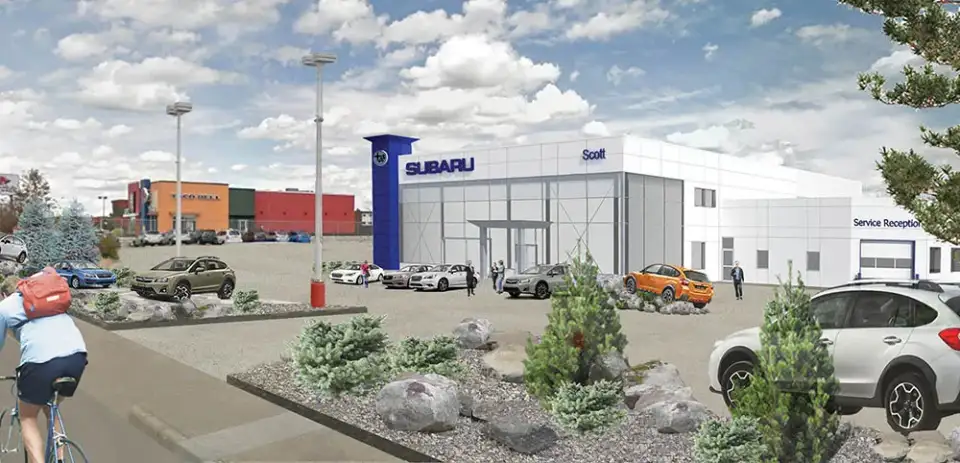
In chilly Red Deer, Alberta, Canada, where the winter design temperature is –29°C (–20°F), constructing any type of Passive House building is a challenge. But a car dealership? With all that glass and the service bays? Fortunately Certified Passive House Designer Lukas Armstrong of Cover Architectural Collaborative and Certified Passive House Consultant Andrew Peel of Peel Passive House Consulting brought years of experience to this complex task. Key team members included architectural support from Elaine Cripps of Sublime Design Studio Inc., wood structural design by Lex3 Engineering, M&E design by 908 Engineering, and contractor Black Creek Developments.
The 1,500-m3 (16,000-ft2) two-story, mixed-use building was the inspiration of dealership owner Garret Scott. As Alberta is also home to the tar sands crude oil industry, Scott says that he saw the project as an “important statement to the industry and the country.” More pragmatically, he understood that it would cost virtually nothing to heat and cool the building. In addition, a Passive House building fully aligns itself with Subaru’s environmental strategy, which includes producing Partial Zero Emission Vehicles. The Subaru of Indiana Automotive assembly plant, the first zero-landfill factory in the United States, originally inspired Scott.
A full-service car dealership requires several distinct types of space—a showroom with adjacent sales offices, circulation, and reception areas; a service area; and a conditioned area where customers can drop off their vehicles for servicing. The sales and showroom spaces need to maintain an internal temperature of 20°C (68°F), while the service and drop-off areas need to be kept at 18°C (64°F). In order to accurately model the building, Peel Passive House Consulting had to create three separate PHPP models.
In addition to the challenging climate, architect Armstrong had to work within Subaru’s corporate design guidelines, which mandated 55% glazing on the west façade with no external shading to mitigate solar heat gains. “Architecturally, probably the requirement to meet the design and branding expectations of Subaru Canada, while achieving certifiability, was the biggest challenge,” Armstrong says. “The building does not look significantly different from other Subaru dealerships, but performs very differently.”
Cold climates present design challenges that are magnified when designing a building that meets Passive House standards. Every decision, especially when it involves airtightness, has a significant impact. Frost protection and low humidity can be problematic. Mechanical equipment and products such as doors need to be suitable for a cold climate. These challenges can be amplified even further when deployed in an unusual space like an automobile service area.
