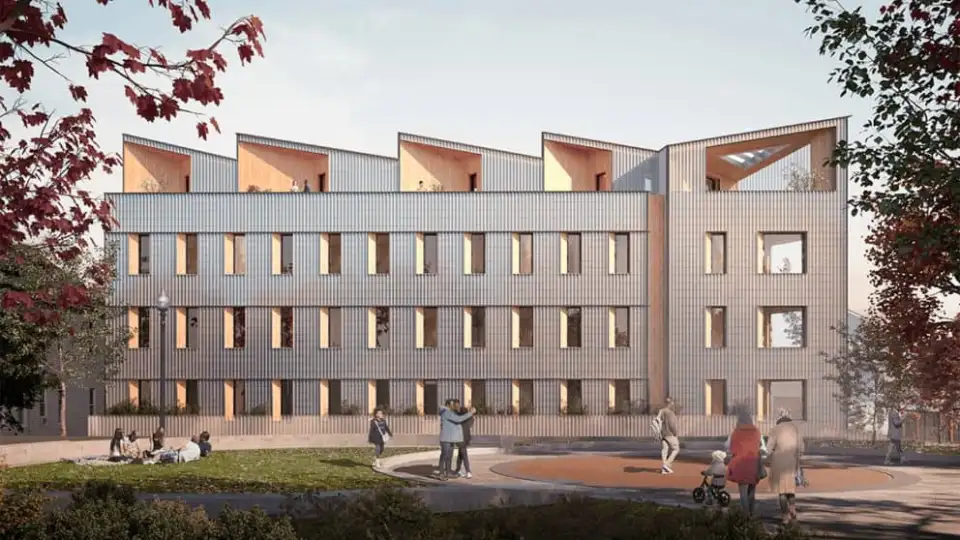
Placetailor, a design-build and development cooperative based in Boston, has been creating innovative passive housing projects since 2008. The group, which originally offered only design-build services, added development to its tool kit in 2010 to pursue the type of projects that were important to it. “There’s so much effort to convince clients to make the right decisions and to get a contractor on the same page who is knowledgeable and won’t upcharge for uncertainty,” says Colin Booth, director of strategy for Placetailor. The flexibility inherent in controlling all aspects of a project was critical to embarking on Model C, a five-story Passive House multifamily building constructed using cross-laminated timbers (CLTs).
Creating high-performance passive buildings that offer the occupants a healthy, carbon-neutral lifestyle has been Placetailor’s main imperative—and has proven to be a successful approach. “We recently looked at our historic sales data,” says Booth, “and for those projects sold at full market rate, we’ve been selling at 8% to 28% above market comparables.” Booth is quick to point out the boundaries of this data. Because Placetailor has a serious commitment to affordability, the group internally subsidizes most of its units. “We do not pursue top sales as the driver for development,” says Booth.
Since its inception, the cooperative has continuously worked to do more to address the climate crisis. Five years ago the group ramped up its carbon-cutting ambitions, setting a goal of shrinking both operational- and embodied-energy use. Modeling with a custom-crafted, life cycle emissions accounting tool led it to conclude that using wood products wherever possible was key to shrinking a building’s overall emissions. “We’ve had our eye on CLT for a long time,” notes Booth. But just using CLTs wasn’t sufficient for Placetailor’s aspirations. The cooperative had a vision of creating a replicable model of a low-carbon “CLT cellular” system that achieved Passive House levels of performance.
