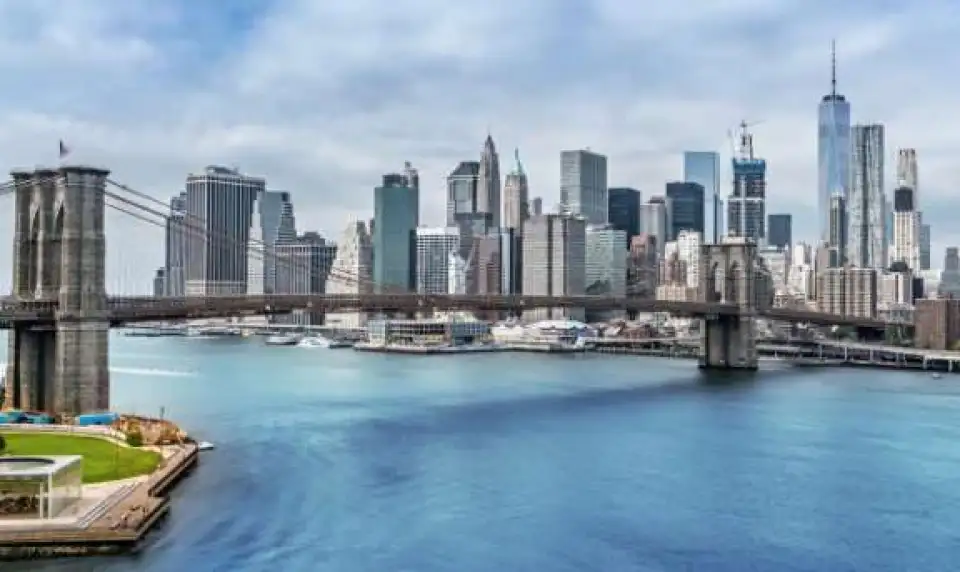
So you want to build a certified Passive House? Of course you do. Who wouldn’t want that?: healthy air, comfortable spaces, resilience against climate change and lower utility bills. What’s not to like? But the next steps after committing to pursue a certified Passive House can be hard to understand, even for practitioners who have been building sustainable homes for years. Below I’ll try and outline the main steps to follow on your road to a successful certified Passive House project.
First, it’s helpful to remember that the term ‘Passive House’ means a couple different things right now in North America. First, ‘Passive House’ is often used to describe an idea or set of techniques. As an idea, ‘Passive House’ has grown rapidly over the past decades as builders, designers and homeowners have sought to design healthier spaces while reducing energy consumption.
But in addition to being an idea and set of methods for creating better buildings, ‘Passive House’ is also a specific green building certification, similar to LEED, EnergyStar and many other programs that seek to help practitioners design and construct better buildings. As a certification, the Passive House method has gained adherents around the globe but is still a relatively small part of the North American construction sector — though growing quickly. In this article I’ll be mostly talking about the latter notion of Passive House: how do you actually take your building all the way to true certification level, what are the steps along the way and the professionals that are involved, and what are the most common hiccups that might derail your certification process as you proceed from design to construction to finished building?
The Road to a Certified Passive House
Step 1: Find your Certified Passive House Designer or Consultant
The first steps to a successful certified Passive House project are largely the same whether you are working on a single family home, a multifamily high rise, a grocery-store, a warehouse or anything in between. The first and most important step is to find a good Certified Passive House Designer or Consultant and fold them into your process as early in the design sequence as possible. These highly trained and knowledgable practitioners have a huge amount of knowledge about the physics of building performance, the particulars of project certification, best practice for your building type or region as well as access to the tools of the trade such as the energy modeling softwares used for certification verification. You will want to rely on this team member early and often to gain an understanding of how your building is performing and whether you are on target for certification.
