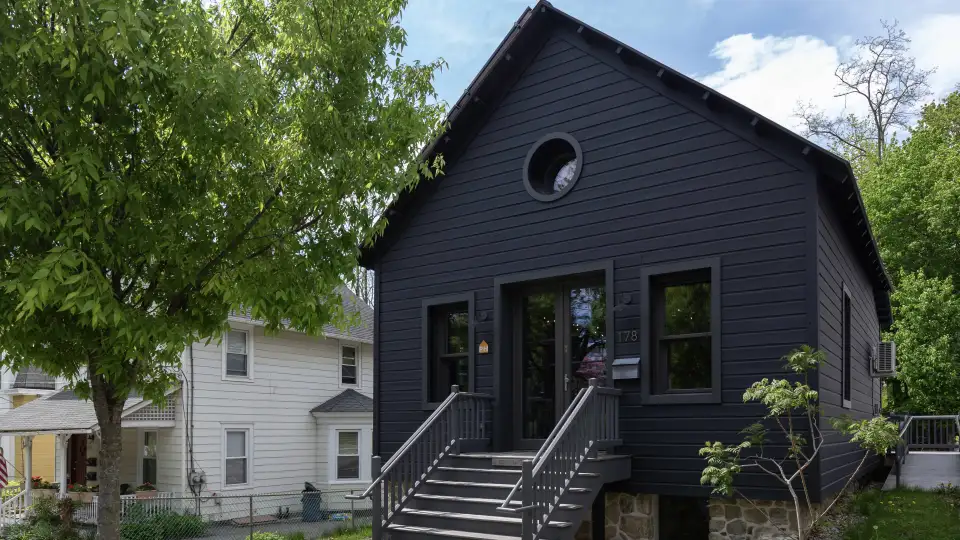
Feature photo Nicholas Doyl
The village of Cold Spring, New York sits on the eastern bank of the Hudson River nestled within the iconic Hudson Highlands, about 80 minutes north of New York City’s Grand Central Station by rail. The town is one square mile in area and home to approximately 2,000 people. Many of the exquisitely-preserved buildings along Main Street date back to the nineteenth century and have become home to several quirky cafes, a handful of antique shops, and one architecture studio dedicated to sustainability through high-performance building design: River Architects.
The Main Street studio is more than just a place of business for River Architects; it is also a manifestation of its commitment to using reclaimed and locally sourced materials, products with low-embodied energy, and Passive House design. Built in the middle of the nineteenth century, the timber-framed structure had many uses before being purchased in 2016 by the firm’s two partners, Juhee Lee-Hartford and James Hartford. Historic land-use maps show it in turn as a hot dog stand, a real estate office, a candy shop, as well as a “Chinese” laundry. Initially, it appears to have been built to accommodate a horseshoe shop with two large roof vents to allow for smoke from the hearth to escape that were still in place when the team bought the building.
The team knew that they needed to make significant upgrades to the entirety of the building’s envelope to certify it as a Passive House. They conceptualized a design solution where the original timber frame structure was exposed; stripping away the sheetrock and AstroTurf carpet revealed the distressed, horse-gnawed timber and hoof-worn flooring. The splintered, old siding nailed directly to the framing would be stripped away and replaced with pre-finished plywood sheathing. That sheathing, along with the timber frame, would compose the interior finish, reinforce the timber frame, and serve as the airtight layer. Larsen trusses were to be added to the outside, and rainscreen siding to match the original was specified.
The initial solution for the basement was to raise the building 3 feet higher to add headroom and to extend the original stone foundation up to the new height. The plan called for a structural thermal break across the top of the foundation wall and the timber frame, and for the interior of the stone wall to be insulated with reclaimed EPS foam. Lifting the building higher not only would improve the usable space in the basement but also would get the timber frame further from grade and the persistent termites that were wreaking havoc on the frame where it came into contact with the soil.
The ambitious design strategy received some pushback from the Historic District Review Board, the body in charge of overseeing the preservation of Cold Spring’s architectural legacy. As James Hartford told the audience of a Global Passive House Happy Hour in late August 2020, “Part of the board was pushing us to keep the building as it was—even the split, old, rotten siding—but the rest of the board realized that anyone else would be tearing this little building down.”