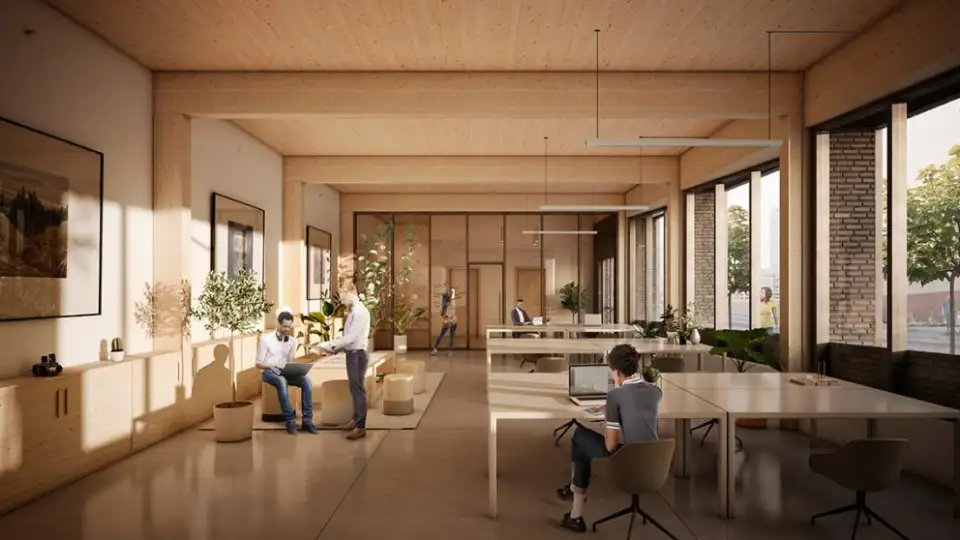
Finally, the time was right. Just as Placetailor was forming the initial designs for a plot of land it owned in Roxbury, the group met with John Klein, then a principal investigator at the Massachusetts Institute of Technology and now the CEO of Generate Architecture and Technologies. Klein and the Generate team have developed a catalog of mass timber building solutions to pave the way toward the rapid deployment of mass timber systems. Calculating life cycle carbon emissions for the Model C project, Klein and his team found that using mass timber and a kit-of-parts approach that they had developed would reduce total embodied carbon emissions to less than half the emissions of a comparable building made with conventional steel or concrete.
To provide for families of various sizes, the 14-unit Model C will include a mix of housing types, from studios to three-bedroom apartments. The ground floor will contain a pilot project for affordable commercial space, intended as an incubator for local businesses. Its urban location and proximity to public transportation meant that Placetailor didn’t have to provide on-site parking.
“The foundation has concrete in it,” says Booth, “and everything else is CLT panels.” Model C is a full CLT cellular system, where the floor, interior partitions, exterior walls, and roof assemblies are all CLT panels of varying thicknesses. These panels provide structural strength through continuous attachment of the panel edges, similar in concept to building cabinets with plywood. The exterior assembly is to be insulated on the interior with high-density cellulose, and on the exterior with wood-fiber board. The sawtooth roofline is also CLT, oriented due south for optimal solar PV orientation.
Placetailor considered sourcing the CLT panels from a European manufacturer that had extensive experience with this technology. However, it found a closer source just over the Canadian border in Montreal. Another panel manufacturer—Bensonwood, based in Keene, New Hampshire—will trim the panels to fit and will oversee their installation on-site. Bathrooms will be self-contained pods.
Mechanical ventilation will be supplied by a semicentralized system, with one ERV unit per floor shared among four housing units. A heat pump will provide the cooling, but not the heating, to prevent the condenser from overcycling while meeting the minimal heat load and burning out. Instead, the small amount of heat needed will be delivered by a simple and cost-effective electric-baseboard system.
