
Legalization is coming. Once a central battleground in the United States’ decades-long culture war, cannabis advocates seem to have won the battle over public opinion. A survey conducted by Pew that was published in April 2021 found that 91% of adults believe that medical marijuana should be legalized and that 60% believe that adult-use cannabis should be legalized.1 Even South Dakota, one of the more conservative states, voted to create a medical marijuana program and legalized recreational use last November.
While it's clear that legalization has ceased to be the partisan issue it once was, one issue that has largely been overlooked is the environmental impact caused by the sudden surge in the number of cannabis farms across the country. Though federal law allows state-to-state transportation of hemp (defined as Cannabis sativa plants with a tetrahydrocannabinol (THC) concentration of under 0.3% by dry weight), the interstate transportation of marijuana (defined as C. sativa plants with a THC concentration of 0.3% or above) continues to be illegal. Consequently, any state that has legalized adult-use marijuana must grow their own cannabis.
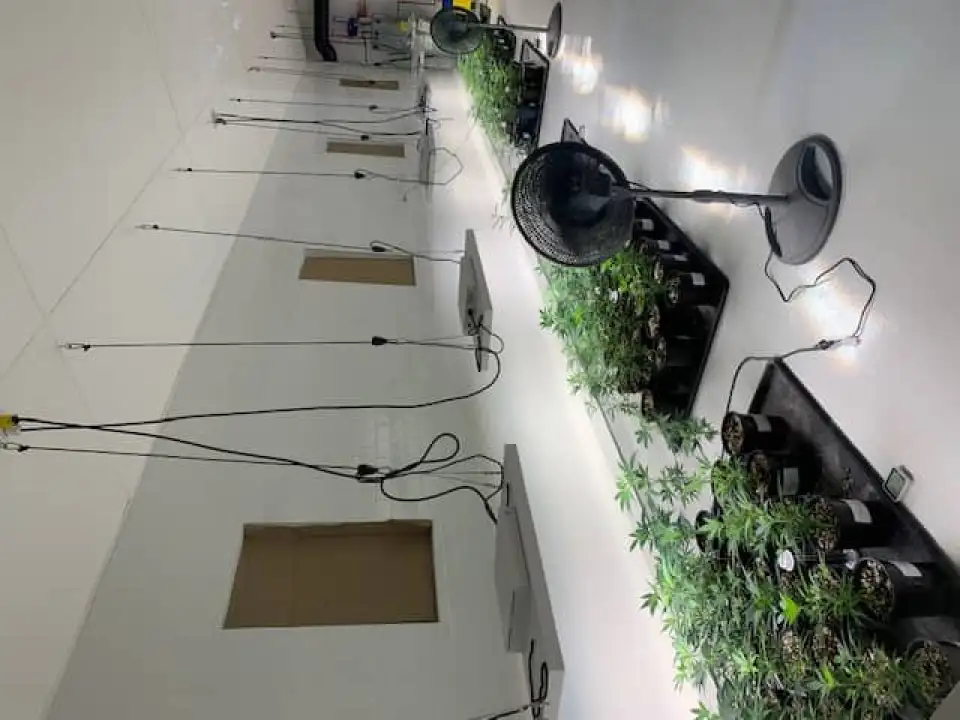
Some states, like California, have climates that allow for growing cannabis outdoors. Other states, however, must rely on indoor farms, which require energy-intensive grow lights and other mechanical equipment to regulate temperature, humidity, and CO2 levels. This is true even in those states that have yet to legalize adult-use marijuana but have created hemp programs for the production of non-intoxicating cannabinoids like cannabidiol (CBD) or products that can be created using hemp fibers.
What comes as a surprise to many cannabis enthusiasts is that indoor farming generates thousands of tons of CO2. In a mature cannabis market like Colorado’s, cultivation is believed to be responsible for 1.7% of the state’s greenhouse gas emissions, according to a paper that was published in Nature Sustainability in March 2021.² Though it is common practice to artificially increase CO2 levels in facilities to accelerate plant growth and create larger flowers containing more cannabinoids, the vast majority of greenhouse gas emissions stem from the use of natural gas to heat warehouse interiors and electricity from grids dominated by fossil fuels. Emissions could be significantly reduced by using passive design principles. The use of onsite renewables could further shrink these facilities’ carbon footprints.
