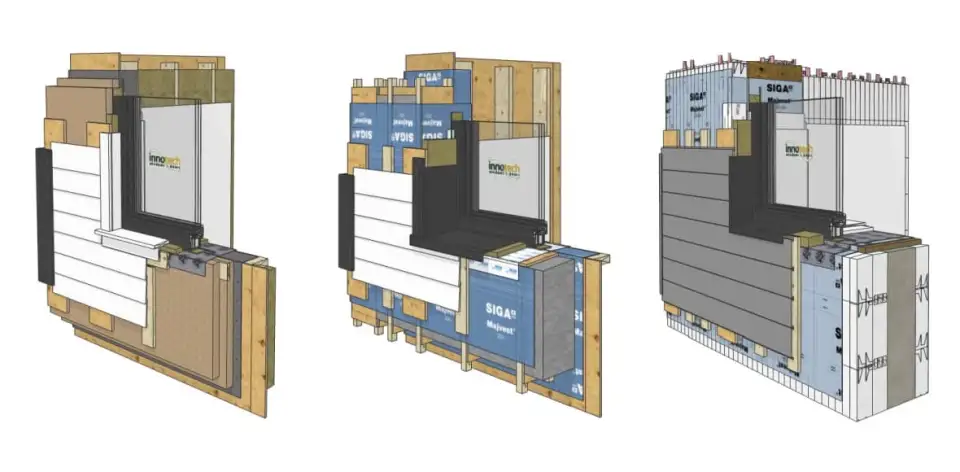
Uninsulated 2x4 walls and single-pane windows installed with nailing fins covered up by a sloppily applied layer of flashing tape isn’t going to cut it anymore. While it’s true that these kinds of assemblies may still meet code in some jurisdictions, they are noisy, drafty, and often plagued by temperature irregularities. In addition to making homes less comfortable, these issues can lead to inflated energy bills and even affect the durability of the home.
We can do better—for the planet and for our clients.
True, designing and constructing wall assemblies capable of Passive House performance requires extra attention to detailing and more sturdy components (including triple-pane windows), but the results are undeniably superior to code-built buildings. High-performance building methods are designed to be highly energy-efficient (airtight and well-insulated), water resistant (mold free), comfortable (thermal and acoustic comfort), and durable (climate resilient). When combined with mechanical ventilation and air filtration systems, as is the case with Passive House construction, wall assemblies that use high-performance building methodologies and components also lead to homes with better indoor air quality and a drastic reduction in allergens and dust. These are all benefits that building occupants notice from day one.
Choosing a Wall Assembly
Of course, building a home with high-performance wall assemblies is not a one-size-fits-all endeavor. Teams have to consider the local climate, any specific code requirements to the area, the project’s specific performance requirements, material and skilled-labor availability in the area, and personal preferences. However, there are some guidelines that can help make the process easier:
Work with an experienced design and build team, including trades and laborers, where all members possess the right mindset, skill set, and training.
Get the entire team on the same page and host regular meetings to maintain a clear, shared vision to prevent siloing and redundancies.
Set performance and budget targets early and prioritize them from the start.
Have a well-thought-out and well-communicated strategy for barrier layers, layer connections, assembly sequencing, and all subsequent air sealing.
Choose the most suitable building materials.
Install windows in the middle of the wall; nail flange installs perform significantly worse and will increase the risk of mold at the window to wall connection (thanks to Enrico Bonilauri of Emu Passive for this tip).
Install all building materials as per manufacturer instructions.
Following these guidelines will help ensure that any wall assembly performs as it should.
In addition to these recommendations, Innotech has designed four wall assemblies with suggested components and techniques for different climates that can be utilized to achieve high-performance targets, including net-zero energy and Passive House. Each example also demonstrates how Innotech’s windows can be installed within the rough opening and in relation to the barrier layers. Moreover, each window installation strategy can be applied to most types of wall assemblies, though the most appropriate wall assembly and window installation strategy depends on project-specific factors, especially climate.
