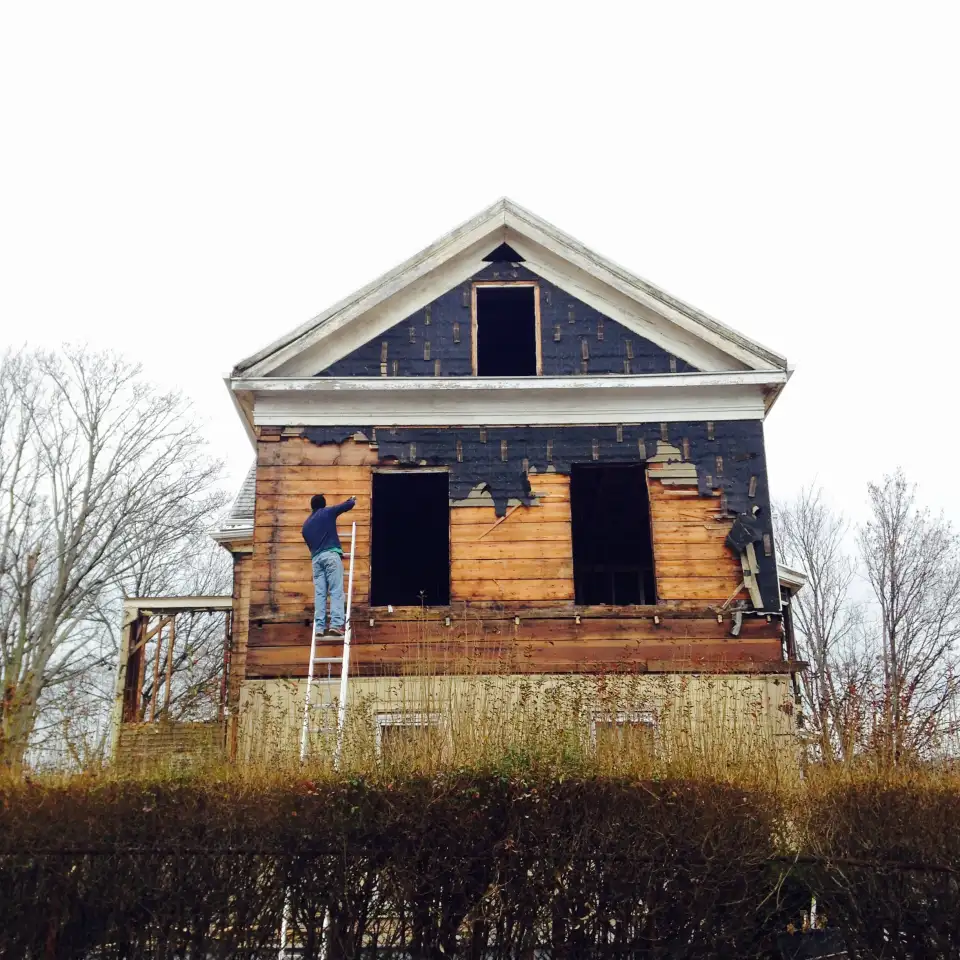
As Paul Hawken describes in his 2007 bestseller, Blessed Unrest, there is overwhelming evidence that we are living through a self-imposed, and accelerating, mass extinction. Fortunately, according to Hawken, we are also witnessing an unprecedented explosion of life preservation-oriented companies and non-governmental organizations, or NGOs, around the world—a global auto-immune response to this crisis.
Last summer I teamed up with one of these mission-oriented companies, Boston-based Placetailor, to tackle the thorny question of retrofits. “The AEC industry, which has been in crisis for decades and unable to innovate at the pace of other market sectors, now has a critical mass of professionals dedicated to driving its rapid evolution,” says Colin Booth, Placetailor’s managing director. He remarks that the Millennial generation, who have spent their lives watching ecological disasters, and much of their careers frustrated by the inability of the typical models to rise to the occasion, are now highly accomplished, influential, and motivated activist-professionals. The greatest roadblock to more sustainable work remains industry inertia. Established companies that follow institutionalized business models and delivery processes may find it extremely difficult to pivot into roles of real climate-focused leadership. Conversely, companies founded upon an explicit mission, led by activist-professionals, are better equipped to provide effective models for delivering a better world.