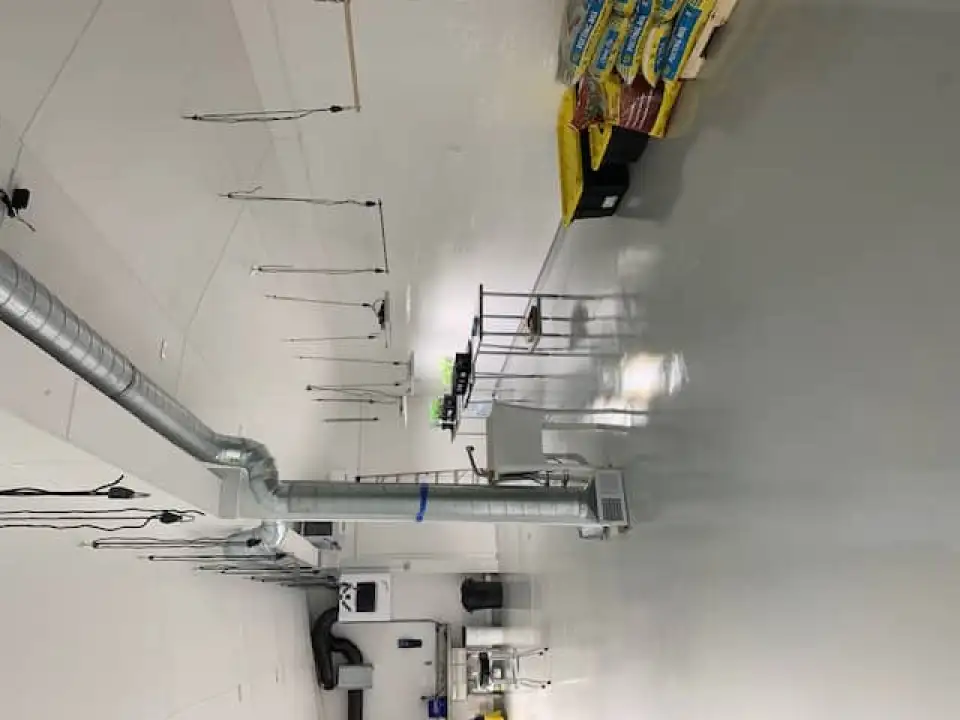
One small cannabis farm in Kentucky is doing just that. The owner, Tony Hammond, aimed to convert a 1,000-ft2 former horse shed into a grow house for hemp. To succeed, he needed superior ventilation to avoid cross pollination and a way to maintain precise climate conditions to ensure the plants did not exceed THC content thresholds due to their size and technically become marijuana. If they did, they would have to be destroyed. Unfortunately, the original structure was poorly insulated and extremely leaky. It was simply not up to the task.
Hammond consulted with Sy Safi, a certified Passive House consultant and the founder and owner of Louisville-based UberGreen Spaces & Homes, about making high-performance upgrades. Safi established UberGreen to promote sustainable design practices a few years after graduating from the University of Cincinnati with a degree in civil and environmental engineering. In 2012, My Green Kentucky Home, a model of Safi’s design, became Kentucky’s first Net Zero Energy and Net Zero Water home.
Safi recommended incorporating several elements of Passive House retrofit design to meet Hammond’s initial budget and needs, with the hope that future upgrades could be made to further improve performance. The first order of business was to work on the building’s envelope. Given that there was no insulation to speak of and the initial blower door test revealed an ACH50 of approximately 33, this project was going to require some extensive work. The walls were retrofitted with 3 inches of polyiso and Henry’s Blueskin was used as the air barrier, while the roof was equipped with a 4.5-inch layer of polyiso. Safi then used AeroBarrier to further increase the airtightness to 3.0 ACH50. He created a Passive House-type barn door assembly using two 2-inch pieces of polyiso board wrapped in an air barrier membrane.
For the mechanicals, Safi installed two Zehnder Q units at either end of the building, ensuring a continuous supply of HEPA-filtered air even if one of the units fails or needs to be shut down for maintenance. The filtered air follows a trunkline across the ceiling, and then drops down to the floor so that it diffuses out at plant-level and pushes stale air up towards the exhaust. While having two units may seem like an unnecessary redundancy, Hammond was adamant about the need to reduce the risk of cross-pollination, as that could potentially ruin the crop. The grow house is also outfitted with a 220-pint dehumidifier and a 130-pint dehumidifier to aid with climate control. To power the dehumidifiers and the ventilation system, as well as the 18 230-Watt LED grow lights, a rooftop PV array was installed. Once the summer starts, Hammond believes that the system will produce as much energy as the grow house consumes.
Hammond has noted an additional benefit that came from using Passive House principles. Cannabis is a notoriously pungent plant, and you can often smell a grow house before you see it. By improving the building envelope and ventilation systems, Hammond reports that now you can only catch the slightest whiff when you are directly by the exhaust.
This pilot project in Kentucky reveals that Passive House design offers numerous benefits to the cannabis industry. It improves climate control, seals in potentially offensive odors, and makes facilities more efficient. If the industry is to cut emissions and become a truly green service, then business owners may want to take note of this project and replicate its use of Passive House principles.
1 Van Green T. Americans overwhelmingly say marijuana should be legal for recreational or medical use. Pew Research Center. Published April 16, 2021. Accessed April 30, 2021.
2 Summers HM, Sproul E, Quinn JC. The greenhouse gas emissions of indoor cannabis production in the United States. Nature Sustainability. March 8, 2021. doi: 10.1038/s41893-021-00691-w.