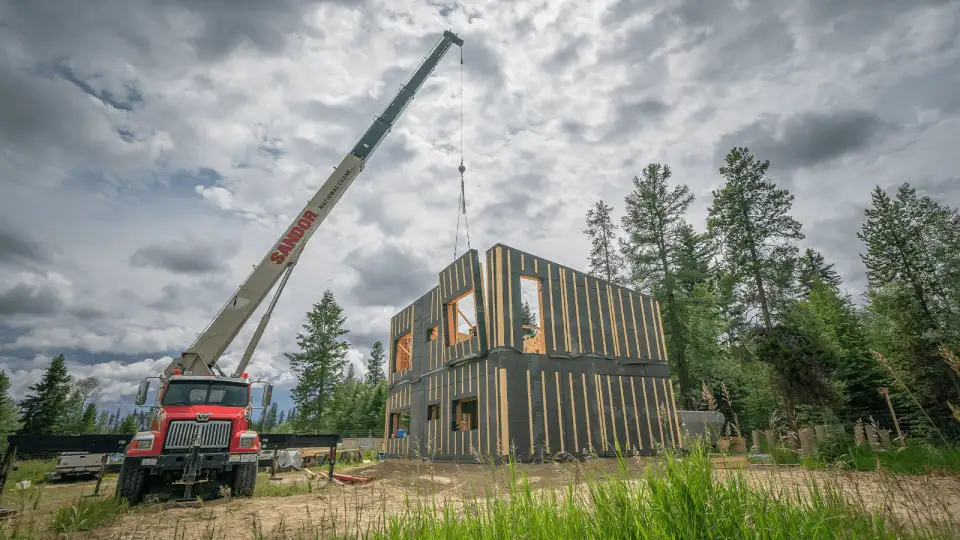
Collective Carpentry is poised to transform opportunity into climate action. In June of this year the panel prefabrication company found out that it had been successful in its application for a grant—its first ever—from the CleanBC Building Innovation Fund and secured $580,000. The funds are to be spent on acquiring semi-automated production equipment, thereby increasing its output of prefabricated buildings and providing its carbon-reducing homes to a greater range of homeowners and builders. "Receiving the grant money has accelerated our growth path, and we are grateful for the foresight of the BC government to tackle the climate crisis head on by supporting the businesses that are working to lower carbon emissions,” says Rane Wardwell, co-owner of Collective Carpentry. “As the effects of climate change show themselves, the urgency to make dramatic cultural changes increases and we feel like this opportunity helps us do that."
Collective Carpentry is currently finalizing arrangements to build a facility in 2022 in the Invermere, BC region where it is based to house, and optimize the capabilities of, its new equipment. “We aim to be building homes for 40 families annually within the next few years,” says Craig Toohey, business development manager at the firm.
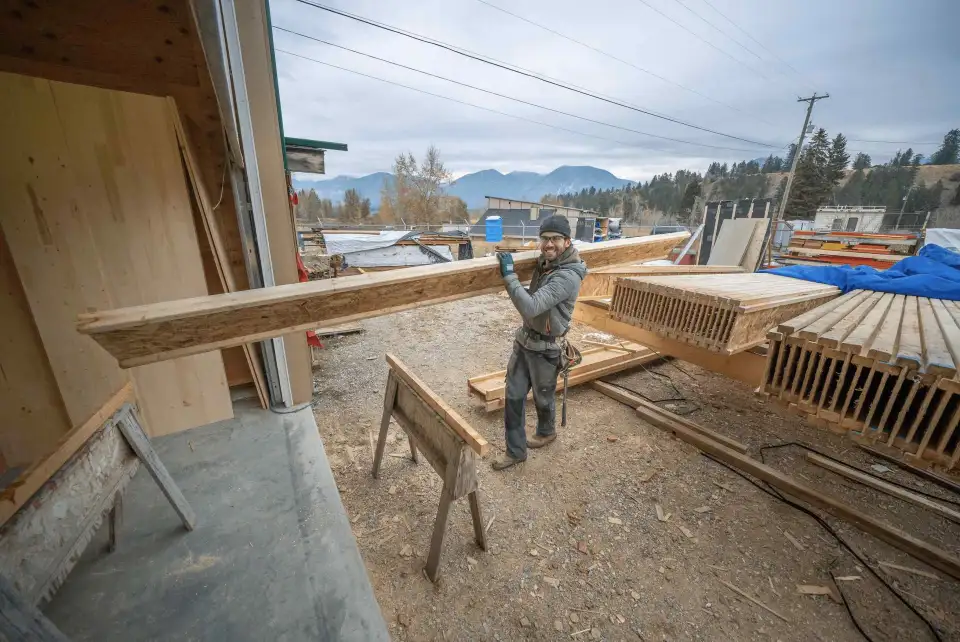
By ramping up production, the firm will be able to supply its high-performance panels at a more affordable cost than it currently can. The greater affordability will in turn pave the way for the construction of more affordable low-carbon homes—ones that can ultimately compete with code-minimum site-built houses. That was the case for a recent project that Collective Carpentry worked on in Whistler. “The homeowners had not been planning to have as efficient a building enclosure as they ultimately did, but because we could deliver our efficient panels within a rapid timeline, they could justify the higher cost,” Toohey notes.
