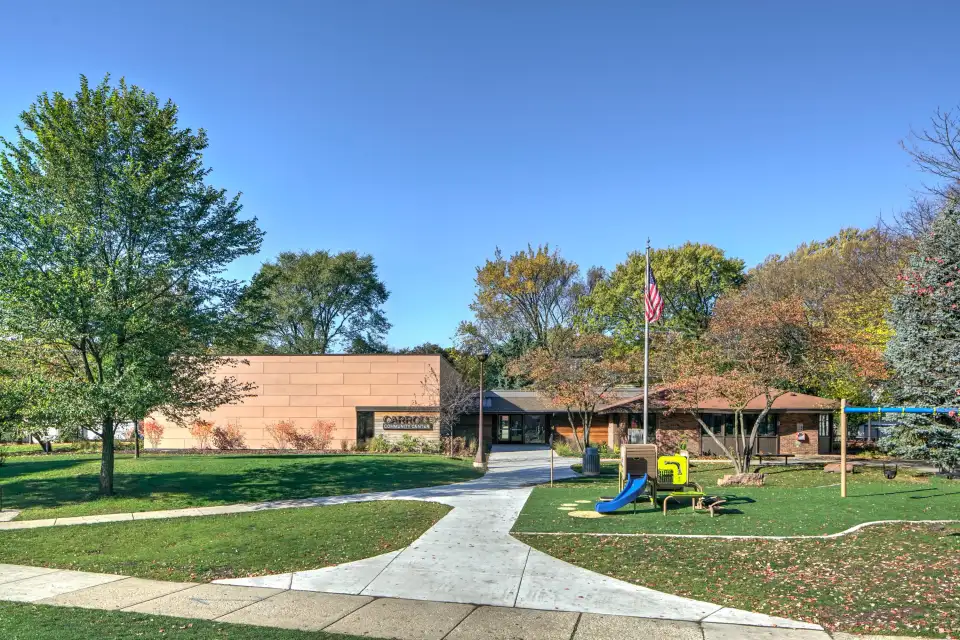
Featured image courtesy Hausman Photography
The Carroll Center is a PHIUS+2018 Source Zero addition and renovation project for the Park District of Oak Park (PDOP), a leading proponent of environmentalism in the community. For this project, pursuing PHIUS Source Zero fulfilled PDOP’s mission while qualifying for an Illinois Clean Energy Community Foundation (ICECF) Zero Energy Building Grant. The original building was built for the Park in the 1920s and added to in the 1940s and 1970s, so it was a relatively leaky, underinsulated hodgepodge.
The building has always been used for preschool and other Park programs, but with a growing population of young children in the community, more space was needed. PDOP also needed a large room where the entire staff could meet, something they didn’t have before the addition.
The brief called for renovating the existing portions (2,800 square feet plus the basement) and adding a large meeting room that could be divided into two classrooms; activities for the building included daycare in the mornings, after-school programs for kids, and evening programs for adults. The addition, including vestibule connection, was 3,400 square feet, for a total of 6,200 square feet plus a 2,100-ft2 basement.
PDOP turned to Tom Bassett-Dilley Architects (TBDA) for the project, having had success with their collaboration on the near-net zero (and LEED Platinum) Austin Gardens Environmental Education Center in 2015-2016. TBDA’s solution for the Carroll Center consisted of an interior Passive House retrofit of the existing building, with a new entry lobby connecting to a large, simple volume for the big room. Given the activity levels of the after-school kids—dodgeball, for instance—windows were limited in the new space. Daylighting was provided through a long, high band of windows on the south, shaded by a wall-mounted PV array, and was balanced by large skylights and small view windows on the north, entry side of the space. The new volume provided ample roof area for the 23.7-kW PV array, providing a calculated 10,000 kWh/yr surplus that PDOP can use as community solar.
