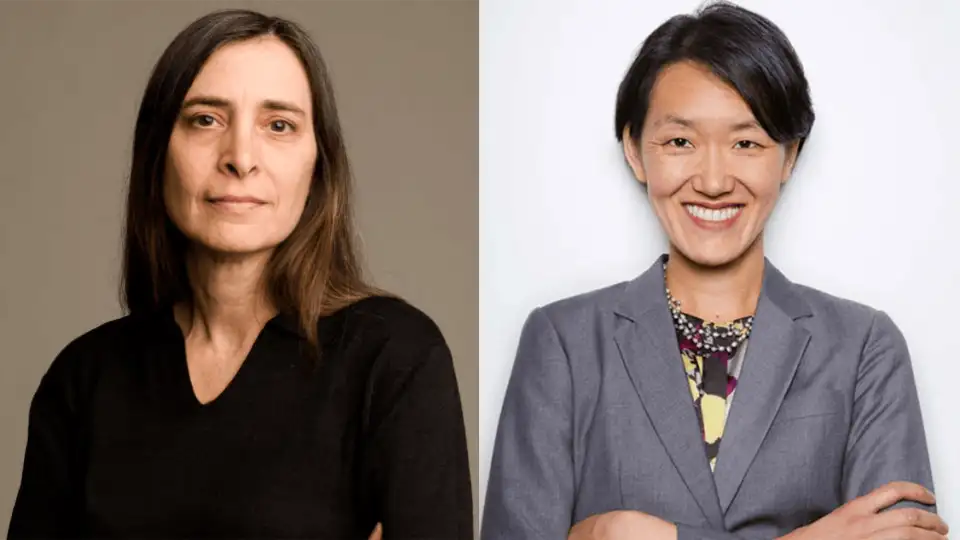
Architect Chris Benedict has been on the leading edge of climate-smart buildings in New York and nationally for more than two decades. I had the pleasure of interviewing her on May 3, 2021 about prioritizing control of air movement as an important part of the post-COVID “new normal.”
Bomee Jung: So now that we’re heading towards the other side of this pandemic, people are talking about healthy homes. I’m wondering, “Why are we being so general?” Let’s talk about compartmentalization! Shouldn’t controlling ventilation, so that air from one apartment doesn’t intrude into another apartment, be top of mind?
Chris Benedict: Well, yes, it should be. It’s just that compartmentalization is difficult to do, especially in existing buildings.
There’s compartmentalization and there’s ventilation. The compartmentalization and the ventilation work together in a positive way. If you have ventilation — say you have exhaust-only ventilation — and you haven’t compartmentalized, then you don’t know where that air is coming from. I think it might be Joe Lstiburek who said, “Is your air new or pre-owned?” That’s kind of a gross idea!
What’s important about compartmentalization is that air moving from one apartment to the other can bring odors, mold, and maybe fumes. Maybe there’s a boiler in the cellar, and those products of combustion are back-drafting and actually coming up through the building because sometimes the stack effect of the building is stronger than the stack effect of the chimney. So it’s got quality of life issues, but it also has health and safety reasons to exist.
