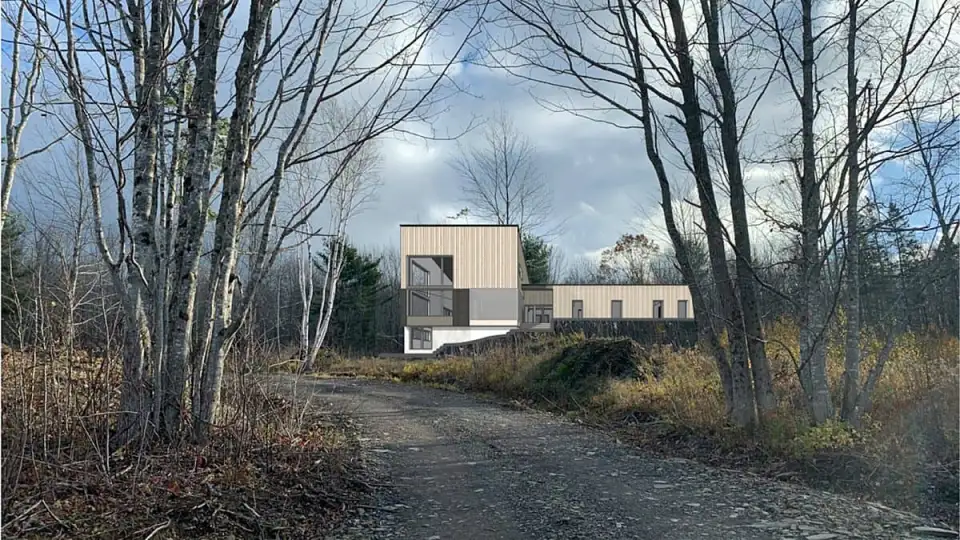
It’s no secret that retrofitting existing buildings is crucial to cutting carbon emissions from the building sector, and yet in most jurisdictions, actual deep energy retrofits lag far behind stated goals. “People have to stop studying retrofits and actually do them,” says Lorrie Rand, principal of Habit Studio in Halifax, Nova Scotia. “Although the province has aggressive GHG [greenhouse gas] targets,” Rand points out, “if we don’t do something with existing buildings, we can’t hit those targets.” Rand has moved into action, cofounding the ReCover Initiative with Nick Rudnicki of RSI Projects, a custom builder, to industrialize deep energy retrofits in Nova Scotia.
Rand is no stranger to retrofits; her firm undertakes 40 renovations each year; but none of them has as yet been an EnerPHit. Even if all of them were, that pace is far too relaxed to achieve the province’s GHG reduction goals, which, Rand says, rely in part on completing an estimated 40,000 deep energy retrofits by 2030—just ten short years from now. Rand and Rudnicki kick-started the ReCover Initiative in January of 2020, and by March they had raised funds—mostly from Nova Scotia’s Department of Energy and Mines—to cover the initial design work. Although most households in the province are single-family dwellings, they deemed it more efficient to first target a multiunit residential building (MURB), because these tend to have simple forms, and they are ubiquitous in the province’s urban areas.
“We have to get one built and publish our findings,” says Rand, outlining the initiative’s trajectory. “And then get other architects and builders on board.” She and Rudnicki are aiming for eight household retrofits in 2021 and increasing the pace of production from there. The fundamental goals for the retrofits include that they be replicable and scalable, that they disrupt the existing occupants’ lives as little as possible, and that locally sourced, low-embodied-carbon materials be used whenever possible. Rand and Rudnicki are targeting 1.0 ACH50 for the airtightness goal, a vast improvement over the average airtightness of the existing MURB stock, which is 8 ACH50.
In late spring the two found a MURB owner in Halifax who had been contemplating a mostly superficial refurbishment, but was excited to participate in the pilot test case. The brick-clad low-rise MURB currently has an annual energy use of 149 kilowatt-hours per square meter. The owner has set a project goal of achieving net zero energy for the building, with the aid of a 25-kW rooftop PV system.
