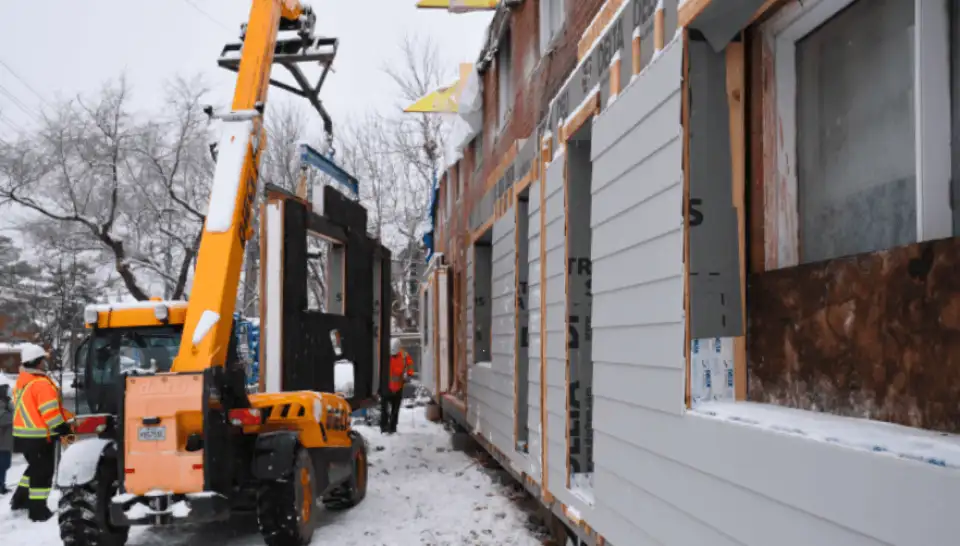
In 2017 Natural Resources Canada (NRCan) started a 5-year R&D initiative to develop and validate a process for retrofitting Canadian housing using prefabricated panels. The Prefabricated Exterior Energy Retrofit (PEER) project involves: assessing the market; developing and testing panel concepts; developing a process for measuring buildings rapidly and accurately; and conducting building science investigations to ensure the refurbished buildings are durable, healthy, and resilient. To date, five panel prototypes have been developed and several pilot projects are underway, with some valuable lessons learned.
PEER Process and Market
The PEER process involves four main steps:
digital building capture to measure the building,
panel design,
off-site fabrication, and
on-site preparation, installation, and finishing.
The digital capture process uses modern 3D scanning or imaging technology to acquire all of the dimensional building data and locations of penetrations. Based on these data, custom, airtight panels with thermal insulation, new siding, and windows and doors are designed and shop drawings generated. These panels are then prefabricated in an off-site shop, and water, air, and thermal control layers are detailed to be continuous before windows are set and the siding is installed. Finally, the building is prepared, panels are transported to site, and then installed. Panel joints are detailed for continuity in the field.
Canada’s Path to Deep Retrofits
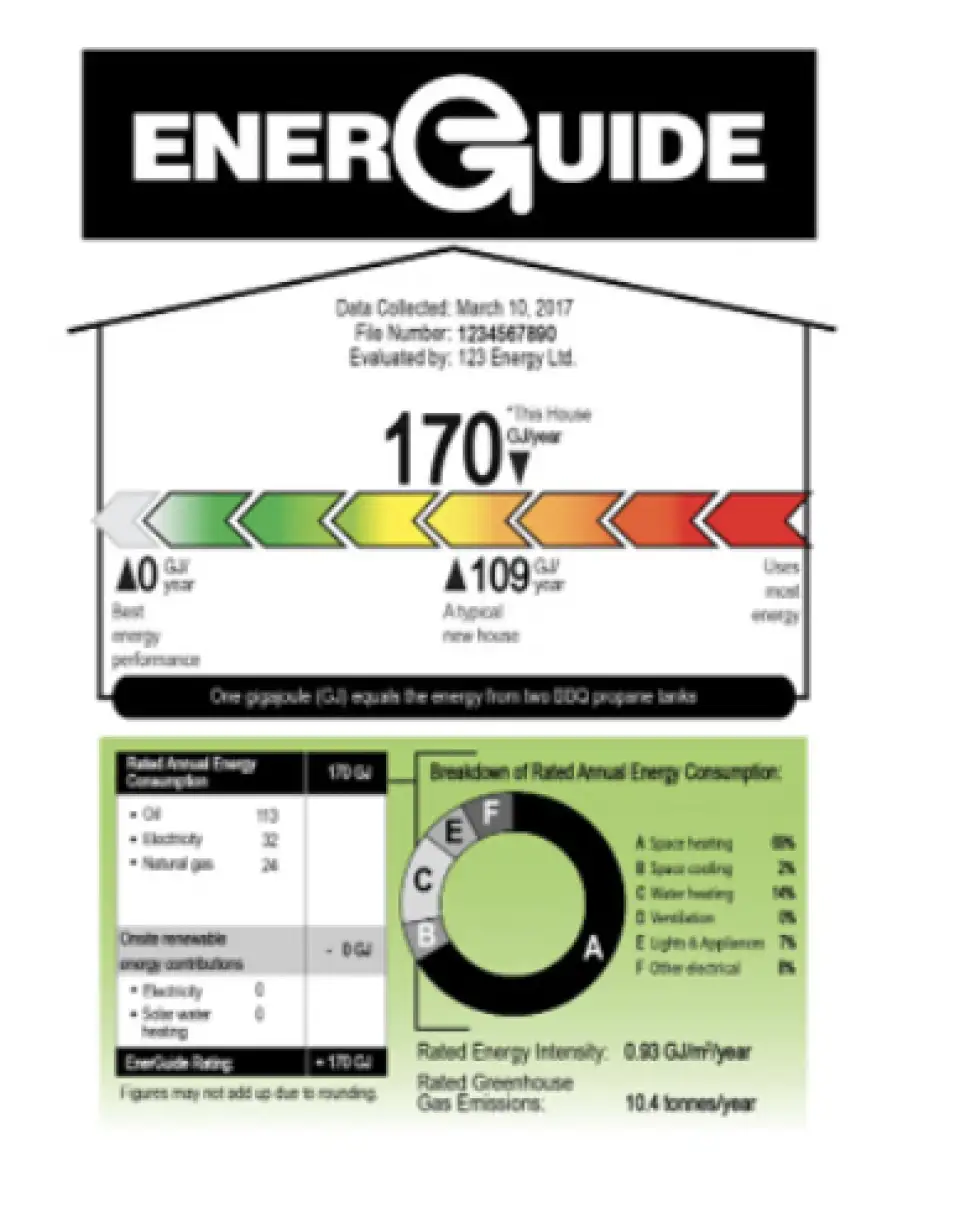
Canada’s housing stock consists of 15.8 million dwelling units1. NRCan estimates that 85-90% of the housing stock expected to be in place in 2030 is standing today, and that more than 67% of that stock was built prior to energy codes. Space heating is responsible for 64% of the energy use and 66% of the GHG emissions of Canada’s housing stock.
