Highland Passive House—the first multi-use warehouse in North America designed to be certified by the Passive House Institute—is currently being built in the community of Highland, New York. Four years ago, the facility was sitting in pieces in several small buildings in rural Maine. This is the story of how Cathy Hobbs, a former Emmy-award winning television news reporter turned top New York City-based real estate stager and interior designer, and Michael Ingui, a New York City-based architect, paired up to make the project a reality.
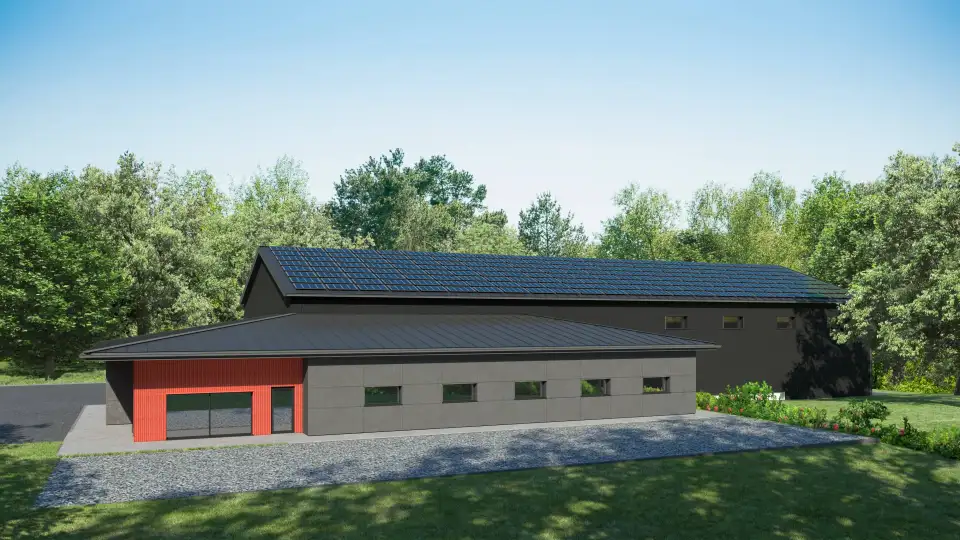
Putting the Pieces Together in Highland

The Reporter
The year was 2009. Cathy Hobbs took a deep breath before walking through the door of the general manager’s office at WPIX. Though Hobbs had enjoyed a storied career in television news and racked up 19 local Emmy nominations during her 20 years as an on-air reporter, the five-time Emmy-award winner had never been in the general manager’s office.
“‘This must be pretty important to you,’” Hobbs recalls the general manager saying once she entered the office.
It was. Hobbs was envisioning a change in career. While many on-air reporters go into public relations or become corporate spokespersons after leaving network news, Hobbs instead wanted her own real estate and design series on the station. Unbeknownst to the general manager and most of her colleagues at WPIX, Hobbs had spent the last seven years delivering the news to New York City at night but working during the day to obtain a second degree, a Bachelor of Fine Arts in interior design from the Fashion Institute of Technology. (Her first degree is a Bachelor of Science in marketing and finance from the University of Southern California.) Combining her knowledge of design with her on-air experience, she said, would make great television.
The general manager agreed. Three months later the first episode of Hobbs’ real estate and design series premiered on WPIX. Hobbs’ show, Design Recipes, ran for 7 seasons, until she placed it on permanent hiatus during the pandemic. Additionally, Hobbs is also an alum of the top-rated HGTV competition reality series HGTV Design Star in which she was a finalist on Season 6.
Hobbs’ success transcends well beyond television. She obtained numerous industry credentials, including ASID (American Society of Interior Designers), NCIDQ (National Council for Interior Design Qualification), and LEED AP (U.S. Green Building Council) certifications and runs her own interior design company that specializes in real estate staging and vacation rental design, Cathy Hobbs Design Recipes. Her client base has grown steadily over the years, and while still concentrated in New York City and the surrounding areas, her company is now expanding into the Hudson Valley, while also providing remote design services nationwide.
With success came a problem, however. She needed a storage facility that could house her furniture, artwork, and accessories, as well as an office and production studio. Moreover, she wanted the space to be centrally located within the valley and with easy access to Manhattan.
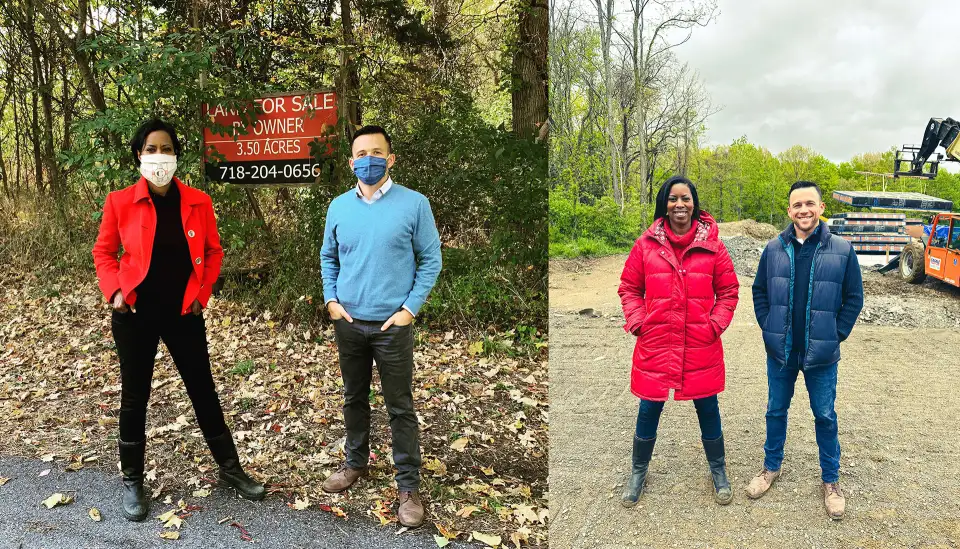
The Site
Much of Highland is a mix of rural and industrial, dotted with warehouses, farmland, residential homes, and vacant land, but it is near I-87, one of the primary arteries connecting New York City to the Hudson Valley. It is no surprise then that Hobbs’ search for a warehouse ultimately led her to the community and to a vacant and roughly four-acre property that was zoned for a commercial building. Moreover, the property was close to I-87 and could easily be accessed by tractor-trailers.
