The city of Troy was the crown jewel of upstate New York at the turn of twentieth century. On account of being one of the earliest manufacturing hubs during the American Industrial Revolution, Troy became one of the wealthiest cities in United States. With great wealth came great architecture, and the nineteenth and early twentieth centuries saw the erection of a myriad of stately buildings along the city’s primary commercial arteries, while residential streets became home to a combination of rowhouses and townhomes—with the occasional Gilded Age mansion thrown in for good measure.
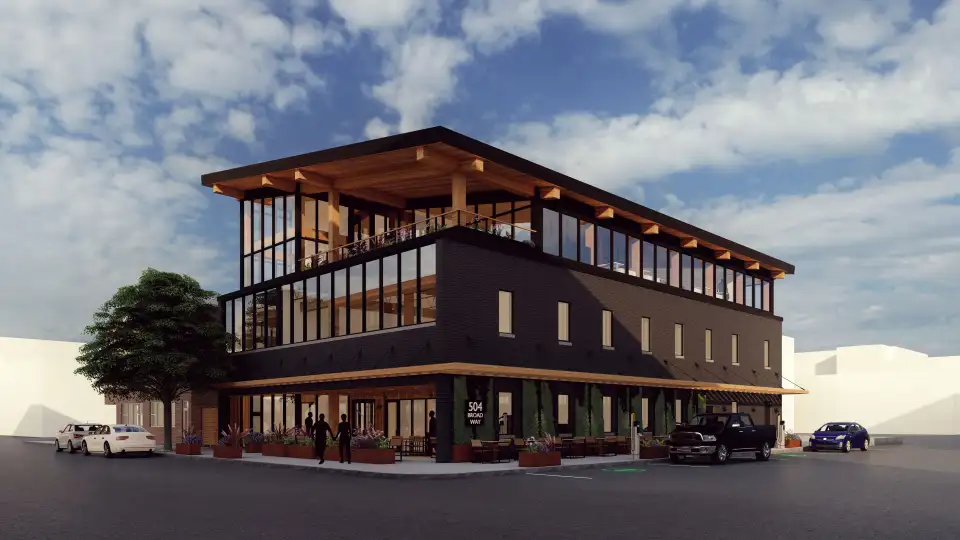
Net-Zero Retrofit to Rise in Troy
The good times did not last. Like much of the Hudson Valley, Troy experienced an era of significant population decline and economic stagnation during the latter decades of the twentieth century, but many of the grand buildings that were erected during the city’s auspicious rise were preserved. Today, its multiple historic districts are helping not only to protect the city’s history, they are also serving as magnets for new businesses, as well as residents seeking to establish—or in some cases reestablish—roots in the community.
This process of revitalization and repopulation accelerated during the first year of the COVID-19 pandemic as people fled from cities like Boston and New York. While the influx of new citizens may have slowed since then, the city of Troy, as well as other upstate communities, are continuing to thrive.
Businesses in the area are thriving too, including Phinney Design Group. Founding Principal Michael Phinney has long been a staple within the upstate sustainable design community and was even on the team (while at WCGS Architects) that designed the first LEED certified building in the state—the headquarters for the Department of Environmental Conservation in Albany, completed in 2001. Phinney has continued to champion both sustainable and biophilic design since beginning Phinney Design Group in 2003, saying that the firm “is founded on trying to minimize our impact on the environment through what we do in the built environment.”
For Phinney, the last four years have been some of the busiest in the company’s 21-year history. It has grown to 40 employees and now operates out of offices in New York City, Lake Placid, Saratoga Springs, and Troy. Given the need to expand its operations specifically in Troy, Phinney purchased a building located at 504 Broadway with plans to convert it into an office for the firm. After receiving funding assistance from the Empire State Development and the New York State Energy Research & Development Authority through the Building Cleaner Communities Competition (formerly known as the Carbon Neutral Community Economic Development program), Phinney is now planning an extensive, net-zero certified retrofit with construction commencing this fall. The project will see the addition of a third floor to the building with approximately 5,000 square feet of space, as well as an elevator.
Once complete, the mixed-use building will house 10,000 square feet of space on the top two floors for the firm, while the 5,000-square-foot ground floor will consist of a lobby area and a bistro with seating for approximately 100 people inside and another 50 seats outside.