Model Follows Mission
Placetailor is a development, design, build, and R&D cooperative, founded in 2008 with the sole purpose of proving the viability of Passive House-level housing. It was the dedication to that mission that drove the evolution of the business model, which in turn spawned a true vertically integrated project delivery process. Without the ability to control critical decisions up and down the delivery chain, it would have been impossible to remain committed to the cooperative’s mission. Its nimble size and proactive leadership rendered the company flexible enough to test technologies, learn how to balance developer and builder perspectives, recruit talent, and educate clients. Today, Placetailor can claim that every project since its inception has exceeded the AIA 2030 Challenge carbon reduction targets—a testament to the power of its mission-driven model.
The primary focus of Placetailor’s work has been new construction. Still, the team has also undertaken a steady string of interesting deep energy retrofits (DERs)—including a Passive House-certified Back Bay brownstone retrofit, a series of triple deckers, and a community center—that have informed the company’s understanding of the relevant technical and financial issues necessary for the rapid decarbonization of the existing housing stock.
What is a Deep Energy Retrofit?
A DER is a renovation that reduces energy consumption by more than 50% before considering onsite renewables. While founded on Passive House principles, Placetailor recognizes that a DER often targets incremental performance gains. Travis Anderson, the company’s CPHC and director of innovative design, has built an informed set of opinions based on his DER experience. “Envelope renovation should be the priority, particularly when considering older buildings,” Anderson states. “As technology continues to improve, all-electric conversions will become easier, and DER-aligned equipment can be installed over time. But heat pumps, PV arrays, and low-consumption appliances become inefficient without a tight envelope.”
That existing buildings contribute significantly to the world’s carbon problem is well known, but the demand for DERs remains low. According to a recent Lawrence Berkeley National Laboratory study, this lack of market share is attributable to a perceived high “hassle factor” and cost premiums. The researchers point out that the number one reason a client seeks a DER is not to save the world. Residential clients seek improved thermal comfort. Conversely, the primary reason they abandon renovation targets like Passive House is the perceived added inconvenience.
Anderson points out that any renovation is a hassle. Once people think in terms of carbon (operational and embodied), he asserts, they recognize the value in upgrading their building’s performance. He believes a greater barrier for DERs is the relatively low price of fossil fuels, specifically natural gas. Also, convincing people to spend money on things they can’t see like air sealing and insulation is challenging. So, how do you solve a problem like a DER?
Triple Decker Challenge: Problems, Solution, and the Business Case
Last summer Placetailor and WestFaulkner decided to collaborate on a DER solution, inspired by MassCEC’s triple decker retrofit competition (see MassCEC’s Triple Decker Design Challenge, p. 40). A replicable, scalable, and affordable solution for renovating our existing housing stock must be found for the state to meet its 2050 net zero emissions goals. Over 60% of the State’s building emissions come from older buildings, with their inefficient heating systems, archaic wiring, and out-of-date plumbing. Triple decker remodels tend to be labor-intensive and messy; and while there is opportunity to capture significant energy efficiency savings through the retrofit of aging multifamily buildings, there is no cost-effective, climate-friendly, or safe roadmap. Furthermore, building owners have little motivation to upgrade the performance of their drafty triple deckers without reasonable terms of payback for the investment. Oil and gas are relatively cheap, and much of our older housing stock is rental with utility bills paid by tenants.
In addressing the MassCEC challenge, we chose to take a district approach, focusing on Boston’s Fort Hill neighborhood, with its concentration of triple deckers and diverse demographics. While no two are identical, a typical triple decker was identified for conversion to all electric systems. Each apartment gained an ERV and mini-split heat pump, replacing the gas-fired boilers, and was upgraded to a solar hot water heater, thus reducing energy demand by 100%. All cavities were insulated with cellulose. A magnesium board retrofit panel was applied directly over existing siding, except for the historic front, which was treated with Aeroseal and not reclad.