“I needed a space to grow, and I also wanted it to be safe. That’s what I found,” she says. “It’s a beautiful location, surrounded by orchards on three sides.”
Perhaps most importantly, the property represents part of a legacy for Hobbs and her family. Shortly before finding the property, her aunt passed away. She later learned that the aunt, a former schoolteacher, left Hobbs and her brother a modest inheritance, one that ultimately became the downpayment for the Highland property.
“I was going to do something that was in her honor and that honored my family,” she says. “I wanted to be able to plant a seed and watch it grow.”
“This is my Raisin in the Sun story.”
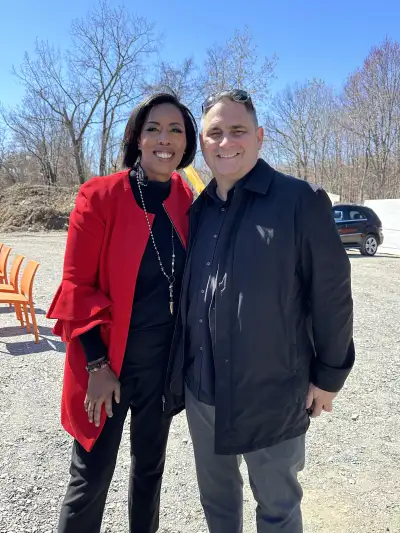
The Architect
While shooting an episode of Design Recipes in 2017, Hobbs had the opportunity to meet architect Michael Ingui of Baxt Ingui Architects PC, as Ingui was featured in a segment on the show. Ostensibly, Ingui was providing a tour of a recently retrofitted townhouse in one of the most exclusive neighborhoods in Brooklyn. However, Ingui used the opportunity to focus on the fact that the luxurious space had been PHI-certified and to describe the benefits of Passive House design and construction in tangible and concrete terms. Triple-pane windows translate into less noise infiltration. Better air sealing means healthier air, less dust, and fewer bugs. Energy efficiency means mechanical systems can be smaller. “It means you get a roof deck instead of a roof full of mechanicals,” Ingui says during the segment.
After touring the townhome and speaking with Ingui, Hobbs found herself fascinated by Passive House and Ingui’s approach to design, but the two didn’t have a chance to speak again until two years later. Hobbs was hosting a real estate panel and saw an opportunity to reconnect, so she reached out to Ingui to see if he wanted to join.
He did.
What Ingui did not realize at the time was that Hobbs had another motive: she wanted him to help her build a warehouse, even though she recognized that he specializes in residential architecture. She told him she had sought him out personally, because she wanted to build it to Passive House standards.
As luck would have it, Ingui knew someone who could help.
The Warehouse
Chris Corson of Ecocor had a problem. He had dozens of disassembled structural insulated panels (SIPs) stacked neatly in several buildings that he suddenly didn’t need any more. The SIPs had been prefabricated in his nearby manufacturing facility in Searsmont, Maine, and they were supposed to become the high-performance envelope of a 16,000-ft2 facility that was intended to be used as a manufacturing facility and showroom for Ecocor. However, following a recent real estate deal, he no longer needed to build the facility.
After speaking with Corson, Ingui told Hobbs that the building (or, rather, the SIPs that would make up the building) were for sale. “‘You tell him I'm flying up this week,’” Hobbs recalls telling Ingui. She then booked the flight, drove to Stewart International Airport in Newburgh, and met Corson in Portland.
“By the time I left Maine, we had a deal,” Hobbs says.
The Final Piece
Though Hobbs had a property, an architect, and several stacks of SIPs, she still needed some help securing financing for the project. This is where the New York State Energy Research and Development Authority (NYSERDA) and their Building Cleaner Communities Competition (BCCC), previously know as the Carbon Neutral Communities Economic Development (CNCED) program, entered the picture. “If it wasn’t for NYSERDA, Highland Passive House would not have been possible,” Hobbs says. “I could not have asked for a better partner for this project,” she elaborates.
It was not an easy process. Hobbs had never applied for a grant through the agency, and she admits to being intimidated by how involved all the paperwork was. However, she attended the virtual information sessions they offered, she reviewed the online material, and she worked diligently on the grant application for six weeks.