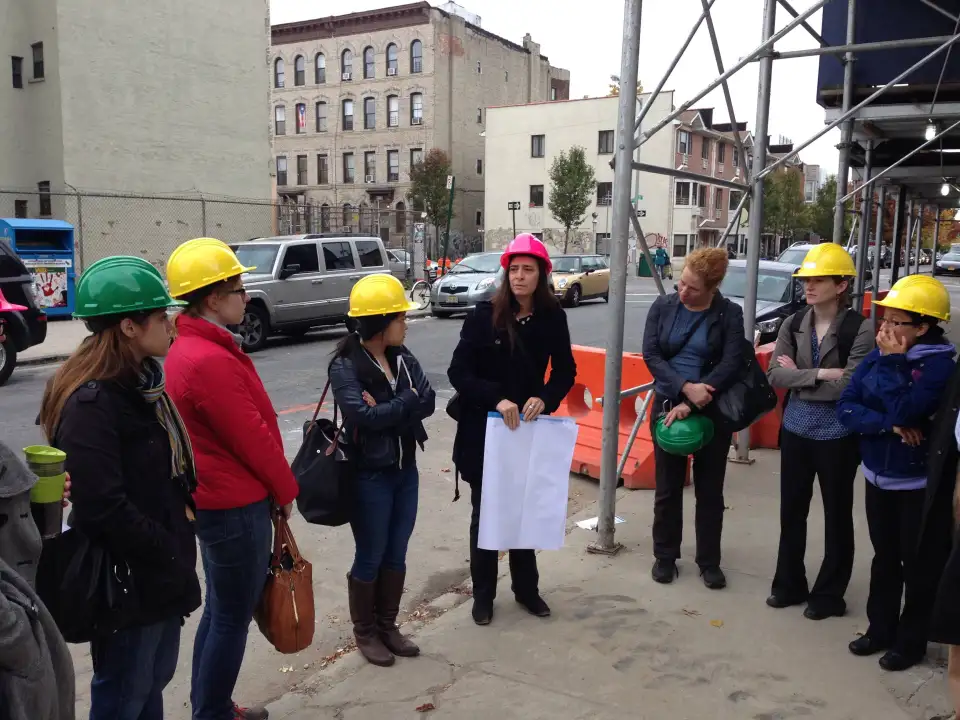
BJ: Is it “compartmentalization” if you pressurize the hallway and deliver fresh air with undercut apartment doors?
CB: No. That is a [ventilation] strategy. It’s one that has been used by engineers over time. But I’ve never actually pressurized hallways. Basically, the way I look at an apartment building is, it’s a single family house, stacked on another single family house, and it should have its own air dynamic going on inside it, regardless whether it’s balanced ERVs, or you’re exhaust-only and you’re bringing in fresh air through trickle vents, like I did very early in my career. It’s each apartment as its own zone. And then, all this stuff outside of the apartment — the public halls, the elevator — is managed separately and maybe balanced through an ERV system.
If you think about this at a higher building science level, you could actually compartmentalize with balanced ventilation. So, for instance, if you had an ERV with equal supply and return airflow in one apartment, and an ERV in another apartment with equal supply and return, you could say, perhaps, that you were balanced between the two apartments.
BJ: Because there’s no pressure differential for air to move between them, even though you haven’t actually done all the apartment air sealing?
CB: Correct. But pressure difference can be induced in other ways. For instance, you can have the stack effect in a building. When I first started doing this work, the most important reason to compartmentalize was the stack effect. The stack effect is heated air rising up through the building and pulling in outdoor air at the bottom. This is a winter phenomenon. It’s actually the opposite in the summer, but not as strong. But when you compartmentalize, then you only have a mini stack effect in every apartment, which is awesome because you really have minimized it. So when we’re building new construction, you can get in there and you can seal one apartment against the other.
In an exhaust-only scenario, if you don’t compartmentalize, it’s impossible to get the fresh air that you want into the apartment. Back on my very first jobs, which were 18 small multifamily buildings in 1999, some Swedish engineers came out to the job. And they were just saying, “Oh, there’s no way an American could possibly make an apartment tight enough that the trickle vent will actually have air coming in when you turn on the ventilation system.” They got up on the window sill and felt the air, and they’re like, in Swedish, “Oh my God! There’s air coming through this!” And the reason it worked was because my apartments were tight.
When I first started using an exhaust-only system with trickle vents, everyone wanted to try it: Where do you get those vents? What do you do? And I just kept saying, don’t even bother if you’re not compartmentalizing, because you don’t know where the air is coming from. And the chances of getting it from the trickle vent are pretty slim, unless you make a “container” [i.e. apartment] that only has a few small holes in it.
BJ: Have you heard people talking about compartmentalization as a response to COVID? Not to suggest that there has been COVID transmission through the ventilation system, but just the idea of indoor air as a vector brings up scary possibilities for future pandemics.
CB: Not really. Why are we not talking about it so much with COVID?
Very early on in COVID, I certainly looked at the ventilation systems that I was specifying. There are two types of ERVs out there: one of them has a core, and the core has air moving in one direction and air moving in another direction with corrugated plastic pieces that create this core. So you get heat transfer in the core, but the two airstreams never touch. There’s a second ERV type that uses a desiccant wheel and the desiccant absorbs the humidity from one airstream and transfers it to the other. I decided to not use the desiccant wheel type ERV if I’m joining a few apartments together with the same ventilation system, in case there might be a chance of virus transferring as the air goes over the desiccant wheel. So I had to actually change a specification midway through COVID.