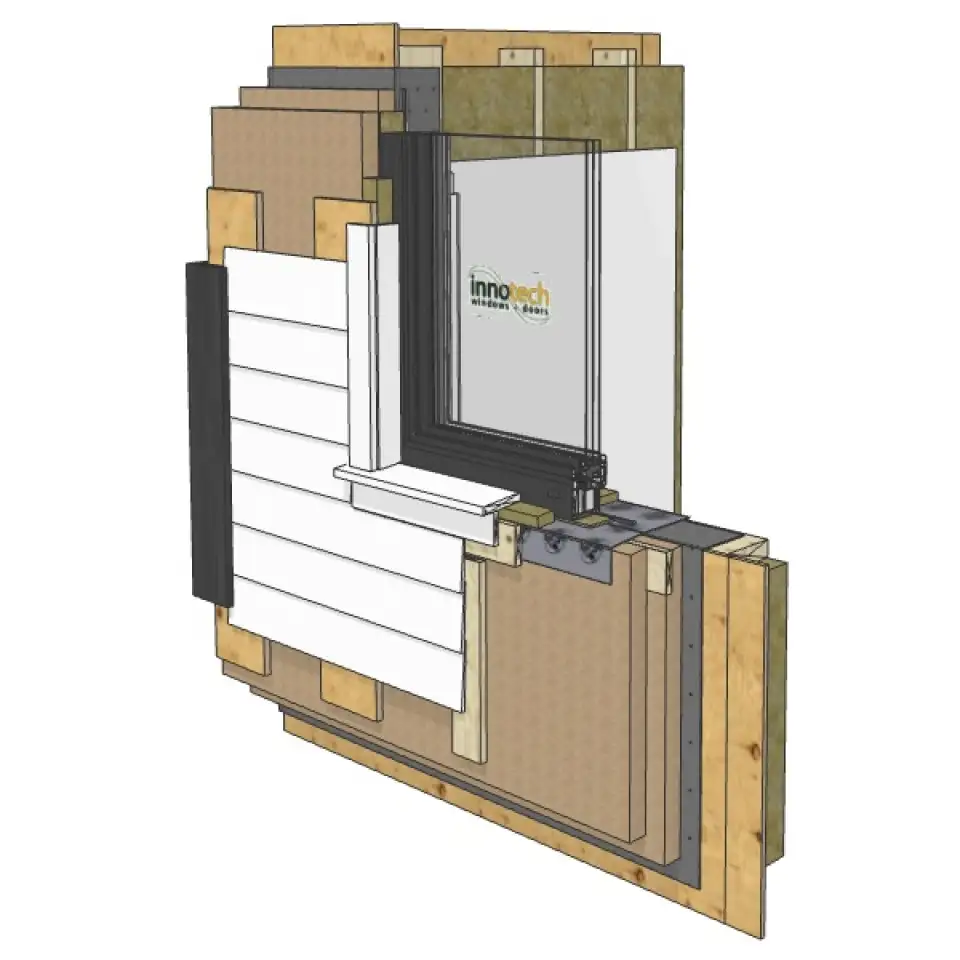
Wall Assembly #1: Split-Insulated Wall (R-30)
The split-insulated 2x4 wall assembly is a versatile, cost-effective, and relatively simple way to achieve excellent thermal performance without extremely thick walls. It does so by utilizing different types of exterior and interior insulations. One of the most crucial considerations for split-insulated walls is the ratio between these two types of insulation, since the ratio modifies the dewpoint within the wall assembly and can increase the risk of condensation and mold. To better understand how climate can affect the optimal exterior-interior ratio and to learn about the best practices in design, download the paper from Morrison Hershfield, Considerations for Exterior and Split Insulated Net-Zero Energy Ready Wall Systems.
