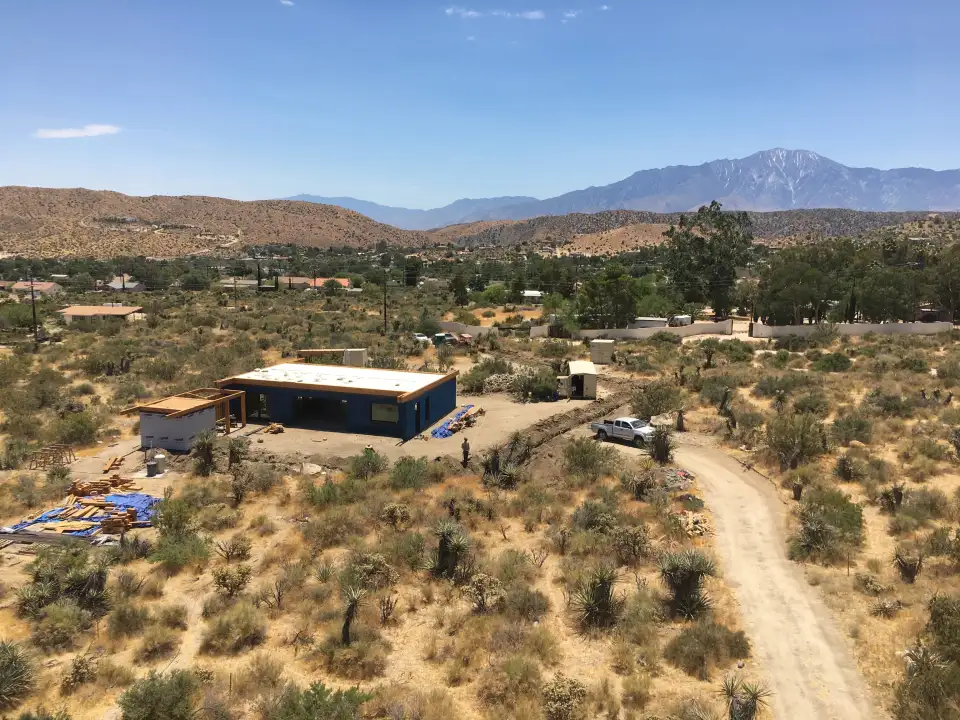
California’s Morongo Valley, just outside of Palm Springs, is quintessential high-desert country. Surrounded by mountains and featuring almost endless sunshine, the tiny town can swing through 30 degrees on a given day and generally bakes during summers when daytime temperatures often hit the high 90s and stay there for weeks or even months. Its challenging climate forces adaptations on its residents, whether they be rattlesnakes, coyotes—or people. Trent Laughton of Not | Not Architecture & Construction, the architect and builder of two neighboring homes here, has had to come up with some inventive adaptations to make his first-ever Passive House project succeed.
“I worked at a high-end design build firm in Los Angeles for seven years, and then after striking out on my own, I wanted to get back towards sustainability,” Laughton explains, as he lays out how he came to be building this Passive House in Morongo Valley, while simultaneously constructing a code-built house on the neighboring lot. His two clients, who are friends, had bought the adjoining lots, and one was willing to pursue Passive House while the other held back, opting for meeting code and investing additional funds in other aspects of the build. “It’s fun, but it's a lot of work,” he says in an understatement that is almost as dramatic as the peaks in the distance.
Since he left the Los Angeles firm, Laughton has been on a steep educational climb, first becoming a certified Passive House designer through the Passive House Network, then diving into multiple Passive House resources, such as the talks and videos on the Accelerator, and ultimately getting connected with Matt Bowers through the Certiphiers Cooperative. Bowers will be the home’s certifier and is helping Laughton as he compiles his first PHPP model. “He has been a great guiding light,” enthuses Laughton, adding, “Watching all these videos, and getting connected with other professionals—the amount of shared knowledge is a little bit new to me. Working in high-end residential construction, it seemed more like everybody was wanting to hide the magic.”
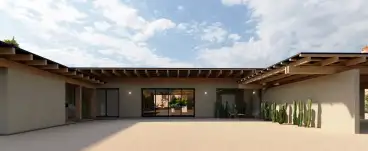
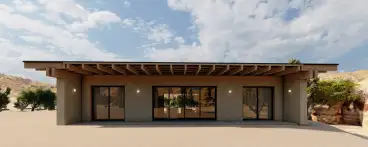
That’s not Laughton’s style. His version of magic—blending high-end design and high sustainability—is in plain sight as soon as you cross the threshold of this Passive House. Large, 16-foot, triple-pane sliding doors frame the view of the mountain to the south, while the north-facing facade’s ample glazing offers amazing views onto another ridge. “I think it'd be hard in Southern California to find a better snowcapped mountain that you get to see right out of your kitchen and living area,” he enthusiastically points out. In addition to the main home’s careful design and construction, Laughton has thoughtfully constructed outdoor spaces that play well with the local climate conditions. There’s a shaded and wind-protected patio to spend time in soaking up the scenery while sheltered from the elements. For those occupants who really want to soak in the outdoors, there’s even an outdoor bathhouse complete with tub, toilet, and shower.