But there’s also UV light treatments that you can put in the ductwork. The problem with that is that there’s a length of the UV [lamp] that’s based on the speed of the air running through the duct. And there really has not been a definitive answer about length versus speed versus intensity. I know that ASHRAE was first working on it when COVID started, but I think that’s kind of gone by the wayside.
Compartmentalization, of course, is going to help any issues that have to do with air movement.
Also, there’s been this misunderstanding that if the air is moving, it’s better than it being still, when, in fact, in some of the first analysis of COVID, the people were in the restaurant and the air conditioning system delivered the virus to them. So it’s not necessarily that air moving is always good; it’s where the air is moving and how it’s moving.
In some cases, it may be better to keep the air still. For instance, we’ve compartmentalized my office to the point where we each have a bubble around us, and the air is still inside of our bubble so we’re in our own air. If any of us has the virus, it’s gonna drop to the floor and not move to somebody else. So, you have to think about it much more than just any set of general rules.
BJ: How isolated does an apartment have to be for you to say “that’s compartmentalized”?
CB: There are different tightness numbers that different standards and different organizations want you to have as your goal. The Army Corps of Engineers has a number. Passive House has a number. Those numbers are not as strict as the goal for entire-building Passive House airtightness. And actually, I don’t know why, except that it is hard to get each apartment as tight as you can get the building, which is a little ironic, but every apartment usually has so much stuff traveling through it that getting it perfectly sealed like you would for a Passive House [enclosure] is very, very difficult.
There’s also a new product out there, AeroBarrier. What they do is they come in with a kind of a fibrous product. They pressurize the apartment and blow it into all the gaps. And you can actually tune your tightness by monitoring it. And it’s an awesome, awesome technique and one that could be used in new construction so that we didn’t have to get people caulking every little tiny crack
It can also be done in existing buildings. But it does mean that you have to perhaps pull out all the furniture and cover everything, in order to not get it all covered with this stuff that you’re blowing. This is a very good product and one that we should be using more often.
BJ: Is it accurate to say that if you’re building to one of the passive house standards, that the baseline requirement for apartment compartmentalization is the best standard that we have to build or design around right now?
CB: I would say the Passive House Institute US (PHIUS) standard is. I don’t know if Passive House Institute (PHI) has a compartmentalization standard — I don’t know if PHI ever put compartmentalization into their repertoire. I definitely think it’s a good idea.
Now, in a situation like a tenant-in-place rehab I’m doing right now, I want to bring it to the passive house [compartmentalization] standard, and we’re going to do the best we can. But we cannot [fully] compartmentalize those apartments, as much as I would love to do it. And we’re doing new kitchens and new bathrooms in those apartments. And we’re sealing all the places where pipes are coming in, but in terms of moving everyone out moving all their furniture, we’re not doing that, because that’s just too overwhelming. So it’s easier to do in new construction — or in rehab where the tenants have moved out — and then you could blow that AeroBarrier in.
BJ: You’ve been doing this for a long time. What are some things that you learned the hard way that people who are just now trying to do it should know?
CB: When I first started learning about it in the building science world, I was wondering, “How the heck could I actually do it?” because it seemed very expensive. And then I realized that the code really helps with that. There’s all these fire-stopping details that we are required to do by code and soundproofing details that are required by code. Between the fire-stopping and soundproofing details, I realized that most of the compartmentalization stuff was baked in. So we would just insist that these details be followed. Now, were people following these details? No — I had to stand there and ask people to do it, and it wasn’t easy, because the details were overlooked. It’s a little frightening how much they had been overlooked and may still be overlooked. In my jobs, we’re getting this sound transmission coefficient rating that’s asked for in the code. That means you must caulk two layers, top and bottom, of the demising partition, and every pipe that goes through one of those walls gets the red gunk around it to firestop it as per the details.
And there’s also a controlled inspection for this through the building department. But even then, you don’t see it done all the time, because at every stage of construction, you’re building something and making new holes in it. And how many times can a controlled inspector come out there, to inspect all of that. So it really takes weekly looking at everything to know that you’re delivering the compartmentalization that you want.
