A deep energy retrofit is underway on a busy residential block in Johnson City, Tennessee. What makes the project so unique is that the home endured for more than 100 years without a comprehensive overhaul, save for the refurbishment of the electrical system and some superficial remodeling. More surprisingly, it was still in relatively good shape.
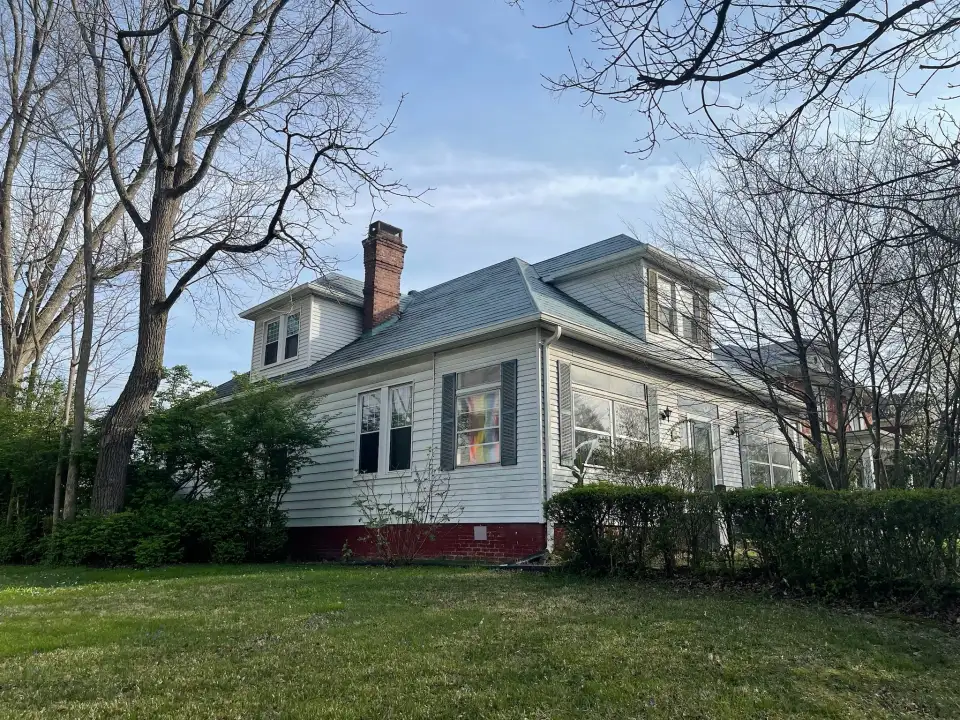
Johnson City Retrofit Strives to Become a Net Zero Energy Home
“Luckily, the renovators hadn’t gotten to it yet,” says Lost Cove LCA President Jamie Constantopoulos. He notes that part of the reason owners Jeff and Martha were attracted to the 1910 home was because it still had many of its original features, including its plaster and flooring. “One of the reasons they hired us is because we recommended not gutting it,” Constantopoulos continues.
While Constantopoulos’ recognition of the home’s character endeared him to the owners, their decision to hire Lost Cove LCA for the retrofit was largely because of Constantopoulos’ experience with high-performance retrofits in southern Appalachia.
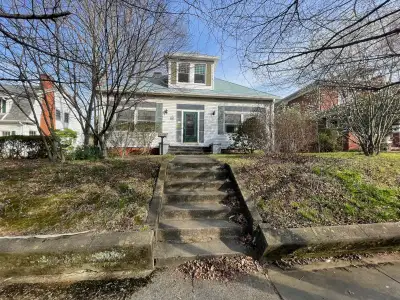
Originally from Arizona, Constantopoulos had come to Tennessee to study music and had been a professional musician for some time, but the pandemic led him back to the construction industry. Since 2020, he has worked on multiple projects as an electrician, started his own residential construction company (Lost Cover LCA), and become a certified Passive House tradesperson after training with Colorado-based Emu Passive.
Constantopoulos has worked on several deep energy retrofits. In the past, he has followed the Pretty Good House approach to homebuilding or replicated Joe Lstiburek’s Perfect Wall concept. However, with the Johnson City project, he is hoping to achieve performance levels that meet the EnerPHit standard, the Passive House Institute’s retrofit program. Constantopoulos says that the owners had been interested in EnerPHit since even before they met him, and that this helped set clear expectations with respect to budget and performance from the project’s beginning.
Additionally, setting expectations early on helped the owners prioritize their goals, as budget restraints will require them to break up the retrofit into two phases. The first phase will focus primarily on making the building enclosure more robust, which will allow them to downsize their mechanical systems and possibly get to (or possibly just shy of) EnerPHit levels of performance. This phase will also include the installation of a modest photovoltaic array (1200W) to offset the new HVAC system, which will be quite small due to improvements in the building enclosure. Once the resources are available, the owners plan to begin the second phase of the retrofit, which will see the installation of a larger solar system and other means of further reducing the home’s emission levels, hopefully bringing them down to net-zero.
Initial Stages
As is so often the case with deep energy retrofits, Constantopoulos started with an energy audit. This was performed through Emu Passive. With the audit, he was able to give the owners concrete data about their baseline energy use and the levels of energy savings they could expect depending on what improvements they made to the home.
Unfortunately, Constantopoulos was prevented from establishing a baseline for the home’s level of airtightness for a fairly unique reason. “These old houses used to be coal-fired,” he explains of the neighborhood in Johnson City. “They have an incredible amount of soot in every single crack in the house.” Consequently, creating negative pressure in the home through a blower door test would result in all that soot getting sucked out into the living space.
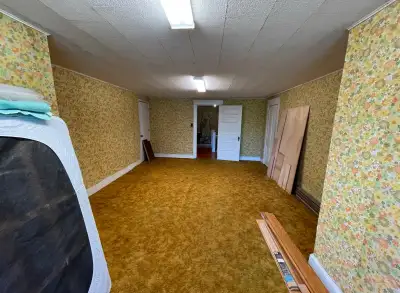
As Constantopoulos learned, it’s way more soot than you think it will be.
On a previous job where he worked as an electrician, he says that the HVAC team installed a ducted system after pulling out the formerly coal-fired home’s radiators. The first time they turned the system on, the negative pressure resulted in a belch of soot from every crevice. “I think they ended up having to do an insurance claim,” Constantopoulos says. “It was that bad.”
This time around, Constantopoulos has solely been putting the house under positive pressure for the duration of the retrofit. If it seems like they’re going to hit the EnerPHit targets, only then will they put the house under negative pressure and deal with the inevitable cleanup.
Constantopoulos also relied on the Emu Project Boost for solar modeling to better understand how to best position overhangs and windows. “It gave us good information about what our heating demand was going to be based on foliage that was blocking sun during the summer and that kind of thing,” he says.
Sequencing Construction
As the owners decided to remain in the home throughout the retrofit, the team had to figure out how to keep them comfortable. They also needed to ensure the owners had access to power at the end of every workday. Luckily, each of the two floors of the 2,400-square-foot home had enough space to accommodate the owners, so this did not present a major problem.
To start, the owners remained downstairs while the team worked on the upstairs interior. They updated the flooring, installed a shower in the bathroom, and modernized the appearance of the space, but did not alter the floorplan. Starting on the upper floor also allowed the team to access the vents in the first-floor ceiling and to begin installing the Brink ERV system.
The owners moved upstairs once work on the top floor was complete, and then the team began renovations on the ground floor. This part of the project also saw work start on the building enclosure and the installation of the home’s new mechanical systems. Some sitework was also done, as the steps leading to the front door and a retaining wall in the front yard had to be replaced. Constantopoulos notes that some additional sitework needed to be done because poor drainage regularly caused water to pool around the foundation.
Wall Assembly
Prior to the retrofit, the home contained no insulation—something common to the area, especially for homes built in the 1910s. The assembly was just an extra thick 2x4 oak structural panel with the original siding plus an additional layer of siding that had been installed over it. The Lost Cove LCA team hopes to use the design of the original siding for the home’s cladding, but the original is no longer salvageable. “It was in rough shape when they resided it and they covered it up with vinyl siding, which just traps moisture and rots out anything that’s there.”