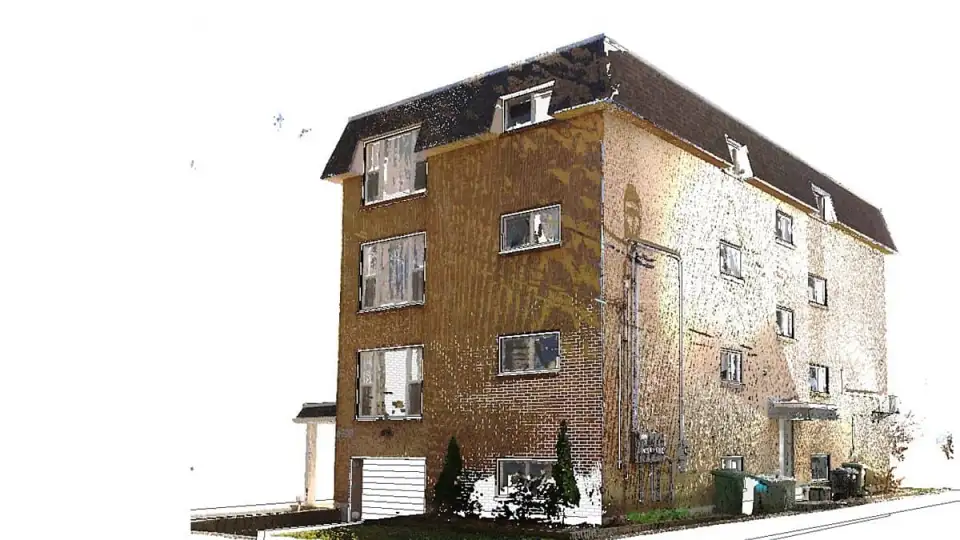
Rand, Rudnicki, and the ReCover design team contemplated various approaches to this first project, including employing prefab panelized components to envelope the existing façade, following in the footsteps of the innovative Energiesprong initiative first developed in the Netherlands. Using WUFI, Will Marshall, with Equilibrium Engineering, assessed the condensation risk associated with applying three types of panel to the façade: metal-clad panels insulated with mineral wool, panels insulated with EPS, and plywood box panels filled with cellulose. All three options would work, so they chose the cellulose one for its lower embodied energy. When they weren’t able to find panel manufacturers willing to meet their specifications, Rudnicki figured that his firm could construct them. He plans to start a panel-manufacturing company after the first pilot is finished.
A LIDAR scan of the existing building offered sufficient resolution to facilitate the production of CAD drawings needed for the panel fabrication. The panels will run the full height of the building, about 32 feet, and wherever possible they will be 8 feet wide to reduce waste. Laminated strand lumber (LSL) beams are integrated into the bottom of the panels, which rest on custom steel brackets that are attached to the foundation. On the exterior will be a water barrier membrane, a drainage plane, and metal siding for easy maintenance. The existing windows will be swapped out for PHIUS-certified units.
Heating in the existing building is supplied by hot water radiators fueled by an oil-fired boiler. Several mechanical-system upgrades were weighed. Given the humid summers in Halifax, ERVs were selected for ventilation, with individual units being installed in each of the four apartments. For supplemental heating and minimal cooling, a combination of mini-split heat pumps and an electric boiler to supply the existing radiators was chosen. Reusing the existing radiators will minimize tenant disruption.
“We are tiny, and our province’s carbon emissions are tiny globally,” Rand acknowledges, “but our entire agricultural industry is relying on dikes to keep the ocean back. Our food security, agricultural livelihoods, and countless homes are one bad storm away from devastating damage. So while we are not the worst polluters in the world, we are going to face the effects of carbon pollution sooner than many places will.” That nightmarish possibility is what drives Rand to do her part to fast-forward deep energy retrofits.
