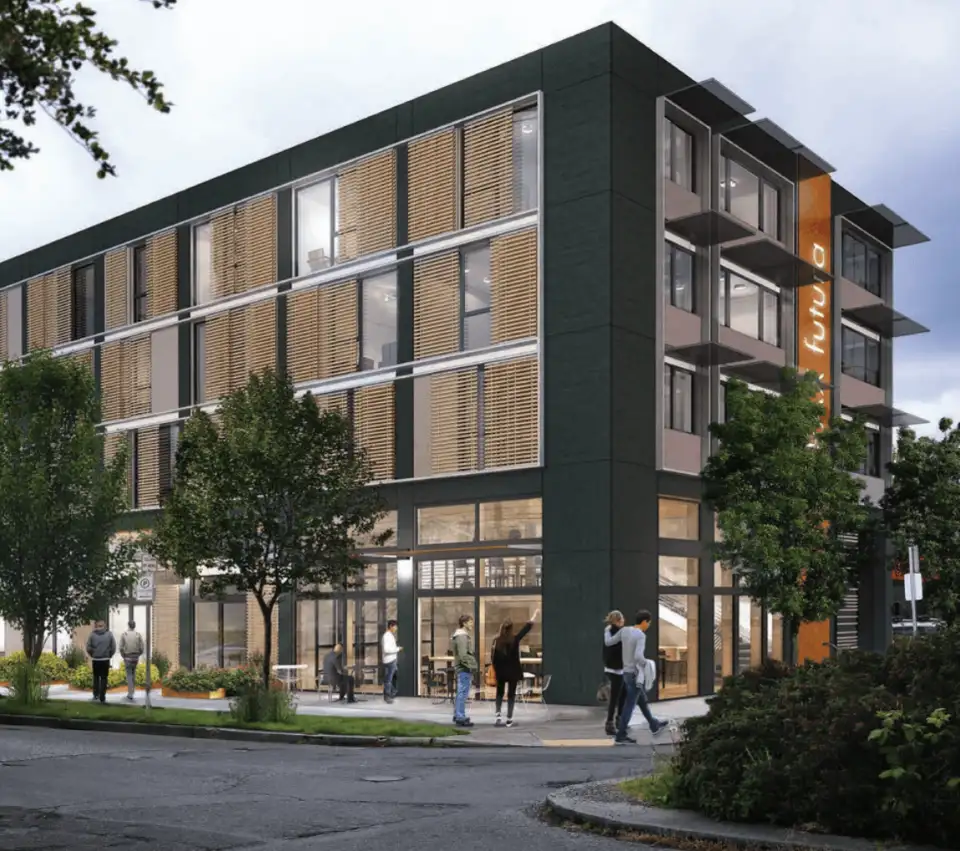
In a bustling neighborhood south of downtown Seattle, a 35-unit multifamily Passive House building is under construction. It’s the brainchild of Sloan Ritchie, president of Cascade Built, and developer, builder, and owner of Pax Futura. Although Cascade Built has had plenty of Passive House experience, this project is Ritchie’s first Passive House apartment building, and is also a first for Seattle.
“It’s new territory,” Ritchie says succinctly. He is referring to the design of the project’s cooling system, but the same can be said about other aspects of this ambitiously forward-looking development.
Filling a pressing need for new rental housing, the four-story building will offer 6 one-bedroom units, 26 studios, and 3 live/work spaces on the ground floor. Located close to a light-rail station and numerous retail establishments, the 50-foot by 100-foot site has a walk score of 94. In keeping with Seattle code allowing developers to eschew parking garages in specified dense neighborhoods, Ritchie opted for bike parking instead of a garage that only would have been able to accommodate six cars—an economically unsound choice and a waste of valuable living space, he points out. By limiting the building height to four stories he also was able to forego building an elevator, eliminating a potential primary energy hit.
With Passive House the goal from the outset, designing the building envelope was pretty straightforward, says Brittany Porter, architect and certified Passive House consultant with NK Architects, the project’s designer. “This project validated what we already knew about the compatibility between multifamily and Passive House,” says Porter. Careful detailing and modeling are critical to any project’s success, no matter the scale, she emphasizes, but multifamily buildings come with inherent advantages.
The foundation assembly is a fairly standard slab-ongrade with 4 inches of rigid insulation and a vapor barrier below the slab. The R-68 roof assembly includes more insulation than is typical but not by a huge amount. The exterior roof insulation consists of tapered polyiso—up to 1 foot thick in some locations. Interior to that is the air barrier and sheathing, supported by 9½-inch I-joists insulated with fiberglass batts.