According to research, achieving a carbon-neutral built environment by 2050 will require deep energy retrofits to 2-3% of the building stock annually2. Current Canadian rates are approximately 1%3. To meet GHG emission reduction targets, some countries have committed to retrofitting 3% of their country’s stock annually4. The Government of Canada proposes to provide $2.6 billion over seven years to help homeowners improve their home’s energy efficiency.5
NRCan has been tracking retrofits for decades, maintaining a database of homes that have undergone energy audits and been evaluated using Canada’s official EnerGuide Rating System (ERS)6. The database contains before and after audit data from more than 1 million homes that undertook an energy retrofit over the last 25 years. Many of these retrofits took advantage of federal, provincial, or utility incentive programs. HVAC system replacement and piecemeal envelope improvements (windows, attic insulation, and incremental air-sealing) proved most popular. On average, each retrofit achieved an annual energy savings of 21%. While impressive, these savings fall short of what research has shown to be necessary to decarbonize the housing stock7 2.
To unlock deep energy and carbon savings, comprehensive retrofits that tackle the building envelope are necessary to reduce heating demand. Despite incentives available for such measures, these retrofits made up only 4% of projects in the ERS database.
There are several reasons why deep energy retrofits remain so rare. They are expensive and they carry both financial and technical risks. Often, deep energy retrofits have been undertaken from the interior and have required a full gut renovation, a major barrier given the disruption to the occupants’ lives. Exterior retrofits can dramatically lessen this disruption, which can be further reduced by using off-site fabricated components that shrink the on-site labor required.