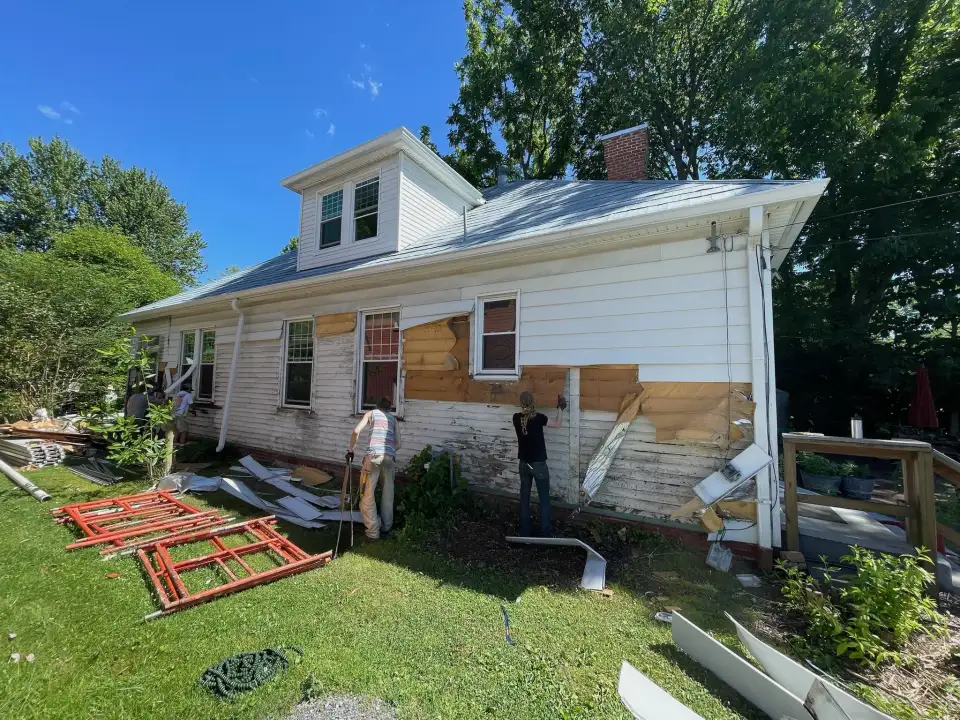
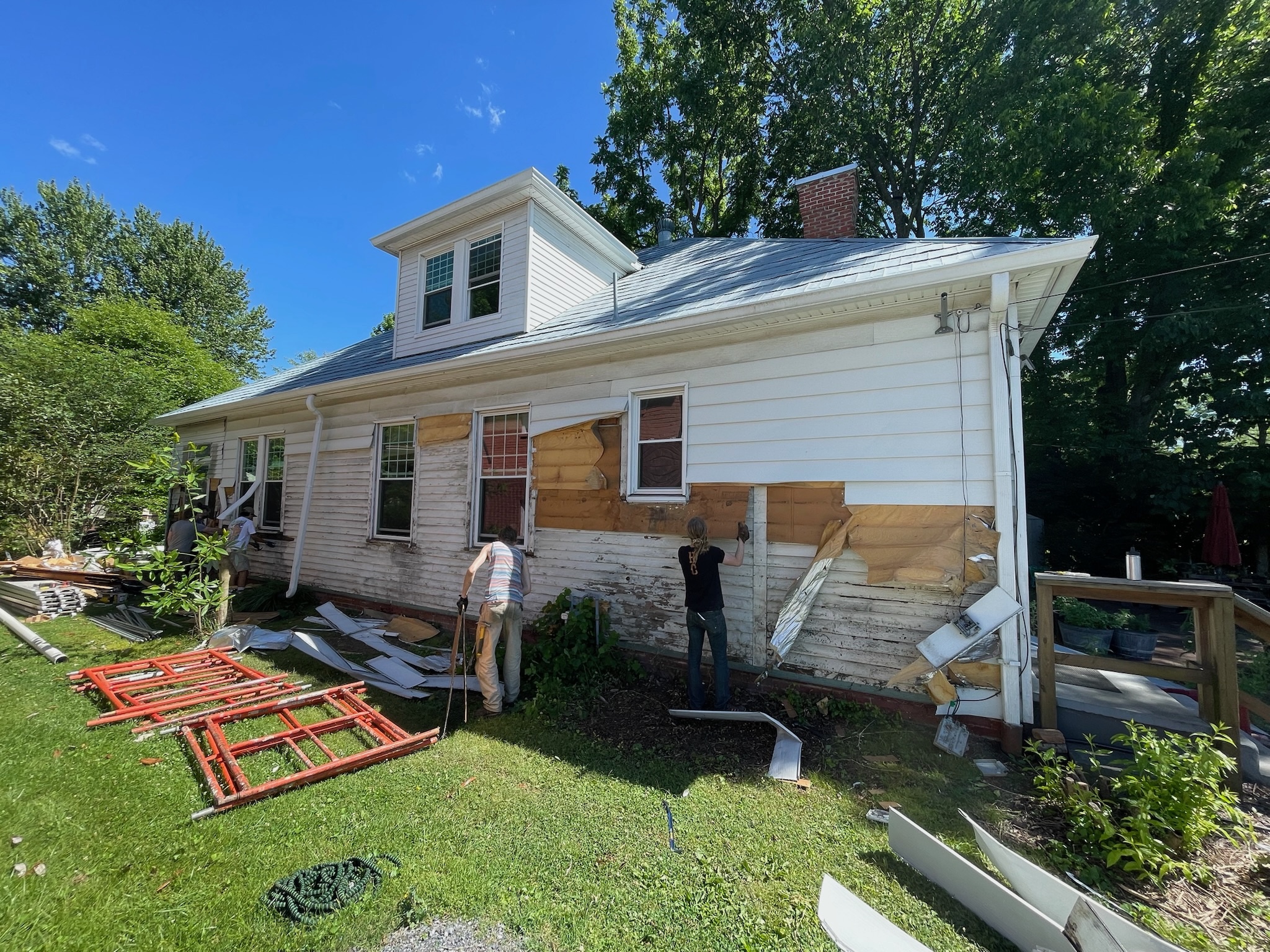
Progress stripping the home's siding and installing the INTELLO X.
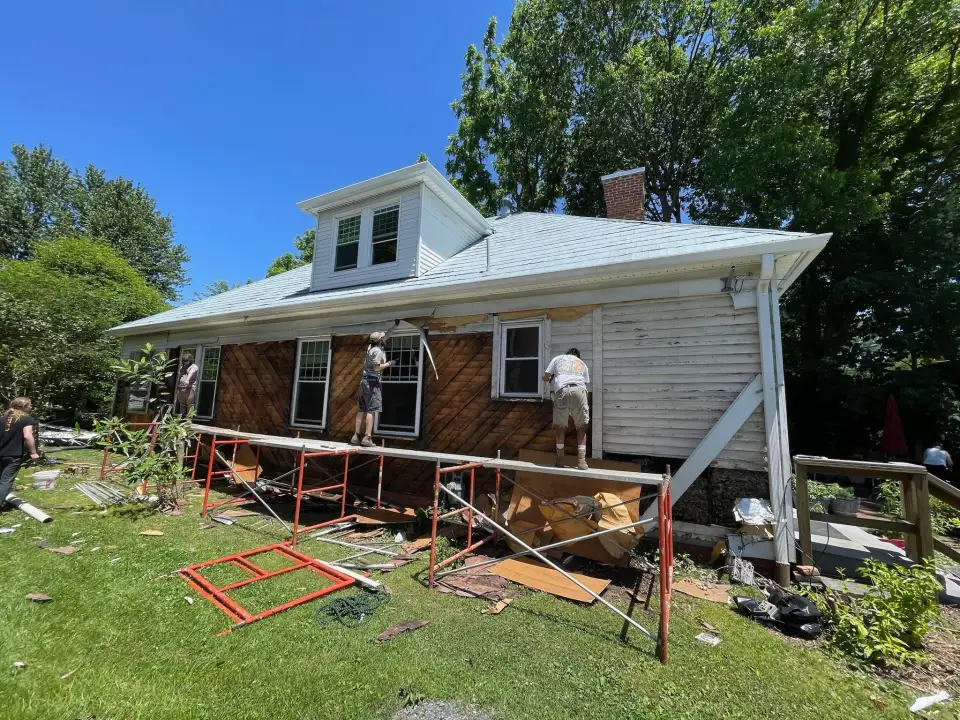
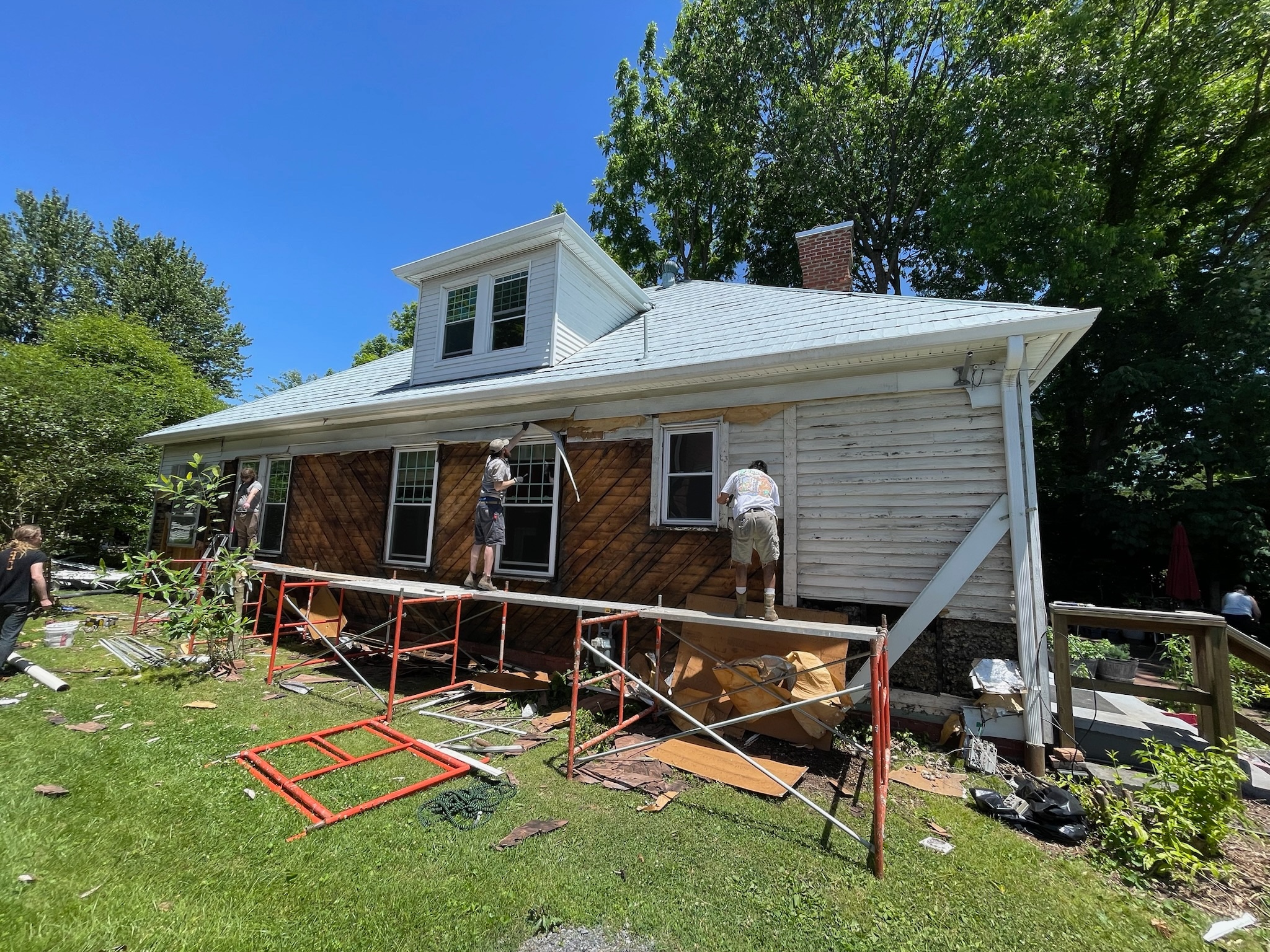
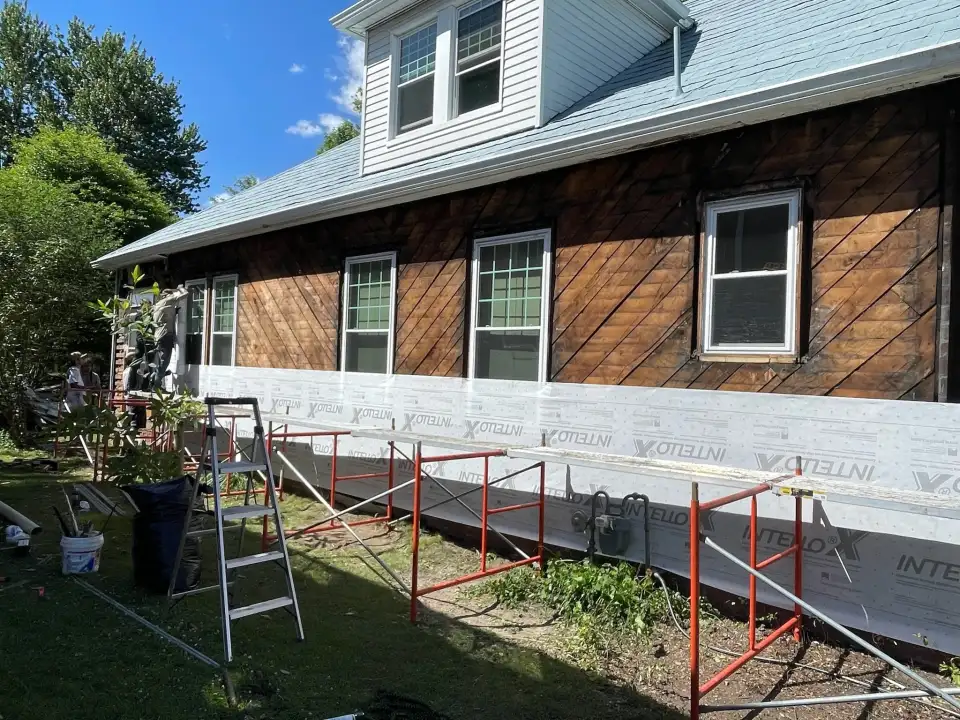
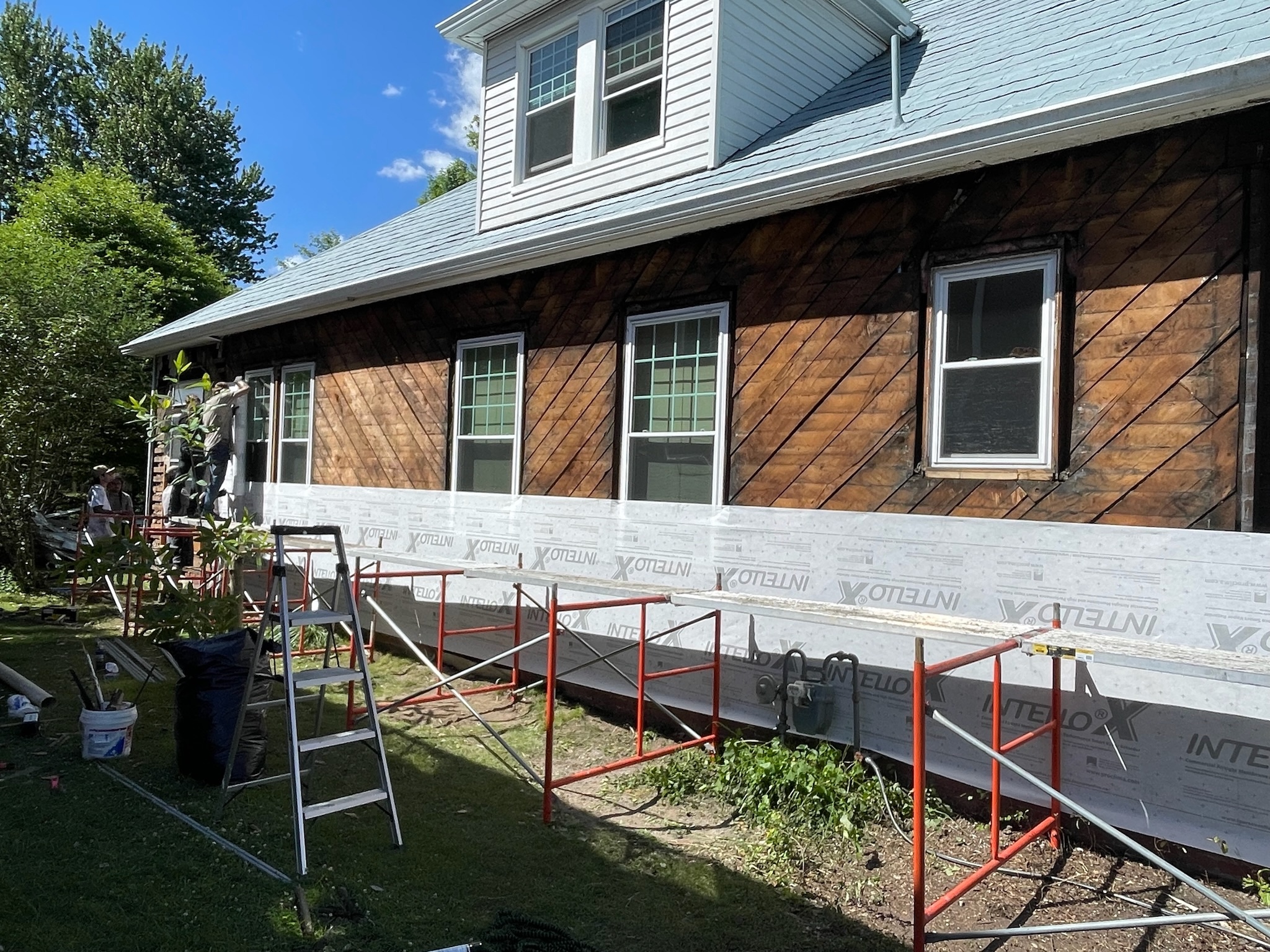
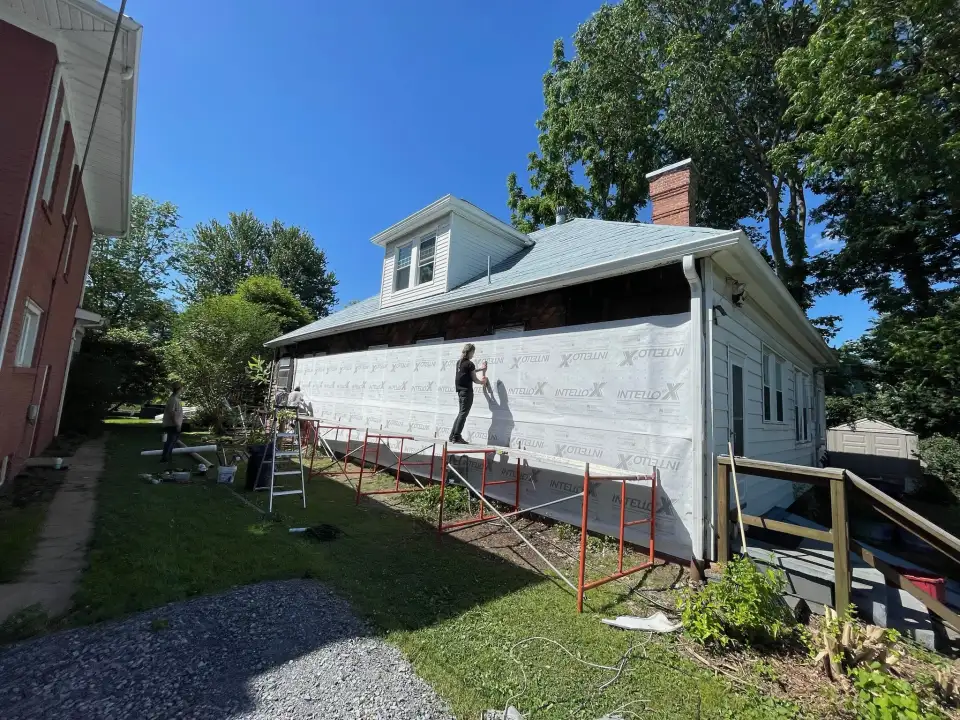
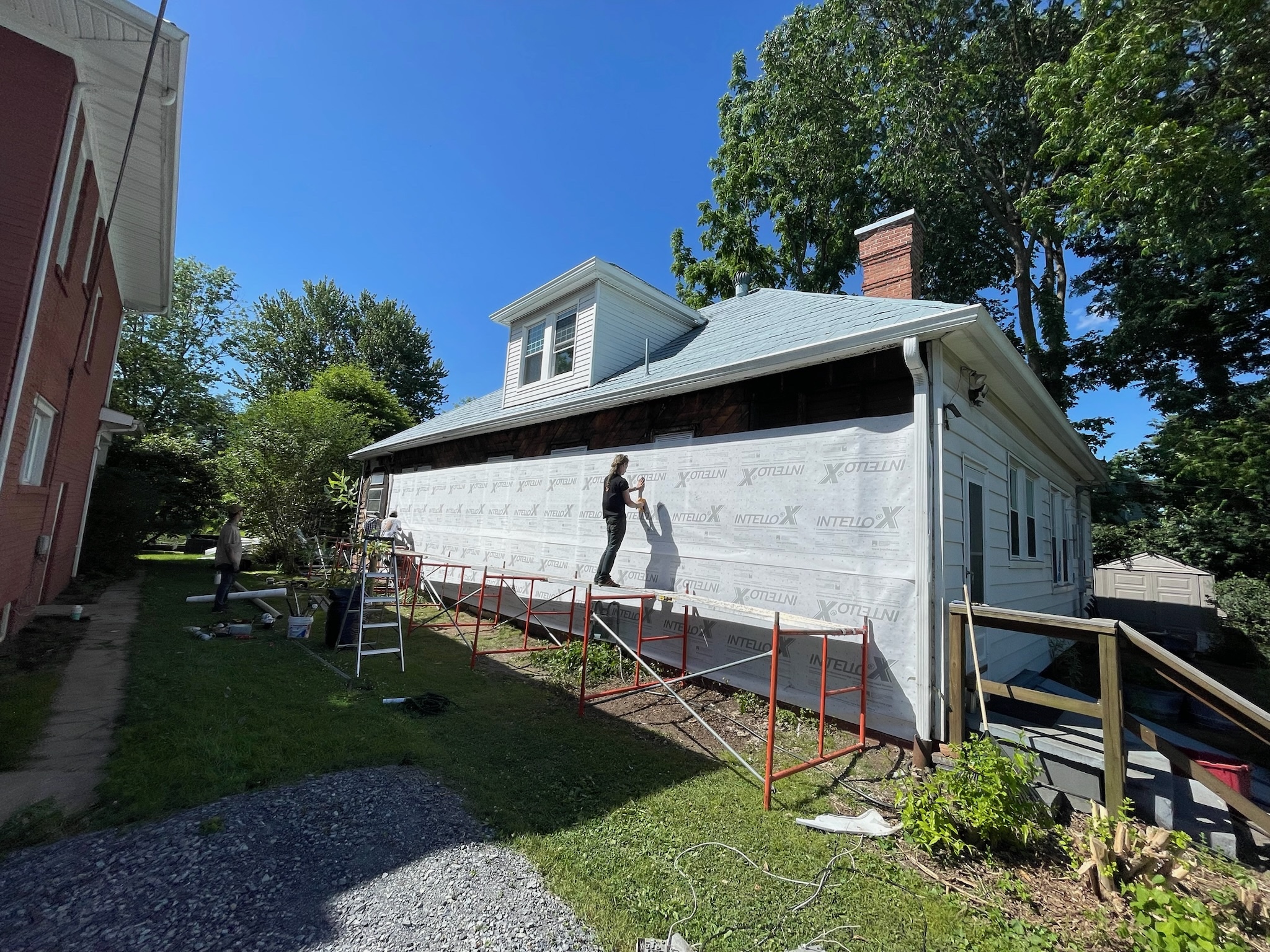
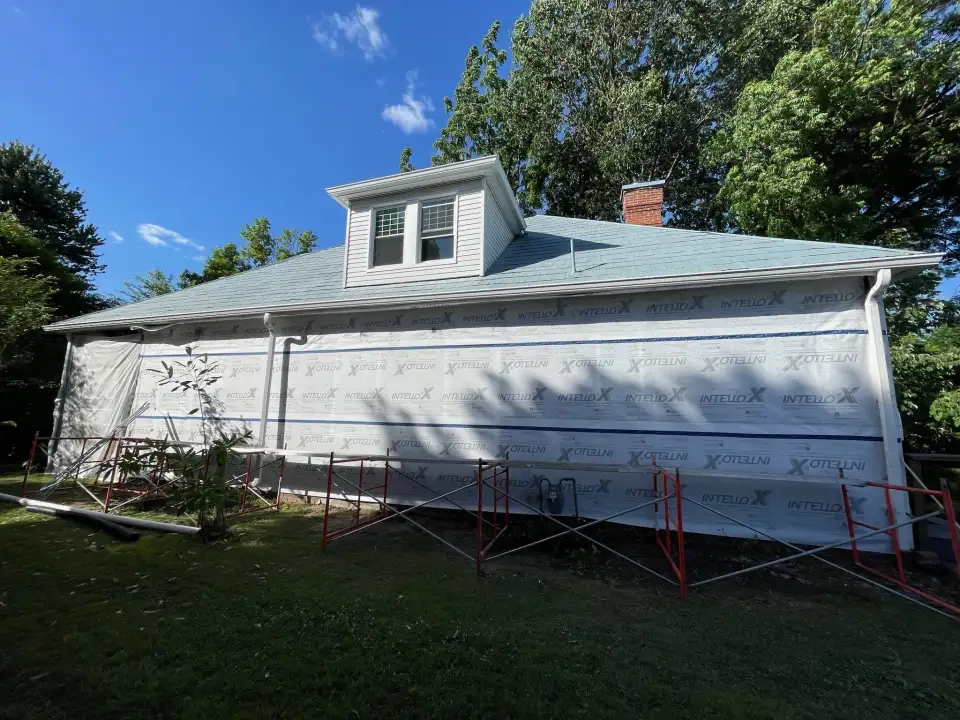
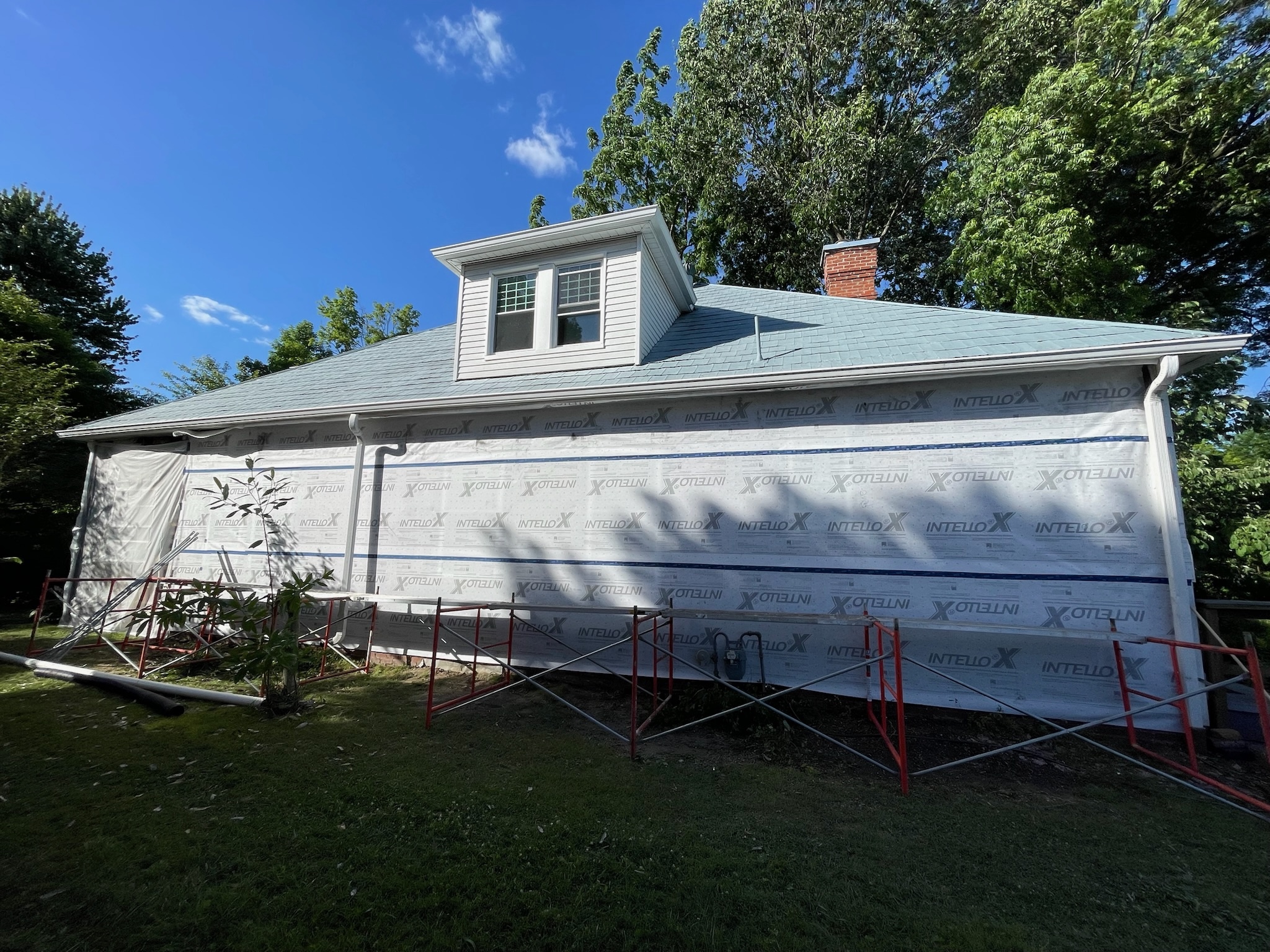
After stripping the siding off, the team wrapped the walls in INTELLO X to create an air barrier and smart vapor retarder. Once the barrier was set up, the team then built out a 2x8 Larsen truss system. On the backside of the truss are OSB plates every 16 inches, which are screwed to the wall. The system rests on a double-ledger board that goes all the way around the truss’ bottom.
On account of a mineral wool shortage, Constantopoulos opted to use high-density fiberglass batt insulation within the cavity of the truss. In addition to solid insulating properties that boosted the average R-value of the wall assembly to R-30, fiberglass also has great acoustic qualities, which is important given the fact that the home is on a relatively busy street. The team then wrapped the home in SOLITEX MENTO 1000 and 3000 and will begin installing clapboard siding in late October or early November 2024.
Constantopoulos notes that one of the trickier details occurred along the connection between the walls and the roof. Constantopoulos had hoped to perform what is known as a “chainsaw retrofit”, which involves lopping off any protruding rafters (chainsaw optional) to make them even with the exterior wall plane. The major benefit of this technique is that it makes it far easier to maintain a continuous air barrier between the top of the wall and the roof.