Important to keep in mind, however, is that just like architects and builders — most Certified Passive House Designers or Consultants will be specialized in one or another building type, region, climate, construction type, or other subset. It’s good practice to ask for proposals from a couple different teams as you decide who to work with and try to find one which will be a good fit for your particular project needs. When thinking about bringing a Passive House professional into your design process, keep in mind a couple of things:
Is the Certified Passive House Designer/Consultant experienced in your project’s type of construction and region?
How local is the Certified Passive House Designer/Consultant? Will they be able to visit your site regularly? Do you need/want them to or will you be relying on a third-party verifier or rater for site inspections?
How well does the Certified Passive House Designer/Consultant interface with the rest of the team? Do they spend time and care on delivering clear communication documents, drawings, instructions to the team? Will they work well with the contractor and design team?
In our experience, this last point is the most critical. You are going to be folding a new professional into the design and construction process and they must be able to work effectively with the rest of your team. Your Certified Passive House Designer or Consultant should be able to communicate their ideas through drawings and diagrams, review project submittals and documents carefully, be able to interact meaningfully with the on-site construction team, and provide consistent notes and follow up throughout construction—all in addition to being able to craft a careful and accurate energy modeling of the proposed building.
A brief note a Certifications and Qualifications.…
There are two bodies in North American which currently certify Passive House buildings as well as provide training and administer qualifications for professionals — the Passive House Institute (PHI) and the Passive House Institute US (PHIUS). These groups have different standards, targets, software and trainings and issue their own distinct certifications. In the US, PHI certifies professionals as ‘Designers’, though in Canada and Internationally they also have a ‘Consultant’ designation. In the US and Canada, PHIUS certifies Certified Passive House ‘Consultants’ with the acronym ‘CPHC’. In addition to these design-side qualifications, both groups have an expanded set of qualifications available for tradespeople, raters and verifiers who may also be involved in the project depending on the scale or type of building.
Ultimately, it’s up to the owner which of these certifications to pursue and it’s highly recommended to rely on your Certified Passive House Designer or Consultant to help you make that decision. You may also want to discuss it with the other team members (designer, builder) as many of them will have pervious experience in, or a preference for, one or the other certification systems and processes. Both certifications will ultimately yield a very good building though, and owners should rely heavily on the team members to help them make this decision.
What if you want to be your own Passive House Designer? It’s important to point out that it’s not required to hire a third party to do the Passive House modeling and certification — if you are a designer or builder who has gone through the Passive House training and you are comfortable working in the energy model (more on that below) as well as the overall certification process, then there is no need to hire another professional to get involved. That said, it is highly recommended to work closely with an experienced practitioner if it’s your first time, or if the building has levels of complexity beyond what you are normally used to seeing.
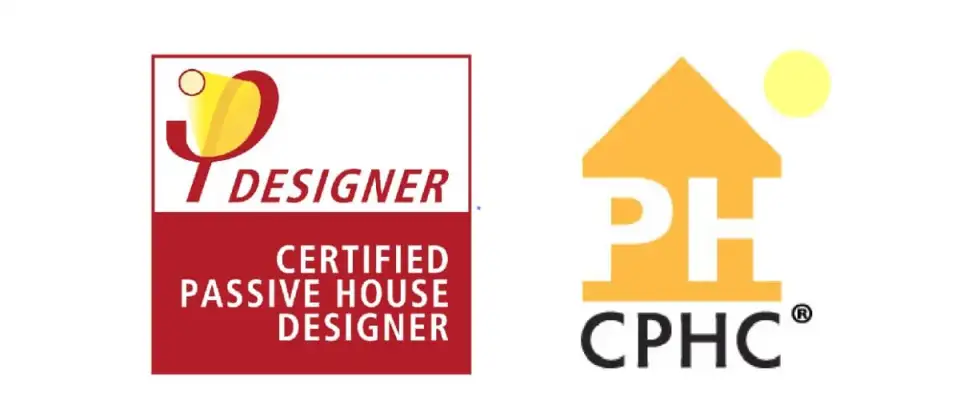
Step 2: Decide on your Certification Goal
This may seem obvious. You want a Certified Passive House—what more is there to know? Well, experienced practitioners will understand that there are in fact a variety of ways to certify any specific project. All of the various methods will result in great buildings, but there have been a variety of pathways which have evolved over the years to allow many different types of projects to reach certification. The PHI certifications include various options for new-construction, retrofits, ‘low-energy-buildings’, buildings with and without onsite renewable energy, as well as specialist ‘prescriptive’ pathways for sensitive historic retrofits. PHIUS includes a range of certification ‘badges’ as well, including options for certifying a ‘supply air heating’ home or ‘Source Zero’ levels in addition to their core certification pathway.