A primary question was how to get enough R-value in the walls yet not take up too much space on a small lot. The answer relied heavily on a structural insulated panel wall that uses a graphite-enhanced EPS to deliver a roughly 15%–20% higher R-value. The taped panels will serve as the air barrier. “It’s a typical 6-inch wall, but it’s significantly more thermally efficient,” says Porter.
Thanks partly to this thermal efficiency and partly to the high occupancy per square foot, the building easily meets the Passive House heating target using double-pane windows. Seven household-sized HRVs, each one serving three to five dwelling units, will supply continuous fresh air. Thanks to this semidecentralized system, duct runs were minimized, sharply reducing typical efficiency losses. When needed, electric-resistance cove heaters, mounted on the ceiling, will provide supplemental heating.
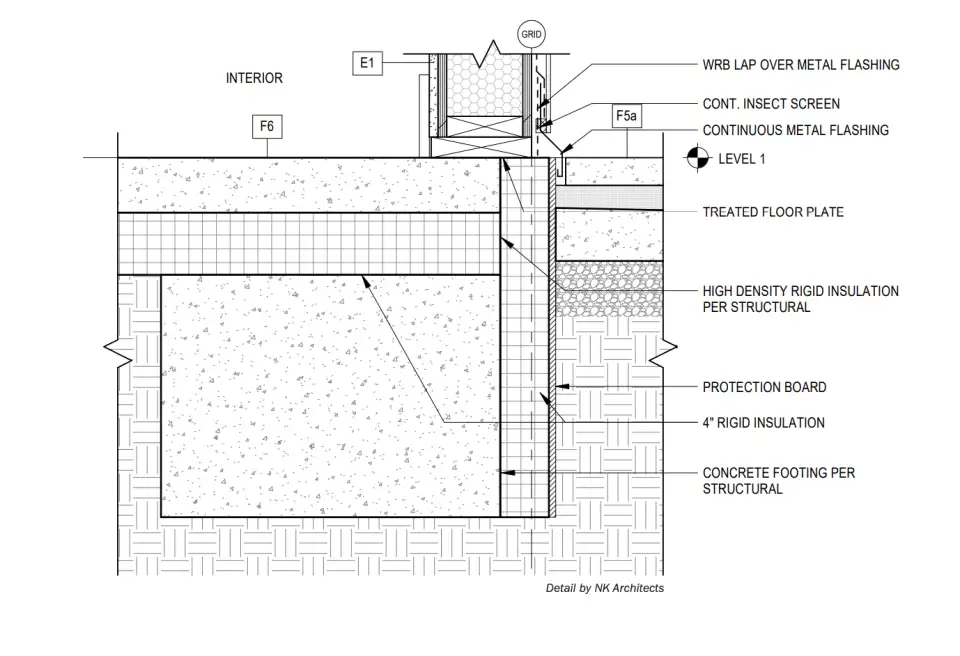
Cooling is a little more complicated. Most of the units in this C-shaped building face west and feature 7-foot tiltand-turn windows on this facade. To shade each of them, Ritchie opted to install two cedar-slatted sliding screens, one 3 feet and one 4 feet long. The tenants can pull one or both across a window and even double them up across a portion of the window if desired. “In our climate people are used to opening and closing windows and shades,” says Porter. For this neighborhood and the likely demographic, she adds, it’s not a stretch to assume that the occupants will be willing to engage in maintaining their indoor comfort.
Although Seattle is far from being a coolingdominated climate, the climate is changing, says Ritchie, and summertime temperatures in the 90s are becoming more common. Still, most summer days are pleasantly temperate, and air-conditioned housing is a rarity. To take the edge off on hot days, Ritchie has chosen to use a centralized heat pump and send its refrigerant through each of the seven HRVs, cooling the supply air when the outdoor temperature rises above a designated setpoint. It’s a novel, energy-efficient means of providing a tempered indoor climate.