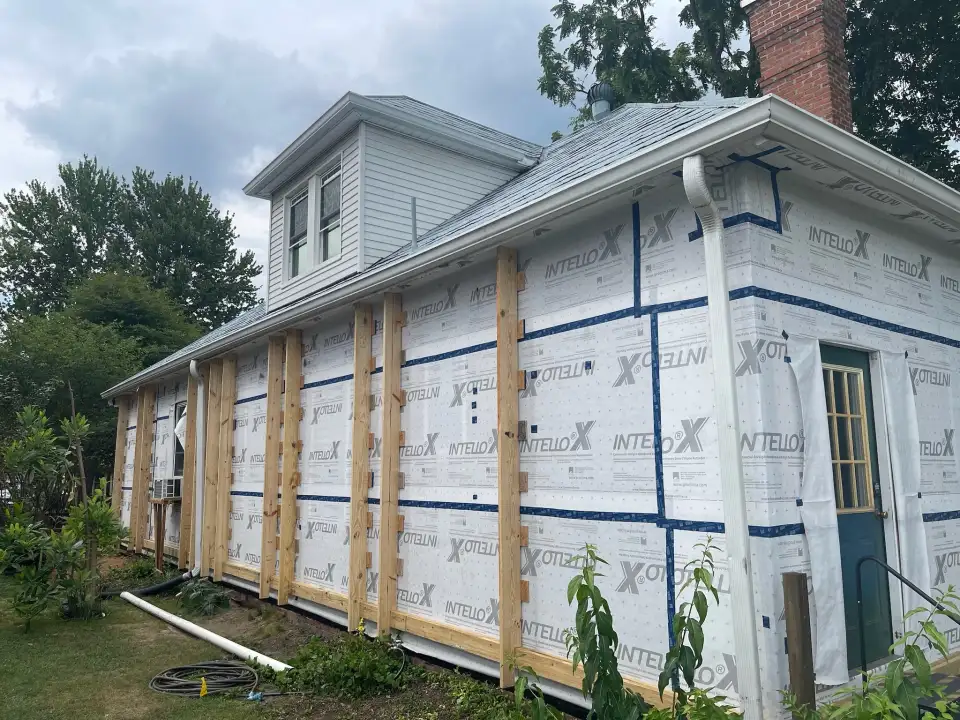
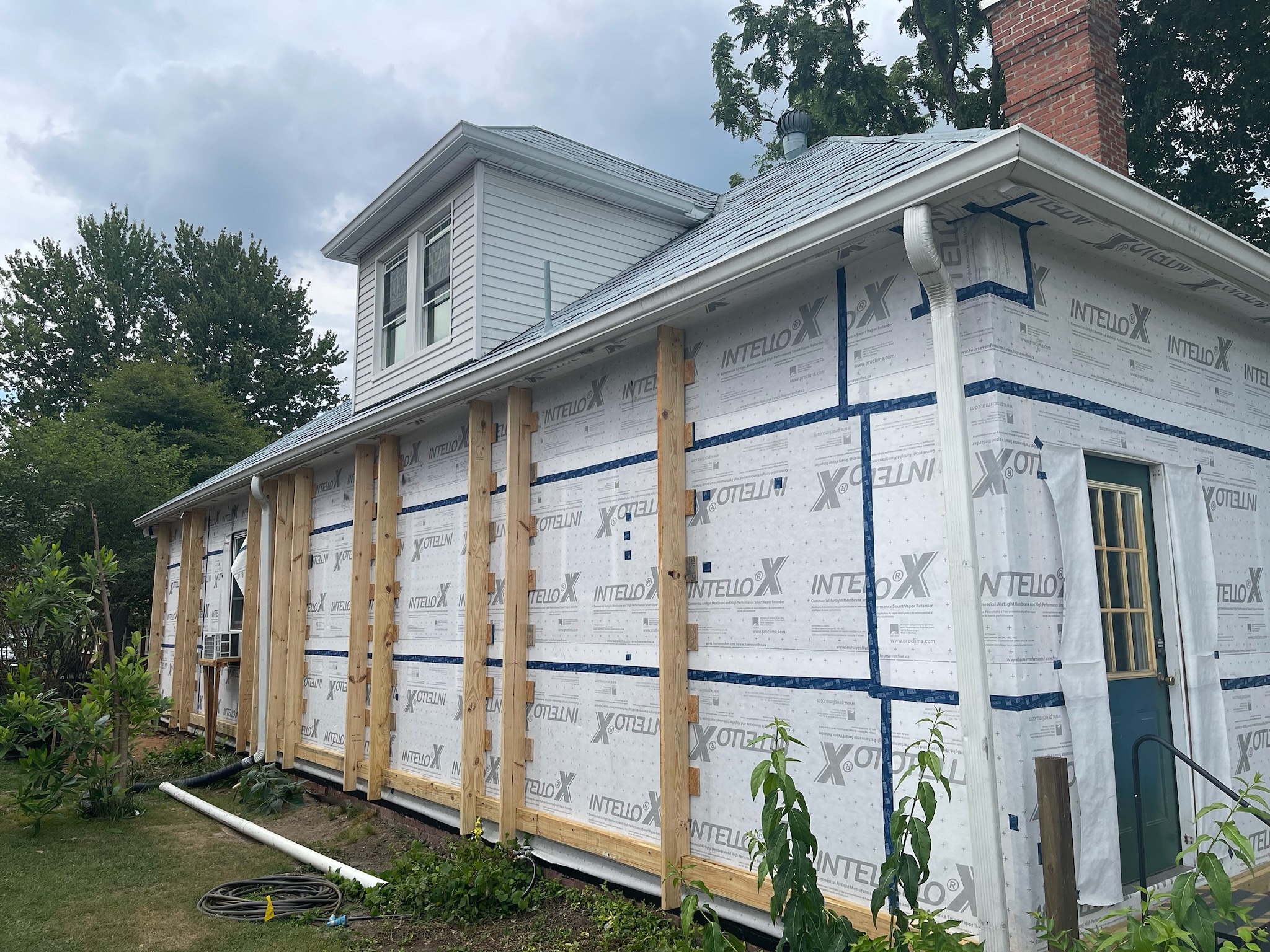
Progress installing the Larsen truss system.
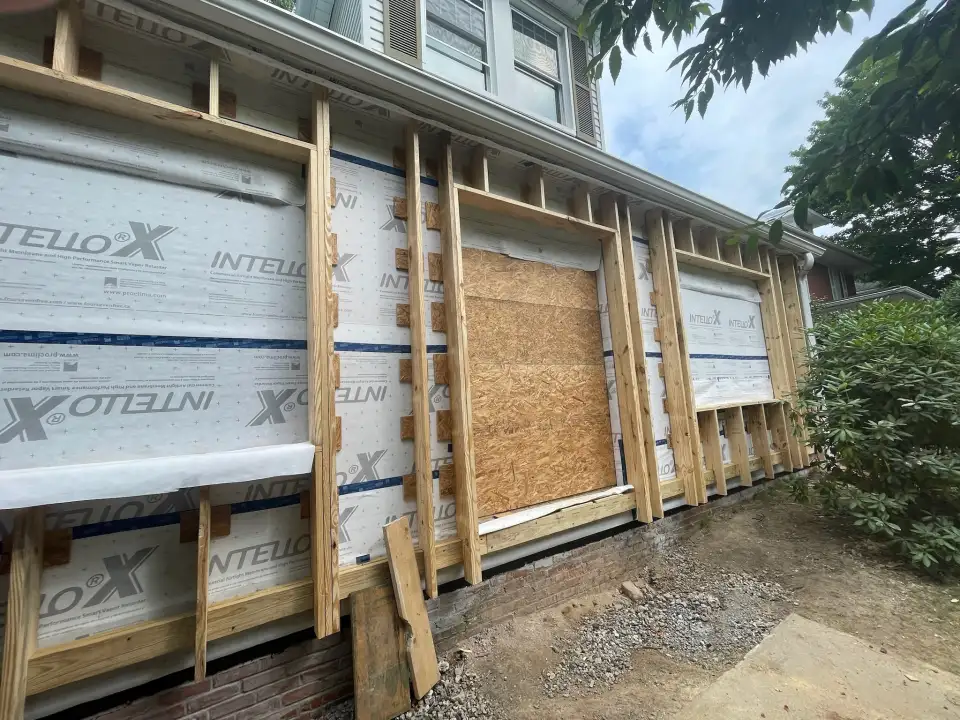
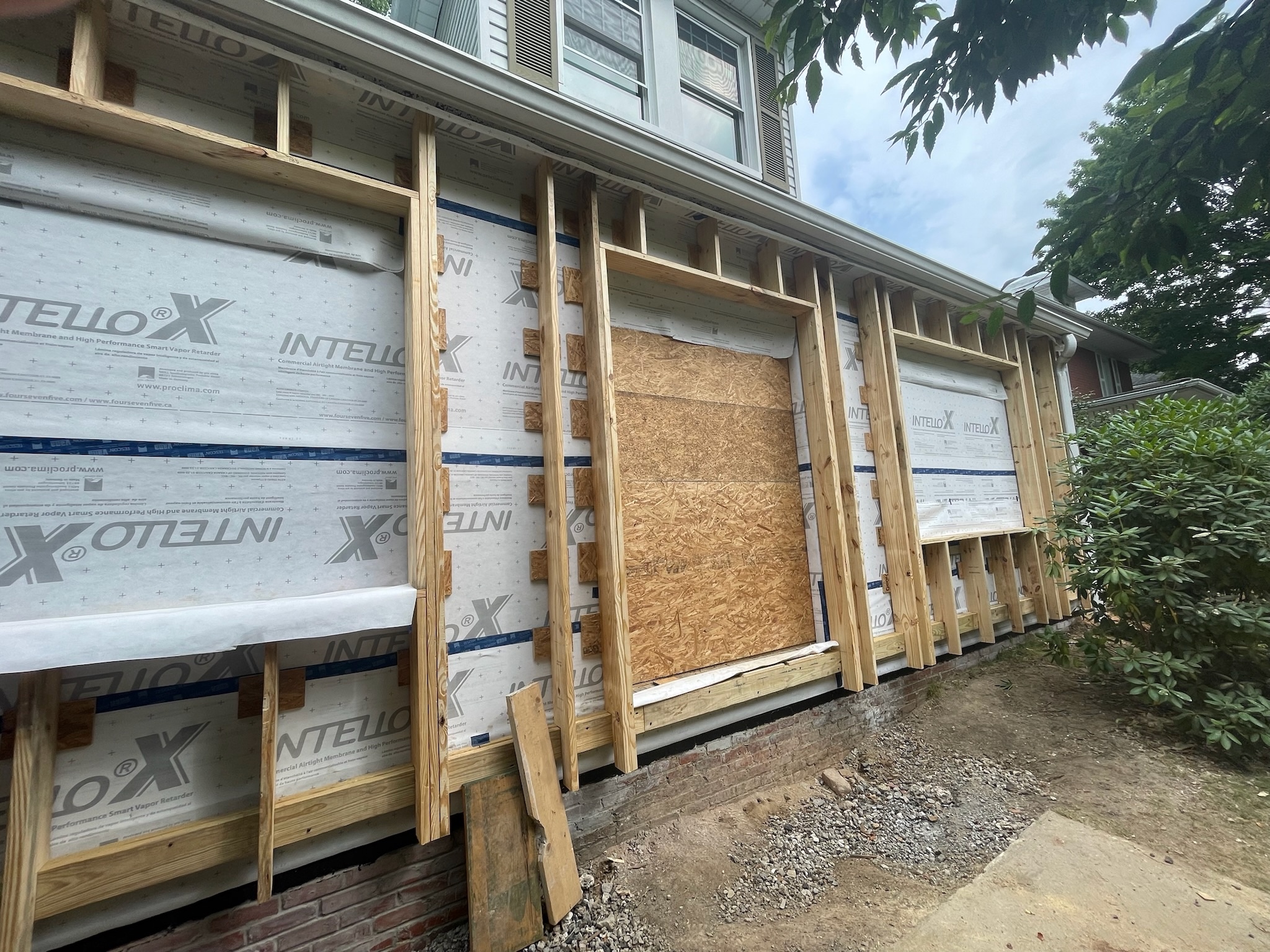
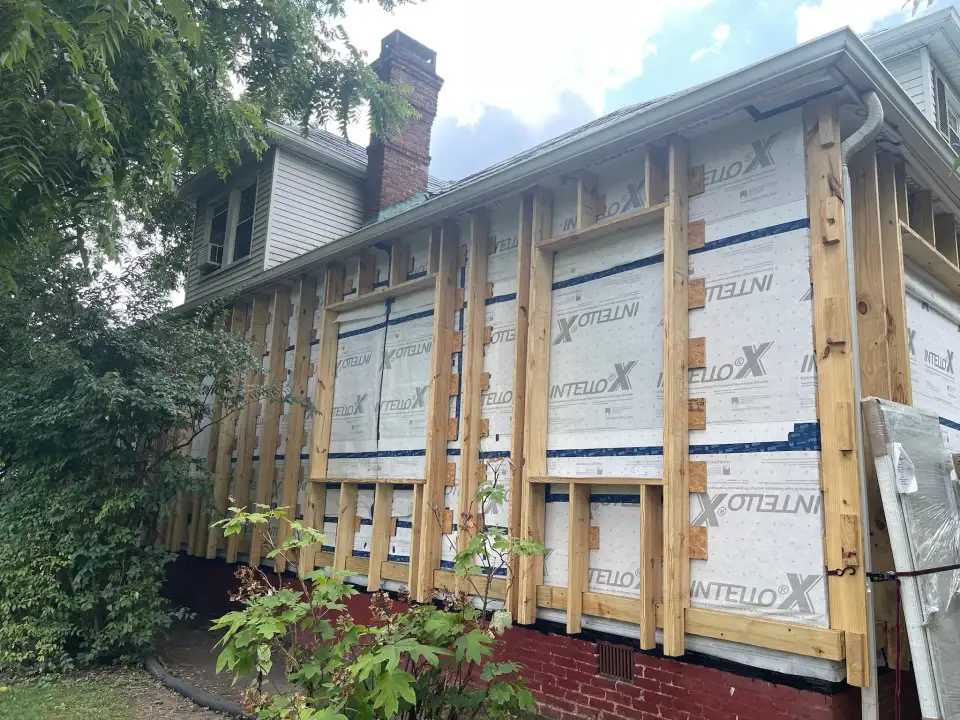
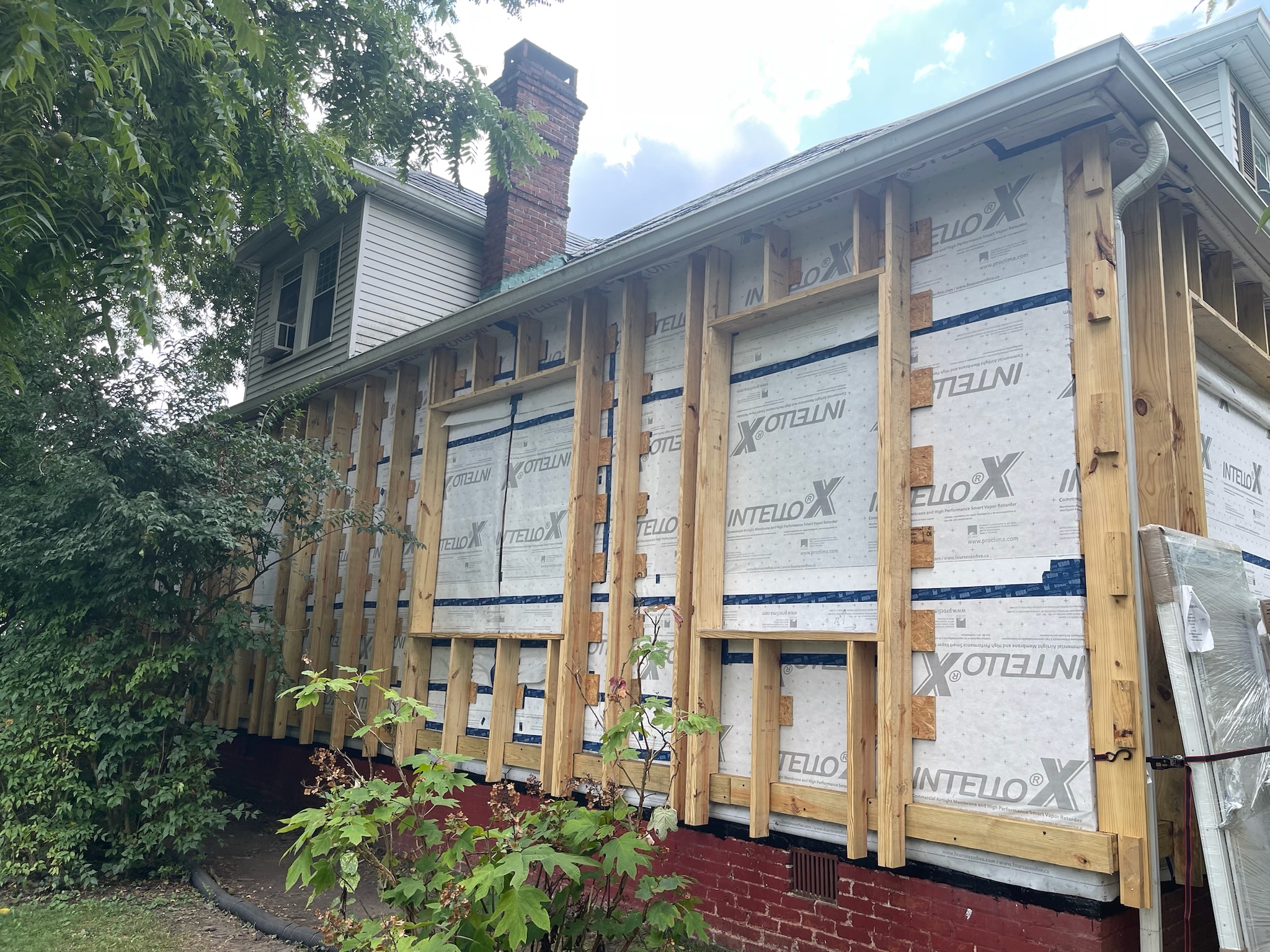
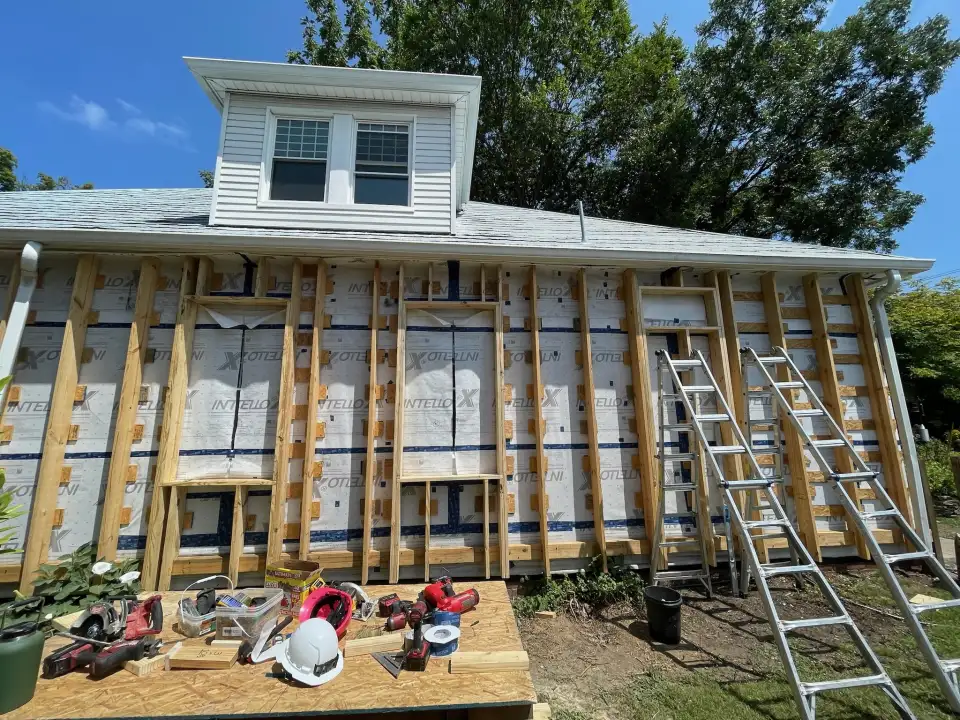
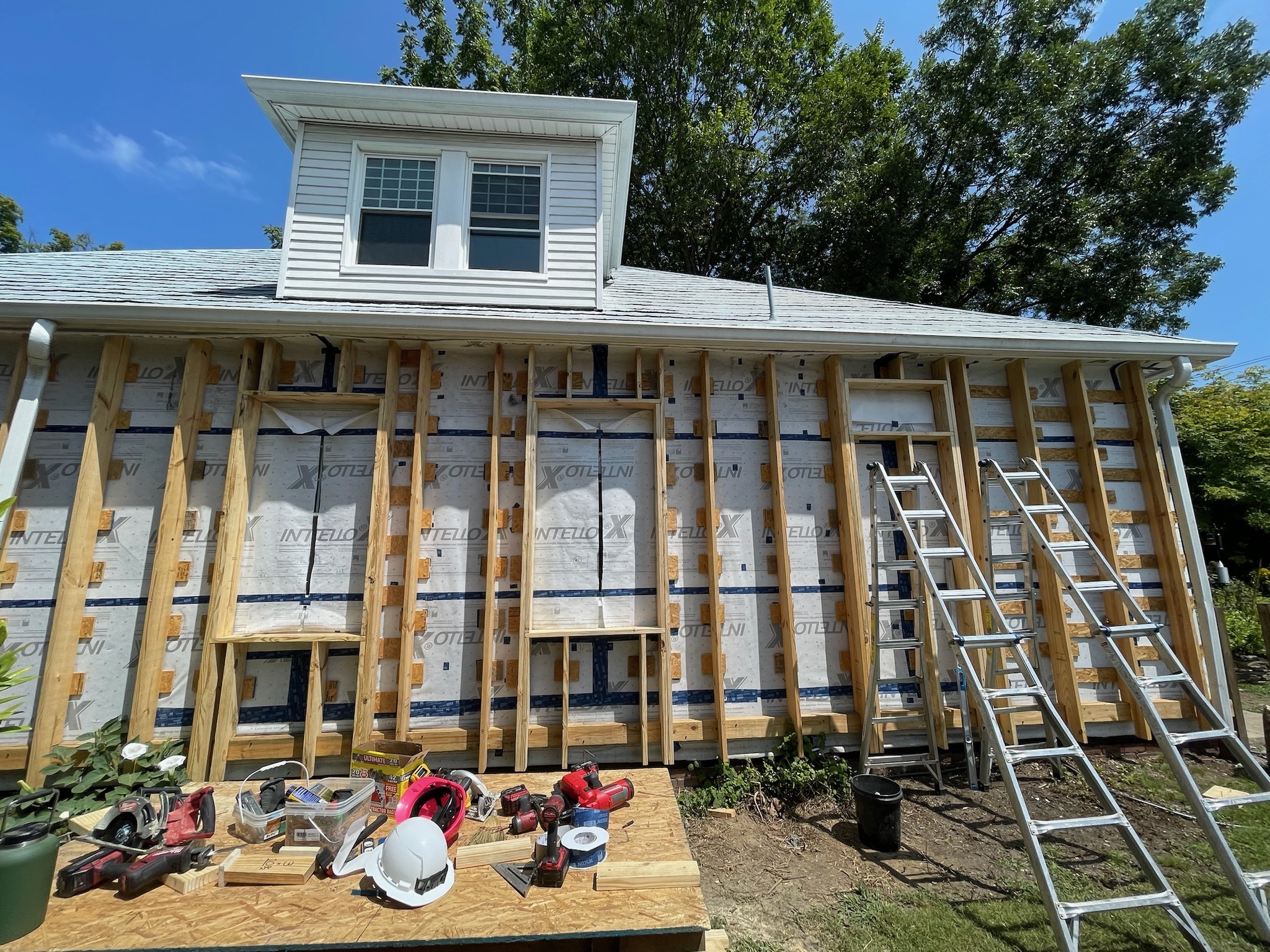
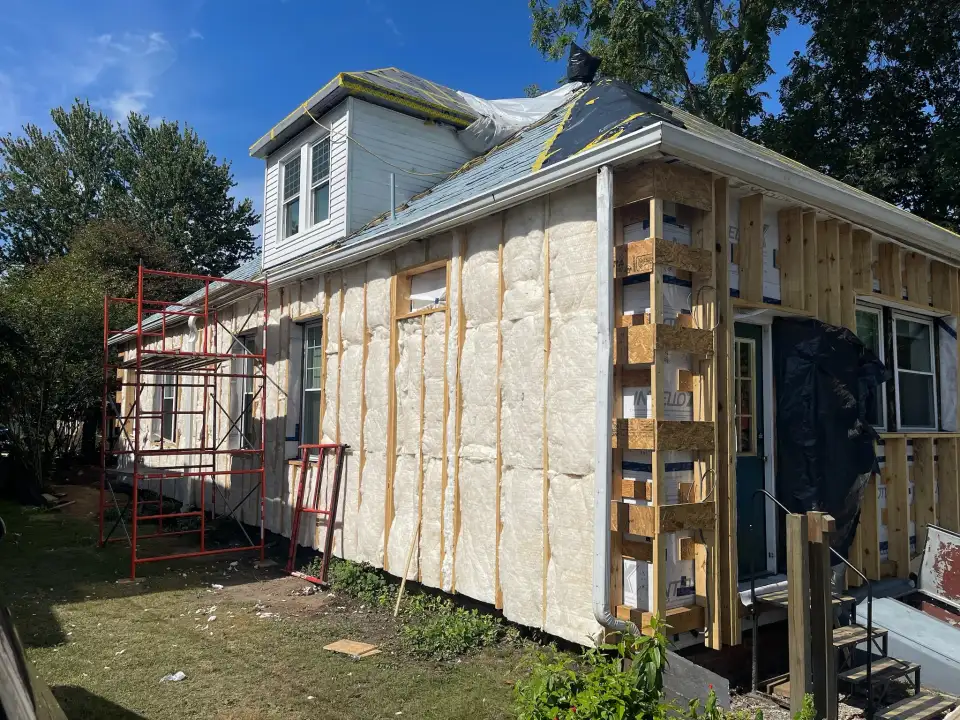
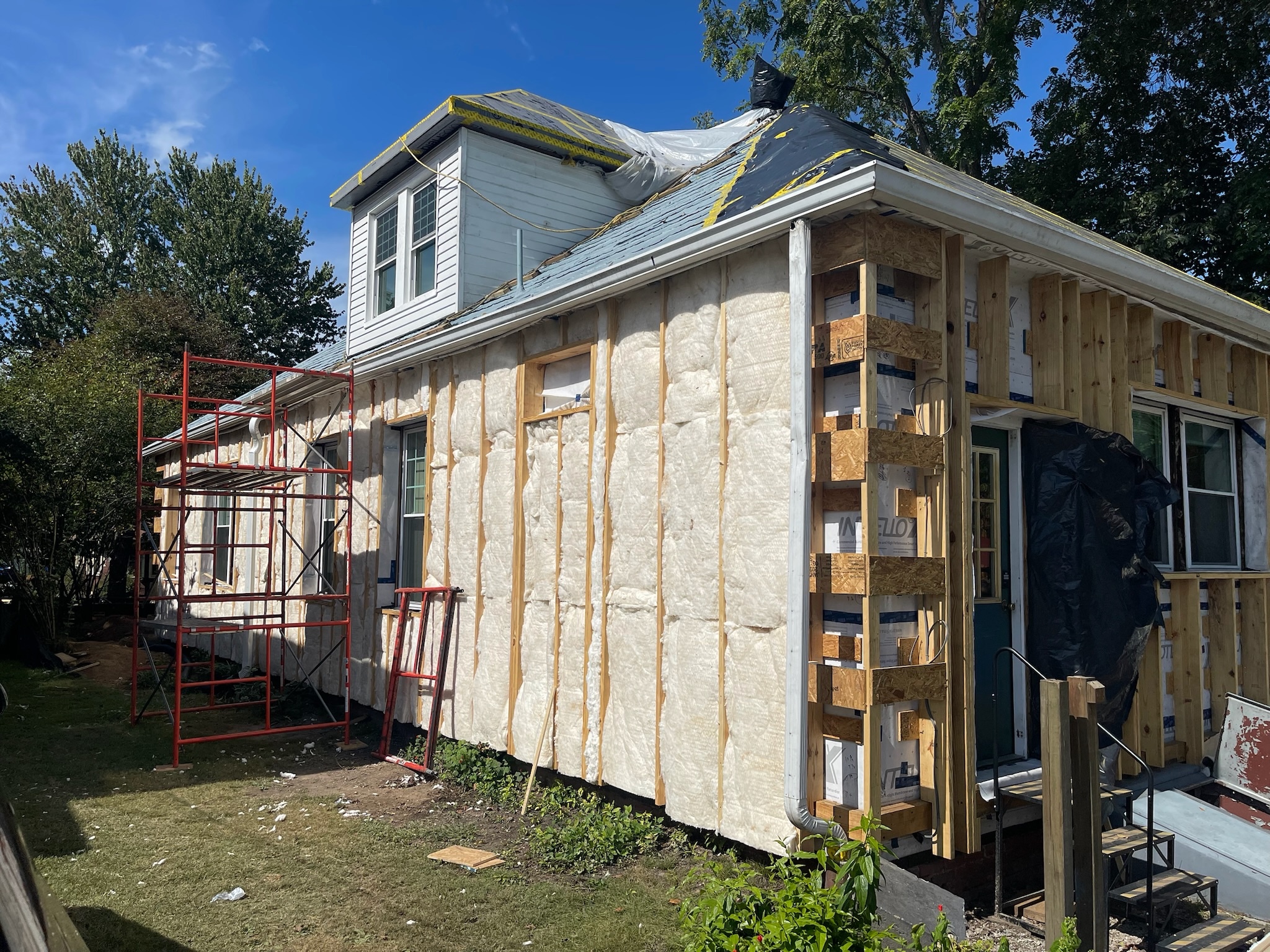
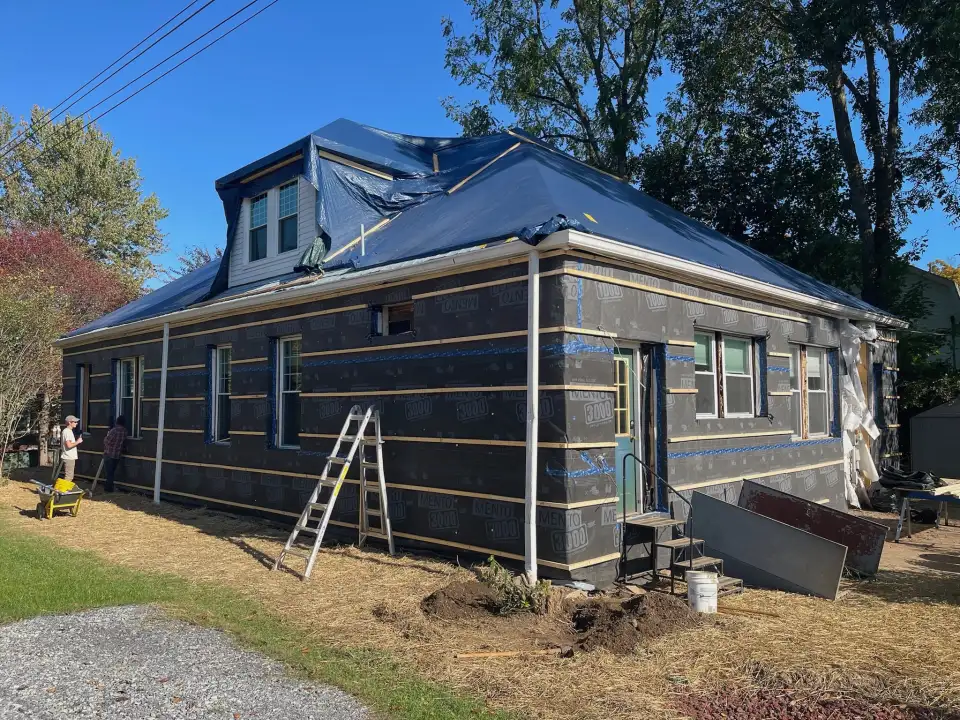
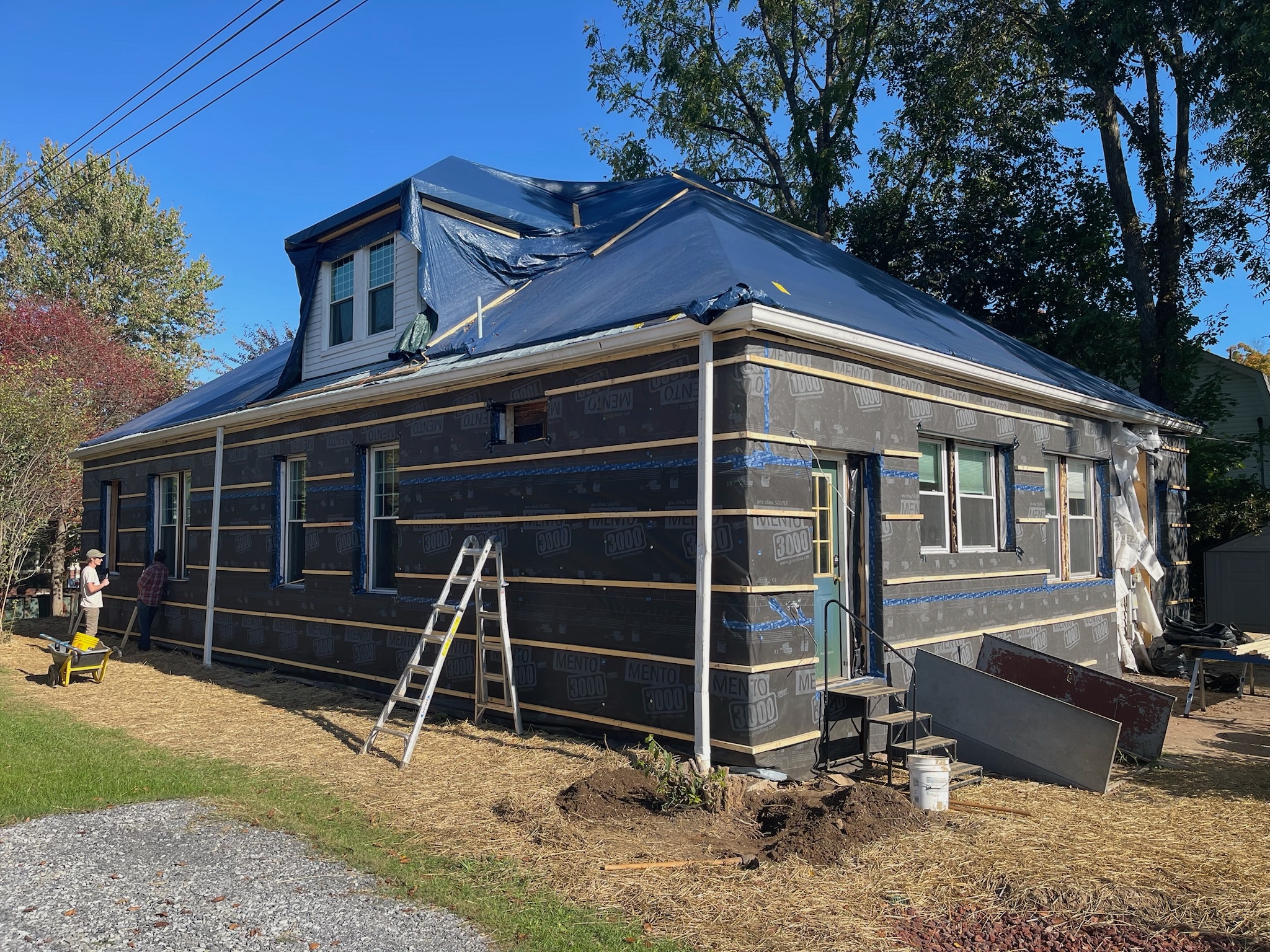
Unfortunately, this wasn’t possible because the overhangs were cantilevered. “Basically, the floor system from the attic goes out over the top plate and then the rafter actually lands out on that rather than on the top plate,” Constantopoulos explains. Consequently, they had to wrap the INTELLO all the way up underneath the soffit. “There's a lot of origami going on in that air barrier, but we figured that was easier than trying to restructure the whole roof.”
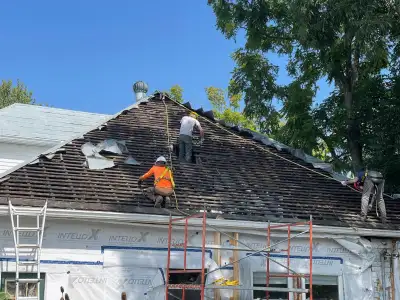
While getting the assemblies to be airtight was certainly difficult, they do plan to hit the 1.0 ACH50 EnerPHit target. Unfortunately, they still may fall short of achieving EnerPHit certification because of structural limitations with the roof system. As Constantopoulos explains, the