The effort paid off. In December 2021, Hobbs received word that she had been awarded a CNCED grant of approximately $1.3 million to help finance the construction of the warehouse, and the balance of the financing for the project is being facilitated through a joint partnership between NBT Bank and the Small Business Administration and its 504 loan program.
“These grant programs are not meant to be hurdles that can’t be overcome,” she says. “I'm a small business owner, just like every other small business owner in the State of New York, who wanted to participate in this program, who wanted to make a difference, who wanted to be part of a movement towards sustainability. I applied for a grant, and I got it by following the steps.”
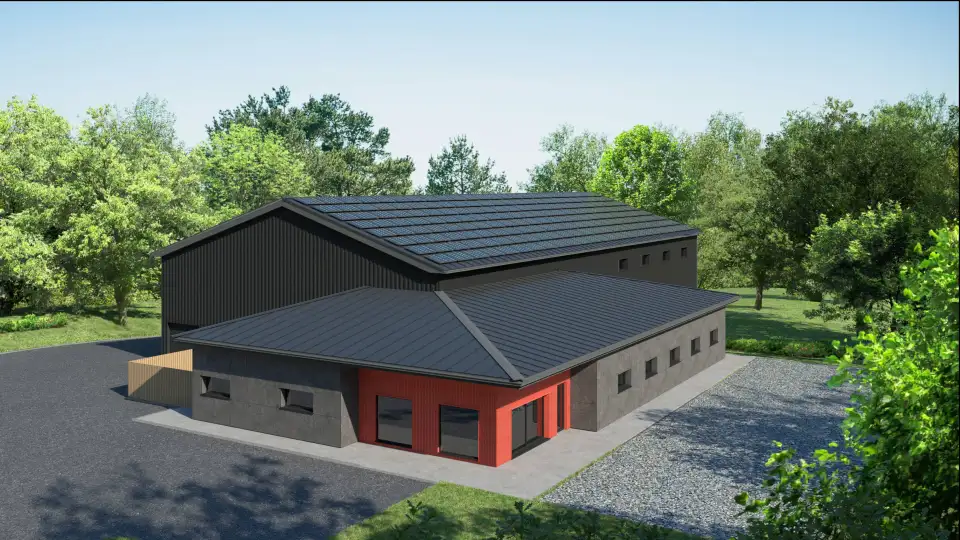
Putting the Puzzle Together
Construction on Highland Passive House commenced in December 2022, and it is slated to be completed in early 2024. However, a significant amount of planning and design modifications had to occur before the SIPs could be connected to form the facility. First and foremost, the team had to decide how they wanted it placed on the site and what was the best orientation to optimize solar gains in the winter and avoid them in the summer. As shown in Figure 1, the facility is clearly divided into two separate areas: the warehouse and the office. More than just serving two separate functions, they are actually two distinct buildings sitting next to one another that have different mechanicals and foundation systems, even though they are seamlessly connected through a doorway.
The warehouse building is 9,000 ft2 and has 20-foot-high walls atop which 11-foot-tall trusses span 67 feet. These massive trusses allow for a column-free design that will leave the interior space wide open. The eastern end of the warehouse is closest to the street and where the loading dock is. It will contain 20-foot racks similar to those found in big box stores to house Hobbs’ home-staging inventory. Such a cavernous space is necessary, as Hobbs’ firm is capable of staging approximately 60 properties simultaneously. “That's a lot of couches,” Hobbs says. The space at the western end of the warehouse will be split by a mezzanine level and used to store smaller items.
