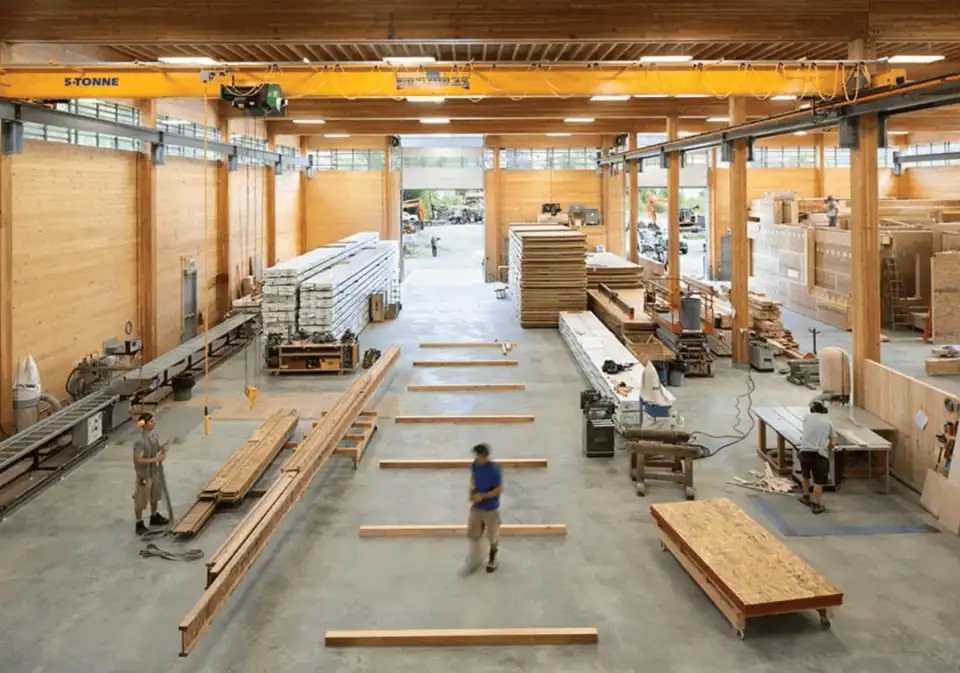
With demand for Passive House-quality panels and modules on the rise, the factories producing these goods are expanding in number, capacity, and production. Most are new businesses producing Passive House-performance exterior wall, floor, and roof panels. Yet a strong contingent of existing businesses are also growing their product lines to include higher-performance, thermal-bridge-free Passive House options.
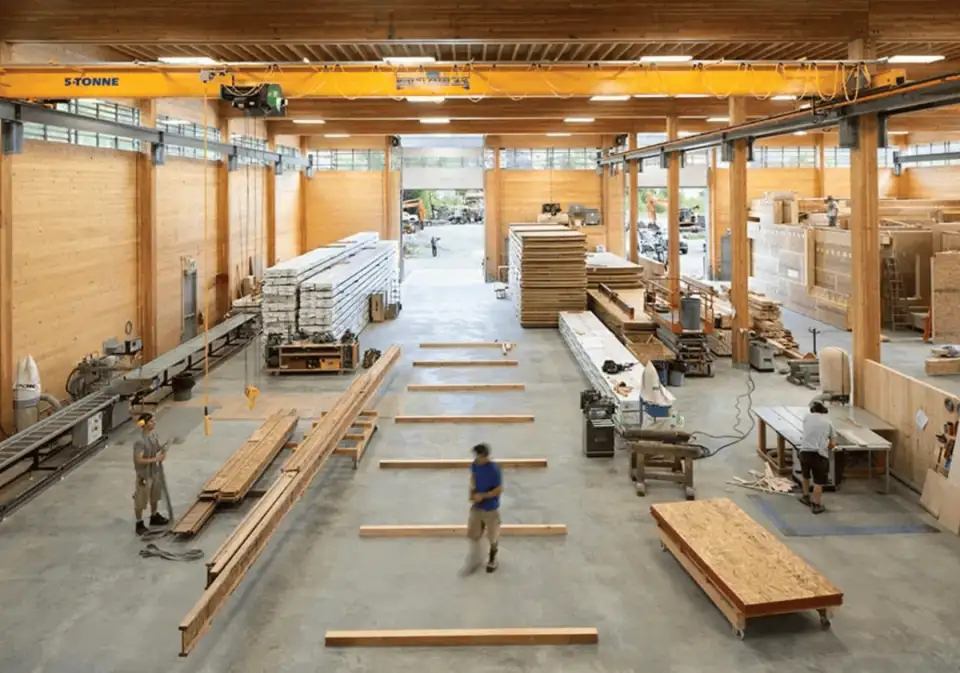
British Columbia and New England remain the anchor regions in the growing community of Passive House factories. (See “Factory Builds Surging,” in Passive House Buildings: North American Highlights, p. 51, for a previous overview of Passive House factory businesses.) While most still are in Canada, these factories—producing panels or modules—are becoming more geographically dispersed (see Panels or Modules?).
