Cork oaks, broadleaf evergreen trees that flourish in Mediterranean climates, feature rough barks that can grow to be as much as 12 inches thick. Its bark can be harvested every nine years without killing the tree and, with fairly minimally processing, can be transformed into star-quality sustainable insulation products. Although most commonly used in its board form, cork insulation can also be found as an EIFS or spray applied product. From small ADUs to multifamily buildings, and in both new construction and retrofits, cork has been a sustainable solution in a variety of projects.
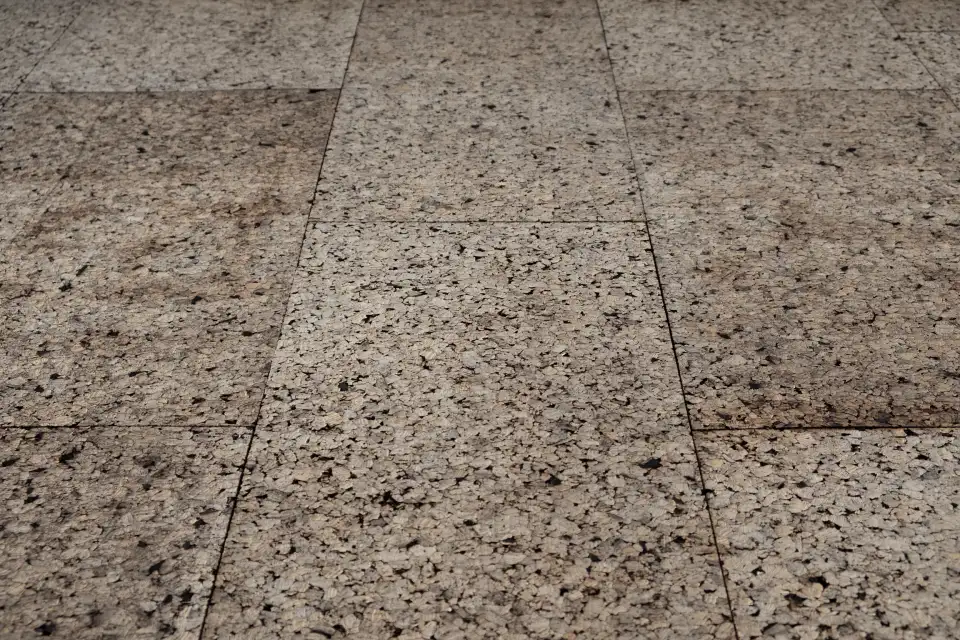
Corky Tales
A deep appreciation for green building is what led Sean Conta, who started Targa Homes in Seattle in 2018, to consider cork. A former Phius rater and Built Green verifier, he brought on Matt Kull in 2021 as a site supervisor and together they build one or two houses a year. While every project emphasizes sustainability and high performance, his clients rarely come to him specifically for a Passive House. However, once Conta explains the benefits of airtight construction and continuous ventilation, they tend to be sold on those concepts. As Conta says, “Rarely do I get a negative response to good indoor air quality.” As smoky events happen more regularity in Seattle, his clients are gaining an increasingly tangible appreciation of healthy indoor air.
While an understanding of the benefits of Passive House may be on the upswing for Conta’s clients, the embodied carbon of their projects has not yet become a concern for most of them. Still, as Conta says, “My real feeling here is that it isn't the client's responsibility to know the right way to build regarding embodied carbon or Passive House methods. That's my job as a professional.” So, he has been taking a deep dive into the upfront carbon piece of construction.
His research into low-carbon materials led him to cork, and he was impressed by its carbon-negative and renewable properties—particularly that they don’t have to cut trees to harvest the cork. “The carbon-sequestering aspect was attractive,” he says, as was the limited ingredient list in the insulation product. “A rigid cork panel is literally ground-up cork that has been heated and molded. And, the cork itself kind of excretes binders to stick it together, so there's no glue involved,” he explains. The clincher for Conta in deciding whether to present this option to his client was that he knew several builders who had tried cork boards. “That client had no experience with green building, but I think some of these concepts—an all-natural material that's renewable and low carbon—can resonate with really anyone,” he adds.
