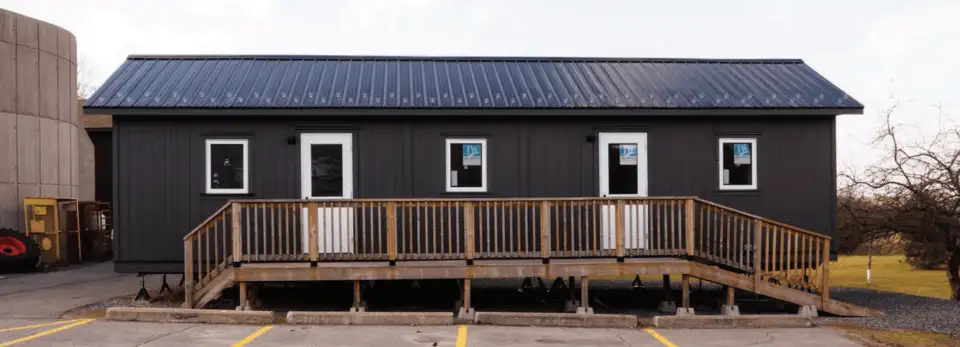
In Canada, buildings are responsible for about 18% of the nation’s carbon emissions, with residential buildings making up 10% of that total. As Mark Carver, project officer with Natural Resources Canada (NRCan), says, “That’s an opportunity.”
The opportunity to retrofit existing housing, though, hasn’t been taken up as enthusiastically as it needs to be to meet the federal government’s climate goals. NRCan has been incentivizing home retrofits for the last decade, says Carver, with some successes. However, only about 4% of the retrofits involved adding on insulation from the exterior to sharply reduce a home’s heating-energy use. “Generally speaking, these are expensive interventions that are seen as having a low return on investment,” says Carver, “and they can be disruptive.”
But then he heard about the energiesprong approach, first pioneered in the Netherlands, which uses panelized components added on to the exterior of a house to drive down the cost and time required for deep energy retrofits. “They’ve made a lot of progress in squeezing the cost down from 140,000 Euros per unit to about 60,000,” he says. The time required to implement a deep energy retrofit of a typical row house in the Netherlands has also dropped, from about ten days to as little as one day.
Energiesprong has been the inspiration for NRCan’s Prefabricated Exterior Energy Retrofit (PEER) project, which Carver heads up. The project’s overarching vision is to enable the Canadian manufacturing and renovation industries to commercialize new prefabricated façade retrofit technology, according to Carver. “We are borrowing where possible from the energiesprong approach and adapting where needed to a Canadian context: our climate zones, our industry, and our building traditions,” he says.
Since PEER started up in 2016, the team has convened an industry working group, and they jumped a bit ahead of their time line to complete their first pilot late last year. “We decided we needed to get our hands dirty,” says Carver.
The research group started with a very small building—actually a construction trailer in NRCan’s CanmetENERGY complex in Ottawa. Although small, it has all the requisite components that would need addressing: walls, windows, doors, and service penetrations. They scanned the building using a 3D laser scanner and imported the information into a building information modeling (BIM) software program. Using that information, they fabricated two types of panel in an NRCan lab facility and attached them to the trailer. Having put moisture sensors in the panels, they will be comparing cost, buildability, and moisture performance of the two different assemblies.
One panel type looks like a structural insulated panel wall, but instead of having two OSB skins, it only has one on the exterior. On the interior is a low-density fiber insulation, such as fiberglass or mineral wool, that is compressible enough to be able to conform to a building’s surface irregularities. They installed a 2 x 10 rim board at the top and bottom of the nail base to give the panels enough rigidity so that they can be hoisted into place by a crane. The other panel type is a conventional wood frame panel. In the pilot, it is a 2 x 4 panel that is stood off from the existing building by about 5 inches. The required R-value is achieved by filling both the stud cavities and the standoff cavities with dense-packed fibrous insulation— fiberglass, mineral wool, or cellulose—that is installed on-site through predrilled holes.
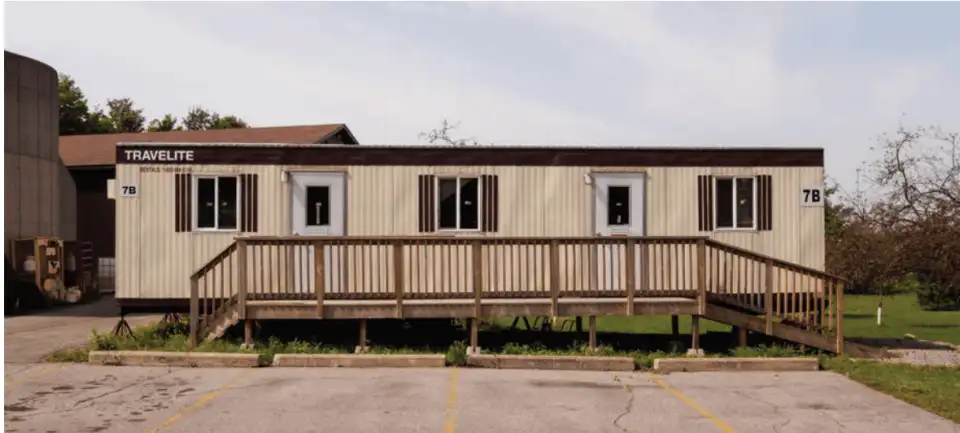
Carver and his team are pleased with how their pilot process went and are refining the designs of the assemblies with an eye to scaling up their pilot. Just as in the Netherlands, social housing is a likely catalyst market, because of the uniformity of the housing units, according to Carver. And because of the scarcity of affordable housing units, no one wants to move out, even temporarily. “Housing providers can’t displace tenants in affordable social housing, so a retrofit that can happen from the exterior makes sense,” he adds. There are roughly 650,000 social housing units in Canada, of which 100,000 are three stories or less, making them good candidates for this approach.
In 2018 the PEER team will continue to collaborate with their industry working group to identify manufacturers who would be interested in these opportunities. They are also working with building capture specialists to perfect that process—and looking toward 2019 for the potential launch of a larger pilot program.
Photos courtesy of CanmetENERGY, Natural Resources Canada