A standout in eastern Canada, Maisons Eléménts in Quebec, focuses on Passive House performance with walls whose R-values range from R-40 to R-60. The firm has been in business since 2013; 2018 marks its first year of exporting walls for a U.S. building. Producing four to eight buildings per year, the firm builds I-joist walls densely packed with cellulose under a fiberboard external sheathing.
Quebec is also home to ConceptMAT, which has produced walls offsite since 1993 and features a vapor-diffusing, open-cell polyurethane stud wall with continuously insulating expanded polystyrene sheathing under strapping.
On Canada’s west coast, Passive House factories are humming. New in 2018, Adaptive Homes joins Tree Construction in Revelstoke, British Columbia, in producing high-performance envelopes in a factory setting. In fact, owner Jocoah Sorensen worked at Tree for six years before launching Adaptive. Sorensen is just now producing his first building, a duplex, and he hopes that factory construction will help him meet the affordable housing crisis in Revelstoke. Sorenson’s hybrid modular development model consists of modular construction augmented with panels to connect modules. Like many other factory builders, Sorensen favors wood fiberboard exteriors.
Also launching in 2018, Simple Life Homes joins Quantum Passive House and Green Giant Design/Build in Ontario. Simple Life Homes owner Jeremy Clarke explains that he started as a general contractor, building sustainable buildings with a focus on natural materials. He became increasingly interested in such building science topics as indoor air quality and heat and moisture recovery ventilation, eventually taking a Passive House Canada training, and now has left general contracting to focus his energy on supplying Passive House panels to general contractors. Simple Life combines a stud wall with exterior insulated I-joist, but instead of using OSB between them, Clarke sandwiches fiberboard produced in Canada for a vapor-open assembly.
2018 was a growth year for earlier entrants to this growing field. Abby Xerri, at neighboring Quantum Passive House, says that Quantum is “crazy busy in a wonderful way.” The growing demand has spurred the company to conduct a hiring spree to bring its own employee count to over 20 and to shift its business model. Rather than mainly delivering turnkey homes—which the firm will still do if required—it is now focusing on creating the superstructures while supporting its general-contractor partners by training their crews to do the installations.
Quantum expected to complete 11 homes in 2018 and is looking at finishing 30 to 45 buildings in 2019. Although most of them are homes, Quantum is supplying for other structure types as well, which is driving innovation. For example, larger panels—such as those required for a 27- to 30-foot wall—must be rigid enough to withstand the stress from lifting, so Quantum has developed systems to stiffen its panels without thermal bridges.
Adam Cronk, at Green Giant, completed a few homes in 2018, but a local labor shortage forces him to turn down projects. Cronk will continue to hone his business toward standardized panels that general contractors can order from a catalog. Although architectural complexity is possible, it is incompatible with his business plan to mass produce affordable Passive Houses. Cronk is currently completing a Passive House that is on track for building certification, and he hopes to eventually obtain PHI Component certification for his building system.
Another well-established business, BC Passive House, reports that virtually all of its customers want Passive House-inspired, performance exceeding code, with roughly 10% specifically asking for Passive House. Like that of BuildSMART in the midwestern United States, much of its production—at least half—is for larger commercial buildings.
