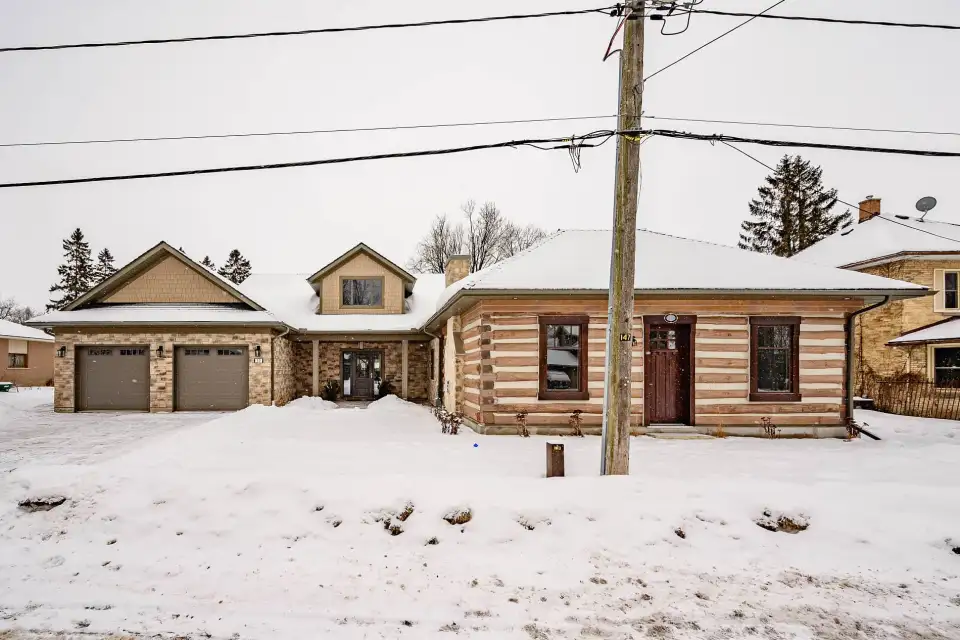
The homeowner purchased an eroding log schoolhouse in Elora, Ontario with an ambitious vision to turn it into a high-performance spec home. Quantum Passivhaus was hired to tackle this project, based on the firm’s prefab Passive House experience, and took it beyond expectations. In this ultimate makeover plus addition of a new 3,400sf structure, the finished home protects a local heritage while incorporating innovative Passive House design, products, and craftsmanship. The new part of the home was built using Quantum’s prefabricated panels.
The guidelines set by the local Wellington Heritage Committee to protect the heritage features of the log school house required that heritage appreciation of all three sides of the log structure had to be preserved from both inside and outside. Essentially this requirement meant that no visible insulation could be added. To add to the high-performance hurdles, having the three exterior sides of the log schoolhouse exposed greatly increases the surface area-to-volume ratio of the building.
This project also faced several other significant challenges such as having to lift the three-wall heritage building in order to install a foundation under it and put it back into place without breaking a window! To move the three walls while keeping the two corners intact, despite not having a floor or roof to help tie it together, we designed, engineered, and manufactured bracing, lifting, and connecting components for the task. (The three log walls had been estimated to weigh 11,000 lbs but actually weighed just under 30,000 lbs due to petrification of the wood, requiring a much heavier crane than anticipated, and even greater attention to technique and safety.) Less dramatic difficulties included low-hanging hydro lines, narrow site conditions, and shading of the site.
Design Solutions
As a solution, the Passive House-compliant addition and the heritage restoration were designed as two thermally separated zones; the slab connection between the zones are thermally broken with Type 3 EPS curbs, the Quantum Type 1 exterior wall, and a CAL exterior door. The areas are also separated by an air barrier. To improve the heritage log wall performance, where possible, we ‘hid’ mineral wool insulation between the heritage logs under the chinking.
To make the best use of fiscal resources, and to treat the building as a whole where possible, the mechanicals are mostly shared—except for the gas heat source in the heritage zone, which was required to make up for the heat loss through the heritage walls. To improve winter performance throughout the building, the SHGC of specific windows was increased, resulting in a decrease in heat load/demand while keeping summer heat load/demand minimized by vegetative shading and overhangs. From an energy modelling perspective, we were reminded that it is key to have your site shading evaluated and verified early in the process and planning!