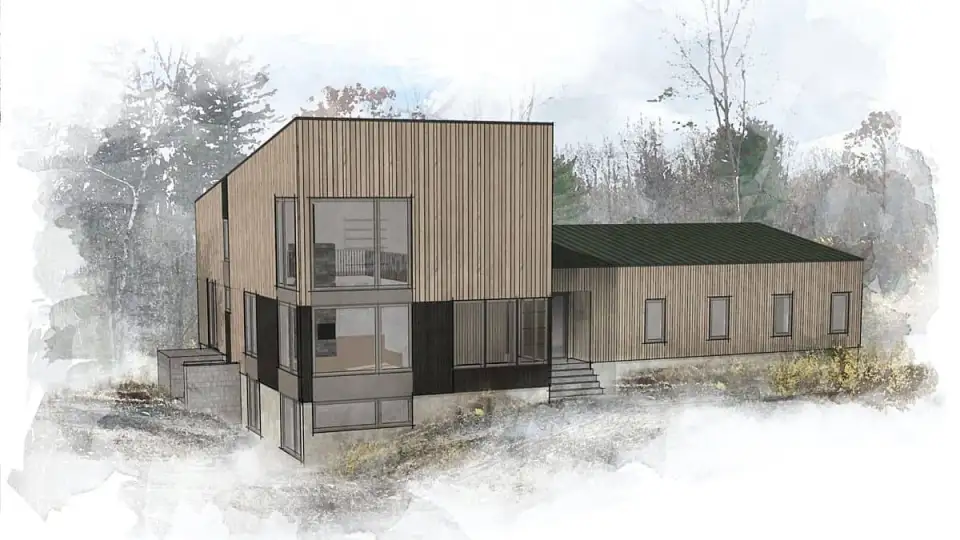
That scenario also prompts her to nudge all her clients—especially those with new-construction projects—toward more ambitious energy and emissions reductions goals. Rand has been a Certified Passive House designer since 2014, and has been modeling all of her projects using either the PHPP or WUFI since then, partly to ensure that every new build comes close to or meets the Passive House targets; she has set that as an in-house goal for all of her new construction projects. At first, meeting that goal was a challenge, but more recently her clients have been coming to Habit Studio partly for its efficiency expertise.
Such was the case for her recent clients, who wanted the best house they could get for their small farm in the Gaspereau Valley. The couple were definitely interested in efficiency, says Rand, but not militant about it. From the house site, the view toward the north overlooks an iconic piece of Nova Scotia landscape called Cape Blomidon, with a lovely meadow in the foreground. Capturing that view with large expanses of glazing was very important to them. Forest surrounds the home site on the other three sides, providing ample shading for the south-facing glazing. By playing around with the window dimensions and specifying very-high-performance units, among other measures, Habit Studio was able to get the home to meet the PHIUS targets.
Bentley Built Homes, which is constructing this home, will be using its typical double-stud wall assembly, packed with enough cellulose here to deliver wall R‑values of 50. The siding will be very locally sourced and milled—from just 5 kilometers away—for most of the building, with charred wood accents sourced from Ontario. The roof assembly will be filled with 24 inches of cellulose. The shed roof’s south-facing side will be covered in a PV system.
With the home’s mass stretched out into two wings, there will be two ERVs, one in each wing. Summers are hot and humid, so a mini-split heat pump that has one head in each wing will help with dehumidification and cooling or heating as needed. Although Habit Studio prioritizes building with locally manufactured products, the firm made an exception for this home’s supplemental heating system, because the clients really wanted a fireplace. The house’s main volume will feature a double-glazed high-efficiency, masonry-style heater from Europe. There will be a separate makeup air supply for the heater, which burns at a low heat for up to 24 hours before needing restocking. With a forest on three sides, the fuel for that heater is locally abundant.
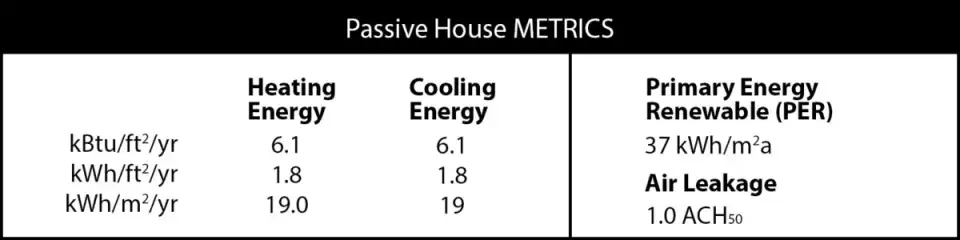
Read more in Passive House Buildings.
Rendering by Lorrie Rand