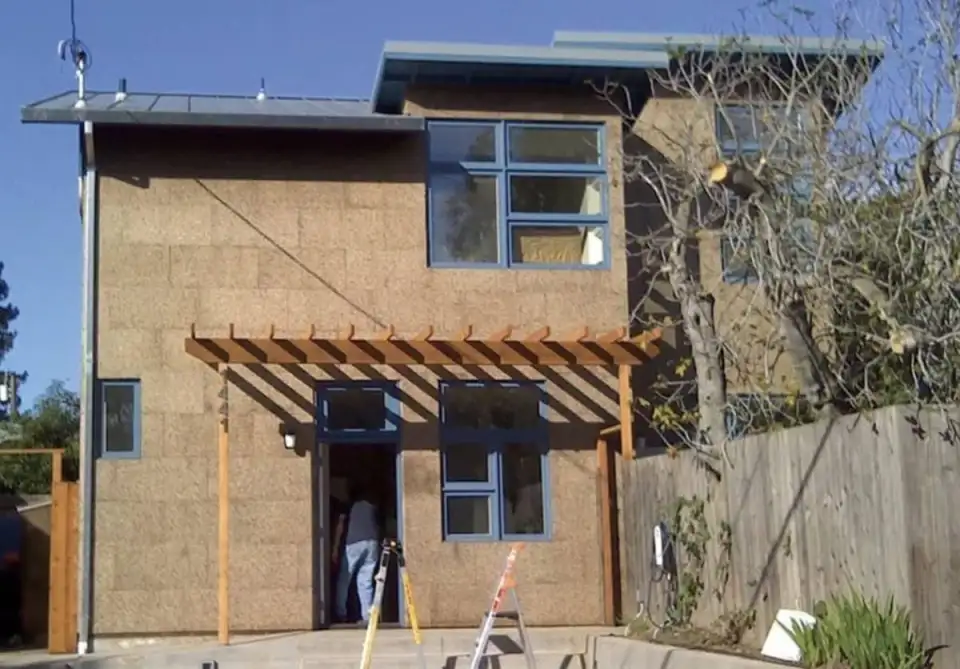
Certified Passive House buildings are not yet a trend in the San Francisco Bay, despite the region’s tendency to embrace techy innovations. This slow uptake is partly due to the mild climate: Passive House certification seems superfluous to many high-performance builders. Ian MacLeod of MacLeod Design & Construction is ahead of the curve, having built and certified two Passive Houses in Berkeley within the past three years.
The impetus for both projects was the clients; they each wanted significant performance. In the case of the Berkeley Way two-story accessory dwelling unit (ADU), a 1,000-ft2 cottage designed for an elderly parent, the clients were easily convinced that certification made sense. In the case of the larger, 3,324-ft2, three-story gut remodel located on Los Angeles Avenue, the engineer-trained client knew from the beginning that he wanted a Passive House.
MacLeod was introduced to Passive House basics by his colleague Nabih Tahan, one of the earliest Passive House pioneers in the Bay Area. Tahan was the architect and builder for the first Passive House retrofit in California. As a builder and architect, Passive House construction made sense to MacLeod. He just had to wait for a suitable project.
Berkeley Way
The Berkeley Way project is located in the relatively flat area of Berkeley close to the Bay Area Rapid Transit system, perfect for the elderly occupant of the house. It was originally designed and had zoning approval by another architect as traditional housing. MacLeod took over the project to do the building permit plans and eventual construction. Once the Passive House goal was set, he redesigned aspects of the house, in consultation with consulting firm Beyond Efficiency, to clarify air and water barrier and insulation details and optimize the glazing.
The modern, angular design is a model of two-story efficiency designed for primarily one occupant, with a second bedroom for visitors. The building shell is typical for a Bay Area building that meets Passive House criteria: 2×6 dense-packed walls with 2 inches of exterior insulation, and 2×12 TJI dense-packed roof rafters, also with 2 inches of exterior insulation above. Current local building practices favor insulated slabs. Location in an earthquake liquefaction zone calls for thicker slabs, generally on the order of at least 8 inches. Berkeley Way only required a 5‑inch reinforced slab with 2 inches of EPS underneath and 1 inch around the perimeter.
