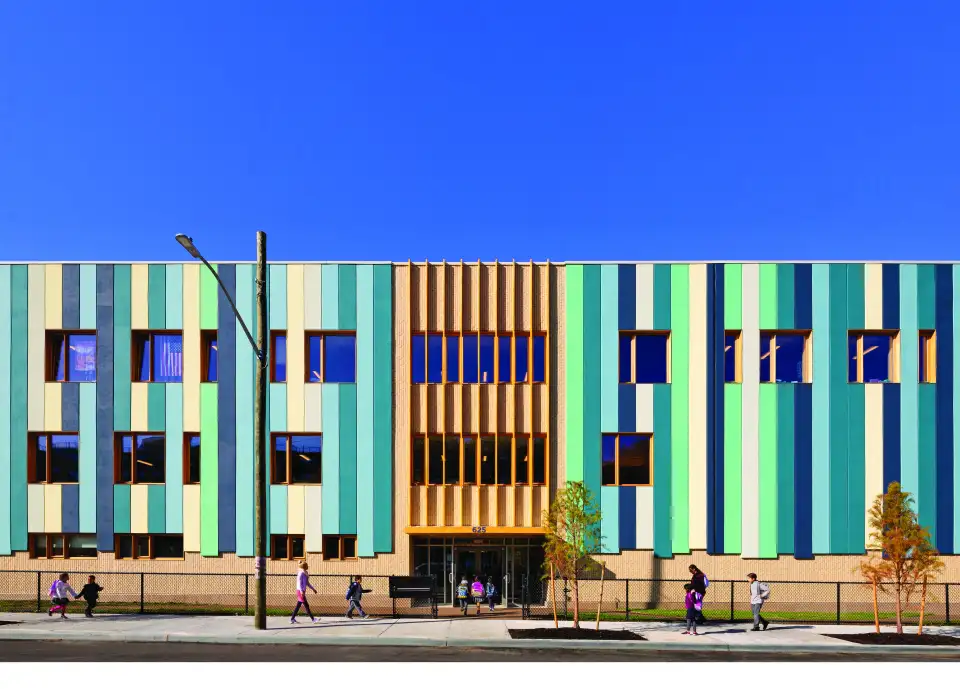
Maybe it is a high-rise, high-profile commercial structure that serves as the headquarters for a multinational corporation with the company’s logo proudly attached to the top floor. Perhaps it is a massive warehouse that will serve as a critical distribution link for an e-commerce giant. No matter the end result, the design vision for any new building begins in the minds of its owner and the architect on the project.
What will it look like? Will it take its cues from the surrounding architecture and perhaps harken back to past influences, or will it make a bold, new statement that looks to the future? What materials will help the building take shape and deliver the aesthetic impact being sought?
At the same time, how will the building protect its occupants and make them safe, comfortable, and secure? And how will it protect the environment in terms of materials used, long-term energy use, and the overall durability and resilience of the façade system?
From the moment an architect’s pen hits the sketch pad, a complex back-and-forth begins to develop, one that must grapple with equal and sometimes competing mandates—performance versus aesthetics, pragmatism versus artistry. Once the decisionmakers settle on a look, they then need to make key decisions on the different components of the wall assembly based on the desired performance of the building.
One approach is to look at each one of these requirements independently and, in turn, find a separate product to deliver on each front.
Alternatively, what happens when a designer specifies an integrated building enclosure system developed by a single manufacturer that effectively delivers a singular solution for all the requirements? It removes much of the complexity from the equation, and it can streamline the process for contractors and installers who will take what’s on paper and build it. For those pursuing Passive House certification, an integrated building enclosure system also ensures continuous insulation and prevents thermal bridging. With the right choice, the designer—and the building owner—can up the ante when it comes not just to building performance, but also to visual stopping power and the overall curb appeal of the building.