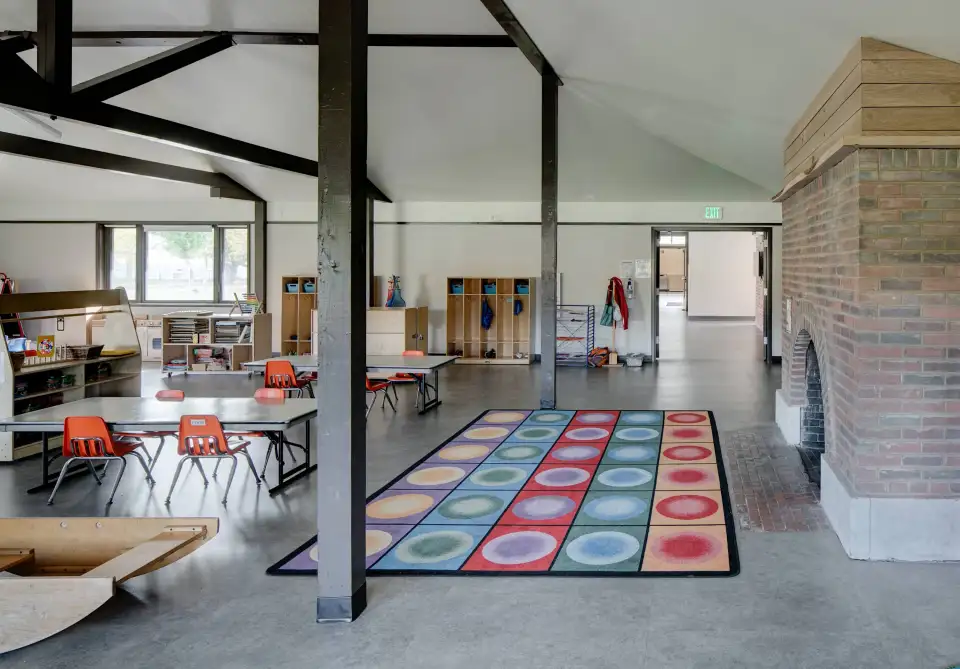
Construction systems on the new portion were straightforward, starting with an EPS-insulated slab on grade. The wall assembly consisted of a CMU wall structure, whose interior was painted as a finish, with an exterior Prosoco air and water barrier, followed by mineral wool and cement board siding. The framed vestibule used 2x6s with cellulose and Zip-R sheathing. The roof relied on polyiso over an air barrier, which was affixed on top of substrate board laying over the steel trusses and metal deck. As usual, the tricky points were the connections: roof to wall and foundation being primary, but each joint between the existing and new sections all took attention.
A scupper drainage detail illustrates one of the unique conditions (see Figure 1). Note that the foundation is the typical 42 inches below grade, and there is no insulation below the footing. This is a thermal bridge (0.081 BTU/hr.ft.F), but it’s not significant enough to warrant the expense and added time to prepare a sub-footing insulation course.
For the existing portion, we needed to keep the insulation and new airtightness layers to the interior. For the foundation, we used foam to the interior, providing both a capillary break and thermal control. We floated new EPS and a vapor barrier over the existing slab, as headroom wasn’t a concern. For the framed walls and roof, we used HFO closed-cell spray foam, after adding furring to increase depth to both wall and roof cavities. With our increased focus on embodied energy, we would now give greater consideration to just enough foam for airtightness and condensation control (2–4 inches) with the rest consisting of cellulose or another lower-carbon-intensive material. Our airtightness plan was to seal all visible cracks, then spray foam, and then bring in AeroBarrier to seal what we missed. However, between the diligence of the foam contractor and Tim Eberline, TBDA’s construction manager, we achieved the airtightness goal without the need for AeroBarrier.
Windows in the new portion are Alpen 400 Commercial Ribbon type, with Alpen Zenith for the renovated portion. Skylights are by Lamilux.