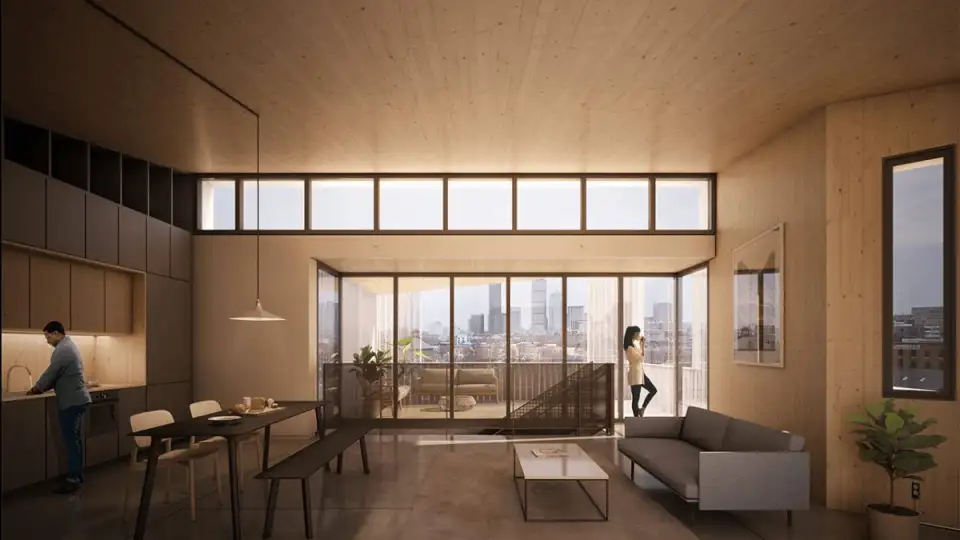
A gas-fueled combined heat and power (CHP) plant will be the building’s source of domestic hot water and some electricity, the first fossil fuel combustion in a Placetailor project in recent memory. Placetailor’s calculations show that overall greenhouse gas emissions will be lower with the CHP system than would have been the case if a heat pump water heater had been used, because of how electricity is generated locally. The group is working into the design a straightforward way to transition to heat pump systems as soon as the grid is cleaned up.
The building will be finished with a corrugated-metal siding with a rain screen air gap behind it. The metal panel will be perforated to afford selected views into the building so the exposed wood panels can be viewed from the outside, especially by pedestrians passing at night.
Placetailor is committed to smoothing the path for other developers of small- to medium-scale multifamily projects to use CLTs. To that end, Placetailor is working with Bensonwood to create a standardized kit of parts using Bensonwood’s PHlex system—preinsulated and airtight panels that come with windows installed and are designed to achieve Passive House performance. “If we, and other builders, are using the same set of panels, then their price comes down,” Booth points out. “Bensonwood has become a strategic partner of ours.”
In further efforts to move multifamily new construction toward carbon neutrality, Placetailor recently collaborated on a Guidebook for Zero Emission Buildings with the city of Boston (available at boston.gov). The guidebook—intended as a resource for developers, designers, and builders—lays out affordable-housing requirements for high-performance assemblies for various building typologies. In researching these recommendations, the team concluded that particular attention to windows, window-to-wall ratio, and airtightness did the most to improve building performance.
The team also analyzed cost data from net zero energy and Passive House buildings in Boston and concluded that construction cost increases were at most 2.5% before rebates and incentives. After accounting for currently available rebates and incentives, the team found that zero-emissions buildings could actually be less expensive to build, while still furnishing long-term operational savings. In other words, as Placetailor has been demonstrating for more than a decade, there’s no reason not to set zero emissions as a project target.
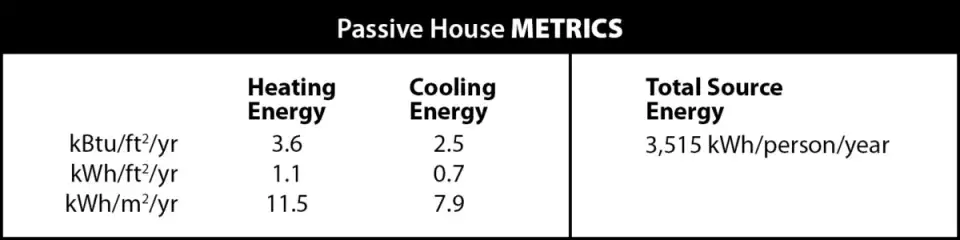