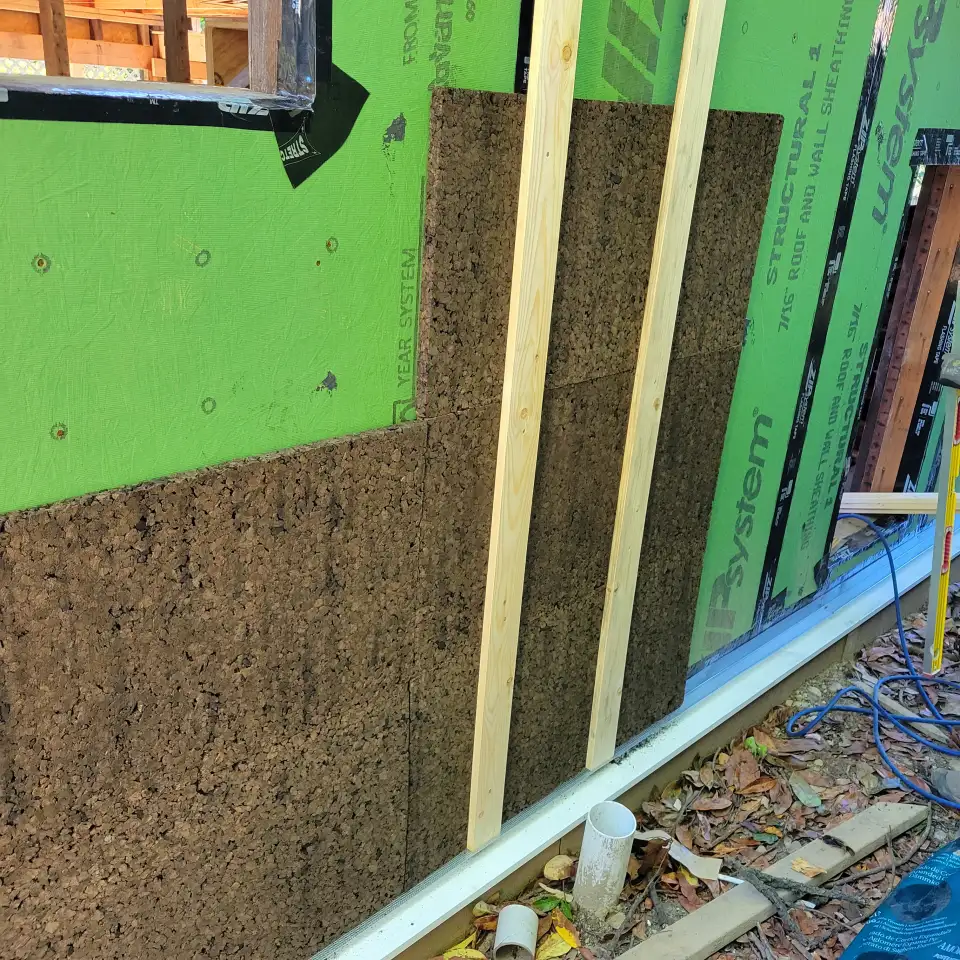
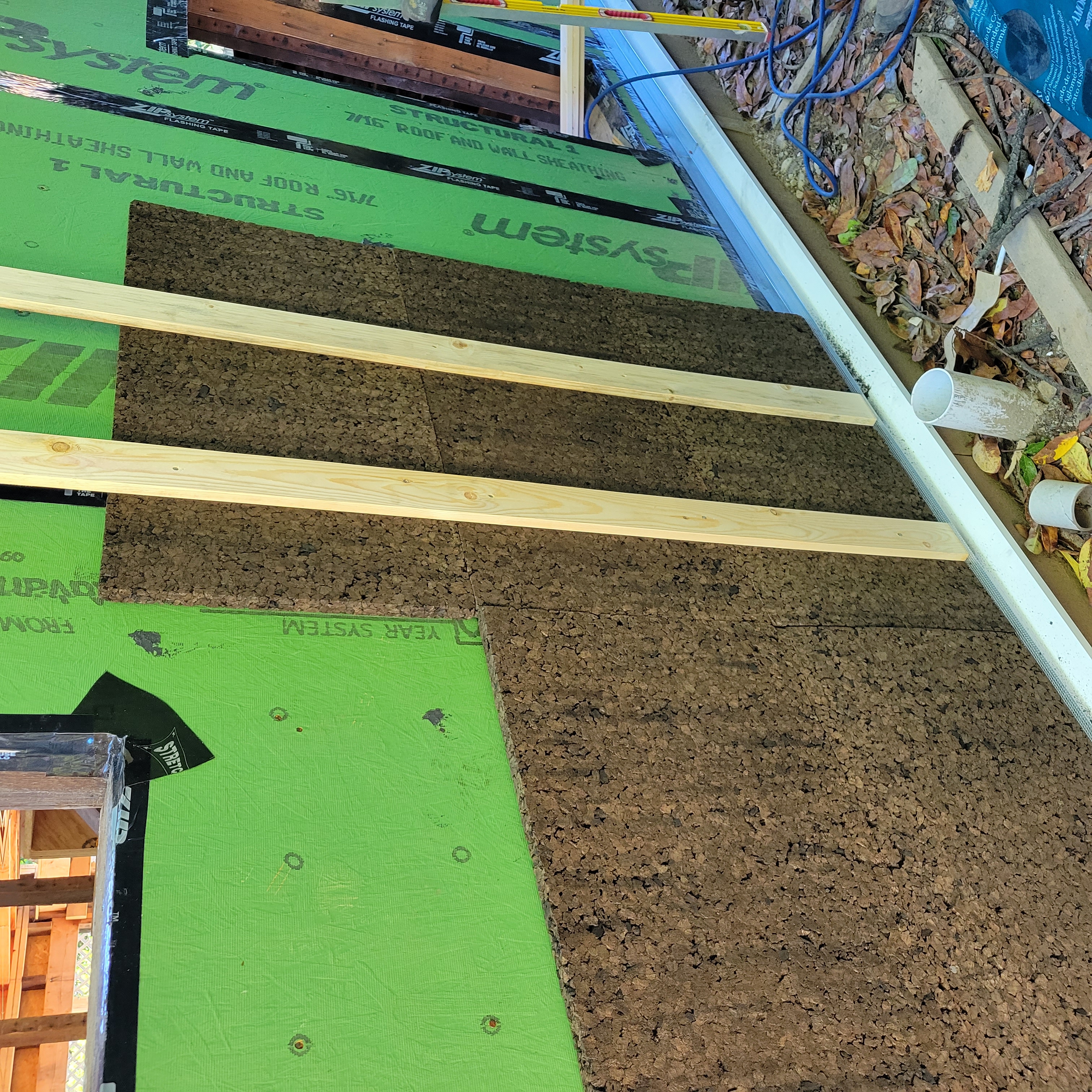
The rigid cork board installed on the outside of the sheathing. Photo courtesy of Sean Conta.