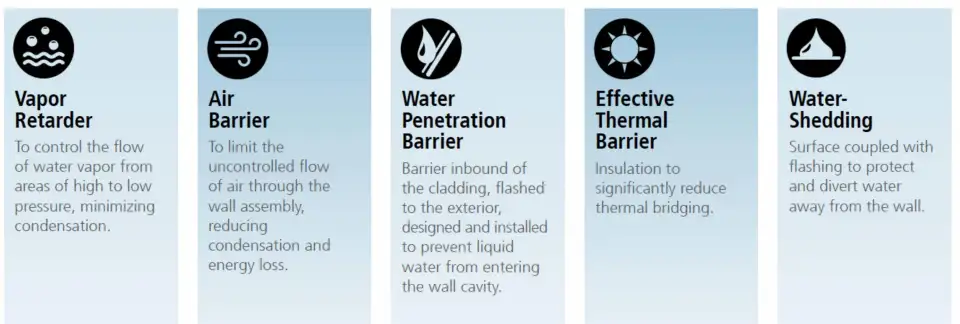
Designing for Durability: The Control of Layers
A building’s façade is constantly bombarded by the ever-present and unrelenting forces of Mother Nature—rain, wind, snow, UV rays, temperatures changes, and more.
The building enclosure’s durability is dependent on having effective components in place, which is why it is necessary to go well beyond the exterior wall and analyze the control layers. They interact to both protect the building from the exterior elements and create a comfortable interior for its occupants. They include:
· A vapor retarder to minimize condensation by controlling the flow of water vapor as it shifts from high- to low-pressure areas.
· An air barrier that reduces energy and condensation loss by limiting the uncontrolled flow of air through the wall assembly.
· A water penetration barrier that prevents water from entering the wall cavity and is flashed to the cladding’s exterior.
· A thermal barrier to mitigate energy loss and prevent thermal bridging.
· A durable and water-shedding façade to protect against environmental elements, impacts, UV exposure, pollutants, and more.
Passive House building enclosure systems must contain all these control layer components in an integrated, tested system. As a single solution, the individual layers work in concert with one another to deliver a holistic approach.
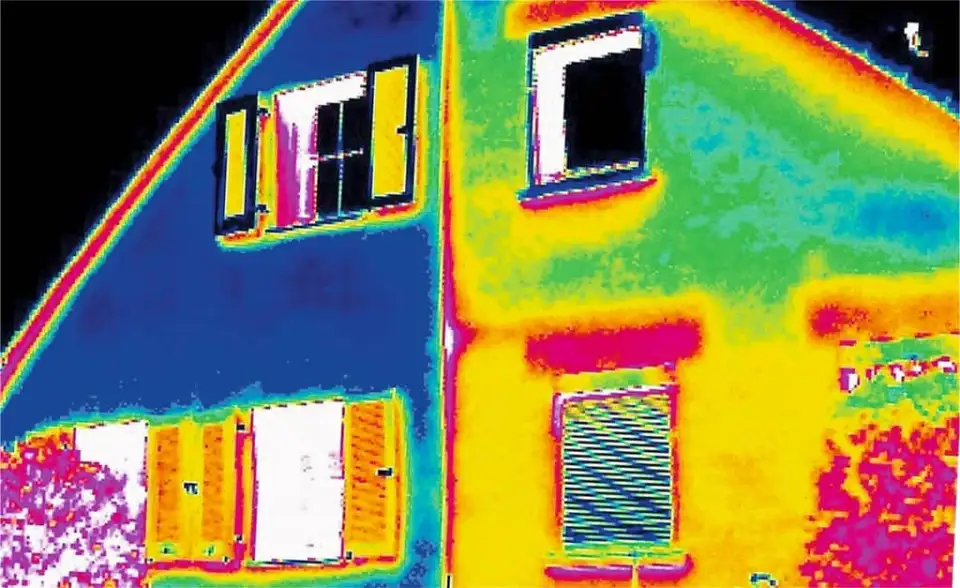
Creating Continuity: The Air and Moisture Barrier
Properly designed air and moisture barriers control the leakage of air and moisture into and out of the building envelope. Put another way, the air and moisture control layers create a line of demarcation between conditioned air (on the interior) and unconditioned air (outside the building). One of the key benefits of Passive House construction is that it creates superior indoor air quality by ensuring that leaks are kept to an absolute minimum through close attention to air and vapor sealing, and that mechanical ventilation systems provide a continuous supply of fresh, filtered air.
To create a tight seal and promote energy efficiency and management of moisture, continuity is key. Any breaks in the air and moisture barriers can promote unwanted air flow, a compromise in comfort for the people occupying the building, potential damage to materials from unwanted moisture build-up, and decreased energy efficiency.