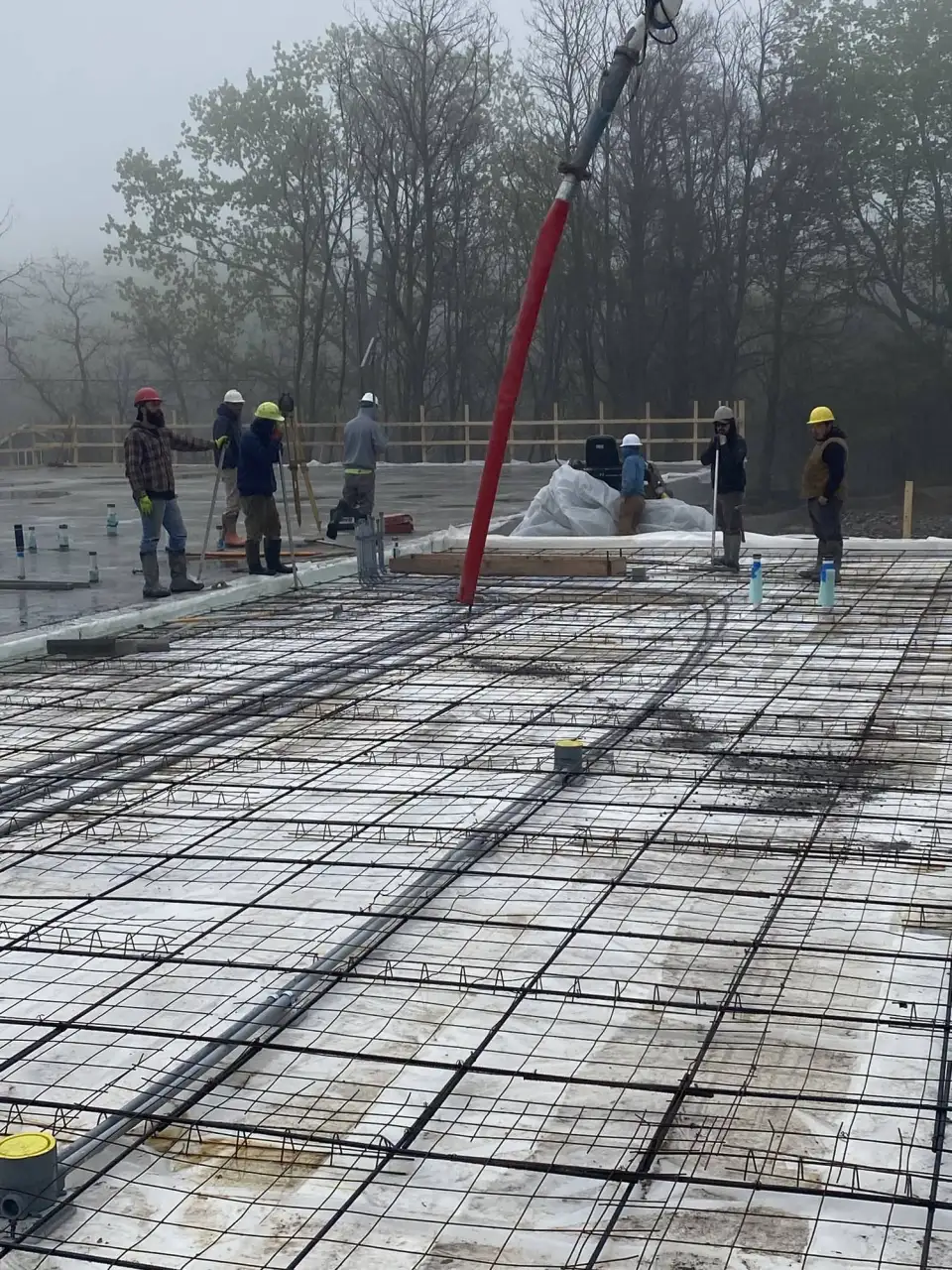
The second portion of the facility is an L-shaped office and studio that is 3,500-ft2. It has 10-foot-high walls that are also held in place by a truss system. It will be connected to the warehouse through a door at the southwestern corner of the warehouse. The office will be open and more fluid than a traditional office plan, allowing for more freedom of movement for employees. Hobbs notes that the space will also be very adaptive and well-lit so that different parts of the space can quickly be converted into sets for filming.
Though the facility was prefabricated, there was some wiggle room in deciding how the two spaces would be connected. According to Will Conner, an architect with Baxt Ingui, the L-shaped space could have been attached to different sides of the warehouse, but they ultimately decided that the southwest corner would be best. “It’s all going to be well lit with lots of natural light,” says Conner. There will be a two-foot overhang on the south side of the building to provide additional shading, but there’s also a tree line that will keep things shaded in the summer.
Once the orientation and site location were determined, they then had to build a foundation to accommodate the facility. For the office space, it’s a slab-on-grade foundation that has a nine-inch layer of borate-treated type-4 EPS beneath the slab, which is eight inches thick. For the warehouse, the foundation is deeper and made of ICFs [insulated concrete forms] manufactured by Nudura. “That ‘I’ stands for insulated, so we already have insulation impregnated in the concrete right off the bat during the pour,” according to Jacob Winterman of Baxter Building Corp, the project manager on the construction side of the project. This means they didn’t have to go back after the fact and install insulation.
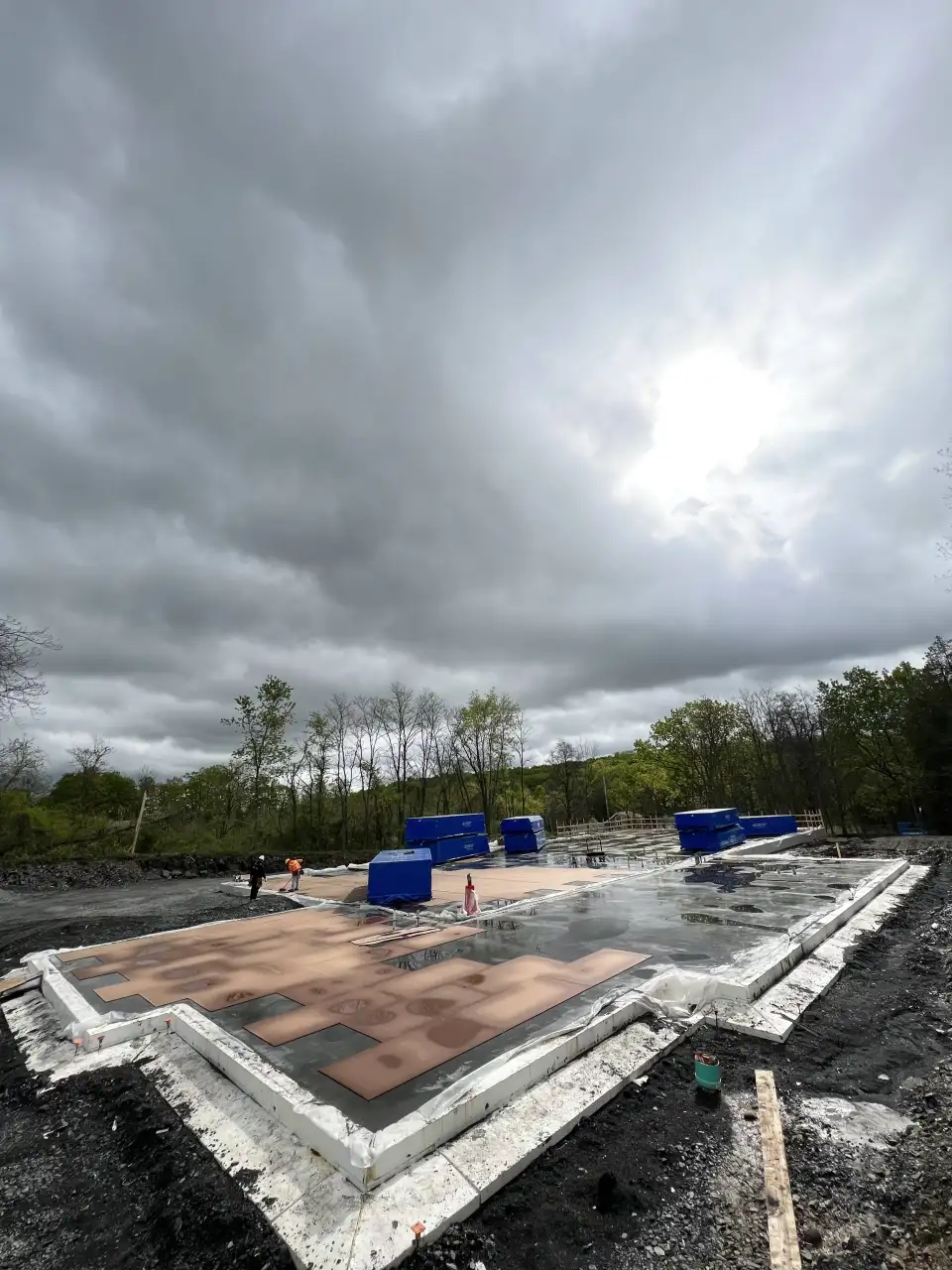
