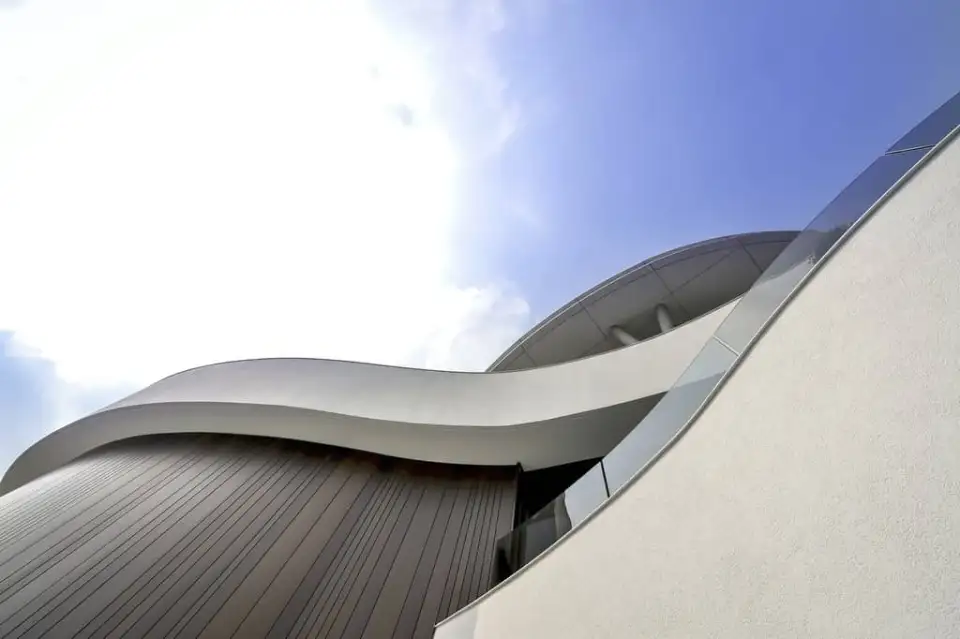
For a building of any kind, the first line of defense protecting its occupants from the elements is the external cladding. It is a critical component of the overall structure that must be designed to ward off wind, rain, snow, cold, heat, moisture, and more.
As an external wall assembly, rainscreens have been around for decades, but advancements in technology have made them increasingly popular. This is due to two key factors—their ability to deliver optimal performance metrics and the flexibility they provide when it comes to design options.
At its most basic level, a rainscreen is an exterior wall configuration on any structure where the cladding is installed such that it stands off from the moisture-resistant barrier on the external wall sufficient for the passive removal of water and vapor. This creates a break between the cladding and the outer wall, an air gap designed to allow for drainage and evaporation. In today’s marketplace, a rainscreen must deliver much more than just protection from the elements.
Architects, specifiers, and designers are constantly weighing competing forces on every one of their projects. They must be able to quantify the anticipated long-term performance of the building envelope such that it will keep the occupants safe and comfortable. When building to Passive House standards, product choices must also account for the demands for greater energy efficiency, enhanced durability, the constant cost pressures to deliver on time and on budget for every project, and the need to create a signature look that will make the building stand out.
Several trends demonstrate how rainscreens are emerging as a preferred solution within the Passive House community and beyond due to their ability to eliminate complexity, achieve cost savings, and deliver on curb appeal.
A System Approach
Cutting-edge ventilated rainscreen enclosure systems are engineered to provide superior weather protection and thermal performance. A successful rainscreen system is comprised of five layers:
· Air and moisture barrier to keep water outside the building. This layer is often fluid-applied, adhere membranes, or factor-bonded with the barrier.
· Subconstruction, or furring, with mounting brackets anchored into substrate to connect the cladding.
· Insulation of varying thickness between brackets, rails, and subconstruction where required by code or as a means to achieve Passive House certification.
· Air and ventilation cavity—the most important layer—that serves as a drain and vent space engineered into the envelope.
· Durable and water-shedding cladding to protect against environmental elements, UV exposure, pollutants, and more.
In the past, contractors and specifiers would bring in a different manufacturer and installer for each of the five layers, complicating the construction process and follow-up coordination. A two-look façade could include up to ten manufacturers—requiring additional documentation and coordination on all levels, multiple warranties to balance, and added scheduling to juggle.
However, that is changing as the success and ease of a system approach rises in popularity. Some manufacturers now offer smartly engineered building enclosure systems that contain all of these control layer components in an integrated and fully tested system. As a single solution, the individual layers work in concert with each other to deliver a holistic approach.
A single-solution rainscreen system also means that architects and builders are dealing with only one warranty and one manufacturer. Designers know the solution does not require them to do additional research and testing to ensure they meet applicable codes and performance standards for certification. Additionally, when the same installer puts on all five layers, there is less guesswork and more certainty in construction leading to less time on site and lower installation costs.