The building sheathing is covered with a liquid-applied air and water barrier. To help maintain the integrity of this barrier, a second layer of roof framing was laid over the roof sheathing, with the exterior insulation laid in between the framing. This strategy made it easy to provide overhangs for rain protection and shading where needed without compromising the air and water barrier.
The original plan was to cover the walls with one and one-half inches of foam coated with stucco. During construction, the clients opted for cork instead, because of its sustainability compared to extruded polystyrene (EPS) foam. MacLeod realized that the cork could actually be used as the exterior finish. The additional cost of the cork was basically offset by the savings from not having to apply the stucco finish. Everyone involved with the project is quite pleased with the result.
The mechanicals are standard fare for small, high-performance Bay Area buildings—a mini-split heat pump for heating and cooling, a heat pump water heater for domestic hot water, and an HRV for ventilation. According to MacLeod, due to the advance consideration of the details, there were no significant challenges while building the house.
The only real hiccup was figuring out the dampering on the kitchen range hood. There was quite a bit of debate prior to construction about installing an electronically-activated in-line damper. The winning solution was to install a magnetic damper on the outside that only opens at pressures above 60 Pascals. This configuration stayed closed during the required blower door testing, but opens when the range hood fan is turned on. Initially, this didn’t work as expected—the damper opened at lower pressures. A few small magnets were added to solve the problem.
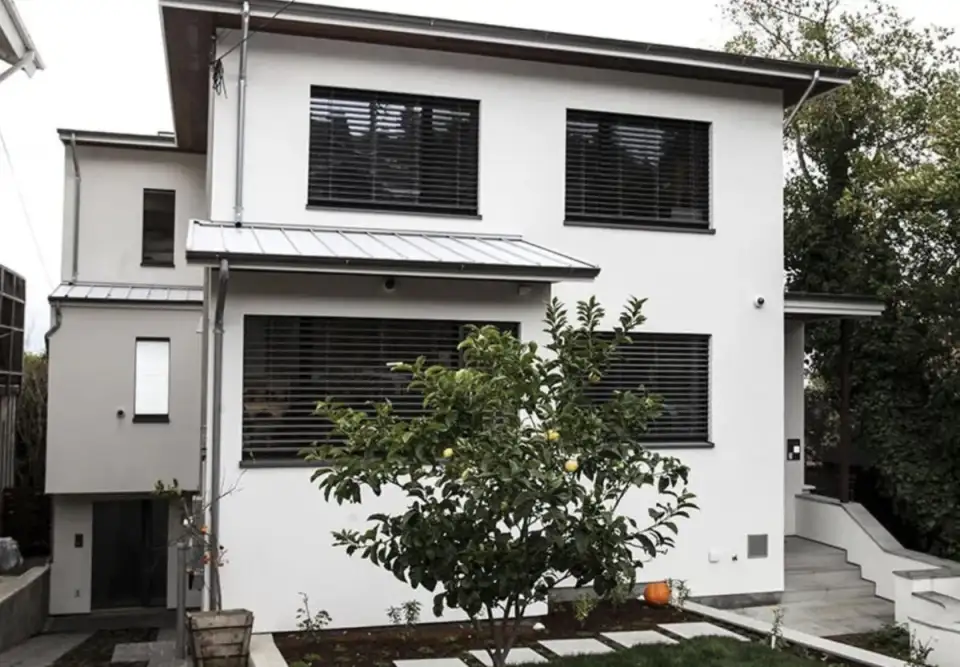
Los Angeles Avenue
The Los Angeles Avenue project was much more challenging for a variety of reasons. It was an existing house in the Berkeley Hills that was essentially gutted. The top floor and roof were removed and rebuilt. All interior and exterior finishes were removed. Window sizes and locations were all changed, many taking advantage of views across the San Francisco Bay to the Golden Gate Bridge. Floor plans were redesigned to accommodate a family of four with open, workable spaces. The ground floor includes a second kitchen and fully outfitted apartment for visitors.