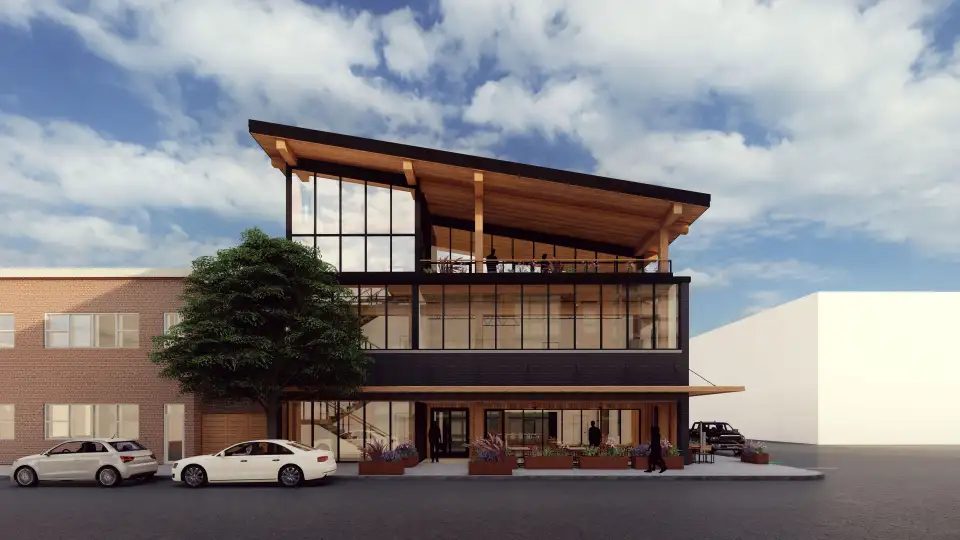
Building on a Solid Foundation
Located on the perimeter of one of Troy’s historic districts at the corner of Broadway and Union Street, 504 Broadway is a boxy, brick office building that was originally constructed in the middle of the twentieth century. Currently, it stands at two stories with no basement and is defined by extensive glazing on its south-facing (and Broadway-facing) façade, while the other three sides are articulated by evenly spaced punch windows. The building was recently vacated by Unity House, a non-for-profit that provides social services to the people of Troy. Like Phinney Design Group, they have experienced significant growth in recent years and needed more space.
Given its location within a historic district and Phinney’s dedication to sustainability, a retrofit of 504 Broadway is only natural. It certainly helps that its brick façade, foundation, and steel support structure are all still in good condition. Still, significant upgrades will need to happen to the building’s envelope systems to give them the performance boost they need.
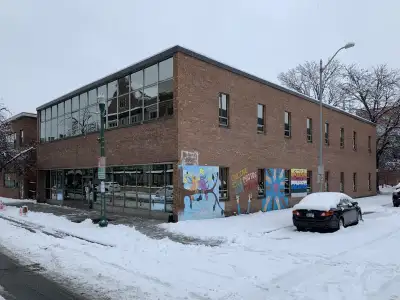
For the foundation, Phinney plans to seal the concrete slab floor with a vapor retardant. He then will likely install a layer of rigid insulation before capping it with a new flooring system. For the walls, Phinney plans to keep a one-inch air gap between the brick veneer and the existing substrate, and then will spray the entire cavity with a soy-based spray foam manufactured by Demilec that serves as vapor barrier and air barrier all in one. The northern wall will be filled with eight inches of the soy-based foam, giving the assembly an R-value of 42. The R-values on the remaining walls will be slightly lower.
Unfortunately, many of the other parts of the building envelope were not fit for reuse, as Phinney has found asbestos everywhere—in the walls, in the floors, in the ceilings, in the window frames. “We basically have to strip the whole building down to its structural core and get it fully cleaned, and then we’ll start from there,” Phinney says.
Not everything will be removed solely because of asbestos. Phinney has also decided to remove much of the existing roof system to make way for a third floor. He plans to leave the open web steel joists of the existing roof in place, and then install new cross-laminated timber (CLT) panels directly on top to serve as the floor of the third story and ceiling of the second. “From the second floor looking up, you'll see the new wood panel finish,” Phinney says. “It will appear that they're being supported by the open web steel joints.”
A CLT panel system will also be used for the walls and ceiling of the third floor, which will sit comfortably on the existing structure and be supported by vertical timber elements. The third floor is where the new offices for Phinney Design Group will be housed. Though Phinney is still shopping around for a manufacturer of these prefabricated panels, he has narrowed the list to a few companies located in the Northeast or Ontario. The third floor will be topped by a slanted roof equipped with a PV system that will range from 50-65 kW.
The addition of the PV system is part of the plan to make the building all-electric. Electrification will also see the removal of an oil-burning furnace on the first floor that Phinney describes as being “the size of an 18-wheeler” that was installed long ago to deal with Troy’s formidable winters. In its place, the building will be outfitted with a geothermal heat pump system. Phinney has had a good experience using these systems for single-family homes in the Adirondacks, and notes that they perform very well in upstate New York. “As far as the heating goes, you're starting with 55°F degrees trying to get it up to 70°F, so it's a lot less energy you're using,” he explains.