Factor Building Panels, located nearby in Squamish, has a goal that many factory businesses echo: producing a high volume of high-performance panels for general contractors throughout the region. Although it occasionally serves as the general contractor, Factor prefers to supply instead. Factor’s basic wall combines stud framing from 2 x 6 to 2 x 12, with a wood fiber insulation on the outside of the structural plywood sheathing. It is considering adding wood fiber insulation up to 16 inches thick for roof panels.
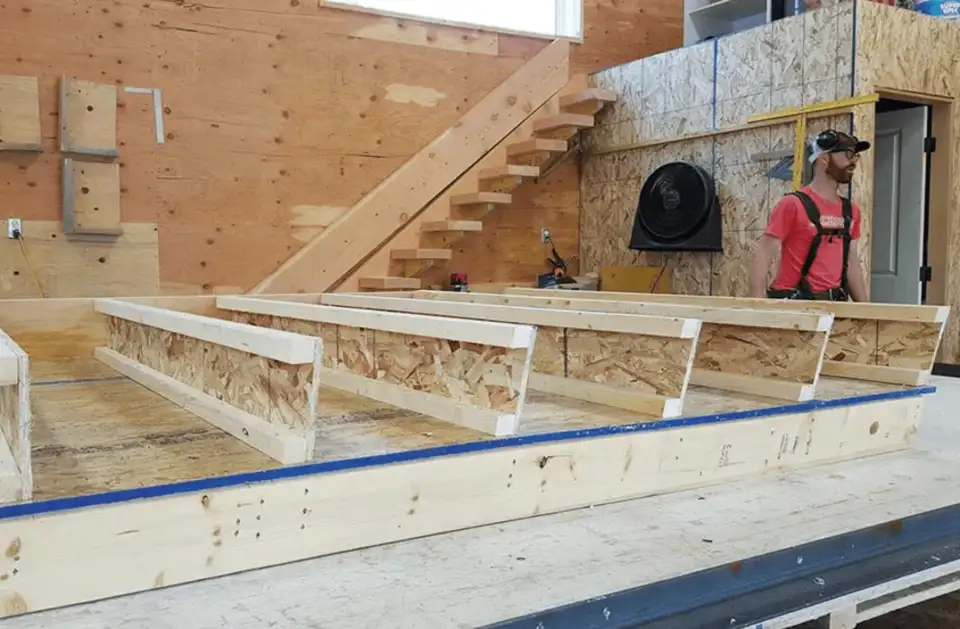
Collective Carpentry, located inland in Invermere, continues to increase annual production, and in 2018 started for the first time to export panels to U.S. customers. Another promising development: Its average shipping distance is decreasing as it wins more local business—meaning business within 300 kilometers (186 miles). This company’s goal is high-volume repeat business from general contractors within a short distance, where lower shipping cost makes its panels an even better value.
Meanwhile, Ecocor in Searsmont, Maine and G.O. Home by G.O. Logic in nearby Belfast are examples of how New England leads U.S. Passive House factory production. In 2018, pioneering Ecocor owner Chris Corson enlarged his factory to meet increased demand. The firm can ship high-performance building shells to just about any site in North America and also offers predesigned homes, as well as custom design-build services.
G.O. Homes developed out of G.O. Logic’s successful design-build business. Although the firm will still produce a turnkey custom home, it will not construct the envelope on-site. Those days are over. Every one of its homes now starts in the factory. As principal Alan Gibson wryly observed, “We’ve been building homes the same way for 600 years. It’s a medieval method, and we didn’t make the leap into the factory like so many other products.” Now he has!
Making its own panels has allowed G.O. Homes to leave foam behind. While the firm’s crews typically used to install structural insulated panels (SIPs) over a stud wall, making their own panels has allowed them to shift to rigid mineral wool panels, typically 6 inches thick, over stud walls.
