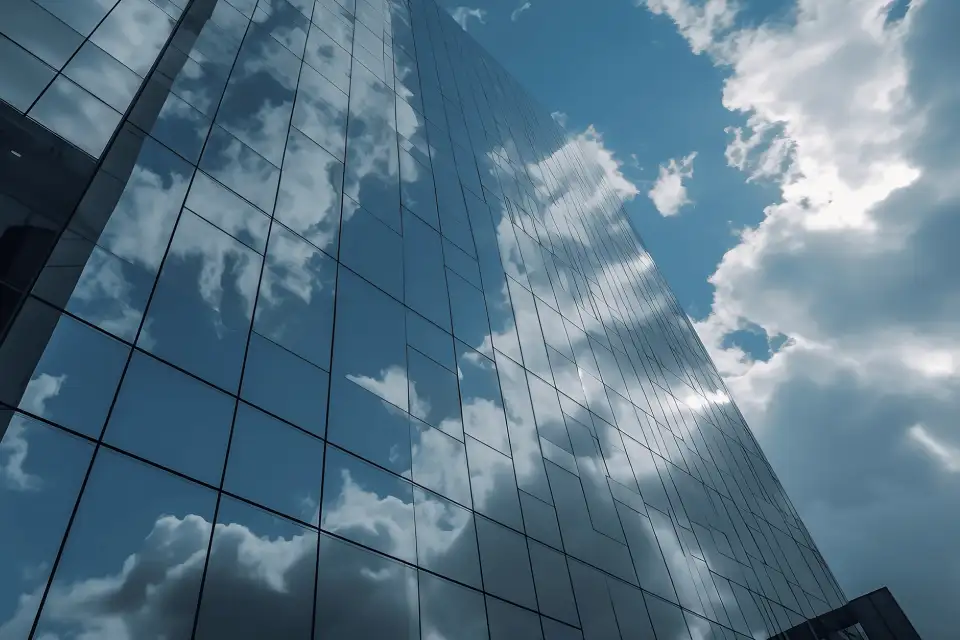
Resiliency can take on many forms. Within the Passive House community, it is often placed within the context of climate change and reflects how passive structures can provide a haven for occupants during very high or very low temperatures, power outages, and the kind of extreme smoke events that have characterized the summer of 2023 thus far.
Of course, resilience within the field of building science can relate to concerns that have nothing to do with climate change and one of them is fire safety. There is a three-pronged approach to fire safety that goes beyond just detection (e.g., smoke alarms, heat detectors). In addition, there are active systems to suppress the fire (sprinklers being the most common) and passive systems, which stop the spread of smoke, gasses, and flames through openings that are present at penetrations, joints, or gaps in fire-resistant wall, floor, or ceiling assemblies. By preventing the spread of smoke, gasses, and flames, passive systems provide occupants more time to escape and emergency responders more time to save those who are trapped and extinguish the fire.
It should come as no surprise that passive fire containment systems have a parallel with some of the principles of Passive House. Passive fire protection and Passive House construction both champion continuous insulation, thermal-bridging-free detailing, and airtight construction. If passive fire containment systems are installed properly and are not disrupted, the systems can remain in place for the life of the structure. It just demands a combination of materials science and exemplary work on the part of architects, engineers, and builders to make it all work.
Putting the R (Value) in Fire Resistance
One of the most common materials used in both passive fire protection and Passive House construction is mineral wool. Within the world of passive design and construction, the property of mineral wool that attracts the most attention is its resistance to conductive heat transfer. Mineral wool can be used in open-vapor systems without degrading thermal performance and has exceptional R-values. Within 2x4 walls, it can deliver an R-17.5. If installed in a 6-inch cavity, it can reach R-27.5.
In addition, mineral wool is non-combustible and designed for fire-rated assemblies, making it an outstanding material in fire containment and passive fire systems. Mineral wool can survive a fire at well over 2000°F for up to five hours, whereas a material like aluminum will melt in a 9-minute fire at 1220°F.
Perimeter Fire Containment and Passive Construction
While there are numerous firestopping applications for mineral wool, the role that the material plays in perimeter fire containment (PFC) systems is where it truly shines. PFC systems are designed to minimize the spread of flames and hot gasses from one floor of a building to the next via the space where the floor slab meets the exterior wall assembly. Of course, PFC is not exclusively a concern in Passive House construction. It is necessary for code compliance, building integrity in the event of a fire, and most of all occupant safety. However, the principles that guide PFC systems align with one of the fundamental goals of not only Passive House, but all high-performance building: durability.
The Reimagine Buildings Collective brings together building professionals stepping up to tackle climate change.
“If they’re designed correctly, if they’re installed correctly, they’re going to work continuously for the life of the building,” says Angie Ogino, the Technical Services leader for Thermafiber® Mineral Wool Insulation at Owens Corning.