In the example below, the split-insulated wall has an insulation ratio (exterior to interior) of 61% to 39%. This balance is ideal for mild climates where the average low in winter is -5°C (23°F). A colder climate would require additional exterior insulation for optimal balance.
Components of this wall include:
Exterior
Pro Clima Solitex Mento 1000 3-layer air-tight, vapor-permeable weather resistive barrier (WRB)
2 layers of Gutex® Multitherm 60 (2 3/8” thick [R-8.5 per layer]) wood fiberboard insulation
Rainscreen
Hardie® Plank Lap Siding in Arctic White
Interior
Rockwool Comfortbatt® insulation (3.5” thick [R-14]) in the 2×4 cavities
Drywall
Window Installation
Innotech Defender 88PH+ XI window installed off-center towards the exterior of the wall
Pro Clima Tescon® Vana 150 at the sill
Rockwool Comfortbatt® insulation in the installation cavity and over-insulation at exterior face and the interior face of the window
Traditional wood trims on all four sides
Note: The window is installed using the anchoring method with rod and caulk on the interior face for air and water sealing. Tape is used on three sides (jambs and head) of the exterior for shedding.
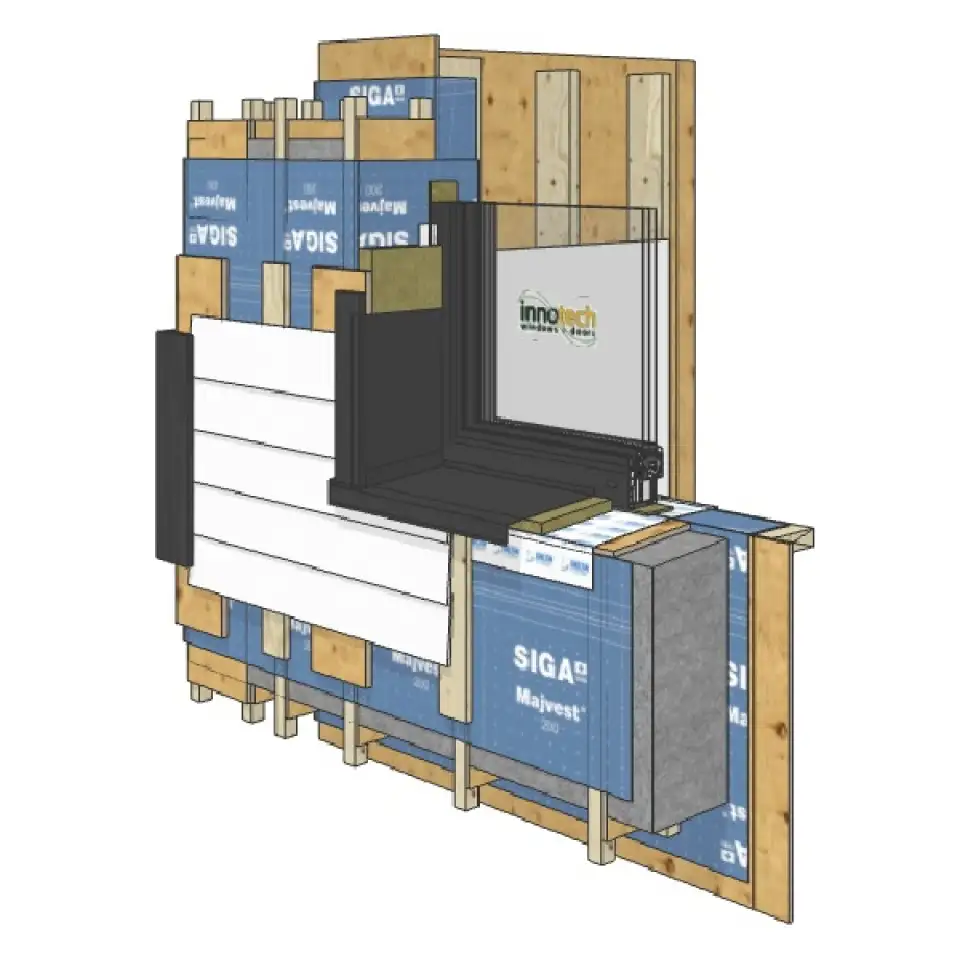
Wall Assembly #2: Stud Wall with Larsen Truss (R-33)
The second assembly includes a Larsen truss, which is an additional, lightweight, and non-structural component on a stud wall assembly that is attached to the exterior of a wall. These versatile extensions allow for significant outboard insulation to achieve high R-values and are typically less expensive to construct than traditional double stud walls (two 2×4 or 2×6 walls). As Larsen trusses are not required to shoulder any roof load, they are frequently used in retrofits.
