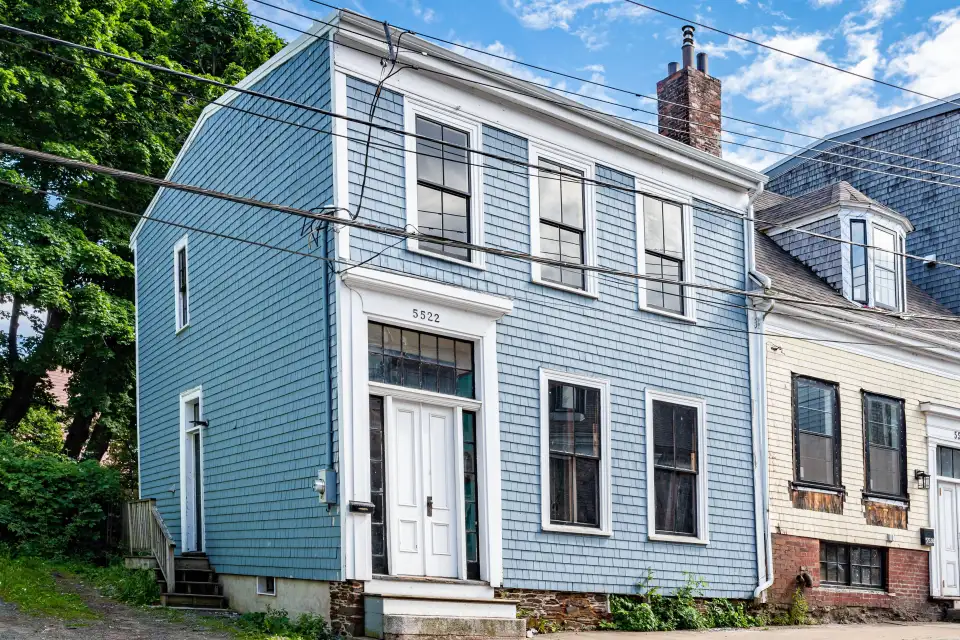
Construction is in progress on Halifax, Nova Scotia’s first Passive House retrofit, designed by Habit Studio and built by Root Developments. The project involves the conversion of a two-story 1850s home into office space for the Habit Studio team. Habit Studio is an eight-woman design firm that specializes in custom Passive Houses and sustainable whole home renovations.
When Habit Studio purchased the house, many parts of the building were in near-original condition, with no insulation, wood burning fireplaces, and 1930s-era electrical fittings. The timber frame structure is supported on a fieldstone foundation, and the windows are single glazed with wood frames, including some with original sashes and frames. The initial blower door test result was 24 ACH50 and the existing heating demand is at least 450 kWh/m2 per year.
The existing building has a simple form; however, it is attached to the adjacent building by a party wall and the north and east walls are built on the property lines, so adding insulation on the exterior is not a viable option. For this reason, Habit Studio has designed an internal retrofit and is following the Passive House Institute’s component method for EnerPHit certification, which offers more flexibility in meeting the targets when installing internal insulation. The expected post-retrofit heating demand, following the component method, is 53 kWh/m2a, an 87% improvement.
In addition to flexibility, the EnerPHit standard has slightly relaxed performance targets compared with a new-build Passive House project because of the limitations of working with an existing building’s geometry. Designers can choose between two modeling approaches, the energy demand method and the component method. The energy demand method works like a classic Passive House project, with heating demand and primary energy targets. However, in an EnerPHit project the targets vary based on climate zone. For Halifax the heating demand is 25 kWh/m2a. The component method outlines requirements for individual building components and does not limit energy demand. Both options have an airtightness target of 1.0 ACH50.
The existing wood shingles and board sheathing are being retained, so the retrofitted perimeter walls have been designed to be vapor open. They are being furred out, with staggered studs to make a 7-inch cavity, then filled with dense-packed cellulose insulation held in place with Intello Plus membrane. The low-pitched roof is also being furred down to increase depth for insulation and to simultaneously reinforce the structure to permit the possibility of a future third floor addition. The walls and roof will have U-values of 0.258 and 0.064 W/m2K, respectively. At the tricky junction where the wall sits on the stone foundation ProClima VISCONN liquid air barrier will be applied.