Energiesprong—an initiative that originated in the Netherlands—has completed thousands of net-zero energy retrofits from the exterior using prefabricated panels and mechanical pods. Solutions have been standardized, and automation is now being exploited to further reduce costs. Although PEER is loosely modeled on the Energiesprong approach, the Canadian context varies in some important ways. Not only is our climate colder, but we have much more variability, with 6 ASHRAE climate zones throughout Canada. In central Europe, builders benefit from high population density, so panels can be produced in a few central facilities and shipped to anywhere in the country. Due to our population density and immense geography, it’s hard to imagine one panel fabricator serving more than a few markets in Canada. In the Netherlands, the building tradition tends to be masonry and concrete, whereas here light wood framing is used almost exclusively for residential construction. Unlike the Netherlands, most residential construction in Canada has a full-basement, complicating insulating and air sealing of the whole building from the exterior. The cost of energy—particularly gas—is high in the Netherlands, which makes the business case to retrofit and electrify more compelling. Financing for these projects in Canada may have to piggyback on other capital upgrades or rely on government assistance.
Finally, Europe adopted off-site fabrication in a major way to rebuild after the Second World War. In Canada, prefabrication is less prevalent, although there are many wood-frame prefab facilities (component fabricators) that currently build trusses and some that build walls who could provide base panels. Similarly, modular homebuilders are well set up for this work. There is also a growing list of high-performance panel fabricators catering to the Passive House new construction market, across North America (see Passive Goes Prefab). These suppliers would be ideally suited for this work as well.
At the outset of the PEER project, the researchers convened an industry working group (IWG). The group is composed of general contractors, modular builders, panel fabricators, manufacturers, building capture and building science consultants, and energy advisors. We developed an Industry and Business Strategy in consultation with this group that conceives of the various industry roles in such projects. The three main categories are:
manufacturers, who produce base panels;
fabricators, who finish base panels in a secondary shop and install them on site; and
contractors, who are responsible for site work
and contracting.
Most of the manufacturers we spoke with are uninterested in producing custom, finished panels. But by supplying base panels, they can continue doing what they’re very good at. There may be opportunities for them to offer some added value such as fluid-applied air and weather-resistive barriers (AB/WRB) in the panel factory. Some manufacturers may be positioned to do this already and, with little investment, could adapt their process to serve this market (i.e., modular builders).
Panel fabricators are accustomed to customizing their offerings and installing membranes and even windows and siding. They may take a manufactured base panel and add layers, or they may elect to produce finished panels from scratch. General contractors (GCs) can set up shop to become panel fabricators with minimal investment. Although very large GCs are doing this work in the Netherlands, we see a more geographically distributed model with a mix of small, medium, and large players making sense across Canada, especially in the North and in areas of lower population density.
Social housing is a logical catalyst market. Much of Canada’s social housing stock—roughly 550,000 units or about 3.5% of the housing stock—was built in the 1970s and ’80s, when energy efficiency standards were non-existent. Many of the units have experienced years of deferred maintenance and repairs to building envelope components and require significant capital investment to replace the original windows, siding, and roofing. With the high costs associated with displacing or relocating tenants to undertake interior retrofits, approaches to rapidly retrofit from the exterior are attractive to housing providers. The buildings in this sector tend to be simple and architecturally similar so they lend themselves to an assembly-line approach. Finally, housing providers take a long-term view to the ownership and management of their housing portfolio, which is critical for realizing returns on such investments.