BJ: Someone said to me, and I thought this was funny and insightful: “You need a better name for this than ‘compartmentalization,’ because it’s got too many syllables and it doesn’t sound nice.”
CB: Oh, totally. I mean, yes. I don’t even know if it’s an actual word! At first, we had a lot of problems with spell check, because it didn’t even know what the word was.
It’s like when ‘passive house’ came in. I used to talk to people before about what I did, and all the time it took paragraphs upon paragraphs, and then all of a sudden, I could just say ‘passive house.’
BJ: Oh, yeah. We gotta rename it. Maybe a contest.
CB: People have a lot of fear. There are some who say “buildings need to breathe,” and things like that, when, really, what you need is managed ventilation. Too much cold air in the winter just dries you out and can make you sick and too much warm air in the summer can bring too much humidity and that can condense in the air conditioning. So, having a good, managed ventilation system is what’s important.
Compartmentalization is always best: no bugs, no smoke, none of your neighbors’ cooking fumes, none of the quality of life issues that drive people insane — and it really helps for soundproofing.
And the joy of it! On our building tours, we would put a boombox in one apartment, and then have everyone run to the next unit, and they couldn’t hear it. Just the look of joy on a New Yorkers face at that! People would say, “oh, you turned it off!” and then they’d run over and see that it wasn’t off. Yeah…things you can do for people’s quality of life. But you’re right, that we don’t have a good name for it.
BJ: What would need to change to make this the new normal? Awareness? Is it training for construction managers and contractors? Is it more codes?
CB: Well, given that we have codes for firestopping and soundproofing that may not be followed all the time, I don’t know if it’s really more codes.
I know that I get hired again by the same client, because I’ve created a high-quality thing. And I might get the job versus someone else. I mean, I’m always up for thinking that making smart business decisions brings new and more business, and also educates others who aren’t doing that yet. For a long time, that was a big thing that my practice was doing: showing people what’s possible so others join in on it.
I think that perhaps the demand from the market could be huge. But people don’t know that some things are even possible. It’s not even out there that you could live in a unit where you’re not hearing your neighbor’s stereo — people just don’t even know that. So, I don’t know, really how it starts. I’m fairly certain I was the first person in New York using the term “compartmentalization,” except for maybe some people in Weatherization. And now it’s a word, and now it’s out there. We’ll change the word! We’ll make it a better word!
BJ: I’ve been listening to Passive House webinars and all the time it’s “This technique, which, as you know, Chris Benedict pioneered in New York,” so I think your legacy there is secure.
CB: Well, it’s nice to have a legacy. And how does it catch on, you know? I don’t do my work this way because it’s code or anything else. I have some spirit in me that really wants to do this. And, I know that spirit is in others, though it’s not everyone. Hopefully those others get hired and get jobs.
BJ: To your point, if the clients wanted it, and they knew that they wanted it, then they would ask for it. And if you didn’t know how to deliver it, you’d have to learn it, right?
CB: Yes! There’s an entire class of consultants, but until architects really learn how to incorporate this into their work, it’s not going to go anywhere. Consultants just add to the fees, so architects learn less. It’s not really hard. It’s just more being persistent.
BJ: What are you finding inspiring right now? I know subsidies aren’t your favorite thing, but we have a lot of money coming in to support faster mobilization on decarbonization and on energy efficiency. Is there anything that you’re really excited about?
CB: I’m actually really excited about my work on Passive House with tenants-in-place. We have a job going right now, and we’re just learning tons and tons and tons about it. So I think that’s one of the big things in my life right now is figuring that out because this is a gigantic area to attack. Another thing though, is that I’m also working on a 13-story modular senior housing building, so I’m learning about modules: what’s good about them, where they’re appropriate, and getting a module to be Passive House. That’s also super cool. And then also, I have some thoughts about a thing I want to manufacture and it’s in the very, very early stages, so I can’t really talk about it at all, but it’s really one of the crazier ideas I’ve had!
I’m lucky to be in a field that just keeps giving. There’s obviously a lot of work to be done and people that are willing to try it. It’s just a very, very good place.
Interview edited for clarity by Tom Sahagian and Rory Christian.