The Reimagine Buildings Collective brings together building professionals stepping up to tackle climate change.
The below stud wall with Larsen truss is a 2×4 framed wall with 8” deep Larsen trusses built with 2×2 and plywood. (Fun fact: The Larsen truss system was developed by an Edmonton, Alberta builder named John Larsen in 1981.)
Components of this wall include:
Exterior
SIGA Majvest® 200, vapor-open, wind and rainproof façade membrane
Larsen trusses with cellulose insulation
Second layer of SIGA Majvest® 200 (this outside layer of WRB retains the cellulose and protects it from liquid water)
Rainscreen
Hardie® Plank Lap Siding in Arctic White
Interior
No insulation (2×4 wall acts as a service cavity)
Drywall
Window Installation
Innotech Defender 88PH+ XI window installed off-center to the interior of the wall
Delta® flashing at the sill
Rockwool Comfortbatt® insulation in the installation cavity, and over-insulation at exterior face and the interior face of the window
Metal window flashing on all four sides to complement the siding with a metal sloped sill and wood trims
Note: The window is installed using the anchoring method with SIGA Fentrim® 430 grey tape on the four sides of the interior face for air and water sealing. SIGA Wigluv® 60 is used on the exterior jamb and head for an additional water shedding surface.
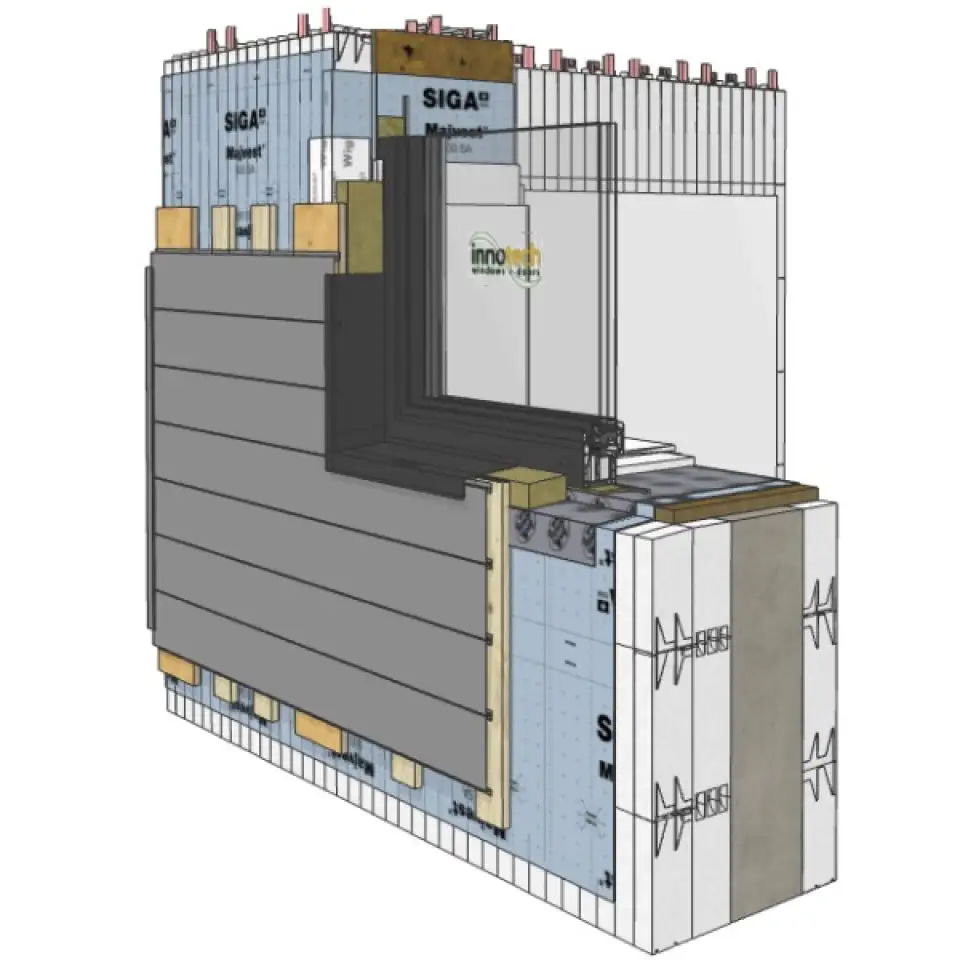
Wall Assembly #3: Quad-Lock® ICF Wall (R-43)
Using insulated concrete form (ICF) walls presents several benefits: high R-values with continuous insulation, built-in moisture resistance, high sound transmission resistance, long-term durability, and reduced construction times. The following wall assembly made with Quad-Lock® ICF panels provides a true R-value of R-43 or U-value of 0.14 and is constructed using (non-HBCD fire retardant) expanded polystyrene (EPS) foam.