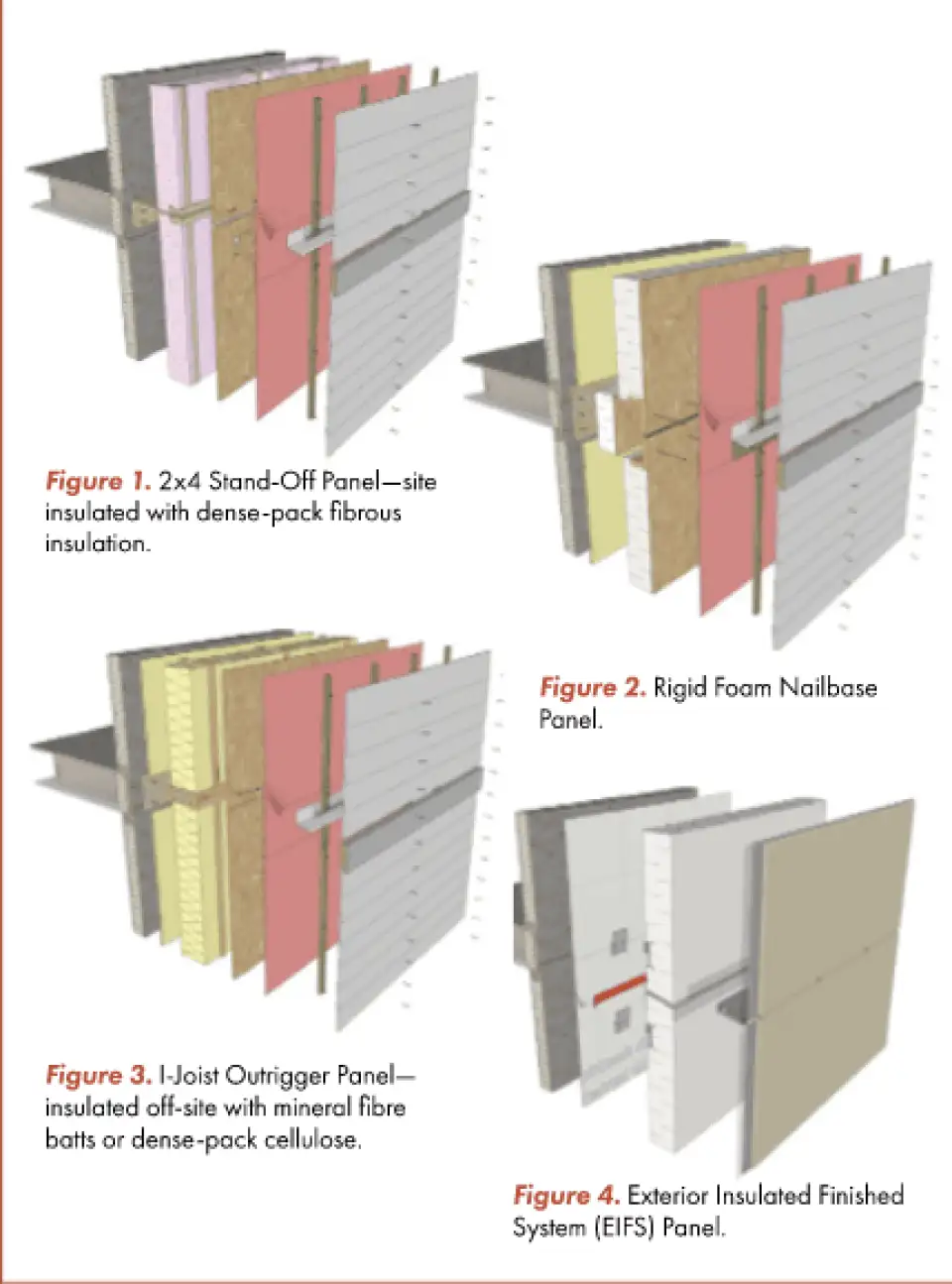
Building Capture
Building capture is the process of accurately recording existing 3D building dimensions and site conditions using scanning, imaging, and/or point-to-point measurements. Using laser scanning and photogrammetry methods, millions of surface points are measured and mapped to create a textured, high-resolution, geometrically precise 3D model. These methods can be conducted from a distance at grade with minimal impact on building occupants and without the need for scaffolding or lifts. Project conditions and panel designs will dictate the necessary degree of accuracy, but we established a 6-mm (1/4-inch) tolerance for the most critical dimensions in pilot projects. NRCan is working on guidance for this application, which should be ready for publication in 2022.
Panel Prototypes
To date, five PEER wall panel prototypes have been developed. The first generation were based on designs that already exist and are widely available for new construction: light wood-frame; structural insulated panel (SIP); and rigid-foam nailbase panels (single-sided SIP). Next-gen panel designs currently under development include an EIFS option for multifamily and a low-carbon, I-joist panel design.
All panel designs include a fully adhered exterior air and weather resistive barrier to provide both water and air control functions. New windows are integrated with this layer. Panel joints are detailed to offer some dimensional tolerance and flexibility while maintaining continuity of control layers. Figures 1-4 are partial exploded views of several of the panel prototype components at floor line transitions.