One of the biggest challenges was glazing, particularly on the west façade. Meeting Passive House space heating demand without overheating required paying special attention to irradiance on the west-facing curtain wall. The site has very little natural shading, and tree planting was ruled out because it would block too much sun, jeopardizing the heating demand target. Operable external blinds were not feasible because the site experiences wind gusts of up to 103 kph (64 mph). Electrochromatic glazing was too expensive, and the specifications were not quite suitable. After much research, the team chose to use automated, operable internal blinds coupled with insulated spandrel panels in the top row of the curtain wall. Since there are no cold climate-certified curtain wall windows, the Passive House comfort requirement was met by placing heating supply ducts close to the windows.
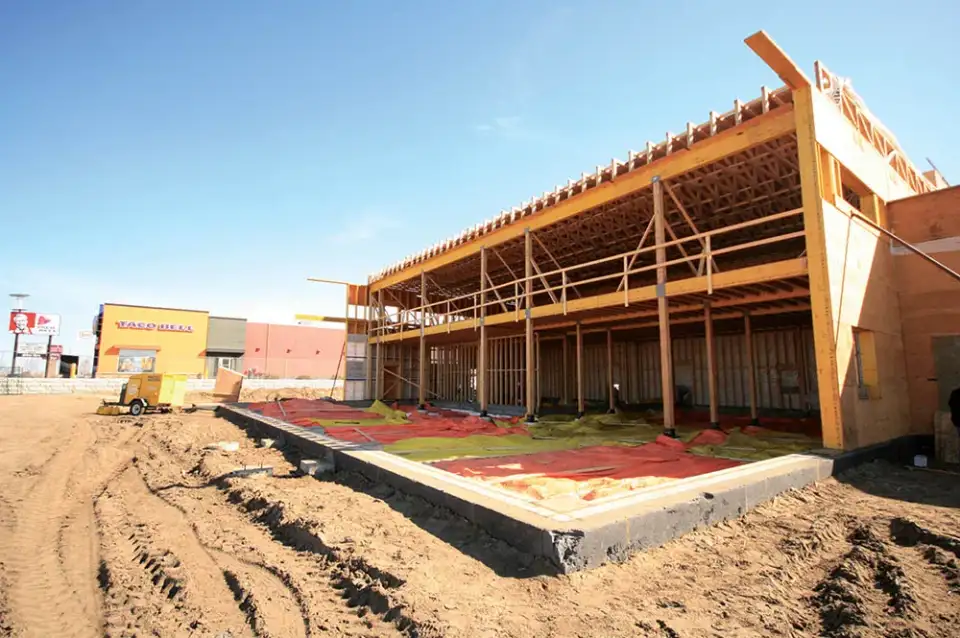
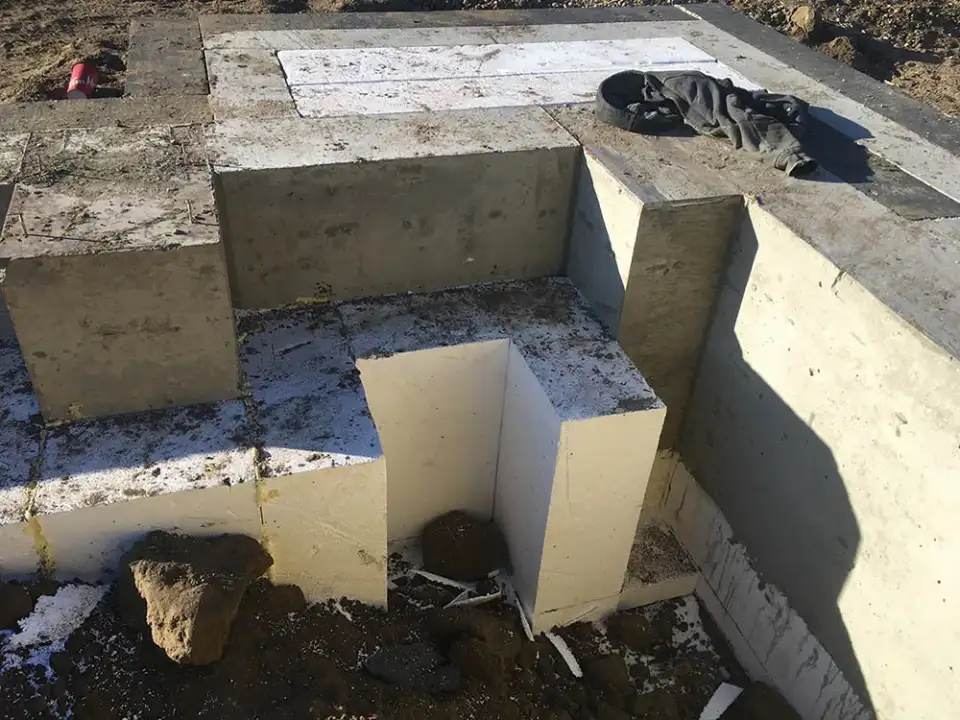
Automobile service areas require doors large enough to accommodate vehicles. This presents several challenges—heat loss from lower levels of insulation, operating heat loss, and air leakage. The original design called for seven overhead doors. The team proposed an alternative design that reduced the number of doors to two, which the client did not support. Through negotiation, the team settled on four. Investigation revealed that heat loss from a single door event was a modest 15 m3h (9 CFM). To solve the airtightness issue, the team investigated European Union (EU)-rated doors. With an airtightness target of 0.4 ACH necessary to satisfy the certification criteria, a Class 2 EU door would use up 20% of that target. The team was able to locate a Class 3 door that would contribute only 10% of the air leakage.