Components of this wall include:
Exterior
SIGA Majvest® 500 SA – Self-adhering, vapor permeable membrane on exterior wall and window rough opening
Rainscreen
KBS Paneling System – Wood grain, 24-gauge sheet metal siding from Klassen Building Supplies
Window Installation
Innotech Defender 76TS window installed towards the exterior of the wall
Protecto Sill Pan Flash™ Wrap at the sill
Rockwool Comfortbatt® insulation in the installation cavity and over-insulation at the exterior sill
Over-insulation of jamb and head faces, and interior four sides, with (non-HBCD fire retardant) EPS from Airfoam Industries
KBS Paneling System integrated metal window flashing on all four sides to complement the siding with a metal sloped sill
Note: The window is installed using the anchoring method with a L-angle, rod and caulk on the interior face for air and water sealing. SIGA Wigluv® 60 is used on the exterior jamb and head for an additional water shedding surface.
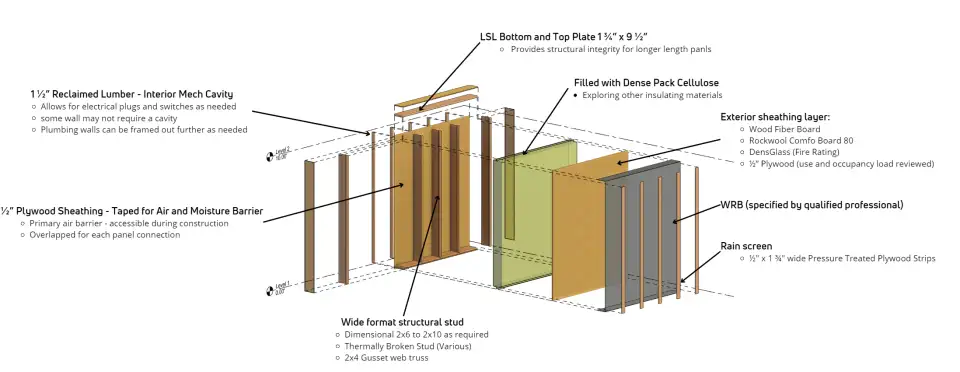
Wall Assembly #4: BOSS Prefabricated Engineered Panels
Prefabricated panels are another option. There are several manufacturers capable of building walls, roofs, and floor panels offsite in a controlled environment without having to face inclement weather conditions or other delays. This helps to improve QA/QC and to significantly cut down on the time it takes to assemble the panels once they’ve been delivered to the job site. As this technology has evolved considerably, many prefabricated engineered panels are now capable of achieving Passive House levels of performance.