Pilot Projects
NRCan completed a proof-of-concept pilot at its complex in 2017 by retrofitting a construction trailer using both 2x4 stand-off panels and rigid foam nailbase panels. This pilot offered the opportunity for side-by-side comparisons of cost, constructability, and performance. Cost and constructability were roughly equivalent. The airtightness of the whole building was improved from 7.62 to 0.82 ACH50, after the floor and roof also had been retrofitted. Hygrothermal monitoring has been ongoing since January 2018. Despite some wetting that occurred before the roof was dried-in, both retrofit wall assemblies have performed well. The VTT mold growth index8 was used as the primary durability criterion, with a maximum threshold of 3.0 on the existing and new sheathing layers. The mold index on the new sheathing of the wood frame reached a maximum of 0.45 while construction moisture was dissipating and has declined since to 0. The mold index at all other monitoring locations has remained less than 0.02.
Table 1. Sundance Housing Co-Op Pilot Key Performance Metrics
Pre-Retrofit |
Retrofit |
|
---|---|---|
Roof R-value (hr ft² °F/BTU |
28 |
78 |
Above Grade Wall R-value (hr ft² °F/BTU) |
15 |
41 |
Foundation Wall R-value (hr ft² °F/BTU) |
10 (partial) |
38, 25 (above, below grade) |
Windows (hr ft² °F/BTU) |
3.0 (COG) |
8.6 (COG) |
Slab on grade |
Uninsulated |
Uninsulated |
Airtightness (ACH50) |
6.5 |
0.7 |
Space Heating |
90% AFUE (gas) |
Daikin ASHP with a seasonal COP of ~2 |
Cooling (SEER) |
n/a |
Daikin ASHP with a seasonal COP of 4.5 |
Ventilation (SRE @0°C, @-25°C) |
n/a |
Lifebreath 267 MAX SRE@0C 75 , -25C 70 |
Domestic Hot Water (Uniform Energy Factor) |
0.56 |
AO Smith ASHP water heaters – Seasonal Effective COP of ~2 |
Butterwick Projects is using the 2x4 cellulose-filled stand-off panel in a demonstration project to retrofit the 59-unit Sundance Housing Co-Op in Edmonton, Alberta to net-zero ready levels. This involves hydrovacing—or using pressurized water to cut—a slot around the foundation, insulating from the exterior, adding the above-grade panels with new windows and cladding, and installing a scissor truss framed over-roof. The project also includes full electrification of the thermal demand. Nine units have been completed to date (see Table 1). The team achieved a very impressive 0.7 ACH50 pressurized, and depressurized, envelope-only blower door result. The cost for each of the semi-detached homes was roughly $120,000 CAN. The target for the other 57 units is $95,000 CAN per unit. The team hopes to find savings from offsite panel construction, onsite efficiencies, and economies of scale.
Ottawa Community Housing (OCH) is using the SIP design in its pilot retrofit of a block of four townhomes. The project has been designed to achieve net-zero energy (NZE) and is being done while the units are fully occupied. The asphalt shingles and existing brick cladding are being retained to speed up construction and reduce demolition labor and landfilling. Modeling and monitoring were undertaken to assess how much moisture can be safely accommodated by the brick prior to over-cladding. OCH constructed its own fabrication shop to build the 24 20x9-foot panels, utilizing in-house carpenters who installed the panels on site with a telehandler and crane. Engaging local contractors, the mechanical and electrical systems were upgraded, replacing all the natural gas equipment with heat pumps and deploying a 35-kW solar array on the roof to make the building net-zero energy and to eliminate operational carbon emissions (see Table 2). The project was completed in spring 2021.
The concept is important for OCH, which owns 15,000 units of residential housing (6,000 townhomes and 9,000 apartments), the vast majority of which are hitting a 60-year cycle turning point. Not only do these units require considerable capital investment for maintenance in the near future, but they are not very energy efficient. Their utility bills represent a significant liability for the corporation as well as the affordability of housing, which OCH advocates must include rent as well as utilities. The goal is that the project’s results will inform the capital planning strategy for OCH’s 15,000-unit portfolio, as well as the rest of Canada’s affordable housing sector.