G.O. Homes has built a fantastic website showing its standard model homes as well as the exterior and interior finish, lighting, appliances, and mechanical equipment options it offers customers. While the firm’s standard models are beautifully simple, G.O. Homes will produce panels for all kinds of designs, for outside architects as well as for its own custom design clients. Gibson says the firm is also looking forward to establishing ongoing business with general contractors who can simplify their own businesses while attaining higher volume by leaving the envelope to experts in a factory.
2018 will also be remembered as the year that Bensonwood put systems in place to propel Passive House from niche to mainstream. First of all, Bensonwood, differentiated into three distinct product lines to distinguish its custom timber frame homes from its Unity Homes (a catalog of customizable factory-built homes uniformly superior to code) and Tektoniks line (Passive House superinsulated envelope panels from R-21 to R-53). Within the Tektoniks brand, Bensonwood offers its PHlexTM – flexible Passive House approach – panels. PHlexTM still takes advantage of Bensonwood’s efficient factory manufacturing, because these panels begin with standard designs while allowing for changes in insulation material and thickness for desired thermal resistance.
Sara Kossayda of Bensonwood reports that this is a response to market demand. Bensonwood is seeing steady growth in the customers who ask about Passive House. Although these inquiries are still only about 10% of its overall requests, Bensonwood is banking on these increasing with Tektoniks. Bensonwood’s extensive online Tektonik product guide is a wonderfully clear catalog showing exactly what you get in a Tektonik wall or roof panel. And like other high-performance factories, Bensonwood offers a wood-based system featuring cellulose and wood fiber insulation.
In addition, Bensonwood has completed construction of its new 100,000-ft2 production facility in Keene, New Hampshire, where it can eventually produce homes in three shifts per day. And though 95% of Bensonwood’s sales are within New England, it ships throughout the United States and Canada. In short, Bensonwood is poised for Passive House growth.
In New York, New Energy Works, another experienced timber framing company, is expanding and diversifying their 30-year business with the twin benefits of computerized design and CNC (computer numerical control) precision cutting machinery that timber frame companies bring to panelized construction. Currently producing panels for 10 to 15 buildings per year, Eric Fraser promises, “Our focus in 2019 is to push this to the next level.” Fraser’s most popular panel is a 2 x 8 stud wall with 2 3/8-inch exterior wood fiber insulation, but New Energy Works plans its next iteration will be to a more complete system, likely with more insulation and windows installed in the factory. New Energy Works operates on both coasts with production in Oregon as well.
Architects and factories work differently. And often speak different languages. Even the software typically used by these parties tends to differ. This inspired a novel factory business model debuted in 2018 by Holzraum (“wood room”), which was cofounded by Passive House architect Ilka Cassidy and factory computerized design and timber frame construction expert Steve Hessler. Holzraum will translate North American Passive House architects’ designs to computerized plans and instructions that high-volume factories rely on for return on their tremendous investment in sophisticated, automated machinery. Holzraum is the communication hub, integrating all of the design, engineering, factory production, and assembly teams. Cassidy and Hessler aim to prevent miscommunication and exploit each team members’ capabilities.
Cassidy and Hessler are currently working on a few Passive Houses with Blueprint Robotics, one of the largest building component factories in North America with advanced CNC cutting machines and automated fabrication equipment; however, Holzraum envisions working not only with multiple designers, but also with multiple factories.
Although many of these developments are taking place in the eastern half of the United States, in the Midwest BuildSMART continues to build market share, especially in affordable multifamily Passive House development. And it continues its innovation with a proprietary superinsulated slab floor system. In 2018, farther west in Grand Junction, Colorado, Phoenix Passivhaus became the third North American building system to earn PHI’s Building System Component certification.
A host of other modular plants have recently introduced Passive House-performance options. Among the modular choices actively marketing to Passive House developers are Metric Modular, in British Columbia, which branched out from its parent BRITCO; BrightBuilt Homes, in Maine; Preferred Building Systems, in New Hampshire; and Beracah Homes, in Delaware, which is currently in planning for multiple Passive row house projects in the Washington, D.C., region for Flywheel Development.
SIP businesses are also taking note of the Passive House market. Foard Panels, in West Chesterfield, New Hampshire, is just one of the SIP plants now selling panels specifically for the Passive House market.