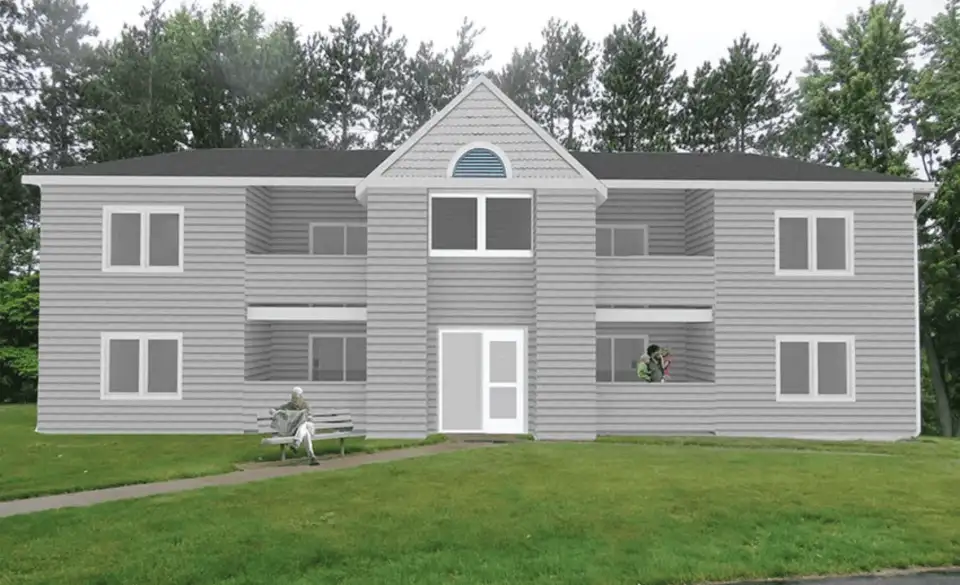
Not all retrofits can be accomplished in one go, as the PHI recognized when it created a certification for phased retrofits, or EnerPHit projects. Deep energy retrofits of existing structures are an absolute must for meeting any reasonable carbon emission reduction goals, but cost-effective retrofits are challenging, to say the least. As reported in previous Passive House Buildings issues (“Scalable, Efficient Retrofit Solutions Under Development,” Fall 2018, p. 20), NYSERDA is pursuing industrialized approaches to retrofits, building on the Energiesprong program first developed in the Netherlands, and actively working toward market viability of deep energy retrofit solutions.
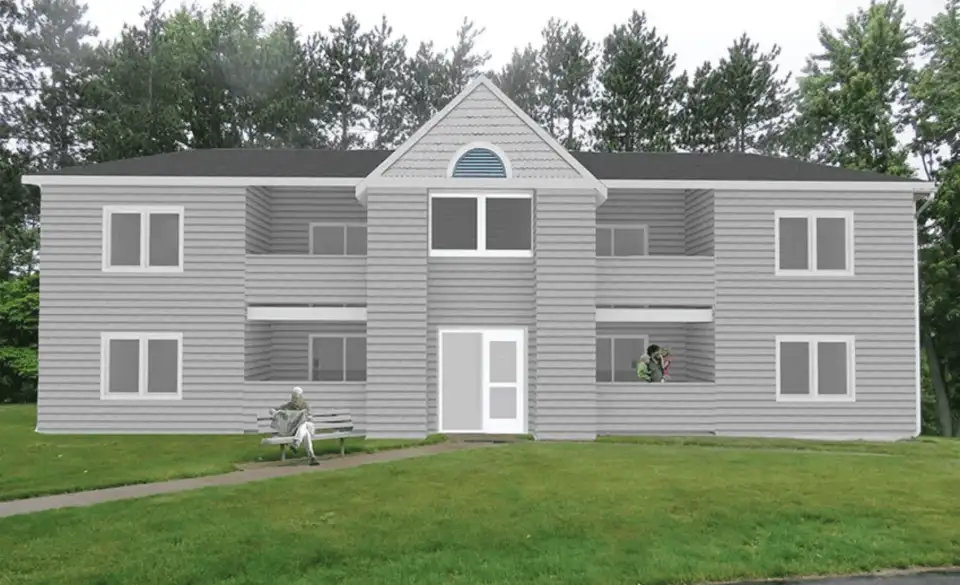
Tom King, of King + King Architects, is leading one such project, spurred on by his feeling that “it is our responsibility as designers, builders, financiers, and owners to step up and challenge ‘Business as usual.’” His scope of work stands out from others in this NYSERDA initiative for a positive reason: The owner of the five-building, 40-unit, two-story, wood-framed apartment complex in upstate New York has been keeping up with needed maintenance and has even undertaken home performance improvements and weatherization measures. Replacing the building’s entire façade, as is often done in an Energiesprong project, wouldn’t make financial sense up front. Instead, bringing the building to a net zero energy and Passive House level of performance is requiring a long-term phased plan of retrofit measures, some of which are cost-effective now, while others will be cost-effective over the next 30 years of capital improvements.
The all-electric complex currently has an annual site energy use intensity (EUI) of 39.4 kBtu per square foot (/ft2)and peak heating and cooling loads of 10.7 kBtu/ft2 and 9.8 kBtu/ft2 respectively. The proposed retrofits are designed to reduce the heating and cooling loads by almost half.