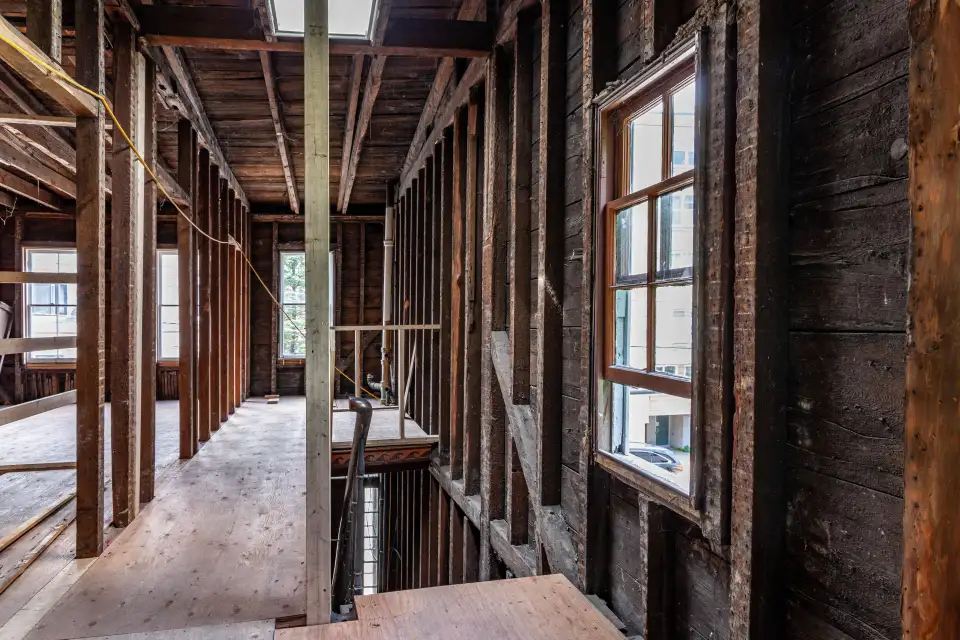
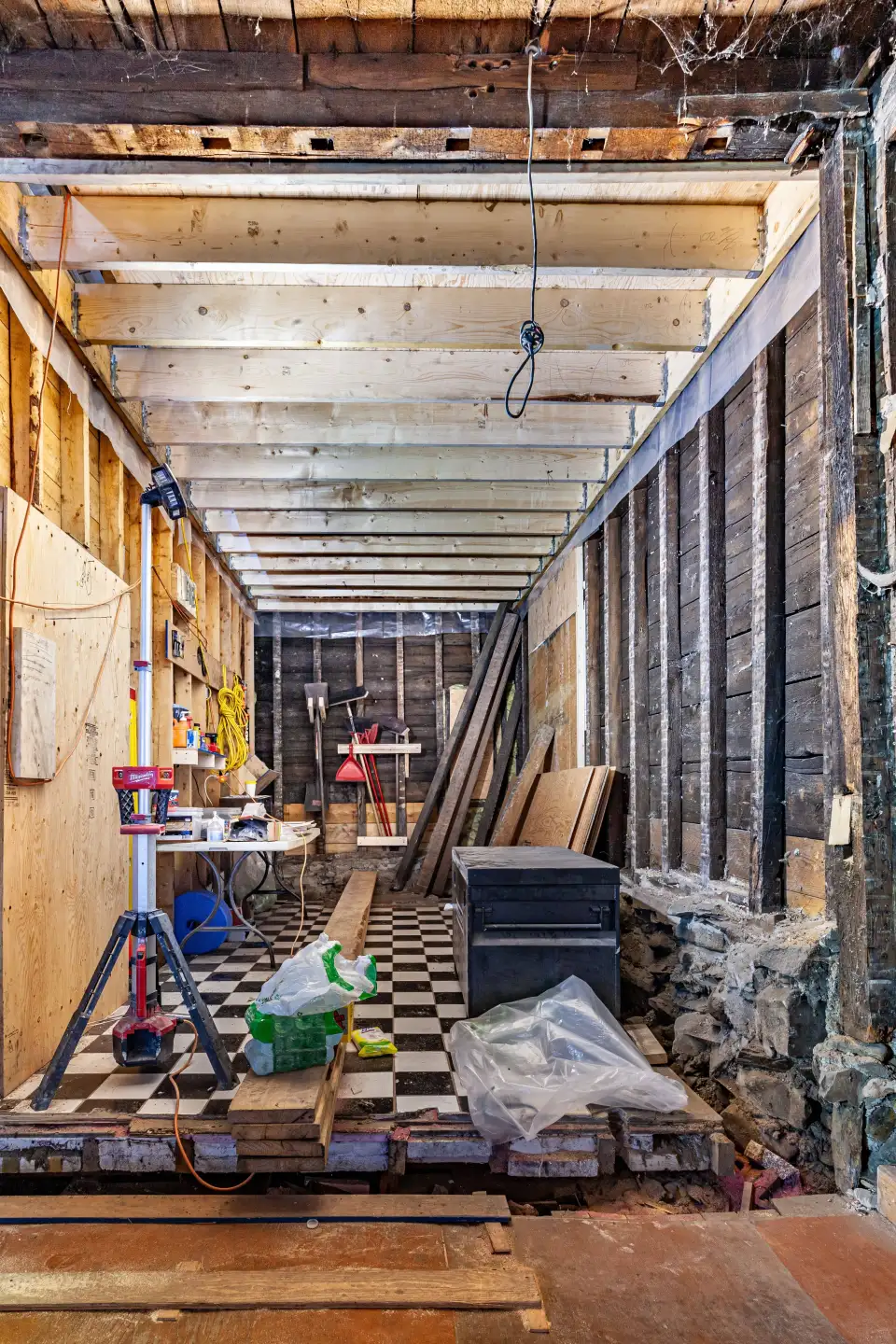
The city of Halifax is built on rock, and many old buildings experience unpredictable water ingress. For at least one full year the basement will be monitored to ensure any issues are resolved appropriately before covering up the stone. The basement space has a very low ceiling and will be used for storage and mechanicals. However, it will be heated and ventilated to ensure its air quality remains healthy and to keep the timber floor structure dry. Ultimately, the plan is to insulate the basement walls with 6 inches of Rockwool.
New windows and most doors are wood frame, aluminum-clad, triple-pane Elite 92 windows supplied by Vetta Windows with a U-value of 0.5 W/m2K and g-value 0.53. The main entry is a wood door with transom and sidelights sourced from Norwood to closely emulate the original entrance screen. This unit doesn’t meet Passive House specifications, but sourcing the door locally guaranteed the best fit. This decision was one of the main challenges in meeting the EnerPHit targets as the Norwood door specs do not meet the targets. Fortunately, the average performance of all windows and doors in the building just meets the component target.