The company estimates that its homes shrink operational energy use by at least 50% compared to a conventionally built one due to the improvements in insulation, air sealing, and thermal bridging that its panels provide. Collective Carpentry’s process further cuts construction-related carbon emissions by relying extensively on lower embodied-carbon, wood-based materials, reducing waste, and lowering transportation emissions during the build process.
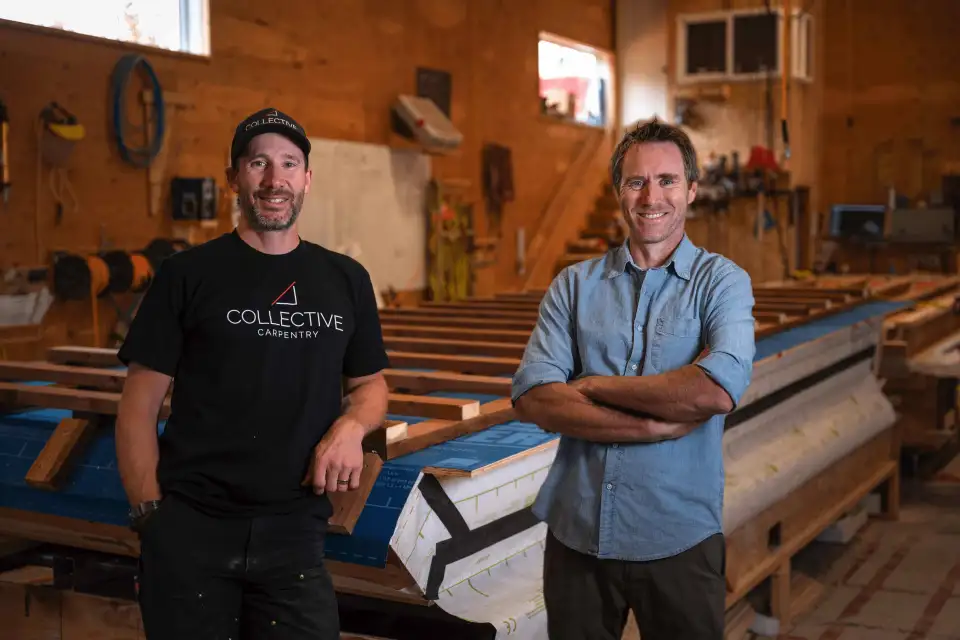
The low-carbon wall, floor, and roof panels that Collective Carpentry produces are constructed primarily from wood, fiberboard, and cellulose. Its wall panels tend to come in one of three general forms: an I-joist wall, a closed structural wall panel with an exterior layer of fiberboard insulation, and an open version of the structural wall panel. All of these come in varying thicknesses and R-values to suit the climate where they will be installed. Buildings constructed with Collective Carpentry panels are designed to be Passive House compliant, depending on the site characteristics.
Jan Pratschke, Collective Carpentry’s other co-owner, is looking forward to being able to meet the growing demand for its high-performance, low-carbon prefab panels with the increased production capacity that the new equipment will bring. Until then, he has devised a stop-gap solution to meeting excess demand in the short term: he has assembled an informal network of prefabrication companies who can absorb some of the demand variability. Sometimes he sends work to other companies and vice versa. Earlier in 2021 a Collective Carpentry installation crew completed the site work in northern Washington State for another Canadian prefabrication company who couldn’t easily get a crew to the U.S. “It is beneficial to everyone to work together,” notes Pratschke. He is also looking to hire more designers and crew in anticipation of an increased sales volume. In the longer term, he hopes to see a new crop of prefab companies spring up as recognition of the value of off-site construction continues to grow.