For instance, water escaping bricks or icicles on the building’s wall indicates air leakage, which is just one form of enclosure failure. Condensation is developing around the warm, interior air that is escaping. Aside from the huge waste of energy, this erodes the material over time, causing performance issues.
In traditional building designs, these control layers are often distinct from each other. Separate systems become incredibly complex, forcing building engineers to maintain an unnatural continuity between them. Greater complexity increases the chances of failure.
A single, unbroken air and moisture barrier like those found in engineered building enclosure systems operates at maximum efficiency. In such a scenario, the enclosure has tighter control measures that operate synergistically. This level of continuity lowers the chances of failures.
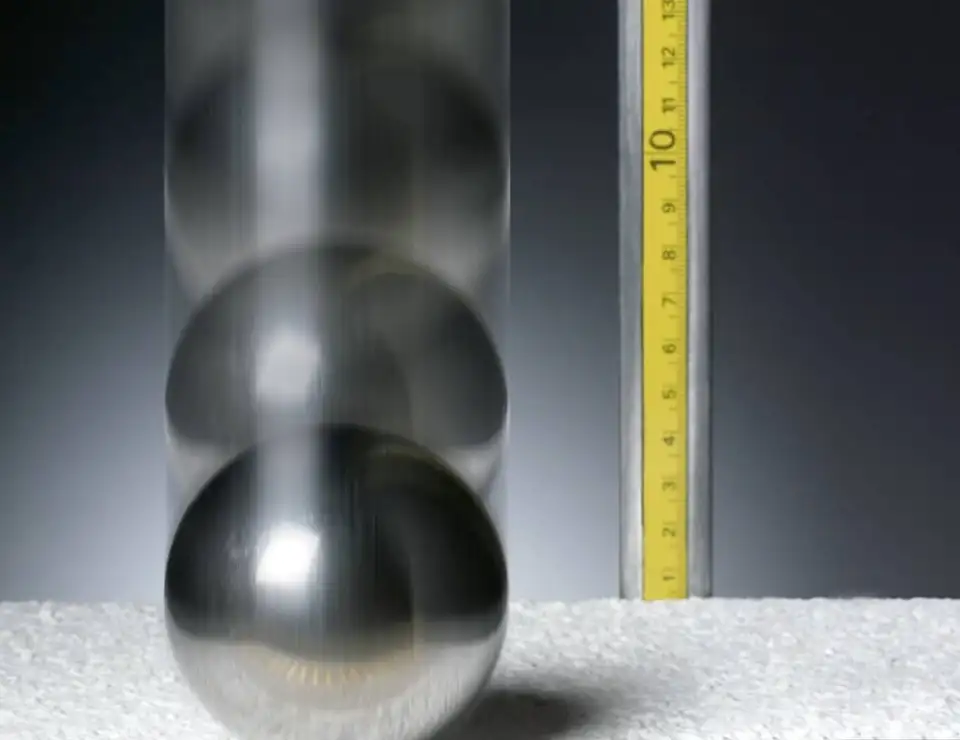
Continuous Insulation for Thermal Performance
The thermal barrier control layer is commonly achieved using insulation and provides crucial control that impacts occupant comfort and energy usage. Hence the reason why continuous insulation is one of the classic five Passive House principles. When the insulation is continuous and is placed on the exterior of the substrate, the thermal barrier lowers the detrimental effects of thermal bridging, where highly conductive or otherwise non-insulating material penetrates the insulation layer and transfers heat.
Metal is a highly conductive material and will siphon heat out of the building if it is not properly insulated. Steel is a key component of the building’s frame and a frequent culprit of thermal loss. Poorly insulated steel framing in the wall can reduce the building’s overall thermal performance, which can dramatically reduce a building’s energy efficiency.
Consider instead the benefits of exterior continuous insulation as a component of a building enclosure system. The continuous insulation maximizes a building’s efficiencies and reduces energy consumption. It also prevents condensation or a dew point within the walls by keeping the temperatures stable inside the wall cavity.
Minimum continuous insulation must meet specific R-values per building codes. There are multiple types of insulation—fiberglass, spray foam, mineral wool, EPS, and XPS, among others. Fiberglass and fibers such as EPS and XPS are optimal for walls and ceilings, while foam is better suited for formed concrete. These materials are widely available, lightweight, and easy to install.