The important thing here is to rely on your Certified Passive House Designer or Consultant to help you decide on the best pathway for certification given your specific building type, climate, project timeline, and other considerations. Some pathways are going to be really, really aggressive and guide you to incredibly high levels of energy-efficiency with lots of onsite renewables, while other pathways are more flexible and allow challenging building types such as retrofits to still achieve certification even if they necessarily have to make some small compromises here or there. But no matter what pathway you choose you’ll still have to meet the same rigorous thermal comfort, durability, sound, health and resilience targets, ensuring that no matter how you certify you are still going to enjoy all the benefits of a certified Passive House building.
Step 3: Use the Energy Model to Inform the Design
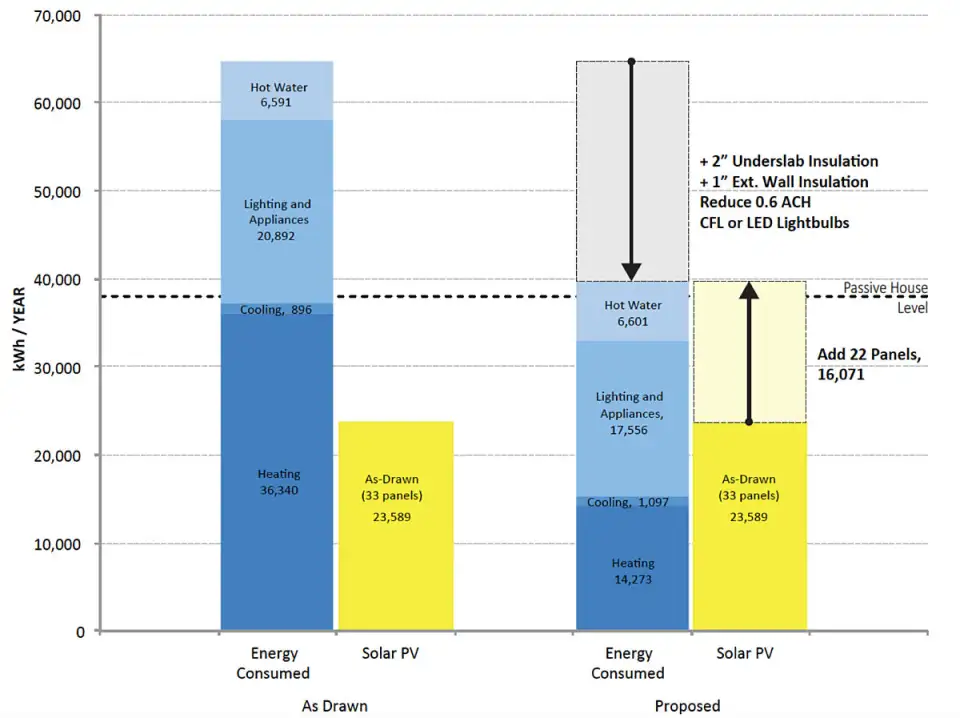
Now that you have your team members in place and you have committed to your certification goal, it’s time to get moving on the design. What that means in a data driven process such as Passive House is that you’ll use the building Energy Model (a detailed digital simulation of the building’s performance) early and often to help shape the design decisions of the building. Massing, glazing, shading, construction types, ventilation and other critical aspects of your building are all influenced and informed by the results from the Energy Model. This isn’t to say the model controls the design, but rather that the model should influence and inform the design decisions.