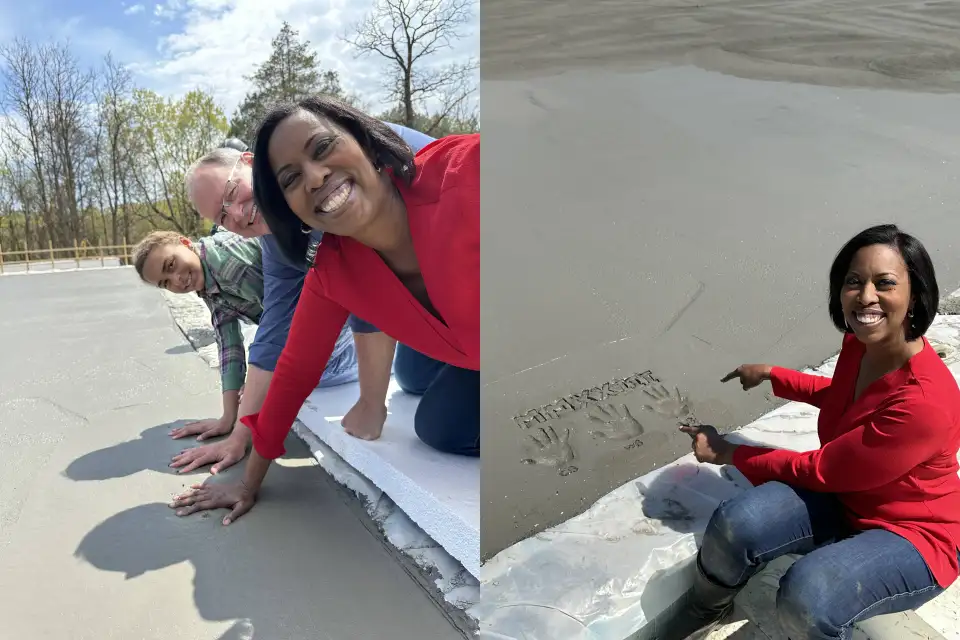
Once the foundation was completed, the panels could be brought to the site and erected. “It’s essentially just a big, adult Lego set,” Winterman says, adding that it only took three weeks to assemble the facility. Accelerated assembly is one of the major benefits of using SIPs, and the pace was even quicker than is typical because of Baxter’s familiarity with the process. “Logistically, it’s a little bit more difficult,” Winterman says. “Instead of getting stacks of lumber, you get giant panels and that’s something you need to figure out in advance. The last thing we wanted was to have a pile of panels with a panel that we needed all the way at the bottom or on the other side of the site.” However, he notes, “Building with this panelized system is pretty revolutionary.”
Working with SIPs also meant that minor modifications could be made to Corson’s original design. The placement of the garage door for the loading dock is a case in point. When the warehouse was originally fabricated by Ecocor, it was not part of the design. However, Ecocor worked with Baxt Ingui and manufactured a large header that the team used to frame out the door rather than building it from scratch. “It’s nice to work with a collaborative team that likes to work and problem solve together,” Ingui says.
The retractable garage door for the loading dock is also an interesting feature, as they are usually placed outside of the Passive House envelope. In this case, it simply was not possible because it is integral to the function of the space. While most of the windows and doors were manufactured by California Deluxe Windows (CDW), a firm with which Ecocor frequently partners, the garage door was supplied by Ikon Windows + Doors and manufactured by the Polish firm Wiśniowksi. According to Adrian Dymarczyk, the principal of Ikon, the doors are “thick, insulated panels with gaskets in between.” Sealing at the top, sides, and bottom of the door adds to its performance, allowing the door to achieve a U-value of 0.33 W/m2K.