BOSS prefabricated engineered panels represent one such system. In addition to performing up to the Passive House standard, their panels are manufactured with low embodied carbon components and 100% electric and renewable sources of energy. The result is a highly sustainable construction material that is low-waste, high-quality, and affordable.
One thing that BOSS panels do not come equipped with are windows and doors. Consequently, high-performance window and door manufacturers like Innotech work with BOSS to ensure:
Superior air, water, and structural performance to complement high-performance prefabricated walls.
Customization to allow the windows and doors to be designed for each prefabricated wall or building solution, since one size does NOT fit all!
The successful incorporation of the windows and doors into the factory prefab wall assembly process to simplify completion and improve processes.
Additionally, there are logistical difficulties that Innotech helps to sort out with the transportation of the panels and the windows. In the case of operable windows, the sashes can be removed for shipping and installed on-site. This reduces the risk of damage to the glass during construction and transportation. For fixed windows, the insulated glass units (IGUs) can be installed on-site to reduce the risk of damage to the glass during construction and transportation.
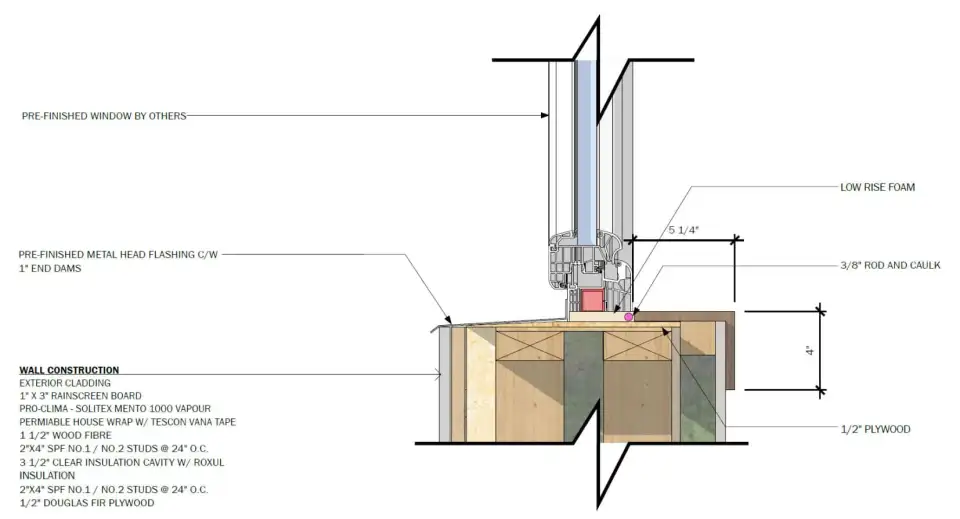
When working with prefab panels, Innotech windows and swing doors are installed using the anchoring method with strap anchors. This installation method provides two important benefits for prefabricated construction:
The anchoring method provides the flexibility to install the window or door anywhere within the wall cavity (rough opening) to achieve the desired overall wall performance, natural ventilation, and functionality.
The anchoring method also protects the windows and doors from movement of the walls, including movement during transportation and installation (an important consideration for prefabricated walls or other off-site construction), naturally occurring building settlement, and long-term movements from wind loads and daily operation.
As these examples showcase, high-performance wall assemblies require more attention to detail and better components, but the extra effort leads to stronger, more resilient homes and healthier, more comfortable interior spaces. Ultimately, building better is about having the right team, a clear plan, and selecting and installing the most appropriate building materials – including windows and doors – for every project. Let’s talk about your next high-performance project!