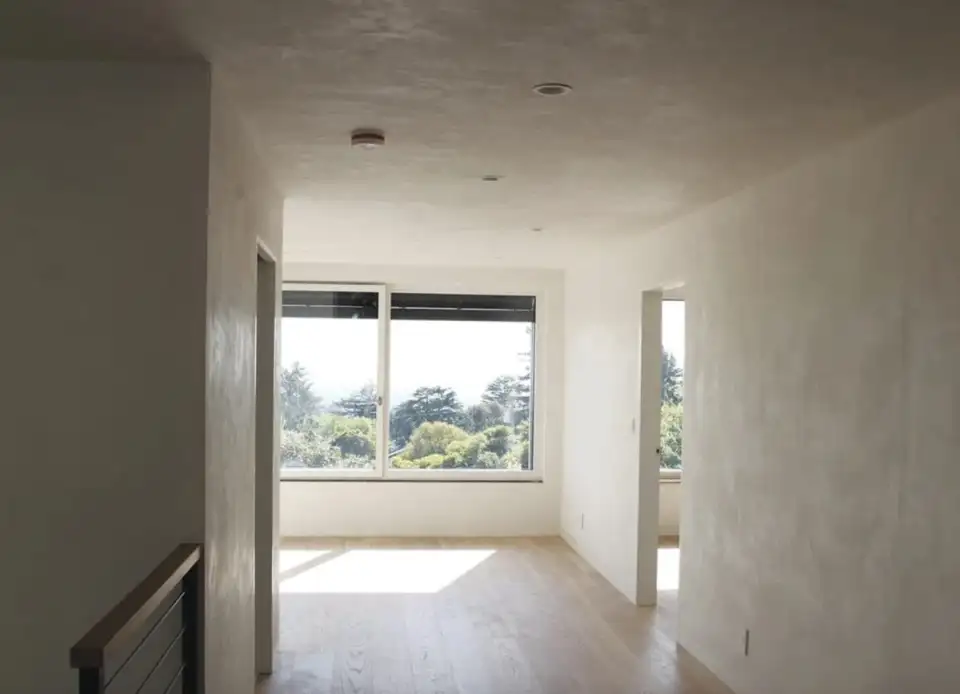
Although this project could have been modeled and certified as an EnerPHIT project, MacLeod and his client decided to pursue full Passive House Plus certification. The biggest difference between these two certifications is the infiltration rate. EnerPHIT projects can be certified at 1.0 Air Changes per Hour (ACH50). Classic Passive Houses have a lower infiltration threshold of 0.6 ACH50.
This ambitious goal translated to some significant challenges during air sealing. There were a variety of situations where new framing components were married to old framing (all exterior sheathing was removed), and access to some of the old components was limited. Several weeks of air sealing work, with multiple rounds of blower door testing, ensued, and some very creative approaches were required. For instance, the first-floor subfloor and framing cavities had to be fully coated with a liquid air barrier product to seal the intersection with the existing unconditioned mechanical room below. The project team eventually reached an admirable infiltration rate of 0.4 ACH50.
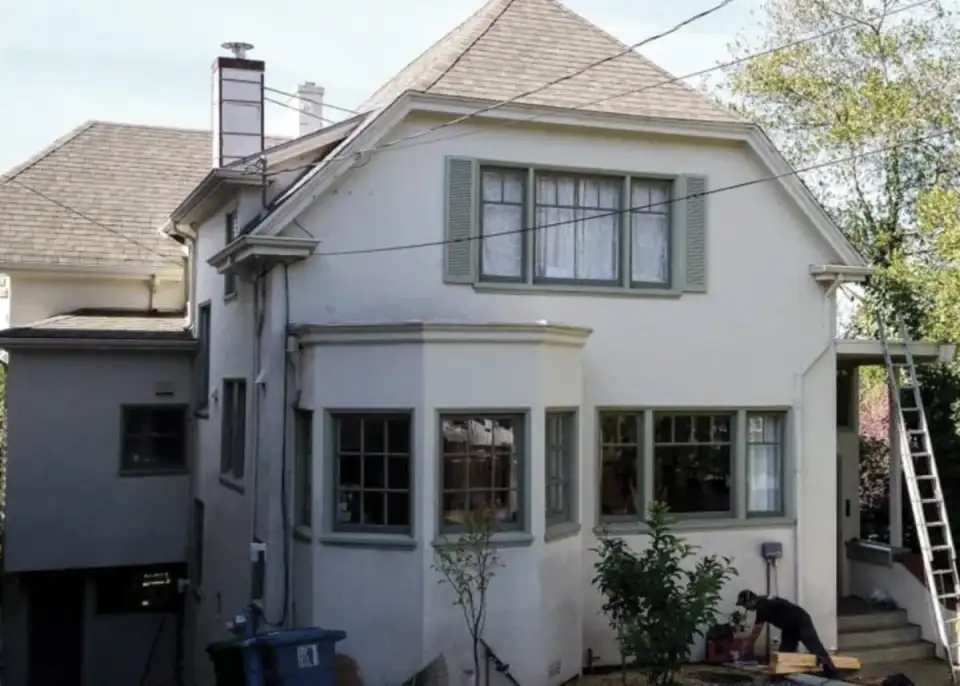
There are quite a few very large windows on the resulting structure (the window-to-square footage ratio is over 31%). Just getting the windows to the upper floors required lots of elbow grease. Many of these windows are on the western elevation to take advantage of the views. Unfortunately, that can lead to overheating. To mitigate the siting, electronically controlled exterior blinds were installed on the western windows.