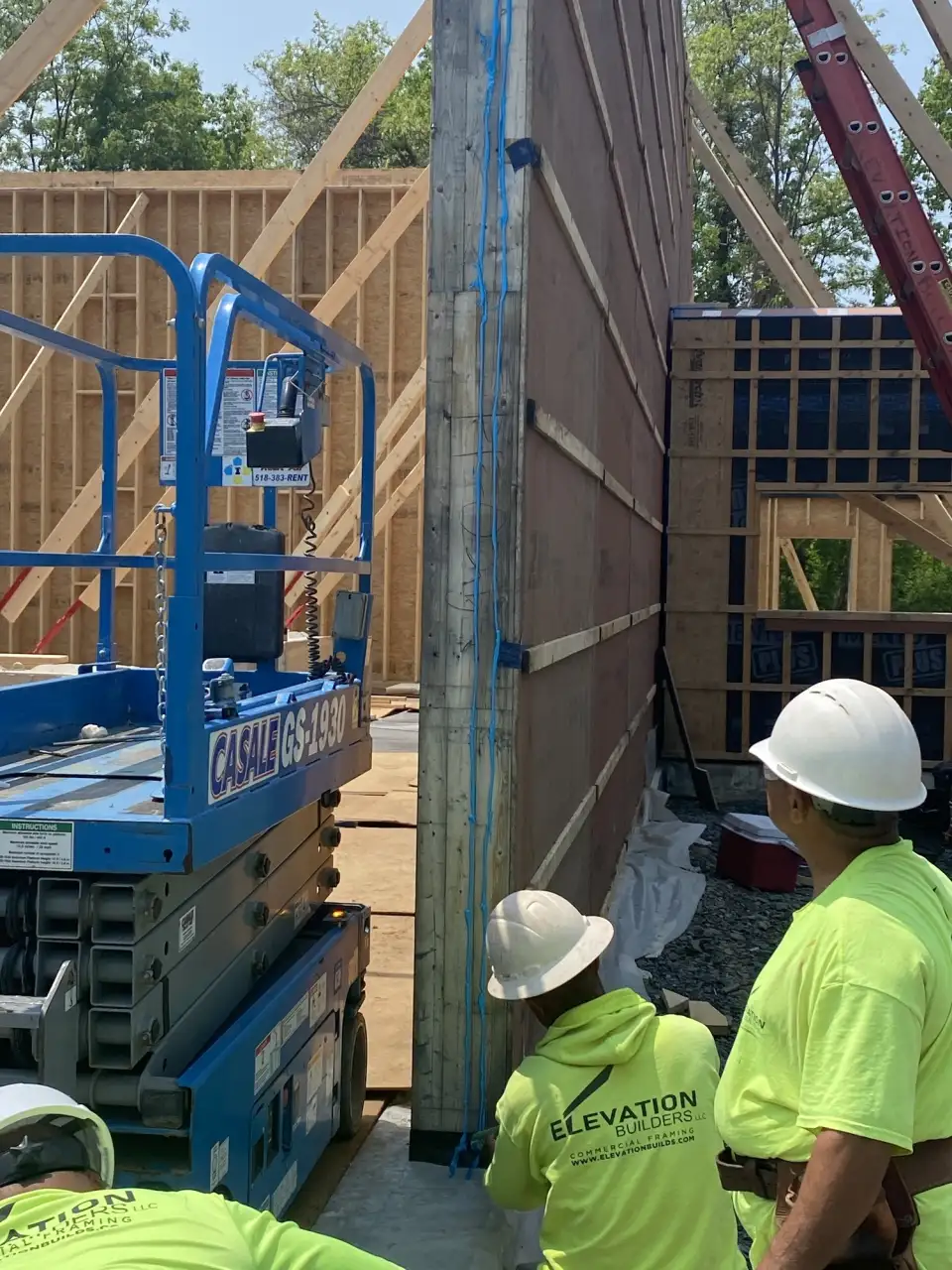
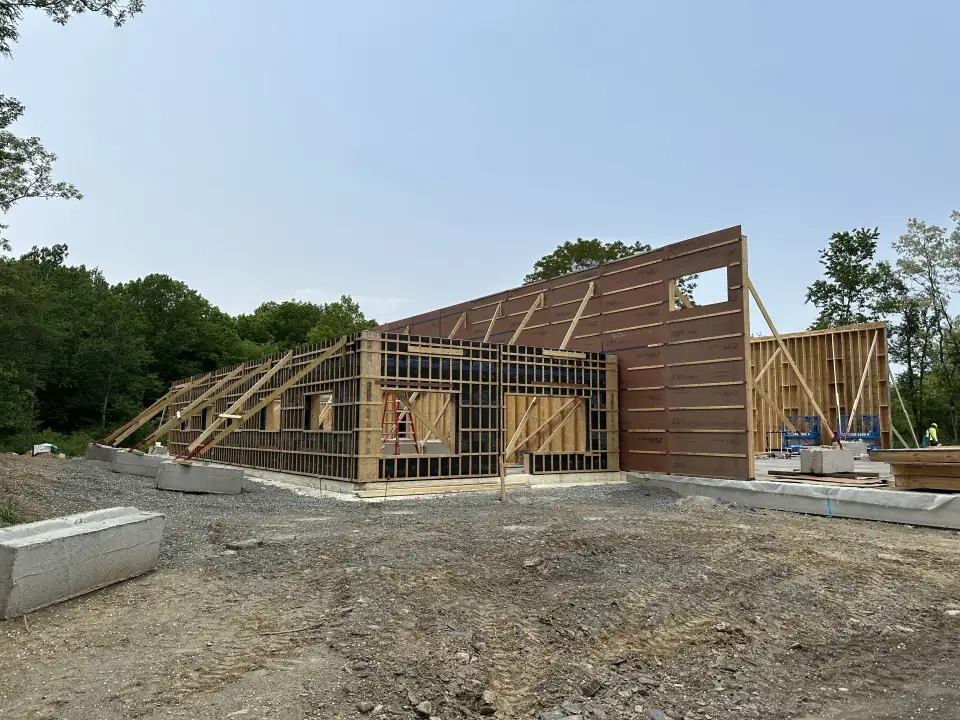
The Ecocor panels will provide a thick layer of insulation and make up the major of the wall assembly. On its exterior will be a stucco system that contains an air barrier and a water barrier. Meanwhile, the roof assembly consists of 10 inches of outboard insulation that will sit on top of the sheathed truss. The roof will be outfitted with a south-facing PV array containing 90 panels. On sunny days, the all-electric building should be completely powered by the array and may even generate excess power that will be stored in Tesla batteries.