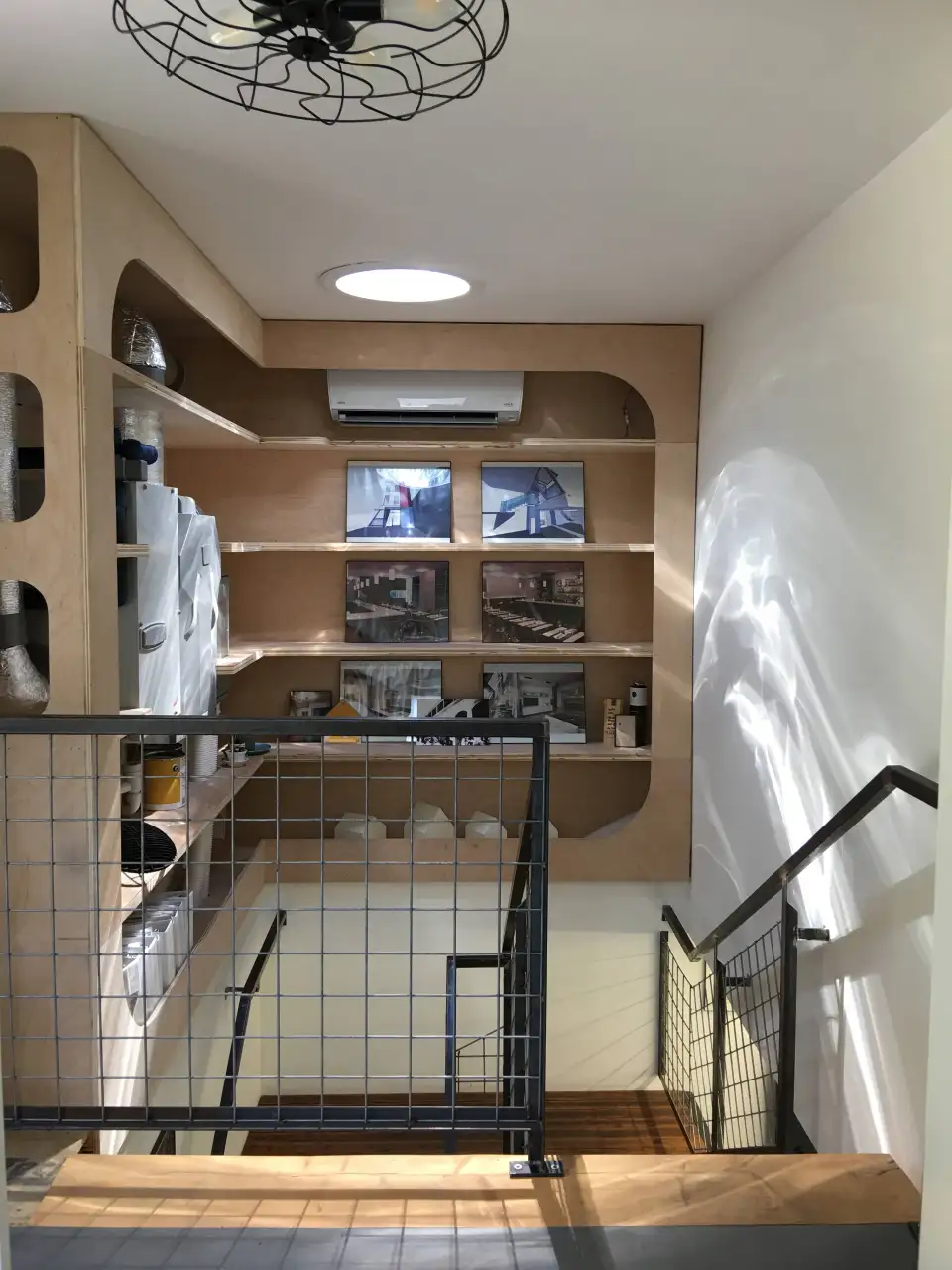
Luckily, enough on the board were convinced, and ultimately the two won approval to make the Passive House retrofits on the condition that they preserve or replicate the original stonework and replace the damaged wood siding with new planks that maintained the building’s original profile and general aesthetic. They were also given permission to extend the existing overhang of the roof, to set the windows deeper, and to convert the vents that had been used by the farrier into light wells to bring natural light into the high peaked ceiling. New tall windows on two sides would bring in light and views to the newly habitable basement.
Of course, once construction began, they realized that the project was not going to be as straightforward as they had anticipated. Erosion had eaten away at the mortar of the original foundation, reducing the stonework to loose rubble that had to be cleared away. This task required shifting the timber frame off the foundations entirely, rather than simply lifting it. Once the frame was parked in the rear yard of the property, an excavator cleared away the stone and expanded the basement to include a portion that previously was just a crawlspace. During the excavation many artifacts were found, such as wrought iron horseshoes, chunks of anthracite coal, animal bones, a copper mason’s pointing tool, and hundreds of abalone shell buttons from a nearby but long-gone button factory.
Not all of the discoveries were fun. Hiding beneath the site was a major problem: gas from a leak at the adjacent gas station had infiltrated into their property. “My excavator called me right away,” Hartford says, adding, “You could smell it a block away.” The discovery meant that hundreds of cubic feet of soil had to be removed. The removal of the contaminated soil (and the resulting finger-pointing) delayed construction by three months.