roof is made of 2x4 rafters that may not be capable of supporting a robust enough layer of continuous insulation to get up to the R-value that was recommended in the modeling (R-60). They have explored alternative methods of getting more insulation into the roof assembly to bring down heating and cooling demands, including extending the Larsen truss over the roof. However, the structural engineer on the project said that the existing roof system wouldn’t be able to handle the weight. The city was also not okay with the idea. Ultimately, they decided to use EPS foam with a deck on it because it strikes a balance of being lightweight and bringing the roof’s R-value close to where it needs to be, but it still may not be enough.
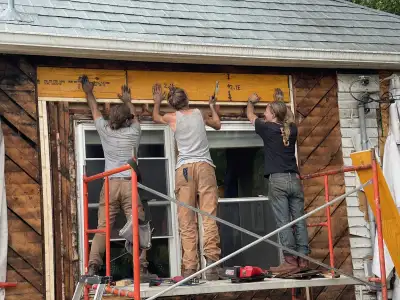
Another issue that came up was the fact that the windows did not contain headers. As the team did not discover this anomaly until after installing the INTELLO wrap, they had to go back, slice open the barrier at every opening, peel it back, put a header in, and then tape it all up. Luckily, many of 32 window openings were side-by-side windows, and they were able to consolidate these openings into one larger window manufactured by New Jersey-based Wythe Windows. Constantopoulos was excited to work with Wythe because they are relatively local and have been able to provide a combination of fixed and operable triple-pane windows in the dimensions the team needed.