As noted before, the two buildings will have different mechanical systems because of disparities in their volumes, as well as level of appliance use and how many people occupy the spaces during the workday. The ventilation system in the warehouse is a massive ERV unit manufactured by Ventacity and is ducted, while they were able to go ductless in the office space and use an ERV made by Zehnder. The heating and cooling systems are provided by Mitsubishi VRF heat pumps.
“It’s wild how small the systems become,” Conner says.
For workers in the office and the warehouse, the conditions will be warmer in the winter and cooler in the summer. Meanwhile, the airtightness and the insulation, as well as the soft goods being stored by Hobbs, will likely make the warehouse a quieter place to work. “Compared to a traditional metal warehouse, where you just have corrugated metal walls and basically zero insulation, it will perform a lot better acoustically,” according to Winterman.
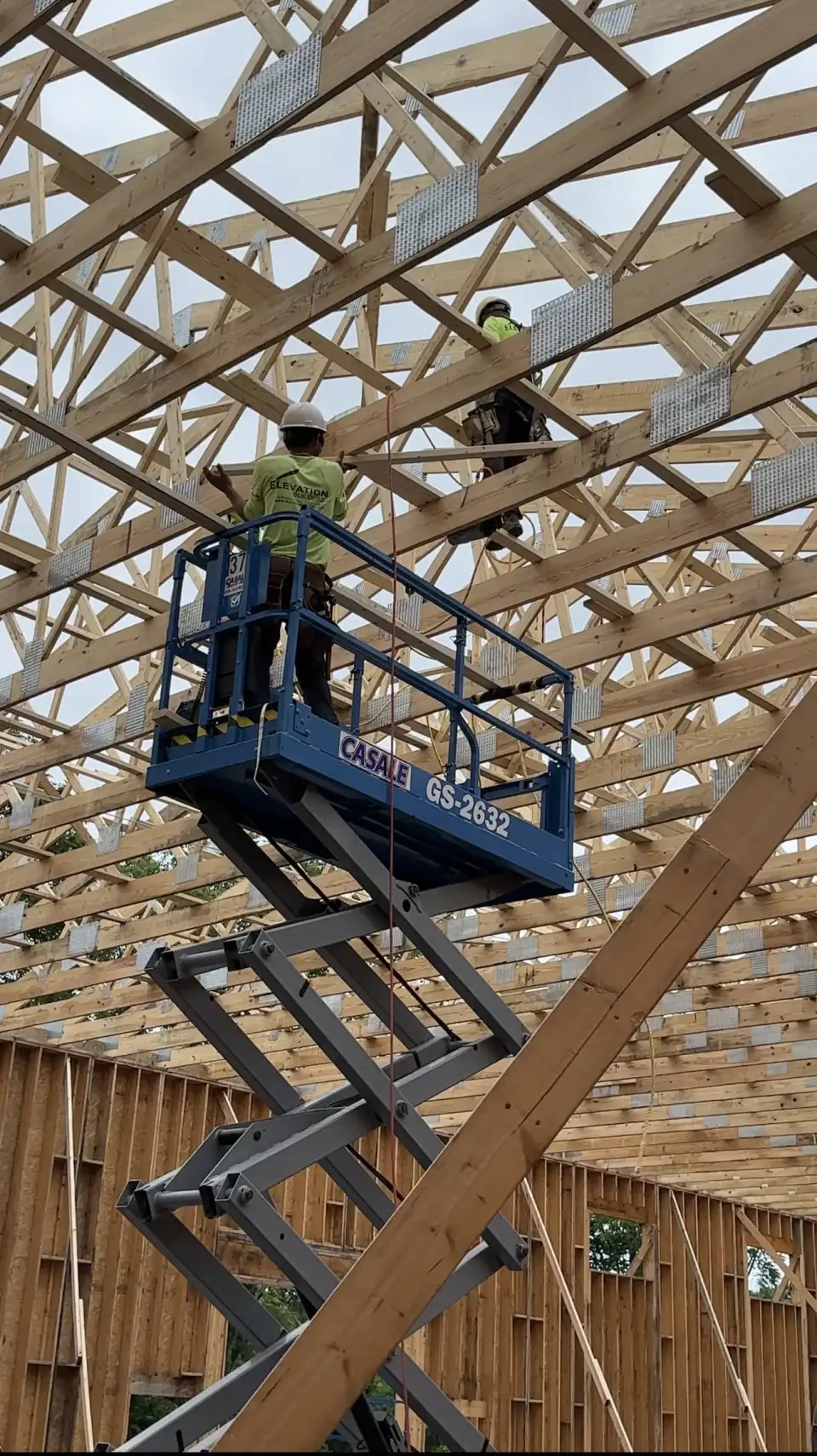
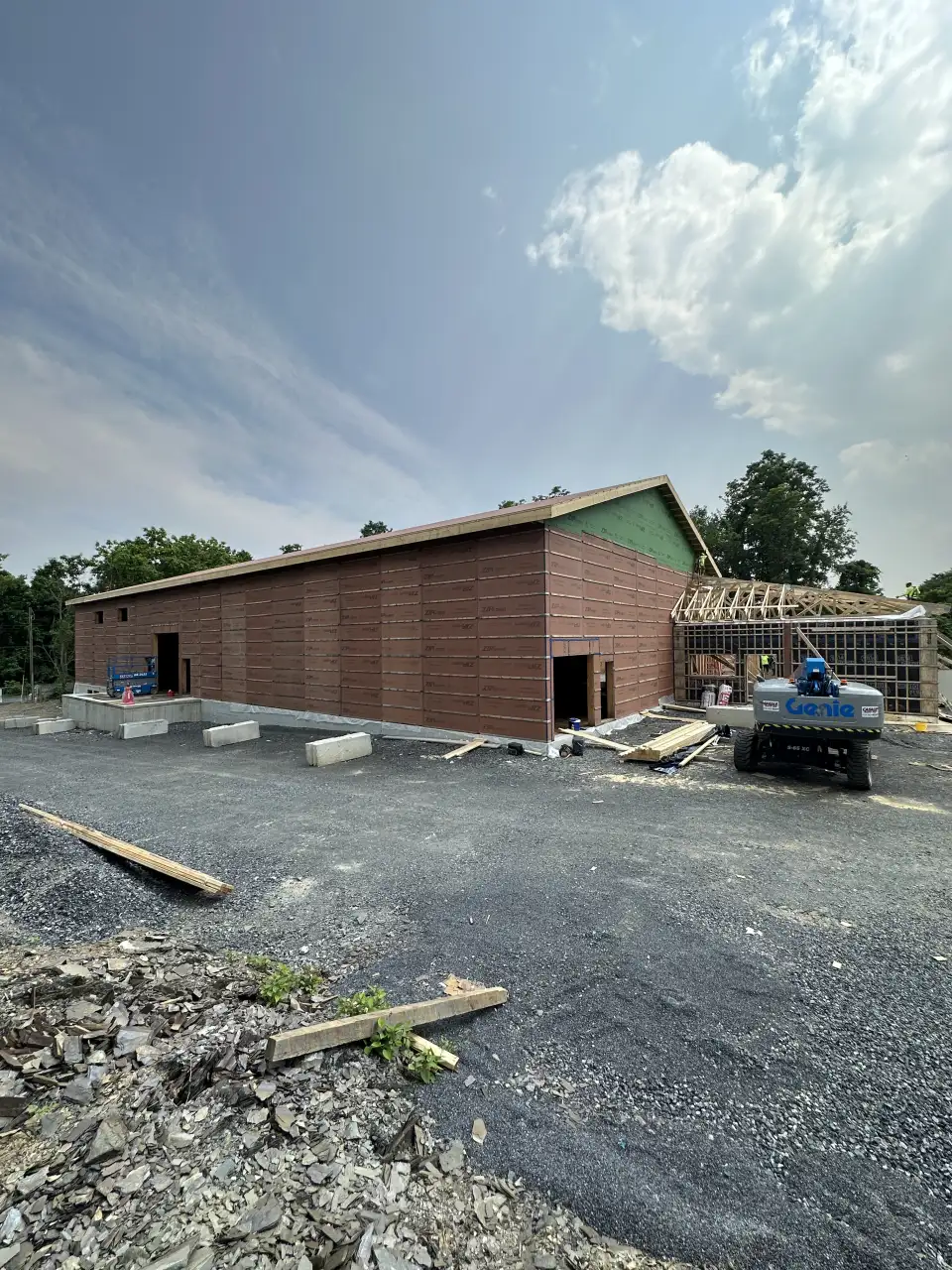
Serving as a Model
In addition to giving Hobbs the space she needs to grow her business and to provide a legacy project for her family, she also hopes that Highland Passive House will provide a template that others can follow in the future.
“My goal is to be an informational source and role model for other small businesses looking to build in a socially and environmentally conscious way,” she says. “What I’m also proud of is that the people who are involved in this project are experts in the field of passive design. That lends itself even more so to this project being replicable, something that can be studied and then duplicated.”