The mechanical system uses a ground-source (geothermal) heat pump for heating and cooling, with six 450-foot wells running two interior heat pumps, one located in the new addition and the other in the old basement for the renovated portion. These are water-to-air systems, so the conditioning ducts were used for ventilation as well. The ERV units are by Renewaire, with CO2 sensors for demand-control ventilation. Lighting was LED with daylight dimming and occupant sensors.
The project budget was $1.7 million, and the ICECF grant provided about $570,000 to help pay for the renovation portion, certification costs, PV array, and upgrades to reach Passive House levels on the new portion. The final 40% of the funds would be available only after a year’s performance period had demonstrated annual net zero—so the pressure was on to deliver with quality assurance.
PHIUS Pre-Certification was achieved in September 2019. Construction began in July 2019 and ended in June 2020. PHIUS+2018 Source Zero certification was achieved March 2021, after a process of getting the ventilation system properly balanced. Achieving this had its challenges. First, one of the ERV units shipped without a variable speed fan, so that needed to be re-ordered. The second challenge—installing dampers to balance the system—was more straightforward, but getting that diagnosed, ordered, and installed took some weeks.
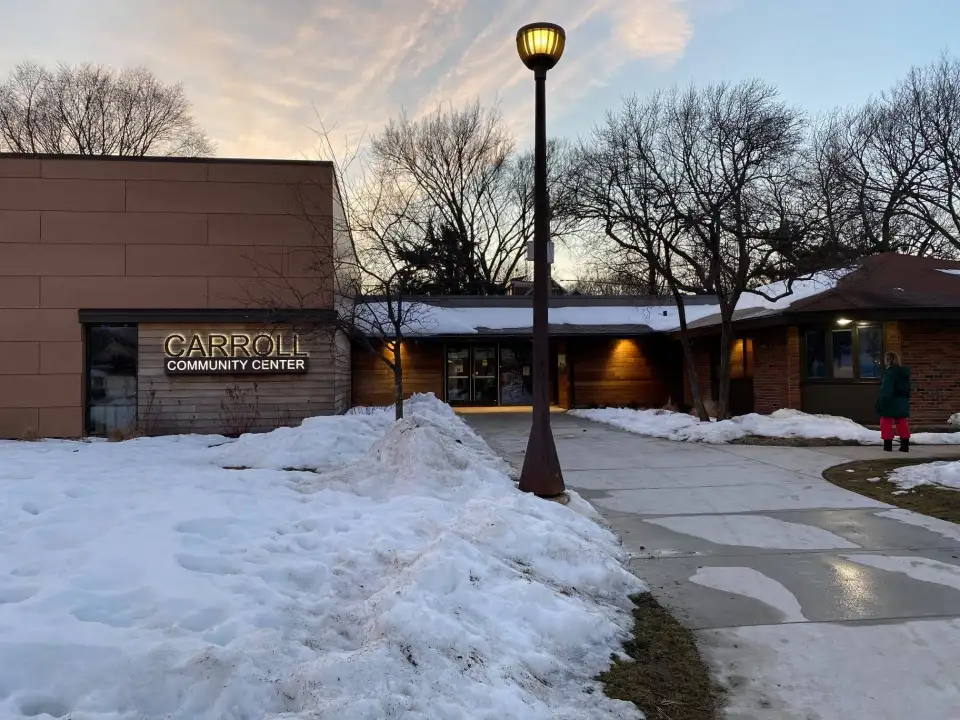
Looking back six months after completion, what stands out are the many decisions and efforts that must each be handled with a lot of care. The blower door test makes many of those decisions and efforts physically evident, especially those related to the hundreds of installations of tape, sealant, and air barrier materials. But there are many preceding decisions, starting with defining the aesthetic character of an energy-conserving structure, managing the quality of the design process, selecting systems and materials, and so on through to the energy model, thermal bridge analysis, and air barrier detailing. Since I took the PHIUS training in 2010, this process has become at the core of TBDA’s culture.