However, despite tax incentives and sizable reductions in utility bills, our team could not make a credible business case for the renovation. Construction costs remain high, and city zoning restrictions inevitably protract the schedule, burdening an owner with cost escalation. Only when a fourth floor was added with a roof geometry optimized for solar arrays did the economics change in favor of the investment, increasing rental income, real estate value, and creating significant behind-the-meter energy production. Seventy-nine photovoltaic panels located on each roofscape easily pushed the site energy use to net positive. In organizing groups of 25 retrofitted neighborhood buildings into solar districts, there would be a combined output of 706,275 kWh/year, with the net excess available to a third-party purchaser (such as the City of Boston). The aggregate of energy sold, utility expenses saved, and added rental income presented a rational business model for the DER.
PT Technologies
The Triple Decker Challenge provided an ideal runway for launching PT Technologies, a new division serving as a formal vehicle for Placetailor’s long-standing research and development activities. During the competition, the team considered a spectrum of prefabricated systems for improving energy use: a magic box for full electric conversion, modular kitchen and bathroom pods, solar water heaters, and insulated mega-panels inclusive of high-performance windows. Post competition, our team returned to Passive House principles to prioritize development efforts. A carbon calculation was re-run with only the exterior panel—leaving the building systems intact—and we determined that the best use of renovation resources would be a thermally efficient building envelope. Working backward from the scale of the mission, it was clear that no existing products met all of the performance, footprint, and cost requirements. Thus, PT Panel was born—designed as a critical component of a complete solution.
Currently available options for retrofit panels are few, and what exists is generally petroleum-based. Whether considering insulated vinyl siding, nail-built insulated panels, or EIFS, a consumer is looking at various sandwich combinations that have been engineered for high R-value and low weight, easily achieved with high-density chemical foams. There are few readily available bio-based options. Panels of straw, mycelium, and hemp are in their infancy. Nonetheless, off-site production of prefabricated structural panels has been expanding (see Passive Goes Prefab 2021), hinting at the tremendous opportunity in the retrofit market. Several start-ups are tackling this colossal problem with funding, both public and private.
PT Technologies, led by myself and Evan Smith, president of Placetailor, is prototyping PT Panel, a viable alternative to a petrochemical-intensive retrofit wall panel. Its wood-fiber substrate has inherently high insulating value and carbon sequestration; it is OSHA-friendly to install and effectively carbon neutral. Fabricated off-site, the panels are controlled for quality and produce little material waste.
Brad Prestbo, Placetailor’s director of operations, points out that a customizable “drop-and-lock” panel solves a number of problems when retrofitting an idiosyncratic triple decker. “Complicated field issues and a multi-layered trade approach make it difficult to upgrade these buildings at any meaningful scale,” he says. Design for fabrication has long been promised in architecture, but rarely achieved. Prestbo notes that a process that starts with a digital scan and ends with a simple installation is the definition of mass customization. This has been the core focus of our R&D effort: to remove as much extraneous or overly complicated labor, equipment, and layers as possible to create a customized component language. PT Panel’s scan-to-skin program has moved beyond schematic design with both digital and physical models being evaluated by outside consultants for structural feasibility as well as thermal and moisture properties.
While there are no national data on the triple decker typology, we know that in the United States there are 10.8 million small multifamily buildings (2–4 units), with the highest concentration being the wood-framed structures of the Northeast. PT Technology is motivated by the economic development potential of providing a widely adoptable market solution. More urgently, however, we are driven by the potential to greatly reduce GHG output from the building sector. PT Tech expects to license the product to other manufacturers as part of the long-term business strategy. As always, mission first, and let the business model follow suit. Due to the scale of mobilization necessary to retrofit so many buildings in such a relatively short time, the problem is far too large for only one maker or one builder. It’s all hands on deck.