To realize this energy reduction strategy, the planned scope of work includes the development of a mechanical pod housing integrated mechanical systems that can be manufactured off-site, akin to those used in the Dutch Energiesprong projects. Advancements and cost compression in integrated domestic hot water (DHW), heating, cooling, and ventilation systems—similar to the Factory Zero equipment available in the Netherlands—have great potential benefit for deep energy retrofit projects here. Analyses of Dutch projects reveal a 37% cost reduction in façade systems and a 73% cost reduction in mechanical system integrations since 2010.
The planned mechanical pod that King + King, along with Taitem Engineering, a project partner, are developing will include an ERV unit, a DHW tank and outdoor unit, a solar PV inverter, an electric service panel, and a new master meter—all of which will be factory installed and delivered on-site. Each of the five buildings will be served by one system attached to the existing exterior, maximizing tenant storage space within units. Ducts and piping will run through an insulated and air- sealed plenum in the attic, serving units vertically through closets that previously housed electric-resistance DHW tanks. This technique will reduce in-unit construction and tenant disturbances during the retrofit.
The ERVs will be fitted with hot water coils integrated with the DHW system to provide additional and emergency heating as necessary, as well as particulate air filters to remove contaminants prior to supplying air to the apartments. A heat pump water heater using CO2 refrigerant will supply the DHW with an aquastat to control recirculation, maintaining proper loop temperature while optimizing pump operation. The electric service will include provisions for the DHW system and ERV to be run on emergency power in the event of grid failure, initially provided by temporary generators but with the ability to add battery backup systems in the future.
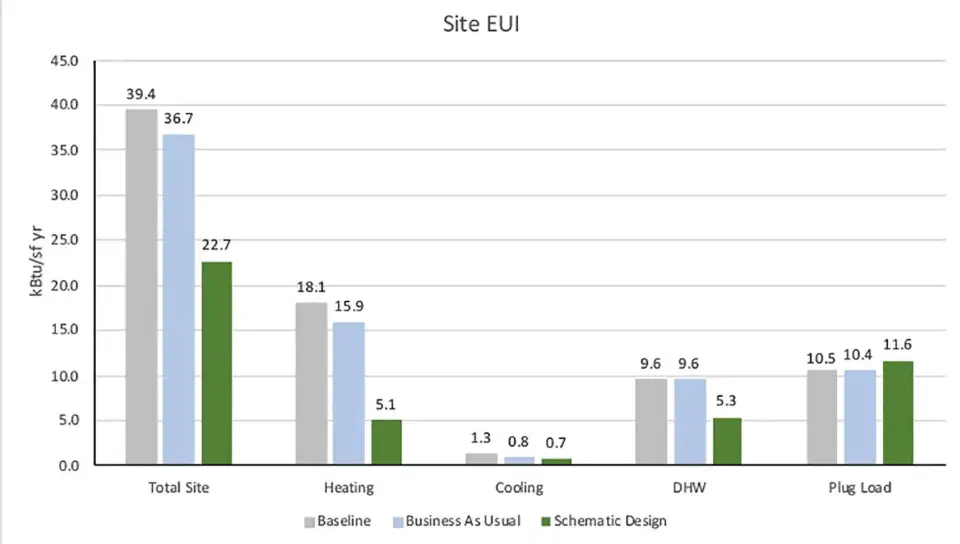
For the first time, the tenants will be supplied with air-conditioning in all rooms using the smallest-capacity air source heat pumps available fitted with variable-speed compressors to manage the loads. This new equipment will help reduce the humidity of the apartments and prevent mold and mildew, while substantially improving indoor air quality.
Of course, the smaller integrated mechanical systems would not be capable of meeting the conditioning loads were it not for the proposed façade improvements.
Blower door tests performed by Taitem Engineering showed the existing building to be at 4.47 ACH50—definite room for improvement. The team identified areas ripe for air sealing: around electrical boxes, pipe and duct penetrations, and drywall at the sill plate. Any existing window unit air-conditioning sleeves will be removed, insulated, and sealed. Additional reduction in total building air leakage is anticipated from replacing all windows and doors with operable, high-performance triple-glazed units. The team is aiming with these measures to achieve an airtightness of less than 2 ACH50.
Additional façade improvements include enclosing each existing exterior entrance and stair to significantly reduce exterior wall surface area and heat loss from each of the apartment entry doors. The new walls will be insulated with 5.5 inches of mineral wool insulation and R-9.6 continuous exterior sheathing, as will the currently uninsulated walls of the maintenance garage, which abuts one of the buildings.
As designed, the retrofitted building should achieve an annual site EUI of 22.7 kBtu/ft2 with 89% of its power supplied annually through on-site PV generation. The next major capital improvement cycle, planned sometime before 2050, would include a full envelope upgrade, allowing the complex to further comply with current New York State and global emissions targets, and likely pushing the buildings to net positive power generation, with the ability to act as a resource for adjacent low-income housing properties.
The biggest challenge thus far, says King, has been trying to identify the most cost-effective solutions while still meeting the initiative’s EUI requirements. The team is looking for ways to further reduce costs through systems integration and shop-fabricated components, but is not expecting to arrive at a feasible solution without programmatic support—as was the case for early Dutch Energiesprong projects.
King has been much inspired by his participation in this initiative, particularly by the immediate immersion into an intensely focused group exchanging ideas freely between teams, rather than in competition. The goal that is driving his participation in this pilot project is pushing to develop, and most importantly implement, solutions that further align the market for full saturation. European models are showing positive results; continued cost compression through technology innovation and demand aggregation is the path toward feasible deep energy retrofits across North America.