Care was taken to select components that were PHI certified or modelled using PHI-approved protocols to aid in energy modelling: Zehnder Q, Elite 92 Windows via Vetta Building Supplies, and the now-certified Quantum Wood Frame Opaque Wall Systems. The Quantum Passivhaus prefabricated components were installed in two days, with the finishes completed by the builder over the next six months.
Construction Costs
This project was a collaboration between Quantum Passivhaus and Remley Custom Homes. We have broken down the cost components of the scope of work we provided under the “Design and Energy Modelling,” “Essentials Package,” and “Plus Package” services.
The “Essential Package” is $114.02/ft2 and includes: supply and install of Quantum Passivhaus engineered raft slabs for the addition, heritage building, and garage; Quantum Passivhaus panelized system (certified walls); floor joists and truss systems; mechanical systems and ventilation; and windows and doors. This cost also includes travel, accommodations, and crane/trucking.
The “Design and Energy Modelling Package” is $0.53/ft2 and includes two phases of conceptual drawings, PHPP energy modelling as a guide to the design process, permit drawings, structural engineering, product and spec sheet evaluations, project budgeting, and flowchart scheduling.
The “Plus Package” is $35.20/ft2, including demolition, excavation, utility services, and site safety costs.
Removing, reinstalling, and restoring the heritage schoolhouse came in at $16.43/ft2.
Energy Performance Results
This project’s final blower door test result was 0.48 ACH50. The PHPP modelling shows an annual heating demand of 17 kWh/m2 and a heating load of 11 W/m2. If the homeowners were to seek certification, this home achieves the heat demand thresholds of PHI’s Low Energy Building. It is just 2 kWh/m2 more than the heat demand criteria of a Classic Passive House and just 1 W/m2 above its heat load threshold.
Team: Project Lead: Abby Xerri, Quantum Passivhaus
Designer: Fabienne Lehmann, Quantum Passivhaus
Energy Modeller: Angie Horner-Xerri, Quantum Passivhaus
Mechanical Design: ZON Engineering Inc.
Prefabrication provider: Quantum Passivhaus
Engineering Raft Slab provider: Quantum Passivhaus
Foundation and Superstructure Installer: Quantum Passivhaus
Award: 2020 Adaptive Reuse Using Sustainable Design Award from Heritage Centre Wellington
Technical Project Details
Climate Zone
Cold
PH Main Structure Size
3398 sq. ft (excluding garage, porch and heritage)
Heritage Structure Size
616 sq. ft
Construction Details
Permit Application
Residential New Addition and Restoration
Walls Type
Quantum PHI certified wall “Type 1.1”. Wood frame, cold climate glass mineral wool prefabricated panel with insulated service cavity. Pro Clima membranes.
Wall Thermal Performance
0.093 W/(m2K) R61 (effective) with negative thermal bridge values
Link to certificate: https://database.passivehouse.com/Media/certified_components_v2/certificate/pdf/z_Quantum_A1.1_20200403.pdf
Foundation Type
QP Engineered Insulated Raft Slab using EPS foam, 15mm rebar and a 6” concrete slab @ 32 MPa, 4” perimeter thermal skirting
Foundation Thermal Performance
0.086W/(m2K) R66
Roof Type
Scissor trusses 24” o/c (ready for solar) and cathedral trusses 24” o/c
Roof Thermal Performances
Cathedral Ceiling: 0.057W/(m2K) R100 (35% of ceilings)
Flat Ceiling: 0.070 /(m2K) R81 (65% of ceilings)
Floors Types
1) insulated raft slab on grade and 2) hybrid open-web floor truss for intermediate floor
Attic Insulation Type
Blown-in Cellulose
Mechanicals
Heating, cooling & some dehumidification:
Passive House addition: Chiltrix system including air to water heat pump, distributing heating, cooling and some dehumidification via fan-coil units.
Heritage Restoration: Gas fireplace heat. Chiltrix cooling and some dehumidification
Ventilation (both) via Zehnder Q 450 with hydronic preheat
DHW (both) tank storage heated by Chiltrix System and inline electric heater.
Windows
Solkolka Elite 92, triple glazed
Ug: 0.53-56 W/(m2K)
SHGC: 0.63 south and 0.53 other
Average Uw installed= 0.92 W/(m2K)
*Over-framing was installed as part of the QP installation
Doors
CAL Artik Model Ud= 0.67 W/(m2K)