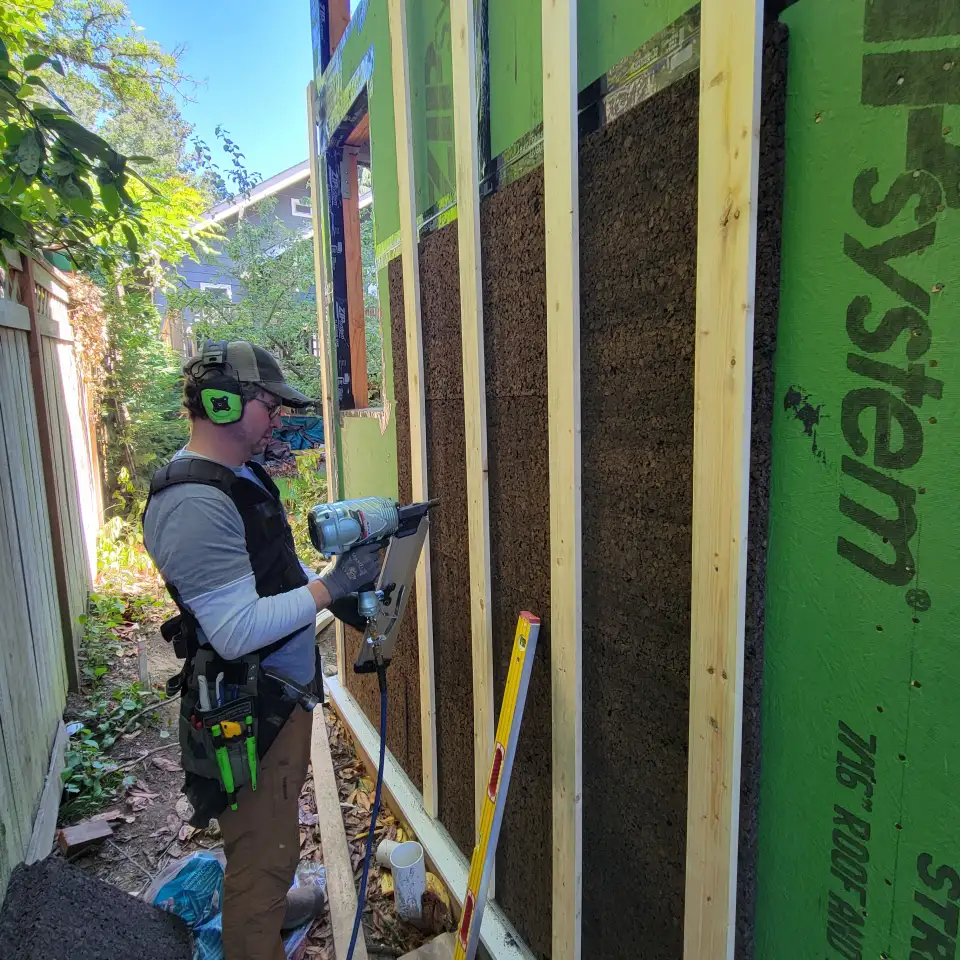
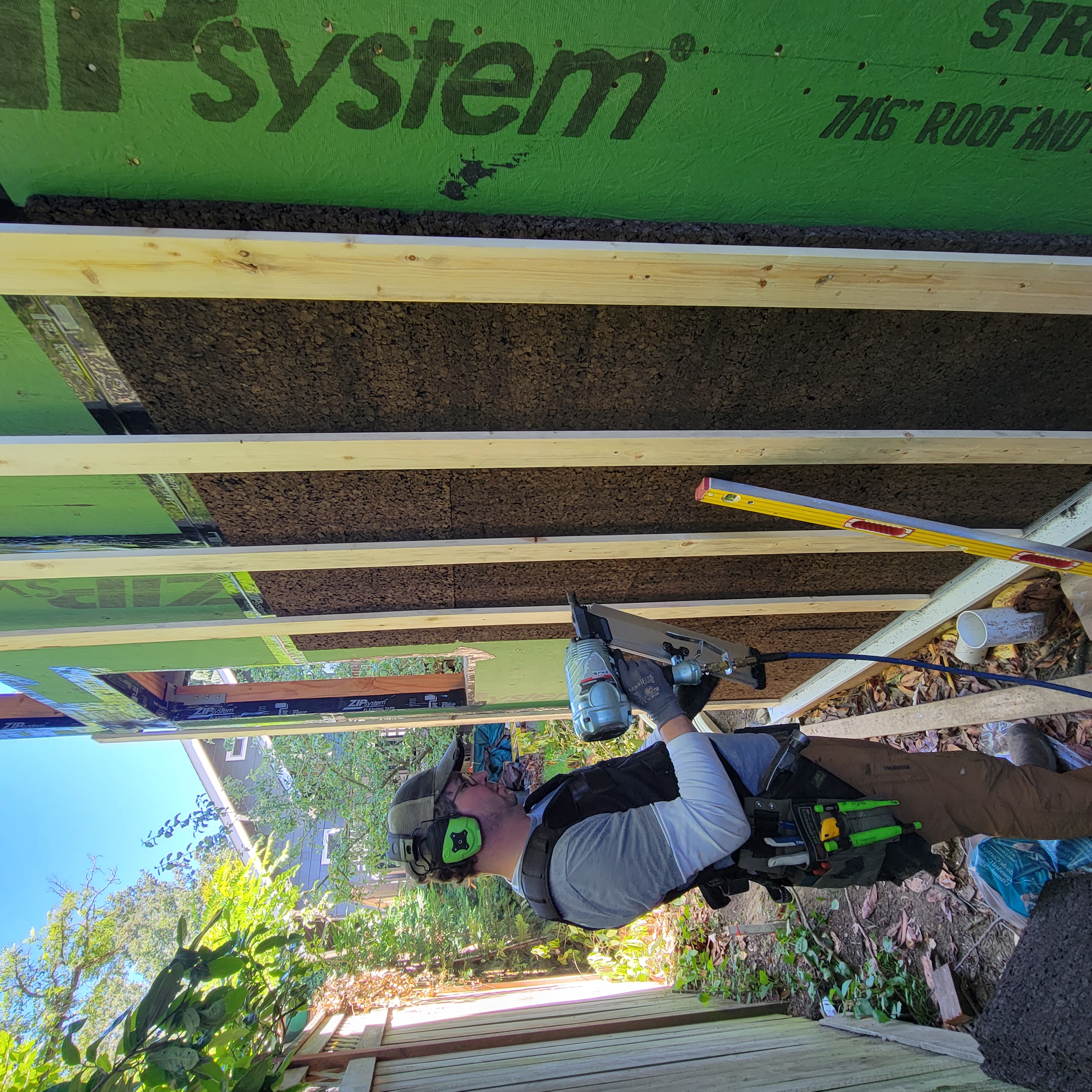
Installing the 1x4 rainscreen battens to hold the rigid cork board. Photo courtesy of Sean Conta.
Other cork attributes that Conta found appealing were its R-value contribution, at R-4 per inch, and that it doesn’t create a waste product. “I hate throwing things away, and it's inevitable in construction,” he says. “Cork, you could literally grind it up and just till it into the soil on your site, if you wanted to.” It’s also easy to cut with a circular saw.
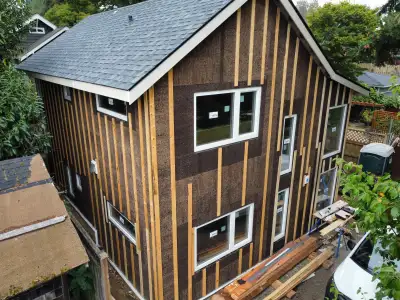
Having sold their client on the virtues of cork, Conta and Kull found it easy to incorporate the product into their standard wall assembly. They use a 2x6 standard framed wall with the Zip system sheathing for an airtight and weather-resistant barrier (WRB) layer. They applied the rigid cork board to the outside of the sheathing, relying on the 1x4 rainscreen battens that they always install to hold the cork.
“Technically, what we do is attach the bottom row of cork boards along with the 1x4, putting the first screw in. Then, we work up from there, slipping the subsequent cork sheets in behind the batten,” Conta explains. They had discussed first putting up all the cork, tacking them up with cap nails, and then coming back and and layering on the rain screen battens, but they found they preferred their one-step method. As the cork boards were only 1-inch thick, they were able to affix the battens with standard 3.5-inch construction screws.