Sitting at an altitude of about 2,800 feet, this Morongo Valley home interacts with a slightly less intense climate than nearby Palm Springs—fortunately. “I plugged in the climate set for Palm Springs and I was like, oh, there's no amount of insulation or high-performance windows that you would be able to get to make that work,” he says, laughing as he reminisces. To optimize the PHPP model’s accuracy, Bowers contacted the PHI to get the most relevant climate set, that of Yucca Valley. “At any given time, it's about 15 degrees cooler where we are right here than it's going to be down the hill,” explains Laughton, “So that helps out a lot.” Morongo Valley freezes during winter nights, and there can be dustings of snow a few times, but it’s the summer weather that has the biggest impact—and summer lasts a really long time here. Creative shading has been the lever that is making this project certifiable, but that’s jumping ahead.
The initial adaptation Laughton dealt with was creating an insulated foundation—definitely not what he was used to doing in Los Angeles. At first, he thought he would need 4 to 6 inches of rigid insulation below the slab and around the stem walls, but working through the PHPP calculations convinced both Bowers and him that 2 inches was the right amount, allowing the structure to shed a little bit of heat in the summer while balancing the heat losses during the winter. Below the rigid foam is a Stego moisture barrier that wraps the slab from underneath and is taped to the interior face of the stem walls; below the moisture barrier is two inches of sand.
He constructed the stem walls using insulated concrete form (ICF) blocks. The four-inch slab sits surrounded by the ICF blocks and was polished and sealed to create the finished floor surface of this single-level home.
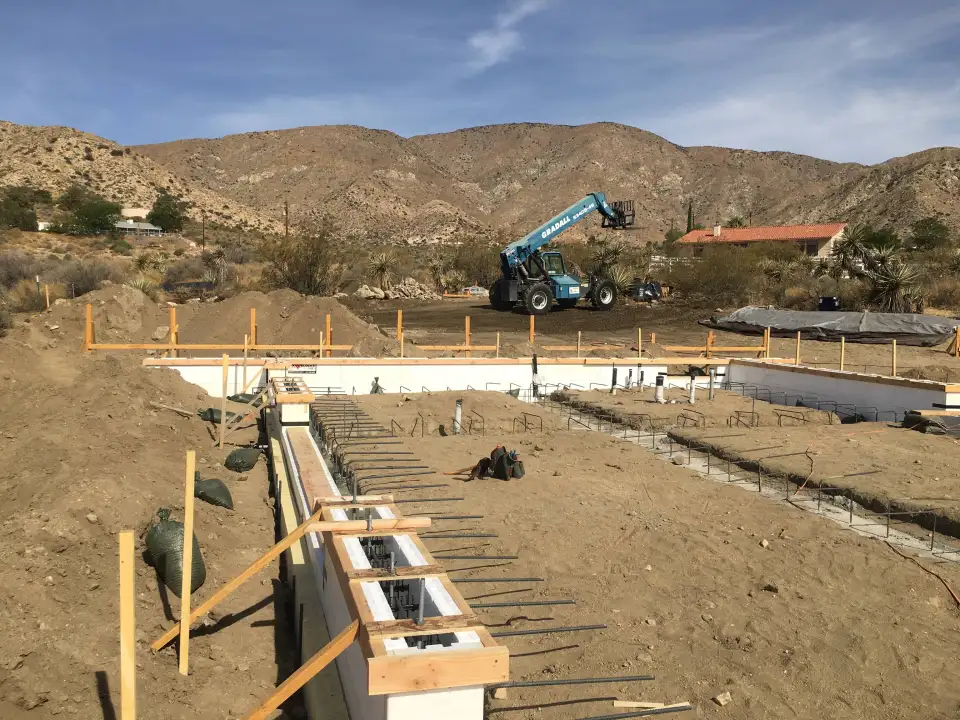
The above-grade walls vary in thickness, depending on which direction each one faces. The north- and south-facing walls are 22 inches thick, achieving R-values of 56, while the east- and west-facing walls are 16 inches thick to hit an R-value of 42. The exterior-most 2 x 8 wall is filled with mineral wool, with an air barrier membrane on the inside that ties into the Stego wrap. Pro Clima INTELLO PLUS is being used as both the interior primary air and vapor control membrane, while Pro Clima ADHERO 3000 is being used for the WRB. Laughton pushed the 2x8 structural framing out to the face of the stem walls to allow the exterior sheathing to run over the stem wall, avoiding a break at the sill plate line, at the request of the plasterers who will be finishing the exterior surfaces. On the interior is a 2x6 wall to fit in additional insulation and then a 2x4 wall to run the utilities and provide a deeper inset look for the windows.