The wall assemblies are a complex mix of new and existing walls with additional interior framing and insulation. Existing walls were built out from 2×6 to as much as 2×10 depth; 90% of the walls are 2×8. All insulation is blown-in cellulose. For exterior insulation, MacLeod once again used cork. The rear southwest and front northeast-facing walls have 6 inches to accommodate the depth of the exterior shades. The side walls have 1 inch of cork. The roof structure is similar to the dual roof assembly that MacLeod used on the Berkeley Way project—dense-packed 2×12 TJI rafters topped with sheathing, then a secondary vented roof structure insulated with 2 inches of mineral wool between the framing.
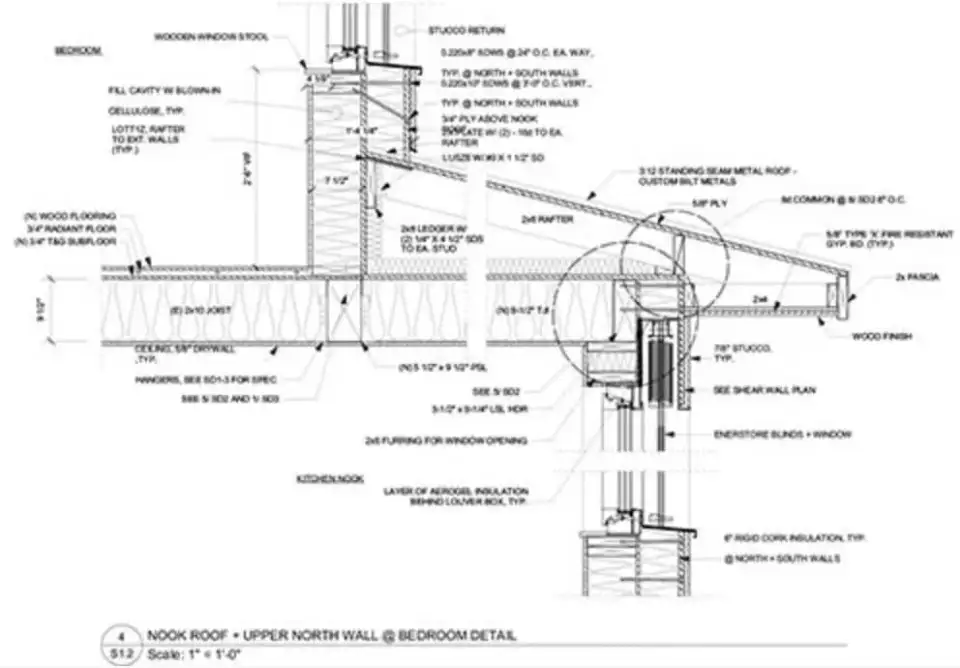
Ventilation is provided by a large HRV in the basement mechanical room. All floors have radiant heat powered by a heat pump water heater that also provides domestic hot water. The radiant heat system is rarely used. A detailed analysis was done to determine electricity consumption and properly size the 10.8‑kWh PV system that was installed to make the home a net zero energy dwelling, including an electric car charging station. In a nod to the owner’s sensitivity about harmful environmental characteristics, the bedrooms are EMF shielded.
Both of MacLeod’s projects demonstrate that the most successful residential Passive House projects tend to have a tightly integrated team. This is easy to achieve when the architect is also a hands-on builder.