While these unexpected bumps in the figurative road proved vexing, resolving them made for a more stable and healthier result. Furthermore, had these issues not been discovered they could have gone unresolved until they demanded attention later. The all-new foundation gained them more space than originally planned. The original stone was salvaged to face the new foundation and was pointed with historically appropriate white mortar. And, while the original contamination was eliminated, the Passive House-standard robust air barrier and the upgrade of a subsoil ventilation system consistent with radon mitigation and the U.S. Department of the Navy protocols for soil gas mitigation (they make a lot of soil contaminated and know how to deal with it) ensures that toxic vapors from future spills will not pose health risks to the building inhabitants.
Once the timber frame was reset on its new foundation with thermal breaks and a vapor barrier in place, the transitions from foundation to wood framing were made, and things started looking up. Windows and doors were supplied by Yaro. The new, brightly painted, exposed-to-the-interior sheathing went up wrapped with a peel-and-stick air barrier (3M 3015), and the 14-inch Larsen trusses and Siga-supplied weather barriers were installed, replete with dense-packed cellulose. Hartford installed his own Zehnder ComfoAir 350 HRV plus preheat ComfoFond geo-heat exchange system, including the 300 feet of well pipe installed horizontally down in the soil under the basement slab and insulation. The building’s mechanicals were intentionally put on display in the stairwell and include a single 9,000-kBtu heat pump by Fujitsu, naturally lit by a Lightways solar tube.
Despite being a small building with only 1,097 square feet of useable space (around 1,500 square feet gross space) and a challenging retrofit, the team achieved a final average blower door test score of 0.20 ACH50 and were able to certify under PHIUS+2015 Source Zero. The CFM50 for the shell was 0.0138.
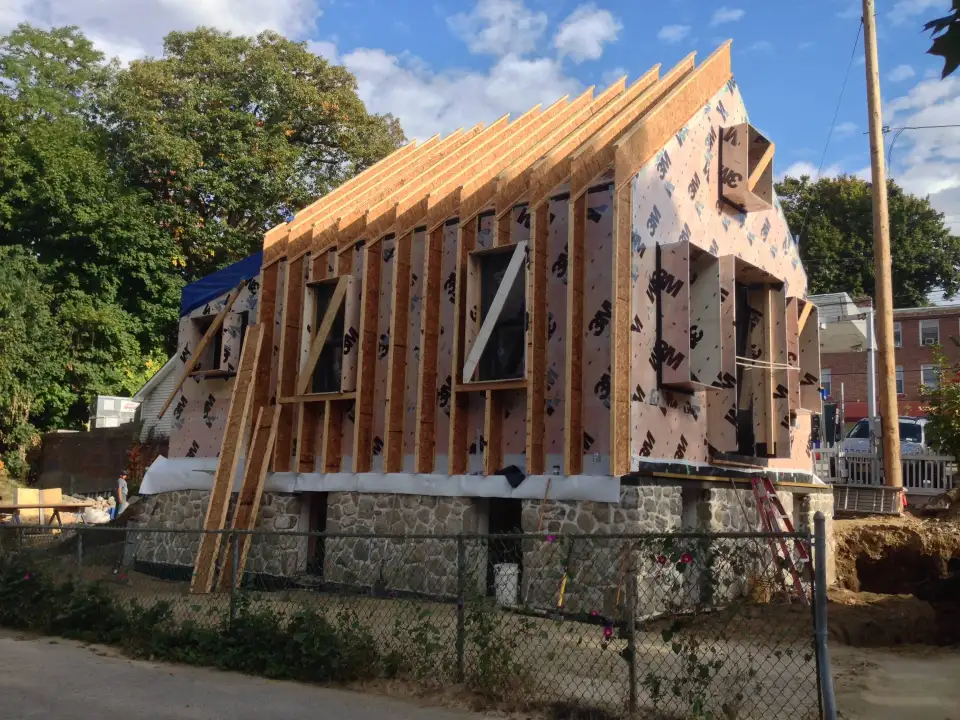
As one would expect, this kind of airtightness score means very little active heating measures are needed to keep the small space toasty even on the coldest of days. This was something that one worker discovered when he arrived on a bitterly cold day to install the Marmoleum flooring upstairs. It was before the heat pump had been installed, and he had given strict instructions about the need for “real heat” to give his materials time to acclimate to the temperature and was visibly incensed when Lee-Hartford gave him a tiny space heater at the start of the day. After all, he had said he needed real heat. According to Lee-Hartford, “By noon he had to unplug it and had to open the doors, saying, ‘I’ve never seen anything like this,’” Lee-Hartford recalls.
Heating energy |
4.5 kBtu/ft²/yr |
Cooling energy |
.4 kBtu/ft²/yr |
Total source energy |
11.9 kBtu/ft²/yr |
Airtightness |
0.02 CFM/ft² at 50 Pa |