One issue that did arise, however, was that many of the spans are very wide—the longest being 13 feet—and the team did have to seek out additional assistance with the structural engineer. “Because we're increasing the roof load by so much, we really wanted to make sure that it wasn't going to start cracking plaster with those big spans,” Constantopoulos says.
Mechanicals
Johnson City is in climate zone 4A and the HVAC system has been designed to operate down to 13°F. Heating and cooling primarily comes from an outdoor Chiltrix heat pump that runs water to the four fan coils within the home and heats the domestic hot water. As the region tends to experience an extreme cold snap every few years, with temperatures sometimes plummeting to 0°F, an auxiliary heater has been included too. All systems, including the auxiliary heater and the domestic hot water system, are electric.
To improve resiliency in the event of a power outage, Constantopoulos updated the electrical systems and installed a SPAN Panel. The smart panel can be programmed to prioritize specific circuits should the grid go down. “It does really well with load shedding and battery backup,” he says. “It also manages solar really well.”
Retrofit Advice
As Constantopoulos wraps up the first phase of the project, he does have a few pieces of advice for teams that want to do a Passive House project. First up: Overestimate your budget, especially on a retrofit. You will be surprised, and you will have to change your plans to deal with these surprises.
Second, installing a dryer in a Passive House can be challenging, especially if you decide to vent it. Consequently, Constantopoulos recommends either putting the dryer outside of the envelope or getting a heat pump dryer that does not need to be vented, which was the solution for this project.
Finally, for those who are doing the tedious job wrapping a house, Constantopoulos says this: “Cut it long and tape all your folds.”
Constantopoulos also recommends using mockups to better visualize how to properly tape tricky corners and connections, since it can be difficult to describe. Instead of talking through it, he says it is far easier to have a visual aid, so he relied on a 2x4 mockup that 475.Supply Senior Product Consultant Nick Shaw created, which has been kept on the jobsite.
Given the attention to air-sealing, as well as the upgrades to the mechanical and electrical systems, the house is sure to be comfortable and resilient for years to come. “It should last another 100 years,” Constantopoulos says.