Another design challenge was the position of the stairs on an outside wall, greatly limiting the thickness of the internal insulation. The depth of the wall at the stair between the first and second floor can be increased by just 2 inches. This section of wall will be insulated with R-24 nominal batt insulation.
The ventilation unit has not been finalized for the project, mainly because of supply chain concerns with preferred options. The selected model will be an ERV to provide humidity control as well as heat recovery. Heating will be provided with a dual head mini-split heat pump, with one head dedicated to the basement and one installed in line with the ventilation ducting.
Energy modelling predicts an 87% reduction in annual heating after work is completed sometime in late 2022 or early 2023, with electrical bills projected to be approximately $500 per year at current Nova Scotia electric rates, a savings of $11,000 per year.
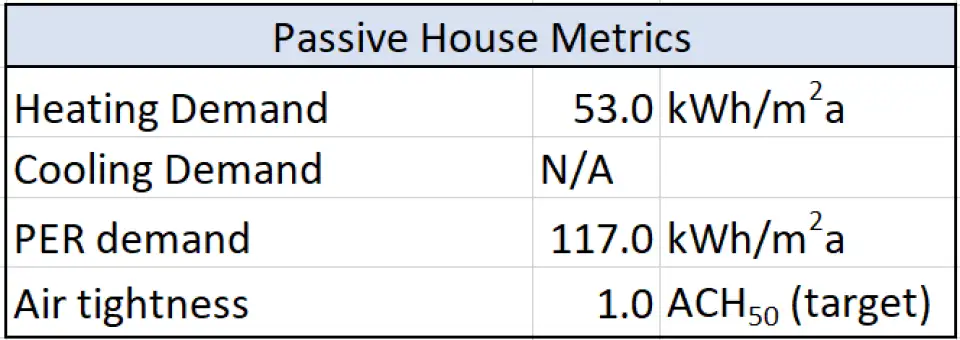