This whole-building energy model will be created by your Certified Passive House Designer or Consultant and will seek to give the design team a window into the invisible flows at work within the proposed building. Things like heat, air, moisture, noise, light and other invisible but critical forces powerfully shape the way we experience and understand space, and the new generation of digital simulation models are finally giving designers a view into these processes and allowing us to shape and control them in ways never before available.
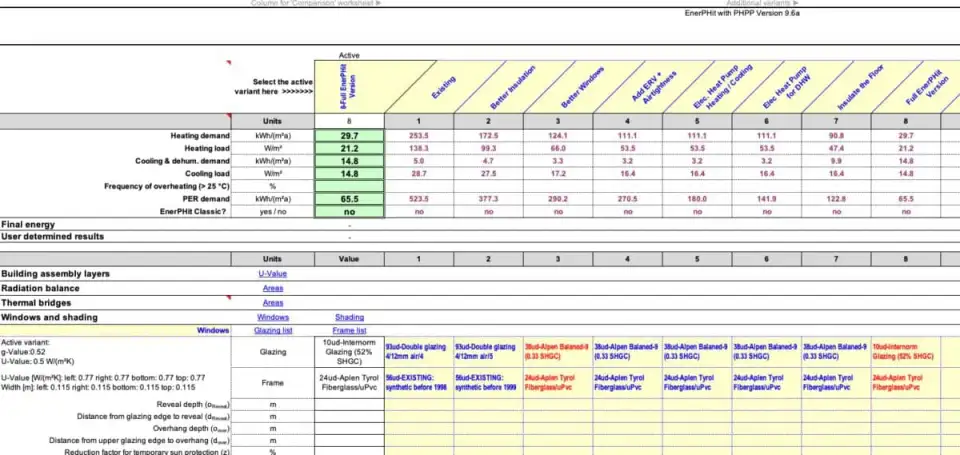
As with all your design drawings, this model should start ‘light’ and schematic. It should allow you to test a range of inputs and evaluate sets of outputs quickly as you zero in on the successfully design. As decisions get set, more detail is added to the model fleshing out a more nuanced picture of the building’s performance. As the design moves from early to late phases and construction detailing more data about specific products, construction details, materials and assemblies all gets folded into the model. Your Certified Passive House Designer or Consultant should be in constant dialogue with your design and construction teams throughout the detailing phase. Critical simulations for evaluating thermal and moisture performance should be executed based on the proposed materials and assemblies and useful alternates evaluated at this point as well. Thermal bridging Psi-Values, surface temperature checks and moisture durability profiles are evaluated for each proposed assembly and detail on the project to ensure that the building achieves the highest levels of comfort and health.
