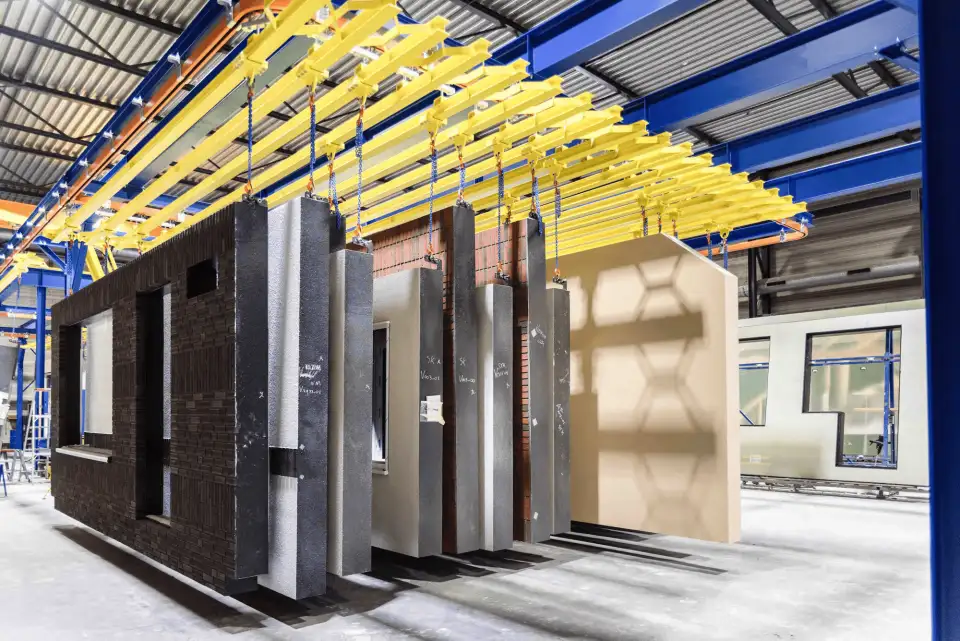
RetrofitNY, NYSERDA’s (New York State Energy and Research Development Authority’s) initiative to scale up deep energy retrofits of multifamily buildings, is moving forward with a refined set of goals for phase 2 of the initiative. RetrofitNY is an adaptation of the Energiesprong approach to industrializing retrofits that was first developed in the Netherlands, has since spread to France, Germany, Italy, and the UK, and has now gotten a foothold in North America. (More on the RetrofitNY initiative here)
The initial phase of this effort saw the creation of six teams with extensive building science experience who undertook proof-of-concept retrofit pilots in low- and midrise residential buildings. Assembling those teams was one of the key phase 1 objectives, according to Christopher Mahase, senior project manager in NYSERDA’s Multifamily Residential program. Mahase is charged with overseeing the RetrofitNY initiative. All six teams produced reports on their progress this past August, which can be found on NYSERDA’s website.
While team building is still a critical aspect of phase 2, says Mahase, lessons learned from phase 1 have informed phase 2 goals. “We’ve added a dedicated emphasis on manufacturing,” he says. “One of the keys going forward is making sure we have manufacturers that have viable products.”
The Energiesprong program in the Netherlands has been succeeding in part because there existed a base of building component manufacturers who responded to the program’s aggregated demand for retrofits by adding to or adapting their product lines. Analyses of Dutch projects show that the cost of essential industrialized retrofit elements has been dropping since 2010—by 37% for prefabricated envelope systems and by 73% for integrated mechanical systems.
In New York the lack of access to specialty retrofit products has been a source of frustration. To quote from a report produced by one of the RetrofitNY teams, which was led by the International Center for Appropriate and Sustainable Technology: “It was NYSERDA’s goal to find or create a market for panel manufacturers similar to those present in Europe, but our extensive efforts failed to identify a single U.S. manufacturer who actually makes retrofit panels.”
Although panels exist for the new-construction market, these panels have a load-bearing capacity that is unnecessary—and therefore not cost-effective—for a retrofit project. A comprehensive, compact mechanical system is another crucial product that so far is missing in action in the U.S. market.
To fill these product gaps, NYSERDA is stimulating the emerging market for comprehensive integrated retrofit components, using a multipronged approach. The agency is working to accurately quantify the market opportunity by such means as updating its multifamily residential baseline study and commissioning more detailed architectural studies of the New York State building stock. Simultaneously NYSERDA is issuing solicitations supporting suppliers. Last October NYSERDA issued a solicitation to design and manufacture what it is calling an energy pod: “An energy pod will meet a dwelling unit’s heating, cooling, ventilation, dehumidification, and domestic hot water needs on a distributed basis in one cost-effective, compact unit.” A separate solicitation is targeting manufacturers of building envelope components to address the need for retrofit panels.
With greater engagement from manufacturers, retrofit costs could become more reasonable, enabling more building owners to undertake the goal of achieving net zero performance in existing buildings. In the first pilots, Mahase was quite surprised at the gap between projected and actual incremental costs. “The incremental costs to achieve an all-electric net zero building averaged $70,000 per dwelling unit,” he says. To facilitate construction, NYSERDA relaxed the prescribed energy use intensity performance targets for the retrofit pilots to 27 kBtu/ft2 per year and is providing subsidy of $30,000–$40,000 per unit to make this achievement more realistic.
The other concession made concerned the agency’s goal of achieving all-electric buildings, in keeping with New York State’s climate goals; at this point all-electric water heating was not feasible for some of the building owners. However, Mahase says that he expects this issue to be solved in the not- too-distant future. In the meantime, the RetrofitNY program is working to leverage all the benefits of electrification, including the potential insurance savings associated with no on-site fossil fuel consumption, because of the reduced risk of fires and carbon monoxide emissions.
Phase 2 of the RetrofitNY program, including the piloting of new technologies and creating a production ramp for engaged manufacturers, is set to kick off in late 2020 or early 2021. Another solicitation will be issued in support of innovative business models in the construction space—ones that can scale up sufficiently to meet the demand for renovating multifamily buildings so that they use at least 70% less energy than previously, and that will movethis sector toward meeting the state’s ambitious climate goals.