Automobile repair presents some interesting internal heat gain issues. The project team had to calculate gains for air compressors, hoists, and other repair equipment. In addition, car engines entering the building give off heat. All cars are washed with 60°C (140°F) water after servicing. Cars also have to be run during repairs, generating exhaust temperatures of up to 343°C (650°F). Overall, the repair shop generated 55% of the internal heat gains, 14% of that from running engines.
Mechanical system choices were driven by climate and servicing requirements. For instance, Subaru services diesel vehicles, which requires attaching a 680 m3h (400 CFM) exhaust tube to each car’s tailpipe during testing. Most dealerships manage this exhaust by running a large fan that evacuates all service bays even if only one requires exhausting. For the six service bays in this project, that would amount to 4,078 m3h (2,400 CFM), potentially generating large heat losses. The project team was able to convince the mechanical engineer to use a separate fan for each service bay. Various options were investigated for heat recovery from the exhaust airstream, but none was feasible.
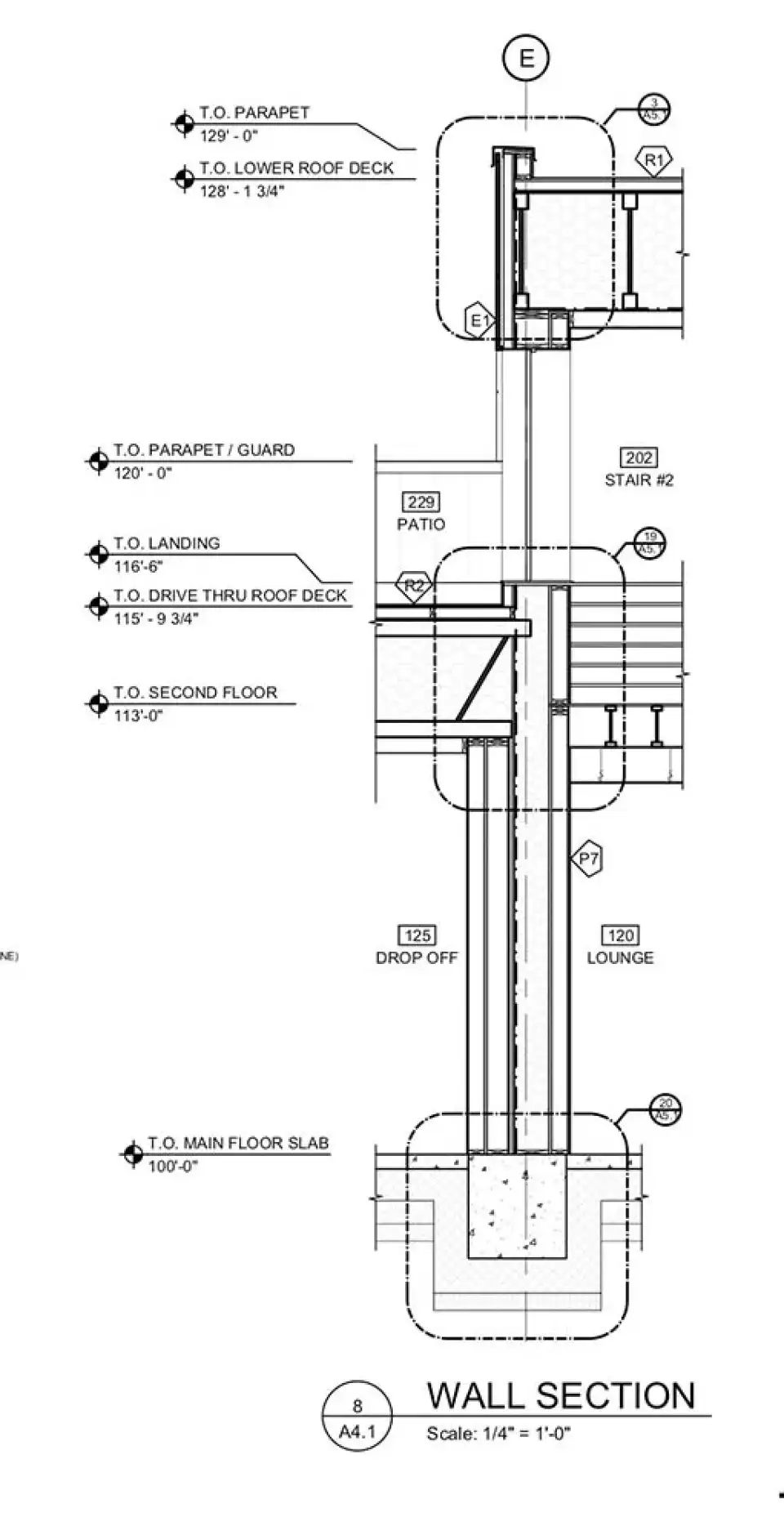
According to Armstrong, “the largest challenge was designing an HVAC system that met the safety requirements of a repair shop as well as the Passive House thresholds.” Heating and cooling are provided by a variable refrigerant flow system with heads in corridors ducted into each room. The system does not operate at the coldest winter temperatures, requiring the use of electric backup heat. There were extensive discussions with the engineer about loads. For instance, PHPP estimated the heating load at 13 kW (44.4 kBtu/hr), and at 21 kW (71.7 kBtu/hr) with no internal heat gains. The engineer’s initial design called for a 64 kW (218.4 kBtu/hr) heating load, or 3 to 5 times larger.
Because of the west-facing glazing, the cooling load in the showroom and office space dominated the HVAC equipment sizing. The team evaluated the cooling load under multiple scenarios, starting with PHPP’s peak cooling day assuming 40% irradiance blockage from internal shades. The team then looked at higher levels of internal heat gains from people, equipment, and lighting during the worst three hours of the day with internal blinds fully open. The normal case required a cooling load of 10 kW (34 kBtu/hr); the worst case was 52.9 kW (180.5 kBtu/hr). The engineer has calculated 57 kW (194.5 kBtu/hr).
The team also analyzed heat loss from car washing, which consumes approximately 2,020 liters (530 gallons) per day. The only viable equipment option was an on-demand gas heater. Because of the equipment choice, coupled with the high volume, high temperature, and frequent use, this function was a good candidate for heat recovery. A horizontal shower-type unit was considered, but ultimately proved unavailable. Instead, the team acquired a vertical unit and installed it horizontally.
If you really want a challenge, Peel says, design a cold-climate car dealership. You need to think through all the details early, especially equipment and all energy flows. Because project parameters may change, you should build some buffer space into your calculations—a wise suggestion for any Passive House project. Use the simplest approaches possible for all aspects of the project, and find engineers who are willing to explore options.