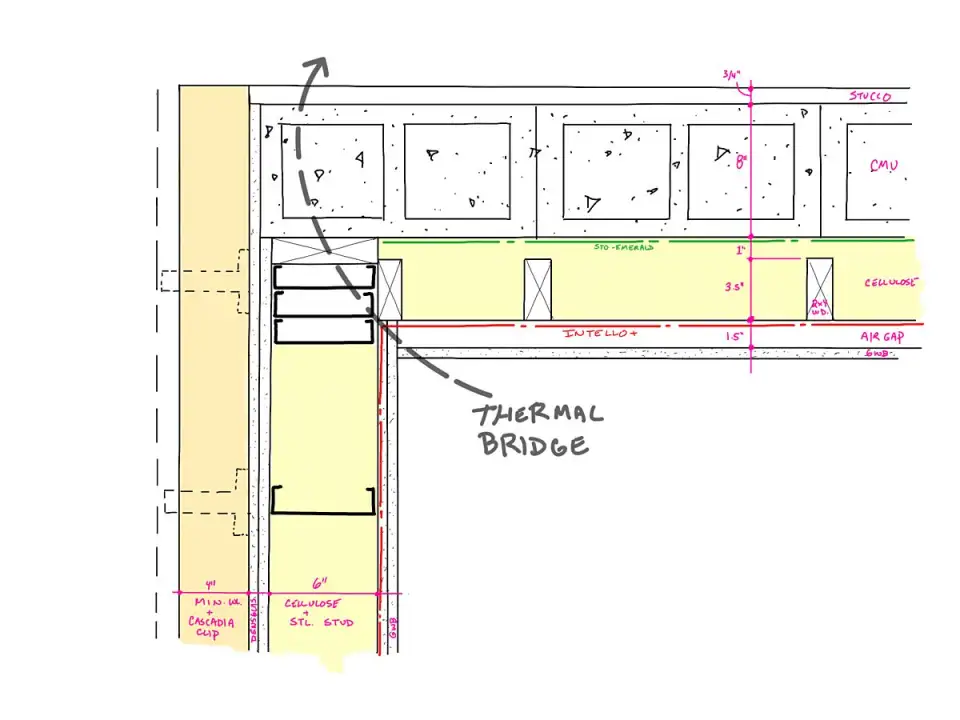
Step 4: Updates to the Model(s)
Even the most thoroughly detailed and complete planning documents and models will need to change when they meet the realities of the construction site. The inevitable changes to the building due to site conditions, schedule, budget or owner revisions will mean that throughout the construction sequence your Certified Passive House Designer or Consultant will need to be keep abreast of these changes and all substantive modifications folded into the whole building energy model. It is this model (or models) which your Designer or Consultant is using to communicate the project with the final Certification reviewers, and therefore it’s critical that changes to the model are executed in a timely fashion and continually reviewed for compliance. No one wants to engineer a successful Passive House just have a surprise product substitution derail the certification at the last moment.
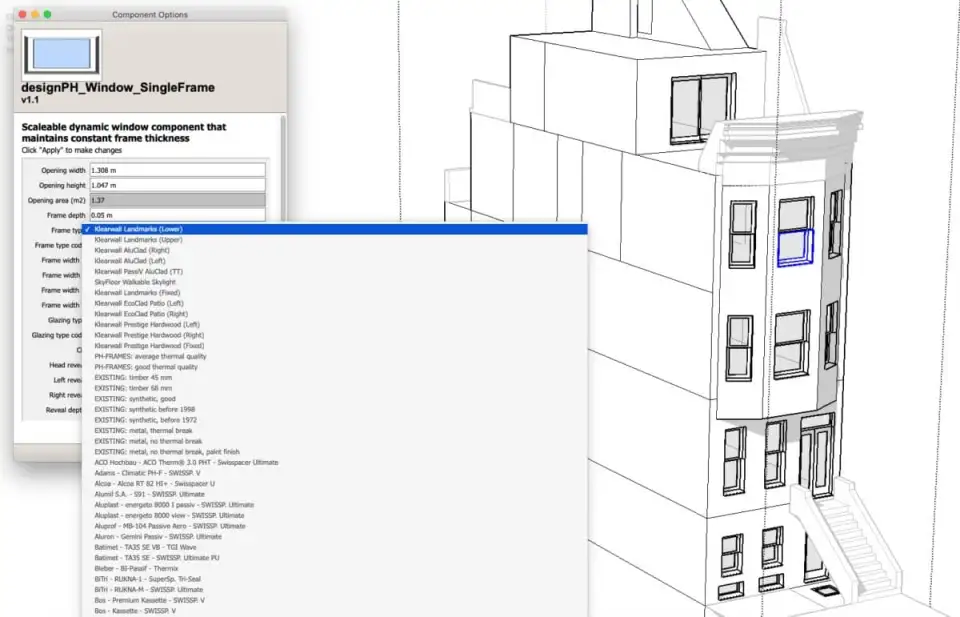
Step 5: Final submission
Once the design and modeling is complete, the products are specified, and the construction of the building is finished, there are only a few additional steps needed to complete your certification. The main item which must be done at the tail end of construction is the ‘Blower Door’ airtightness test. This test is used for the Passive House certifier to verify the quality level of the on-site airtightness. The test is relatively straightforward for most projects, and involves using a fan to alternately pressurize and depressurize the building. As this fan pressurization/depressurization is occurring, sensors are used to determine the amount of air leakage through the envelope. The final test should be carried out once all the airtightness elements are in place and the main construction activities are complete.