This all-electric house will include a Brink ERV for fresh air and humidity control to help keep the home comfortable even with the desert’s dry air. A Rheem heat pump water heater, located in an exterior mechanical closet, will provide the hot water. Heating and cooling in the Passive House will be amply supplied by a 9,000-Btu Mitsubishi ducted mini-split. That’s a tiny system compared to what he had been used to installing and what the neighboring code-built home will require—63,000 Btus of heating and cooling there. That 9,000 Btus is also almost 50% larger than what the PHPP predicts will be needed, but it’s the smallest Mitsubishi unit that was recommended.
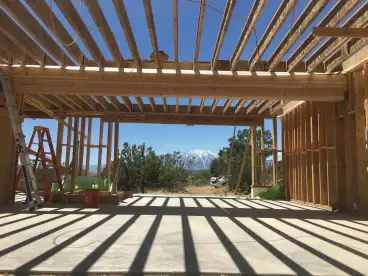
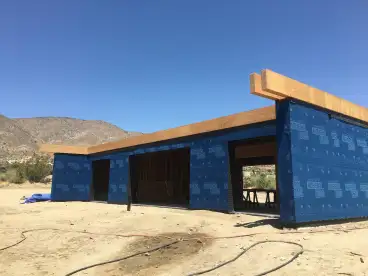
How did Laughton manage to shrink the heating and cooling demand that much? “The big aha moment for me was when I started playing with the shading,” he explains. He could dial up the insulation, or input the highest performing windows, or even reduce the glazing—not a choice the client would tolerate—and none of that really helped. “If I shaded the roof, 100 percent, I was able to tip the scales,” he realized. The shade roof, as he terms it, acts like a permanent parasol, sitting above the watertight and well-insulated R-62 roof, and cantilevering out eight-and-a-half feet to the south and six feet to the north. Instead of paper or fabric, though, this parasol consists of a corrugated metal sheet supported by rough-sawn 6x10s that tie into blocking mounted to the watertight roof structure. For additional sun protection, every window has an exterior, motorized blackout shade, providing both shading and privacy, when needed.
Laughton is installing energy monitoring devices to track this passive home’s energy usage, as well as the code-built home, to be able to compare and contrast once the two homes are finished and occupied. Additionally, he will use these data to commission the homes during the first few years of occupancy and gain greater insight into both homes’ performance.
The heavy lift to get these homes designed and built, which included months of camping at the site in a temporary shelter, is finally winding down. Although filled with challenges, the process has also been rewarding, almost magical. “It’s been a revitalizing process for me in both design and construction,” reflects Laughton. “And, I think what's been really fun, too, is that my small crew and the subcontractors that come through, everybody's really interested in it. Once you start to talk about the principles, everyone's like, wow, this makes a lot of sense.”
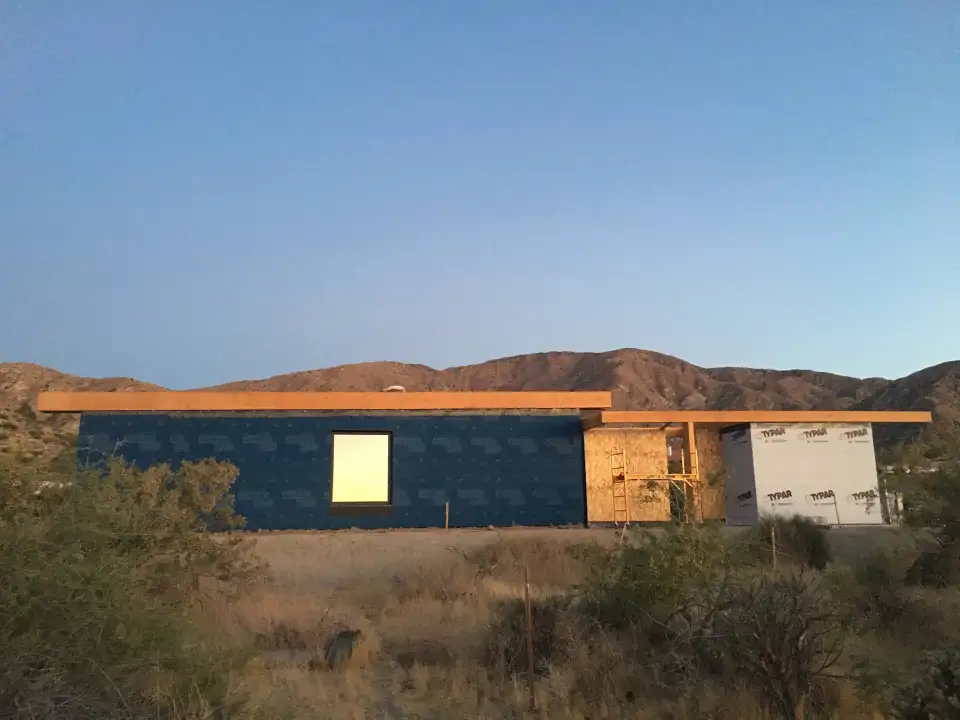