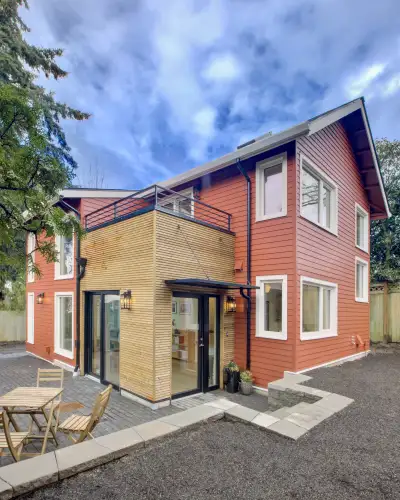
Conta does have some considerations about working with cork, namely that it’s a little delicate and floppy, so has to be handled somewhat carefully to avoid breaking the boards. He also recommends getting a white Pica marker to mark them. As much as he enjoyed working with cork, he has not found the right opportunity to use it on subsequent projects.
At a much larger scale, the team working to create the 131-unit Meridian at Petaluma North Station in Northern California is planning to use cork as both the exterior insulation and siding, although city approval for the plan is still pending. Developed by Danco Communities, the low-income apartments will be spread across six 3-story buildings and one 4-story building. The project will also include large green spaces, office spaces, therapy rooms, a gym, and a multipurpose room. Construction is slated to begin in 2025.
The all-electric development is targeting a grid-sipping status, with a large—just under 1 MW—solar array and a likely 4-MWh battery storage plant. “We should still be able to keep the project off grid 96% of the year,” says Sean Armstrong, partner and managing principal of Redwood Energy. Redwood Energy consults for developers of affordable housing and zero-net-energy buildings, conducts green building inspections, and leads research efforts and trainings on electrifying everything.
For the Meridian project, the team is specifying cork boards for the cost savings. “It actually saves money compared to a cementitious fiber board siding that we put three inches of foam underneath—although that’s not an option we are considering,” Armstrong explains. The savings lie in cork not necessarily having to be covered over, while still providing R-12 of continuous insulation for the 3-inch-thick boards. Redwood Energy is exploring possible coatings, such as latex paint, to add further protection to the exposed cork siding, and some of the cork will be covered with metal siding for design purposes. “I have had cork on my tiny house bathroom here for the last 10 years, and it's untouched, and it's great on the west, east, and north sides. The south side has gotten kind of crinkly,” adds Armstrong.
“We may end up with a combination of some finished exposed cork siding in some areas, and lower grade cork applied under metal siding in other areas,” says Garrett McSorley, principal of McSorley Architecture and the project architect, adding, “In all cases we would still have a 1-hour fire rating.” To the interior of the cork, the proposed wall assembly would include a weather-resistant barrier (WRB), 5/8-inch Type X exterior gypsum board, ½-inch plywood, 2x6 framing insulated with R-21 Knauf EcoBatt, and 5/8-inch Type X gypsum board.
Redwood Energy is working to keep the Meridian within budget by optimizing the project’s balance of sustainability and cost efficiency. Water heating will be supplied by 120-V heat pump water heaters that will be within the envelope to supply free cooling—a big plus during California’s increasingly warm summer seasons. That large battery storage system is planned to be sourced through ReJoule, a company that evaluates used batteries for a second life. Other green features include edible landscaping and a greywater system for irrigating non-edible landscaping.
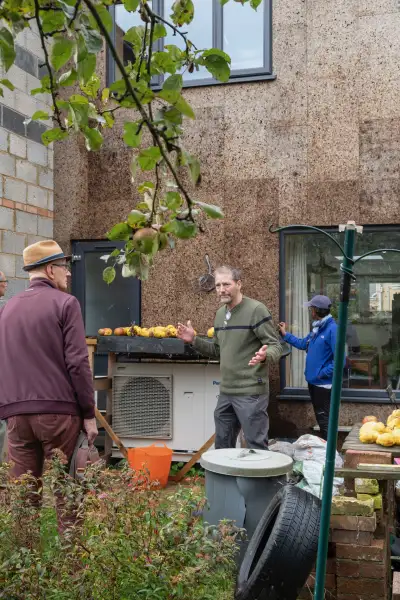
Roughly 5,000 miles away, in Cambridge, England, Paul Kershaw has been stepping through a phased, largely DIY, retrofit of his home. Although he hasn’t set a specific energy target for the project, he has been aiming to sharply improve the home’s energy efficiency, mostly by externally insulating the facades and upgrading the mechanical systems. “My main driving force has been affordability, because I'm doing the retrofit on a budget,” Kershaw explains. He embarked on planning his retrofit in 2017.
In the early stages of his project, he had received a government grant to insulate his attic with spray foam—a choice he now regrets. “What I didn't know before that went in was the carbon cost of that product,” he notes. That error turned into a search for more information on natural insulation products for his walls, among other retrofit aspects. “I didn't come from a background in building or engineering, so I very much started from knowing absolutely nothing, and that was part of the learning process,” he points out.