The First Line of Defense
With the building’s façade, aesthetics is paramount. However, the façade is also the first line of defense against any forces acting on the building. The façade needs to be strong and durable to resist these forces, in addition to having a pleasant appearance.
Here are six forces that the façade must withstand:
· Mechanical, or ballistic forces, as well as interior shifts from metal expanding and contracting during temperature changes.
· Air pollution that’s either organic (soot or nitrogen oxide) or mineral pollution (dust from rock or dirt).
· Biological organisms (pests like insects or rodents) and microorganisms (fungal and mold spores).
· Water (through precipitation or humidity from dew and fog).
· Temperature changes (seasonal, HVAC-related, or due to fires).
· Light radiation (UV and infrared).
A smartly engineered building enclosure system enables designers and building owners to get optimal results on multiple fronts by relying on an all-encompassing protective system.
An enclosure that is resistant to mechanical or impact damage is less susceptible to deterioration from natural forces. Often, this becomes hyper-regional to account for weather events such as hurricanes in the Southeastern United States. Strong mechanical resistance reduces the risk of bulk water entry into the building during these events.
Certain building enclosures also have antiballistic capabilities. This protects the building from high-force winds found in hurricanes and from forces such as hail or bird collisions.
In addition, designers may employ new coating technologies such as UV resistance and biomimetic principles to provide additional protection and durability to the building enclosure.
UV-resistant coatings protect against the sun’s rays for years to come, preserving the colorful façade put in place while preventing further wear from occurring.
Biomimetic coatings and finishes mimic microstructures found in nature. One example is that of the Lotus leaf, which gives the coating a self-cleaning capacity. Every time it rains, the rainwater actually carries away dirt particles and other harmful contaminants. Another is a coating that emulates the microstructure of the fog-basking beetle, which promotes fast drying of surface dew and mist particles, removing a food source that mold and algae use to grow on the façade surface.
The Power of One: A Systems Approach
Specifying a single-manufacturer, all-inclusive building enclosure system that is comprised of all control layers for the building’s exterior translates into smarter, more efficient management of the many variables in the design, specification, and construction process.
Code compliance and fire testing are important considerations, too. NFPA-285 is a system-level fire test. This means an entire assembly with all control layer components undergoes testing to determine if fire can transition to the interior, potentially move laterally across the building, or migrate vertically from floor to floor. Using a building enclosure system that has passed NFPA-285 testing provides peace of mind because the entire solution is deemed compliant before it is even installed.
On the job site, hiring a single subcontractor to install the combined air barrier, insulation, and façade—all components of a building enclosure system—saves both money and time. Having less to schedule in advance lowers the risk of delays that might interfere with other contractors’ schedules.
Then comes the warranty. Using three different products means dealing with different warranties and different sets of performance criteria. Doing so also raises compatibility and continuity issues, which can introduce a host of unforeseen challenges. A single-source building enclosure system provides an entire solution covered by one warranty, resulting in fewer questions, less complexity, and one manufacturer to handle it all.
The ultimate result is a higher performing, more compelling building that is ready to stand the test of time.
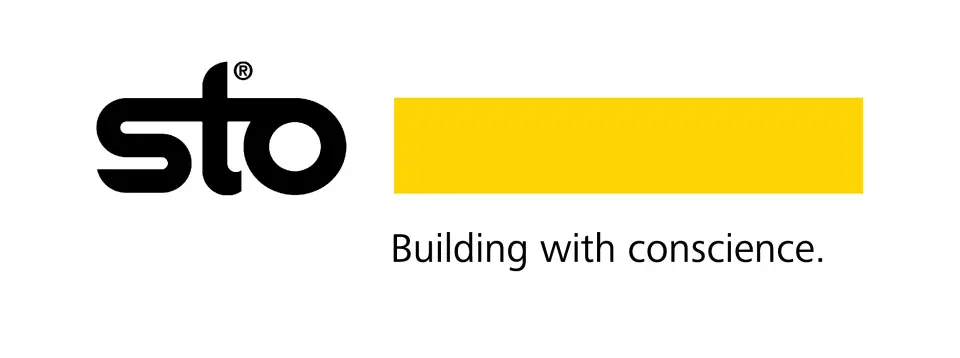