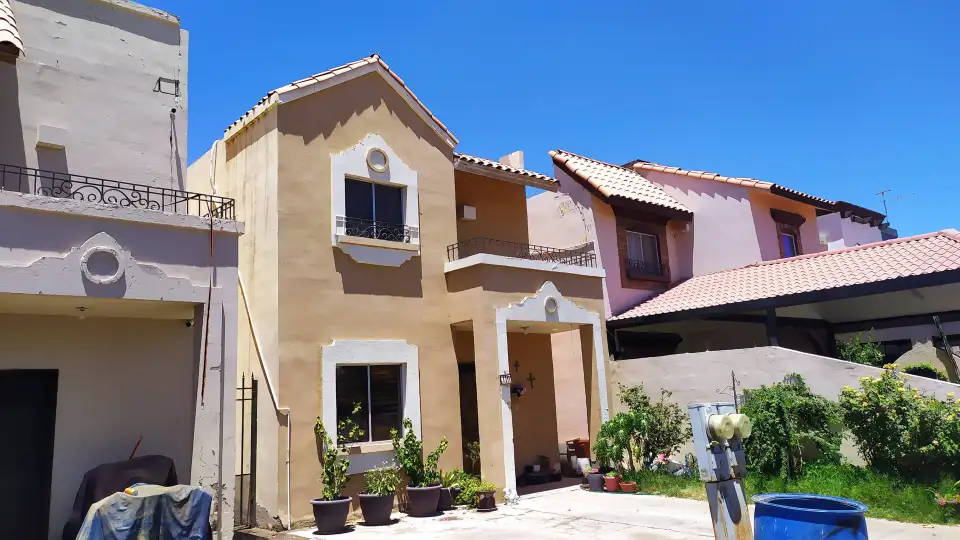
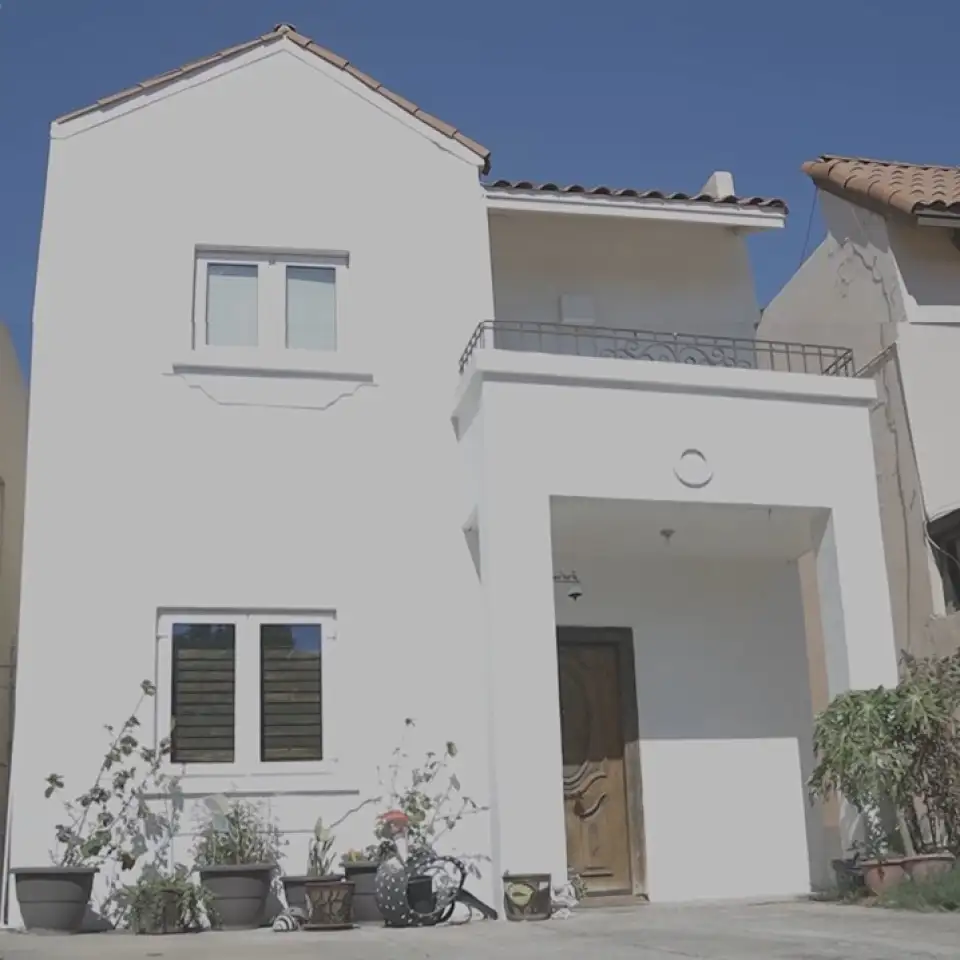
The lessons learned from this demonstration project regarding overcoming the existing barriers to achieving EnerPHit include the supply and installing of PHI-certified components. Barriers to more broadly implementing airtightness measures could be addressed by importing sealing tapes at a low cost and training local workmanship to install them. Decentralized HRV units could be produced in Mexico by involving local manufacturers, who could design and produce models for the social housing segment. Local air conditioning and mechanical ventilation installers could be trained to assure proper installation. The cost barrier for highly efficient PHI-certified windows, especially for the social housing segment, could be overcome by locally adapted design and production. These solutions would incentivize the development of a national market and trigger the expansion of mass-producing Passive Houses.
Long-term financing solutions that include lower interest rates are necessary to achieve a positive net present value for these types of retrofits. The Step 2 and Step 3 retrofits were heavily subsidized from a grant agreement with funds of the German Federal Ministry for Economic Cooperation and Development (BMZ) and implemented by GIZ. This pilot opens the discussion for future solutions to overcoming the technical and economic barriers for efficient, comfortable, and healthy mass-produced social housing in developing economies, while avoiding the lock-in effect from installing not-so-efficient retrofit measures. Financing mechanisms such as international climate funds could be coupled with state incentives and lower interest rates, leading to affordable solutions for the existing housing parks of Mexico and leaving no-one behind.
Videos about this project are available at https://youtu.be/dsnaM3HrfLk and
_________________________________________________________________________
FOR MORE INFORMATION on the pilot project, please contact Salvador Rodríguez Kuri and Albert Beele, at [email protected] and [email protected].
FOR FURTHER INQUIRIES about the program, please contact Liliana Campos, program director of the GIZ Program Energy Efficiency and Renewable Energy in Existing Social Housing in Mexico, at [email protected].