When it comes to fire containment and PFC systems, Ogino and her team, Thermafiber Insolutions®, are Owens Corning’s secret weapons. Ogino has been with Thermafiber for 25 years and her specialties include providing development and testing of perimeter fire containment product and systems, engineering judgments, and technical assistance to architects and engineers on mineral wool product performance in a range of applications, particularly firestopping. The Thermafiber Insolutions® team has been instrumental in creating innovative solutions with Owens Corning® Thermafiber® mineral wool that help prevent the spread of fire and smoke throughout a building, particularly PFC systems for high rise buildings with curtain wall systems.
In addition to designing and testing these multi-story systems using UL or Intertek laboratory fire testing, the Thermafiber Insolutions® team also provides guidance on how to properly assemble the products and the systems to provide the anticipated level of fire performance with what are known as engineering judgments. “Thermafiber pioneered perimeter fire containment, and we’ve been testing this for over 45 years. It’s through this extensive testing that we’ve developed in-depth knowledge around the design components that are required for successfully containing fire,” she says.
“Contrary to popular perception, there’s more to fire containment than simply stuffing and spraying the void between the floor and the exterior wall.”
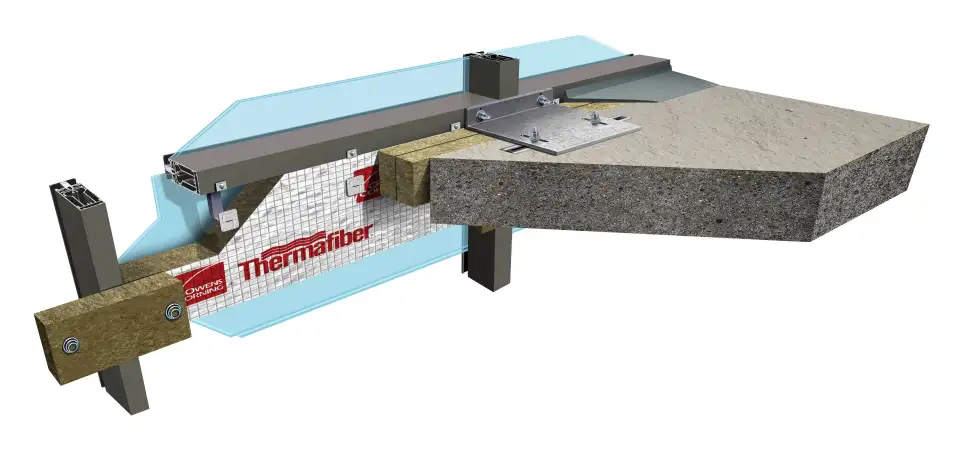
Zero Spandrel Construction and Engineering Judgments
Mineral wool is always an integral component of PFC systems and becomes especially important in PFC systems that have space constraints, which is common in high rise buildings where the walls contain a far larger percentage of vision glass. Ogino says that several decades ago, the spandrel (defined as the area of a curtain wall located between vision areas of windows, which are typically opaque to conceal structural columns, floor slabs and shear walls) were around 72 inches, and that PFC system could be contained in this space. Since that time, there has been an aesthetic push for vision area made up almost entirely of floor-to-ceiling glazing and just a few inches (or even zero inches) of spandrel. This design choice makes the implementation of robust PFC systems far more challenging. It also makes the Thermafiber Insolutions® team’s work on engineering judgments that much more important.
“As manufacturers of these products and these systems, we have to meet the demand of design and make sure that we keep developing and innovating safer assemblies for more complex design scenarios,” Ogino says. The Thermafiber Insolutions® team has invested significant purposeful time and resources in developing and testing their products and assemblies (including zero spandrel assemblies), this puts them in the unique position to review and assess project drawings and their potential fire performance to write engineering judgments for projects. They identify the weak points in the assembly and recommend alternative means that can address and rectify problematic areas while achieving the design goals of the project. “Because no two buildings are identical, we get the opportunity to review project-specific designs and integrate our perimeter fire containment systems into those designs,” she explains. “That’s the unique thing that Owens Corning provides over other mineral wool manufacturers—the ability to provide these engineering judgments. Because we pioneered these PFC systems and have spent years testing them and learning from those experiences, I believe that puts us in the best position to provide engineering judgments.”
Designing for Fire Performance
Over time, Owens Corning® Thermafiber® has amassed an encyclopedic knowledge of perimeter fire containment systems and individual components for building occupants, but their expertise is only valuable if fire performance is a consideration during the design phase of a project. “Once a building is already designed and under construction,” Ogino says, “it becomes more difficult to make sure that we are able to implement all of the design components required to make these systems work. For example, if there’s no access because there’s a very deep floor where you can’t put the curtain wall insulation in place or the joint material in place, it’s difficult to implement a tested and proven solution.”
Making buildings resilient to fires is an industry-wide effort, according to Ogino. It’s not just the inspectors who are enforcing building codes; designers, installers, and manufacturers all need to recognize the risks that fire poses and to create buildings with a balanced approach to life safety that includes detection, suppression, and the proper design and installation of passive perimeter fire containment systems. “We all have a role to play.”
For more information about fire containment systems and Thermafiber® mineral wool insulation, or to request an engineering judgment from the Thermafiber Insolutions® team, please visit the website for Owens Corning, found here.
Copyright© 2023 Owens Corning. All Rights Reserved