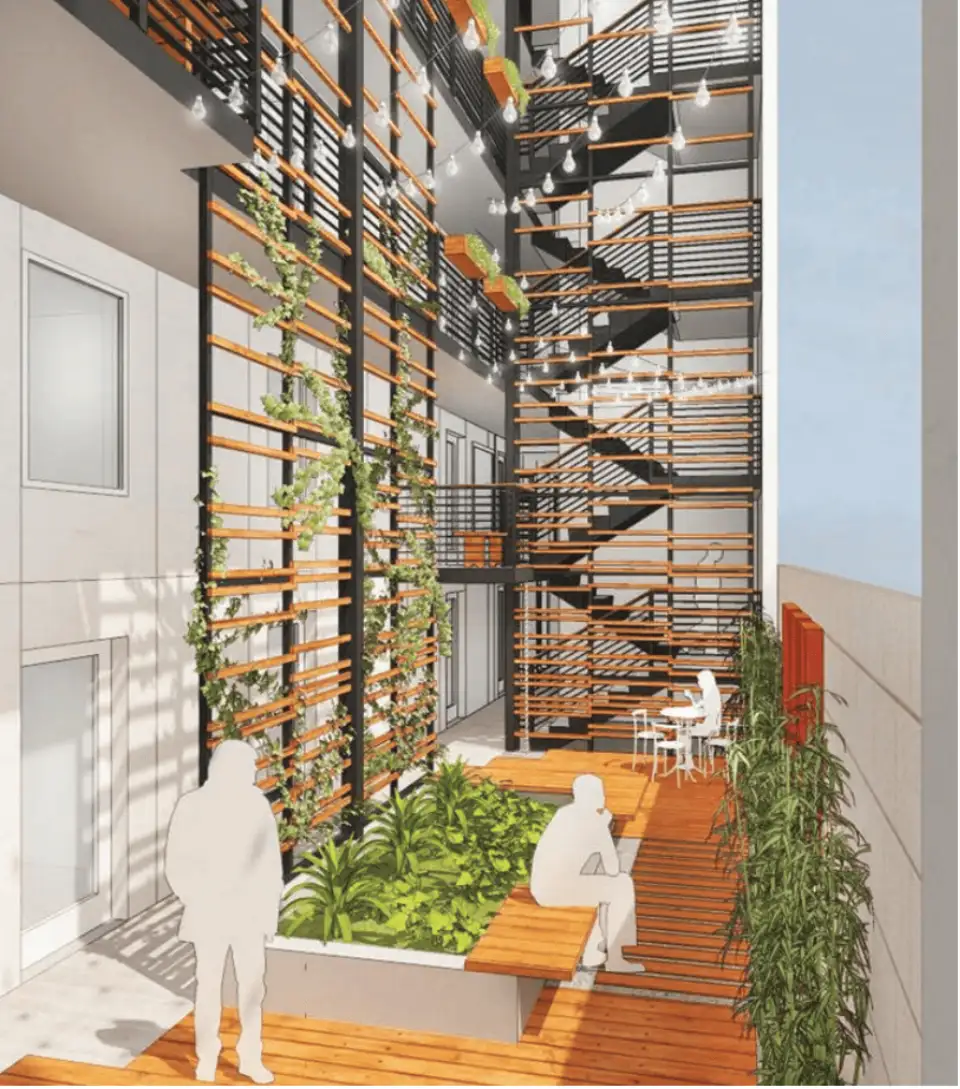
With the heating and cooling load minimized, domestic hot water is typically the largest load left in a multifamily building. “If we can reduce that load, it will be a benefit to us and the larger community,” Ritchie says. Meeting a high bar for environmental benefits, the water heating system relies on a renewable technology that some have characterized as down for the count—a roof-mounted solar-thermal system. This solar-thermal system, designed by a local company, has been optimized to perform well even in Seattle’s typically cloudy weather. Ritchie is excited to be trying it out.
And the final mountain to scale? Plug loads, says Porter. That’s the biggest unpredictable load, but with 35 small units, the plug load density is expected to be high. To reduce this load a bit, individual washers and dryers are not included in the units. Instead, shared laundry facilities on two floors are available in semiconditioned spaces that are outside of the thermal envelope.
Offsetting the building’s electrical use will be a roofmounted PV system. The likely tenants of this Passive House building hopefully will be excited about its many efficiency features and will act strategically to maximize the impact of this renewable resource—carrying the building ever closer to net zero energy and carbon emissions on an annual basis.
Heating energy |
Cooling energy |
Total source energy |
Air leakage |
---|---|---|---|
2.4 kBtu/ft2/yr |
1.0 |
54.0 |
0.6 ACH50 (design) |
0.7 kWh/ft2/yr |
0.3 |
15.8 |
|
7.6 kWh/m2a |
3.0 |
170.0 |