His brick-and-block home was originally constructed in 1968. A 50-mm (2-inch) cavity between the brick and the blocks had been filled a number of years ago with blown-in fiberglass. The next step to further insulate his home was to add continuous exterior insulation, and by this time he had learned about the advantages of biomaterials and vapor permeability. He chose cork for the rear of the house and wood fiber for the front, as he worried that the local planning council would not approve of the look of cork from the street.
When preparing for the cork installation, Kershaw first hired a builder to do what he could to even out the brick, using mortar to fill in gaps and create as flat a plane as he could for the cork to be adhered to. Kershaw bought a specialized fixing mortar, Isovit E-Cork by SecilTek, made from lime binder, cork aggregate, and a small amount of cement to cover the surface of the brick, which the first 80-mm (3.2-inch) thick layer of cork boards got pressed onto. This layer was then mechanically attached to the brickwork using thermally broken fasteners to minimize thermal bridging. The final 20-mm (0.8-inch) facade cork boards were then attached solely by mortar.
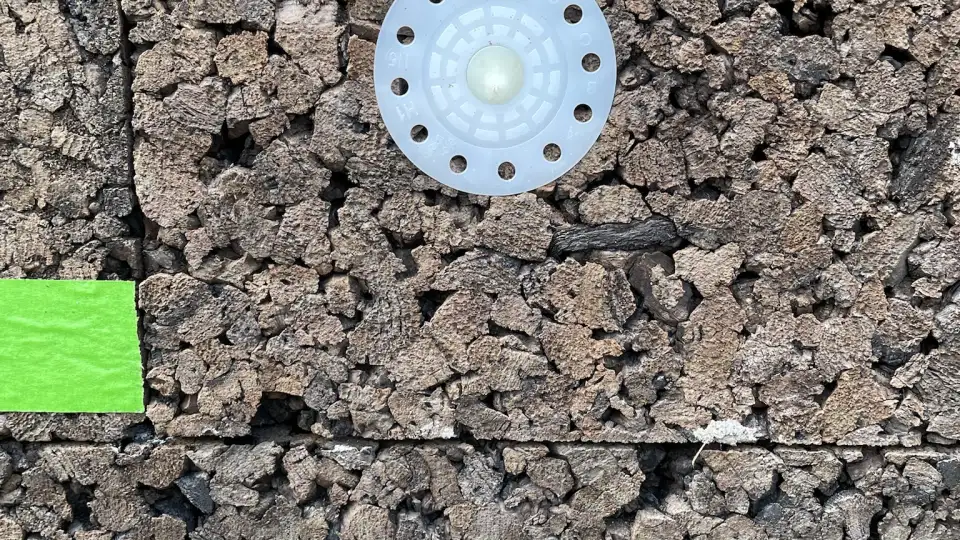
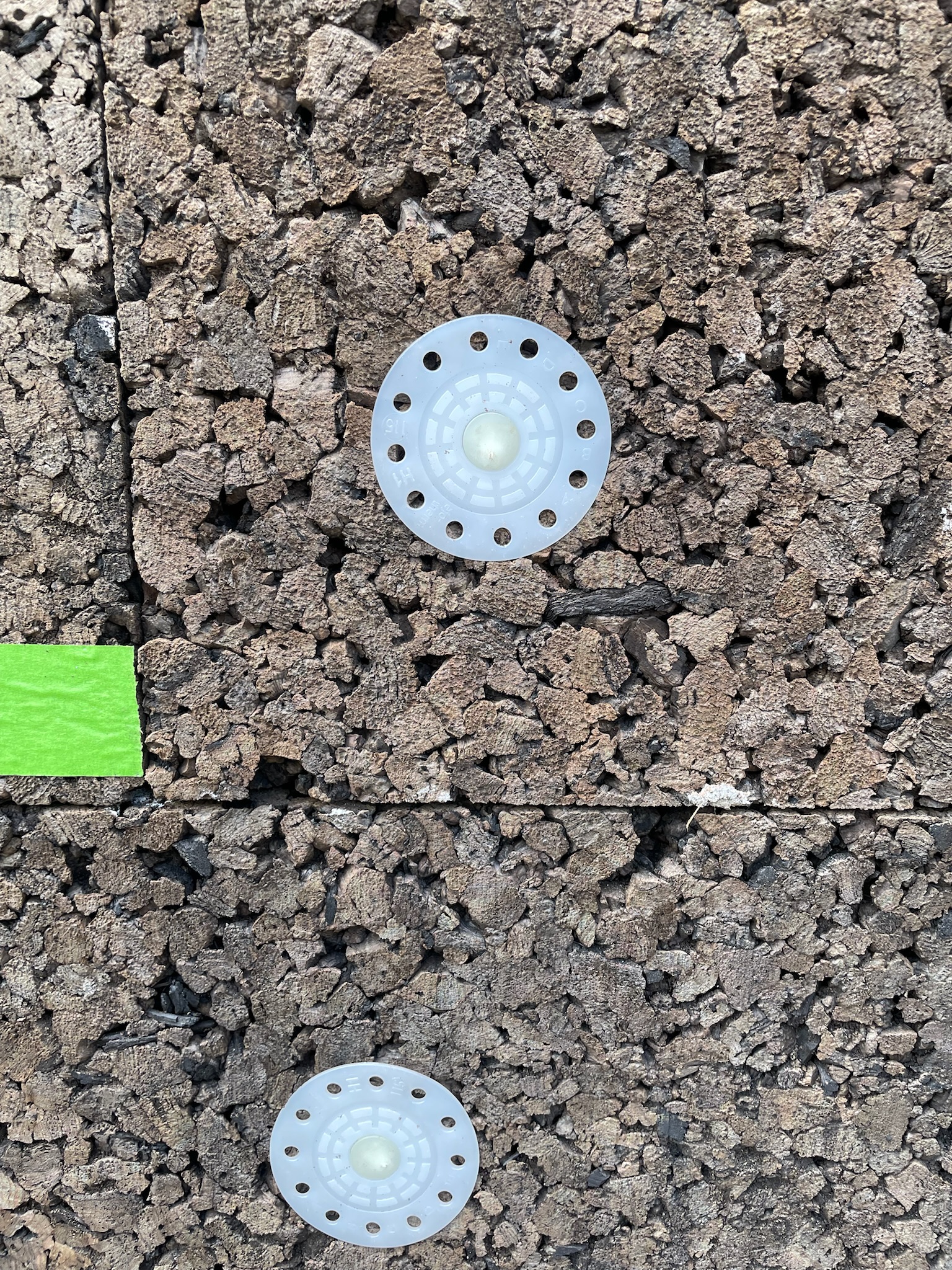
A closeup of the thermally broken fasteners. Photo courtesy of Paul Kershaw.
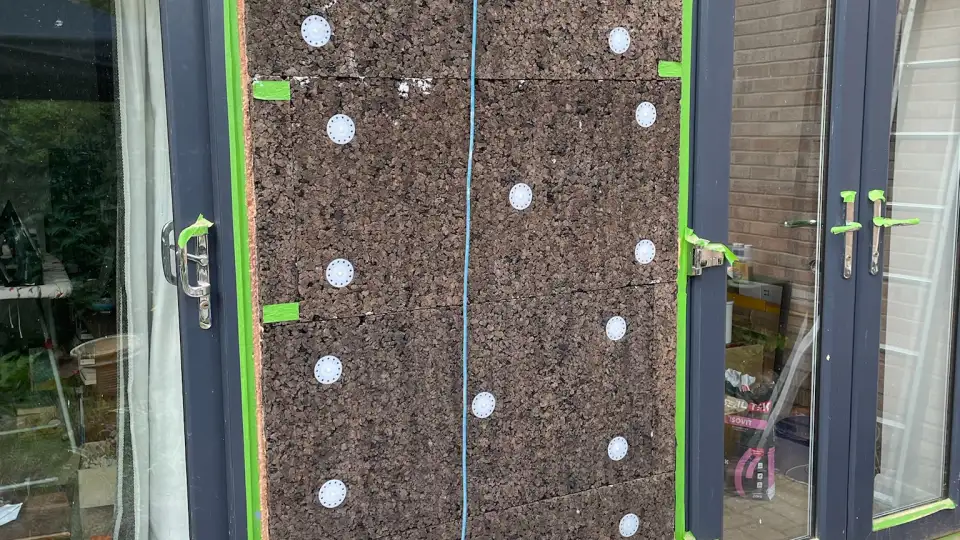
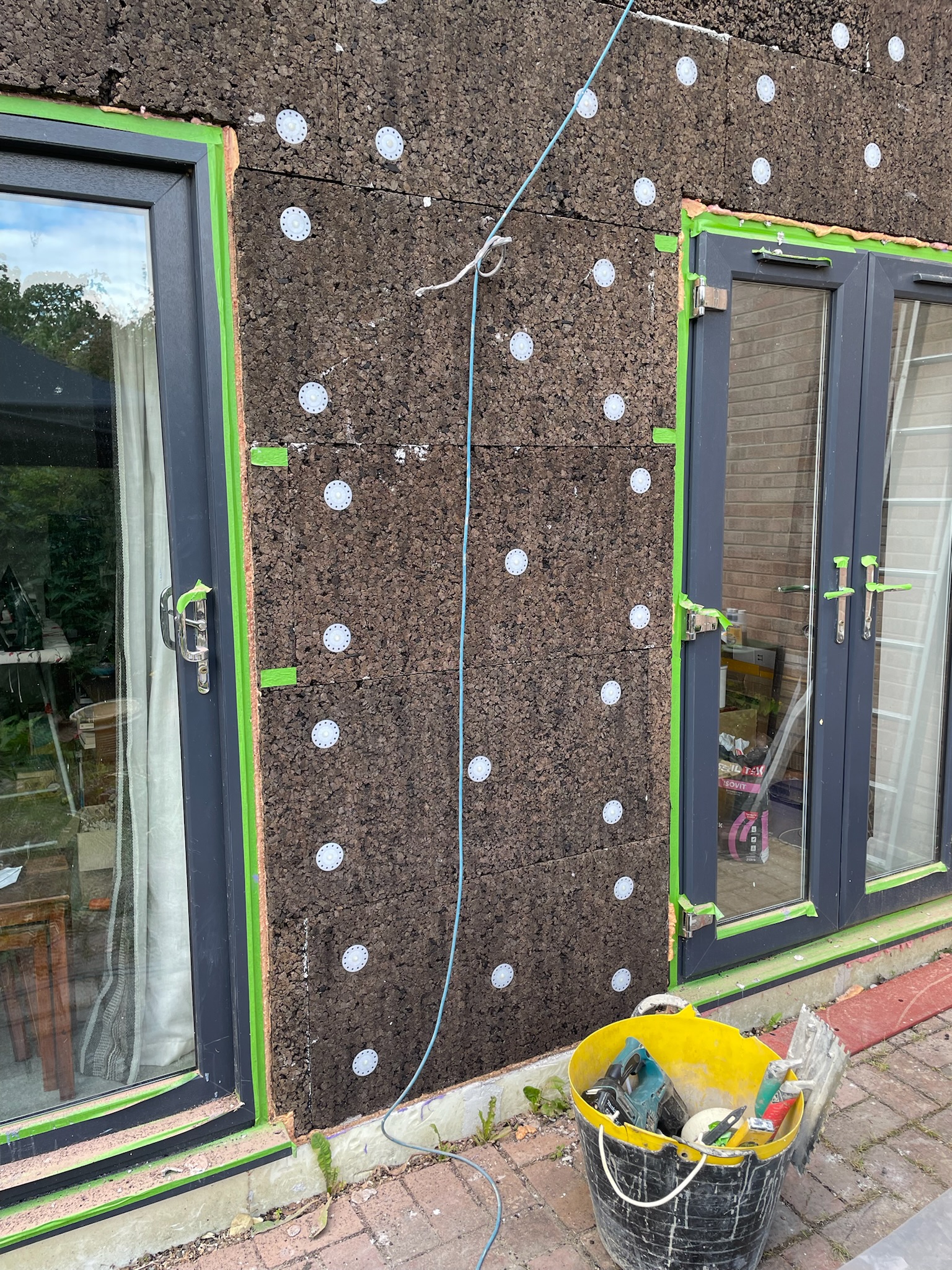
The thermally broken fasteners dotting the wall. Photo courtesy of Paul Kershaw.
“The builder had never worked with cork before either, so there was quite a learning process, but it was a really quick learning process. He would find that, on the second day, he could do almost twice as much as on the first day,” he remembers. Indeed, as the days went on, the contracting team shrunk from three to two people, and they got quicker and quicker.
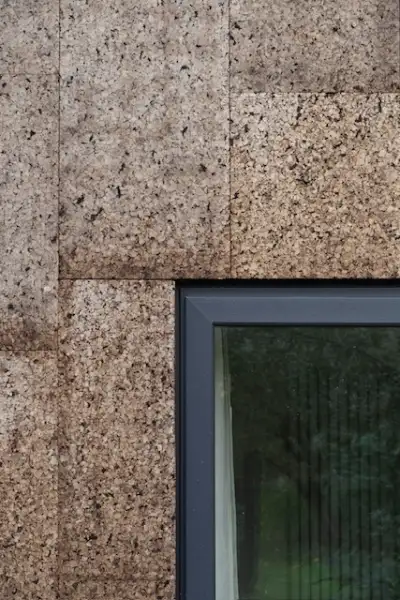
Like Conta, Kershaw and his building team also found that the boards have to be handled with care to prevent pieces snapping off. “But also, when bits do break off, it's very easy to reaffix them almost invisibly, so it's a very forgiving product in that respect,” he explains. Another pro tip that they learned through experience was that the builder had to be careful when pressing the boards on top of the mortar, which turned out to be a white-colored product, so that no excess mortar would get squeezed out and show up as a white line.
The cork went up earlier this year, but before the installation could happen, the boards had sat in Kershaw’s backyard for almost a year. “During that time, it did not attract any attention from rodents, insects, or birds, so that was a very good sign,” Kershaw says. So far, he’s quite happy with the cork’s performance and look. He does point out that the dark brown cork boards get silvered in a few days by the sun, which changes the product’s appearance. “Instead of being very dark brown, it goes a silvery brown, which is just absolutely gorgeous,” he notes happily.
As the cork was less costly to buy and install than the wood fiber insulation, he wishes in retrospect that he had braved the design review process and specified the cork for the front façade as well. He later heard of two other houses featuring cork facades in the Cambridge area. “The architect I worked with has since gone on to work on another property with cork as well, so it's certainly gaining in popularity. And, it's raised a lot of interest here in the retrofit community,” Kershaw enthuses.
Top image courtesy of Lambertian Architectural Photography.