And at that point, if you have a good result on your blower-door, you’re all set. You’ll need to update and finalize any missing documents or spec’s for the Certifier, but once this is complete you will be issued the final certification documents or plaques for your project.
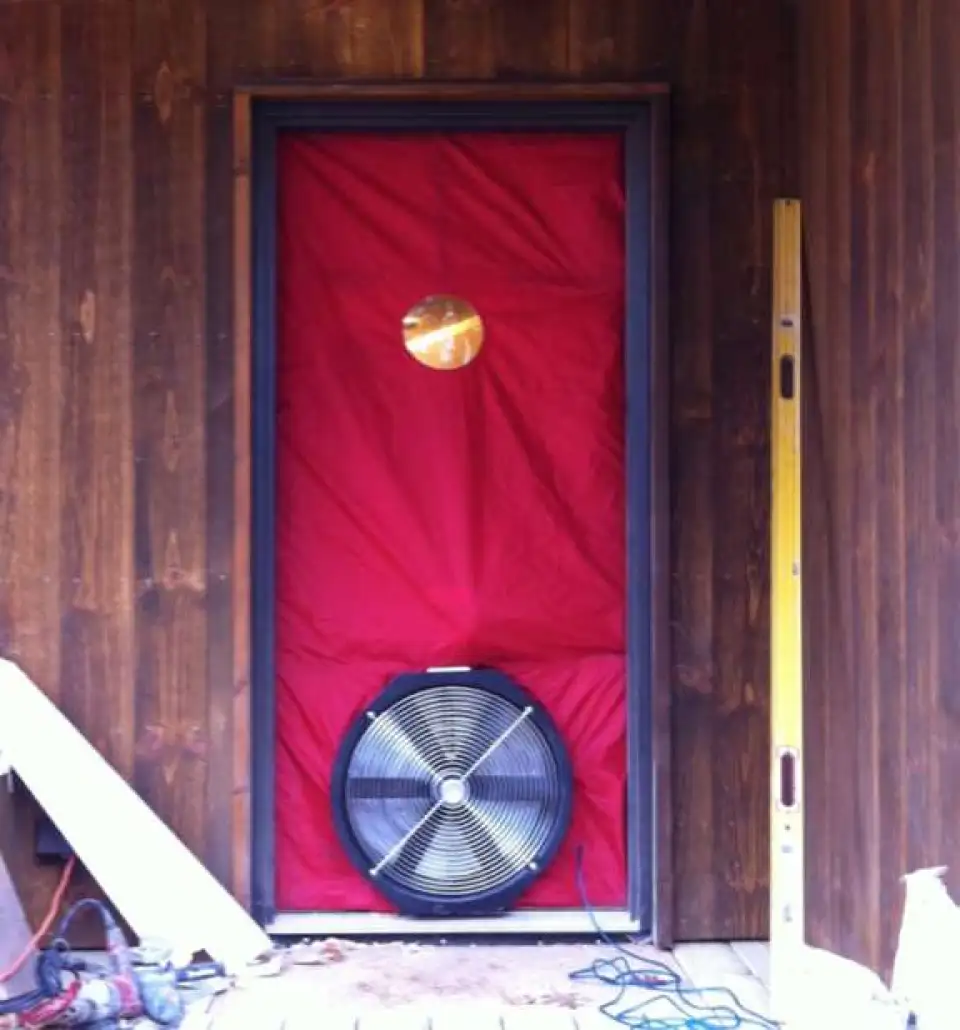