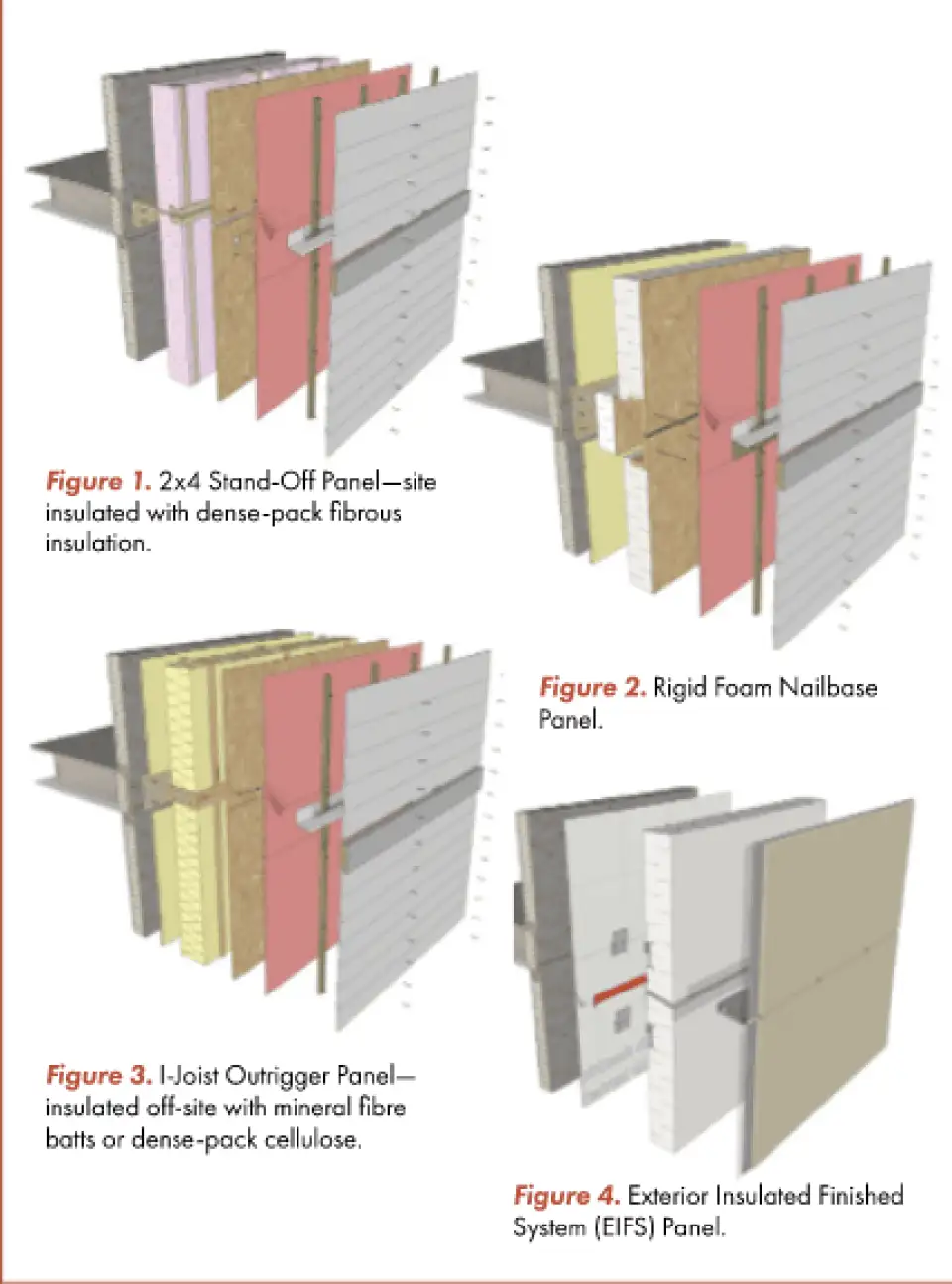
Next Steps for PEER
Case studies are being developed, and ongoing monitoring of the OCH pilot’s energy use, air quality, comfort, and hygrothermal performance will take place. The lessons learned through the pilots will inform the development of a PEER Building Capture and Design Guide that is currently scheduled for publication in 2022.
The team is also developing PEER modeling and monitoring protocols to inform best practices for consistent hygrothermal modeling methodology, parameters, and boundary conditions. This work will also be instructive to determine how long an existing enclosure assembly—particularly those with reservoir claddings—must be allowed to dry to assure that built-in moisture is below safe limits. The team then plans to turn its attention to mid-and high-rise construction and low-carbon panel designs.
Many thanks to Jeff Armstrong at Cold Climate Buildings, Dan Dicaire at Ottawa Community Housing, and Peter Amerongen at Butterwick Construction for their contributions.
Publications will be available on the NRCan website.
For more information or to be added to the distribution list, please contact: