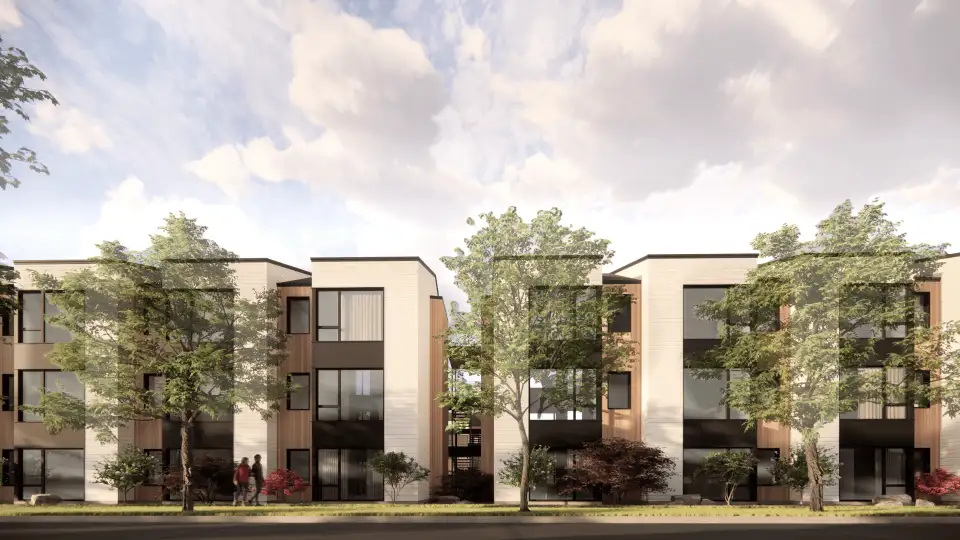
It’s a whirlwind of activity at the office of the Artisans Group Architecture and Planning in Olympia, Washington—the temporary office, that is. The 11-person practice, which is headed up by Tessa Bradley and Roussa Cassel, currently is operating out of a 900-ft2 former home, but plans have been submitted for a new building on the front portion of the property that will allow the team to expand into a more reasonable 2,000 square feet of space. The new office will occupy the ground floor of a three-story building that will include six units of market-rate rental housing on the top two floors.
Will it be built to Passive House standards? Of course! Constructed using prefabricated panels? Naturally. “That’s 90% of what we do,” says Bradley. The Artisans Group was an early Passive House adopter and has become known for its seamless intertwining of building science and outstanding design. Its passive projects, once entirely single-family homes in or near Olympia, now come in a variety of building types and can be found throughout Washington, Oregon, and even as far away as Texas.
Groundbreaking on the firm’s new, 6,000-ft2 mixed-use building likely won’t commence until late 2023, but when it does, it will be built using the same assemblies found in many of the firm’s single-family projects. For a couple of years now, the team has been working closely with Collective Carpentry, a prefabricator of high-performance wall and roof assemblies, and says Bradley, “I’m very comfortable with their system, and I like cellulose.” Collective Carpentry’s standard panelized wall assembly basically consists of a TJI filled with dense-pack cellulose hanging off of an open-framed structural wall. The group has finished two homes built with Collective Carpentry’s panels, has three under construction, and has about a dozen others that are in various states of completion.
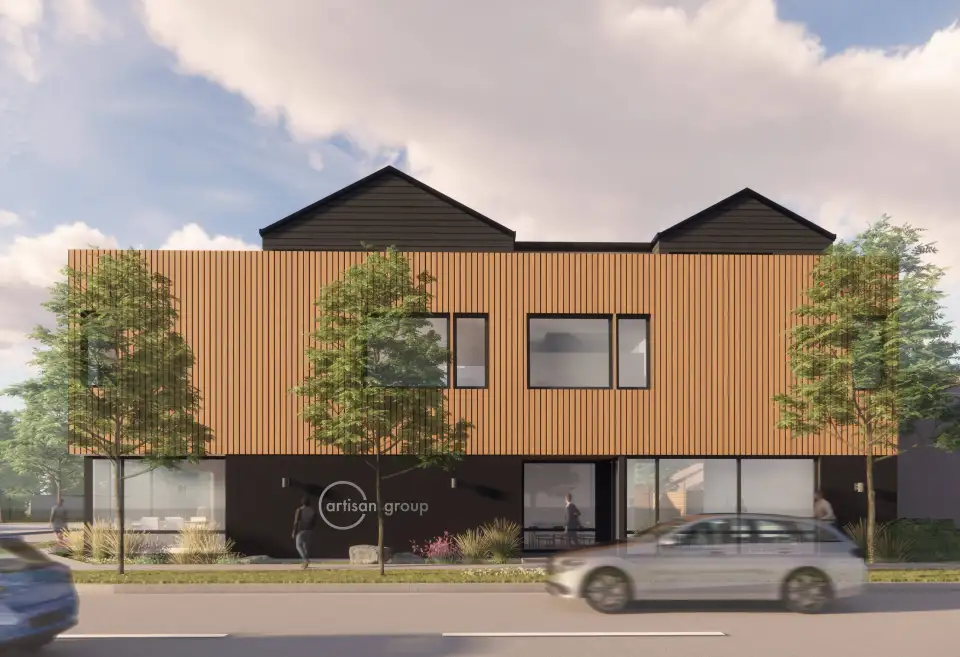
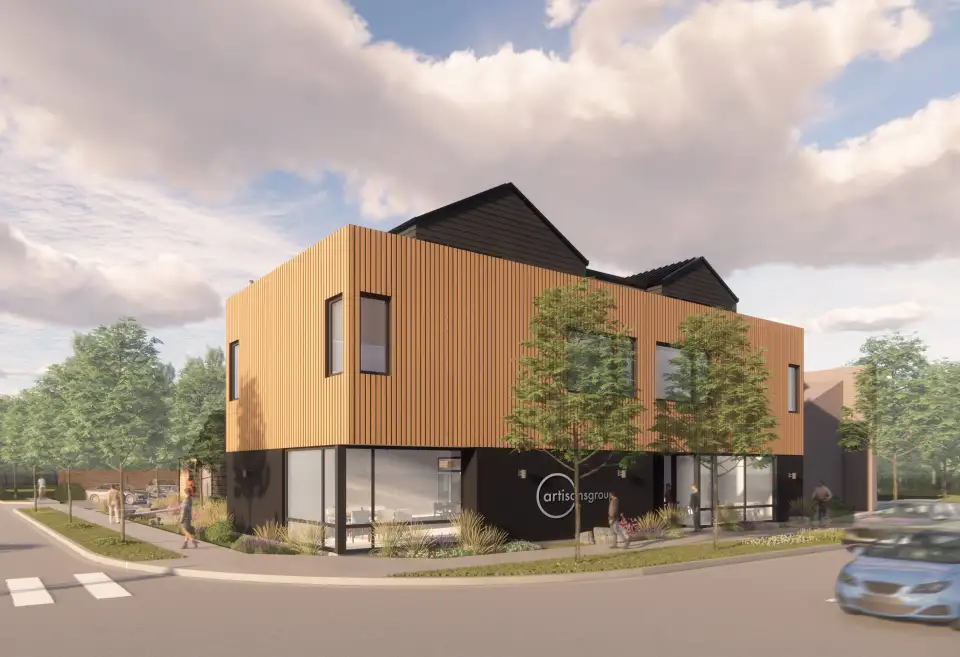
The office building’s design process was a quick wrap, as Bradley and Cassel were doing it in their spare time, which they point out is pretty much non-existent. “And, maybe we already know exactly what we want,” Cassel adds semi-jokingly, “We made some creative choices.” One of those is working with Collective Carpentry to specify a thinner-than-typical wall assembly for the first floor—the commercial portion—and the standard thicker wall assembly for the two residential floors above. The first floor’s 2x8 walls will still be superinsulated, with 4 inches of rigid insulation on the exterior, followed by an absolutely standard rain screen gap beneath the siding. “The climate is very wet in here in Olympia. We have 20% less sun than Seattle,” notes Bradley drily.
Designing for themselves allowed the pair to try out a product they don’t normally get to use. The new office’s ceiling will feature exposed CLT and glulam beams chosen for their beauty and their brawn, as they will be distributing the structural loads.
Another project getting squeezed into nonexistent spare time is the completion of Cassel’s home. The shell of this 1600-ft2 home was erected in a matter of days from panels shipped from Collective Carpentry in January of 2022. “That’s allowed my partner and I to self-perform the rest of the project,” says Cassel, who is planning to move in in March 2023. This DIY approach may not work out for everyone, but this project’s success is guaranteed, given the twin talents of Cassel and her partner, a general contractor.
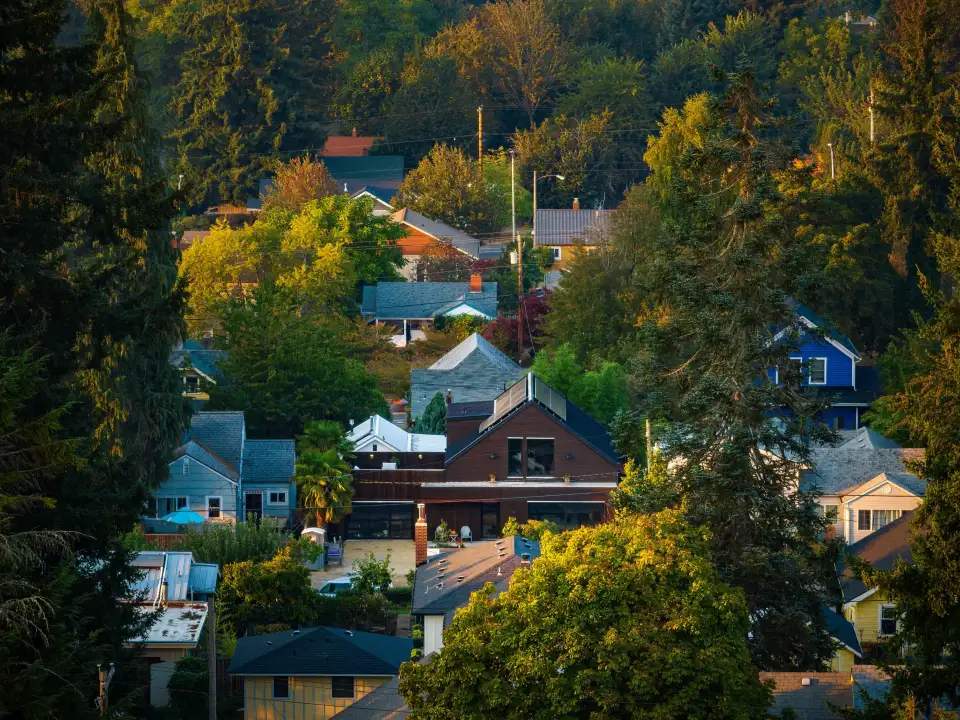
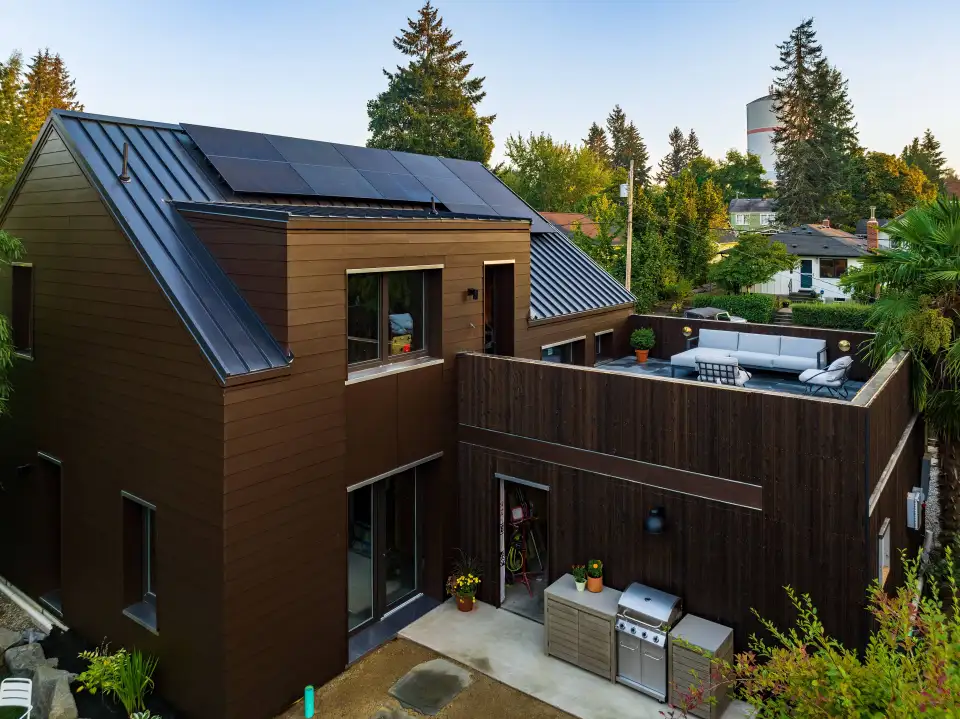
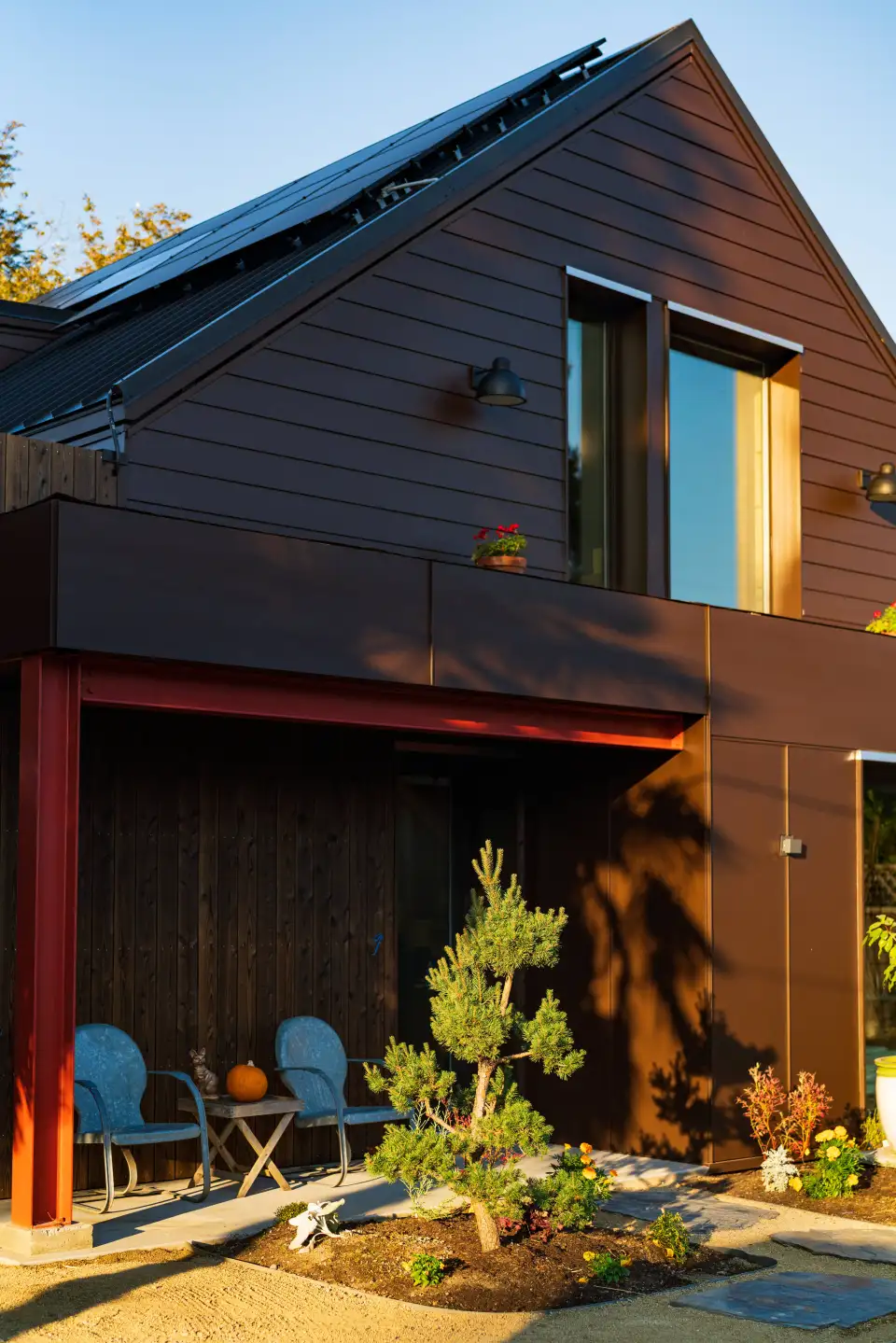
While single-family homes have been the firm’s Passive House bread and butter, the group is also working on a number of larger passive multifamily projects and is currently immersed in designing what could be their largest yet: an entire neighborhood in Olympia for Habitat for Humanity. The 10-acre neighborhood will add 123 units of affordable housing for middle-income residents who otherwise can’t afford to buy in this city; potential Habitat homeowners earn 30-80% of the area’s median income. “A single parent with two kids that is a teacher could be a Habitat homeowner—nurses, medical assistants, people who make our community work,” says Carly Colgan, CEO of South Puget Sound Habitat for Humanity.
This property, which the chapter acquired from the city for a nominal fee, is the largest one this chapter has ever taken on, and the planned development includes a number of building types that are new to it. There will be 48 apartment-style units in 4 multifamily buildings, 48 townhouses, 27 senior cottages, and a 3,000-ft2 community center. “I’m a firm believer that the right people come into our organization at the right time to help us on our journey,” comments Colgan, referring to the Artisans Group. The group has been collaborating on two other Habitat developments—28 townhouses in Tumwater and a 22-unit property in Yelm.
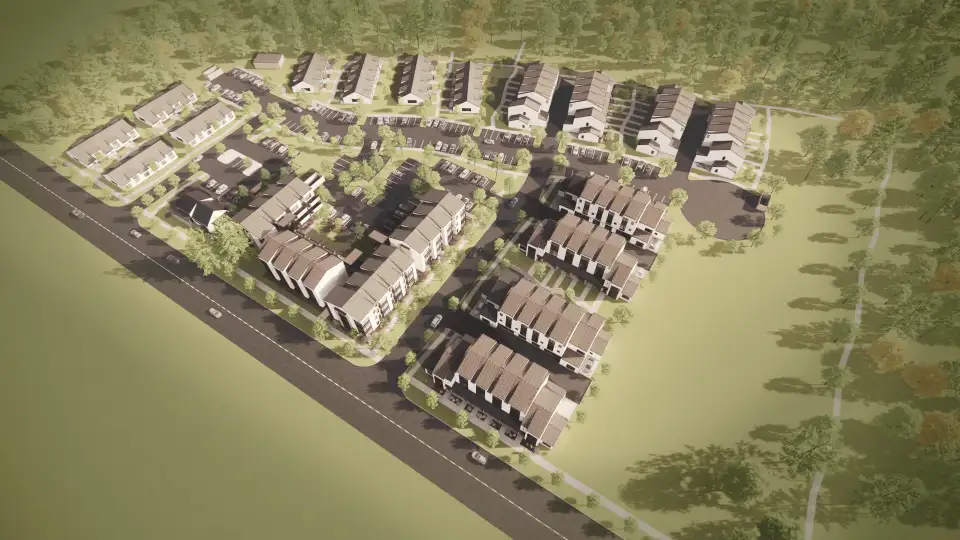
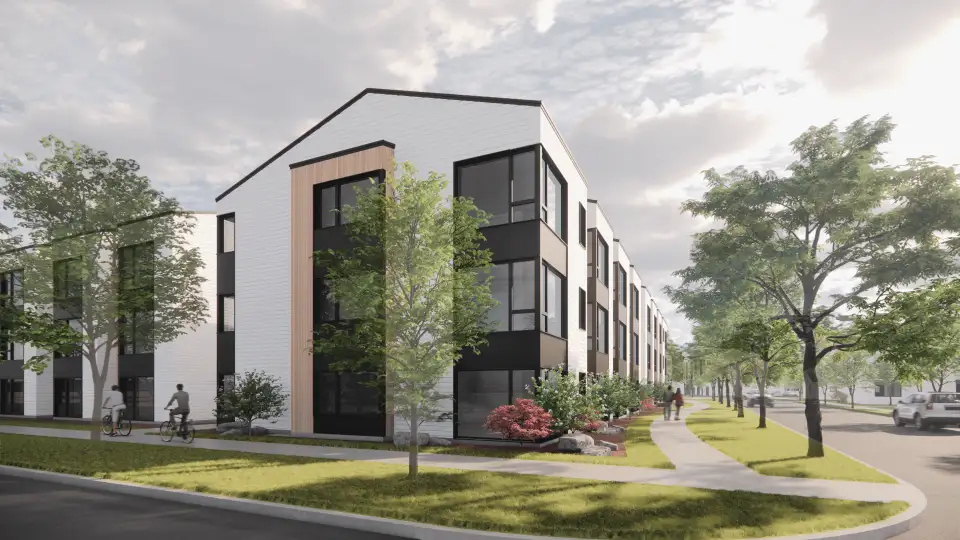
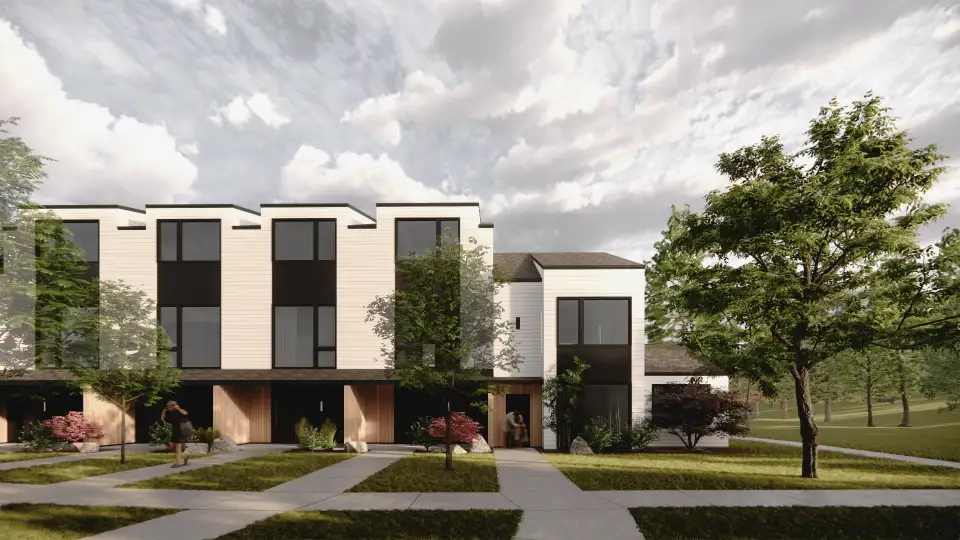
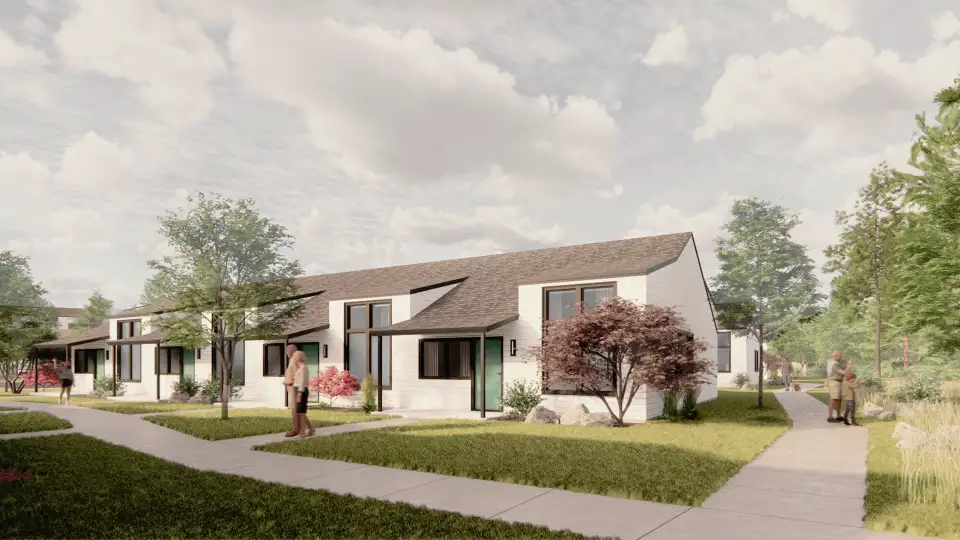
A big priority in the 10-acre development is moving the project to as close to a passive neighborhood as the budget will allow. “We are definitely looking for the simplest passive solutions, because there’s no wiggle room in the pricing,” explains Bradley. She adds, ”I really love that as a challenge, because if we figure it out here, then there’s no excuse not to do it everywhere.” Potential solutions include the use of double-pane windows that could be compensated for by using more insulation elsewhere in the envelope and detailing the construction tasks that will be performed by a general contractor to be as standardized as possible. As is typical with Habitat for Humanity projects, parts of the construction process, such as air sealing, will be done by volunteers.
While the chances of Bradley and Cassel attaining their cost-effective passive goals are high, there would seem to be a lot less certainty about them reaching another of their goals—slowing down just a little in 2023.
All renderings courtesy of the Artisans Group Architecture and Planning.