The cooling is a little bit more complicated. “You’re getting free cooling to a large degree because you're not using any electrical condensers or refrigerants—you're using the earth,” he says. “That will work typically really well until you get into the mid to high nineties, multiple days in a row.” Though these kinds of heat waves are uncommon in Troy, they do happen. Like much of upstate New York, Troy is notorious for its winters, which can see temperatures plunge to -30°F with 10% humidity, but summers can occasionally get to 105°F with close to 100% humidity. Given such an enormous range in design temperature, Phinney has accepted that there may be summer days where the comfort level in parts of the building falls short of optimal, though he anticipates that the use of passive cooling techniques will prevent serious overheating.
Although the building is not pursuing Passive House certification, Phinney does plan to use triple-pane windows throughout the building and to employ passive cooling strategies, particularly for the ground floor. “We're doing a translucent canopy all along the western face and southern face that will not only protect outdoor diners from rain, but it also kind of prevents the summer sun from overheating the first-floor space,” he says. The panels will be timber-framed.
As Phinney has learned from designing other all-electric commercial kitchens, including the Coat Room in Saratoga Springs, induction stoves may generate far less heat than conventional ranges, but it still gets hot in the kitchen. Phinney has found that the addition of a few ductless splits for supplemental cooling solely in the kitchen can resolve the issue without requiring a reconceptualization of the building’s mechanical systems.
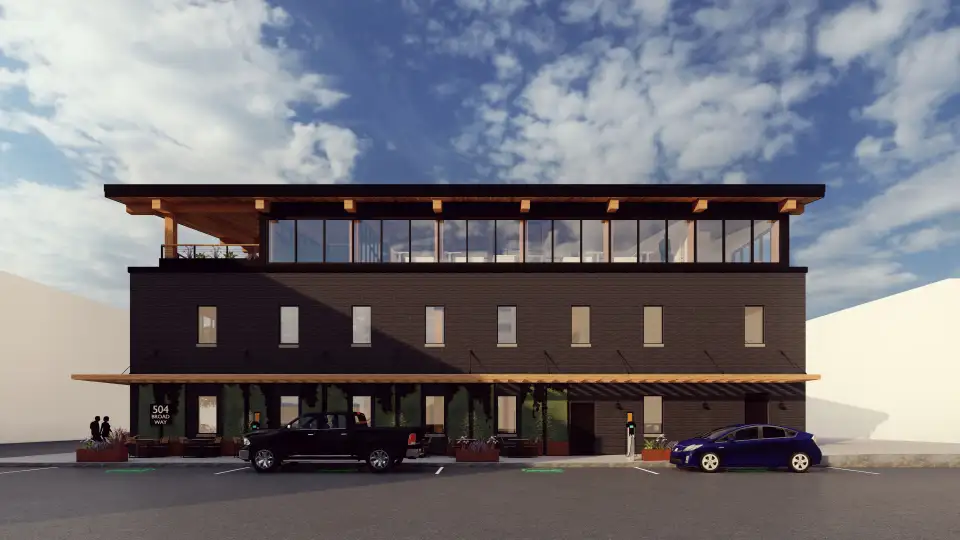
Building Equity and Community
There are several benefits that come along with building your own office, Phinney notes. First and foremost, it allows the firm to build equity and it more firmly ties them into the fabric of the community. Another reason that is fairly innovative from a business standpoint is that it allows the firm to flex their interior design skills.
The firm’s furniture procurement program has grown in recent years, and Phinney wants to use the restaurant to serve as an active showroom for furniture lines, as well as a design center. The model is similar to Restoration Hardware in the sense that shoppers can casually peruse the showroom with a glass of wine or a coffee. It can also serve as a meeting place for members of the Phinney team to show clients individual pieces of furniture or for anyone in the area who just wants to grab a bite to eat.
More extensive interior design opportunities will exist on the second floor, where there will be additional showroom spaces, as well as five or six short-term apartments. “We'll furnish them and rent them nightly or weekly, probably to a lot of people we know that are coming and going and clients that are coming to visit us. But it'll also be an opportunity for us to showcase our design skills and also our furniture.”
Phinney notes that the project would not have been so extensive without the assistance from NYSERDA and the ESD. Specifically, the addition of the third floor and the CLT panels would not have been feasible, meaning that the second floor would have been reserved for the new office space and that the showroom and apartments would have been scrapped. “It would have been a much more modest project and wouldn’t have created the number of jobs we’re going to create either,” he says.
Phinney believes that more retrofit projects are on the horizon, especially with more local and state support. “One of the biggest and best things you can do, considering where we are right now, is to promote development in existing urban cores where there's existing infrastructure, existing public transportation, existing facilities,” he says. Beyond bringing new life into the community, high-performance retrofits, combined with new PV generation, like the one at 504 Broadway mean more buildings that generate as much, if not more, energy than they consume, keeping useful materials out of the waste stream, and reducing the need to manufacture carbon-intensive materials like steel and concrete. When a significant percentage of an existing building’s materials can be salvaged, it can also result in lower costs for developers, since less needs to be purchased, transported, and installed.
Given all these benefits, Phinney says, “I think you're going to see a lot more of this happening.”