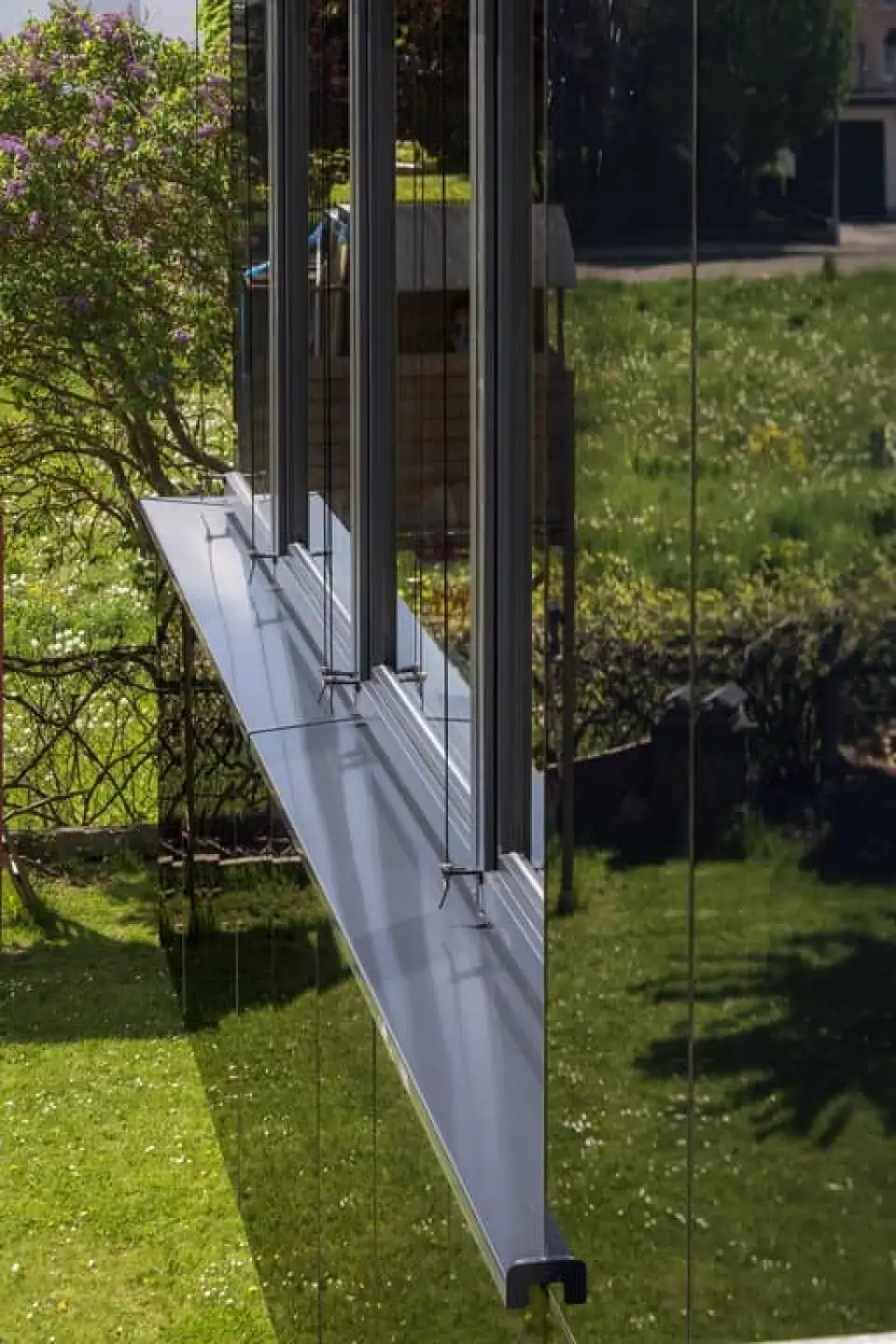
Versatile Aesthetics Brought to Life
The days of creating plain concrete boxes and straight brick exteriors are most certainly in the past. Today, innovation and creativity are a mandate rather than an option when designing a building of any kind. The look and texture of building exteriors are expanding—from an eye-catching entryway to a creative shape that stands out or a colorful logo that places the company’s brand on the building.
Discerning architects and specifiers seek products that have versatile finishes, providing them with design flexibility—everything from coarse textures to ultra-smooth surfaces, all in a variety of colors and materials.
As an example, rainscreen systems that employ glass for the outer cladding layer create even more possibilities for designers and architects to put their signature on the exterior wall while still creating an effective thermal and moisture barrier—even when building to Passive House standards. Opaque glass rainscreen systems use pigments that are fused into the back of the glass, providing permanently colored glass panels that resist wearing, scratching, fading, or water damage.
Incorporating materials such as glass, tile, wood veneer, cultured stone, or novel and sustainable biomaterials into a rainscreen system is on the rise. With the rising desire for unique building facades and the need for high-performance building enclosures, versatile rainscreens are delivering aesthetic appeal more readily and effectively than ever before.
No More Snow Days
When there is a polar vortex, a heavy rain, or extreme heat, construction often slows down or comes to a complete halt on a project. With the rise of panelization and modular construction, however, there are no more “snow days.”
Construction crews can fabricate the exterior walls of a building in a warehouse along a production line, starting with building the stud wall to adding all layers up to the cladding. This may include the installation of a rainscreen system in a factory setting. When using aluminum composite materials or veneer cladding, the cladding can be installed in this controlled environment. For designs utilizing heavier materials such as fiber cement, the cladding can be installed on site to make transportation safer and easier.
Upon arrival, the prefabricated system is installed by crane, further limiting the specialized crews and equipment needed onsite to install the building envelope. Panelization also means onsite air sealing only needs to occur at the seams of the panels and around penetrations. Shop fabrication shortens construction times and gets buildings completed faster, an important advancement as the industry’s workforce shrinks.
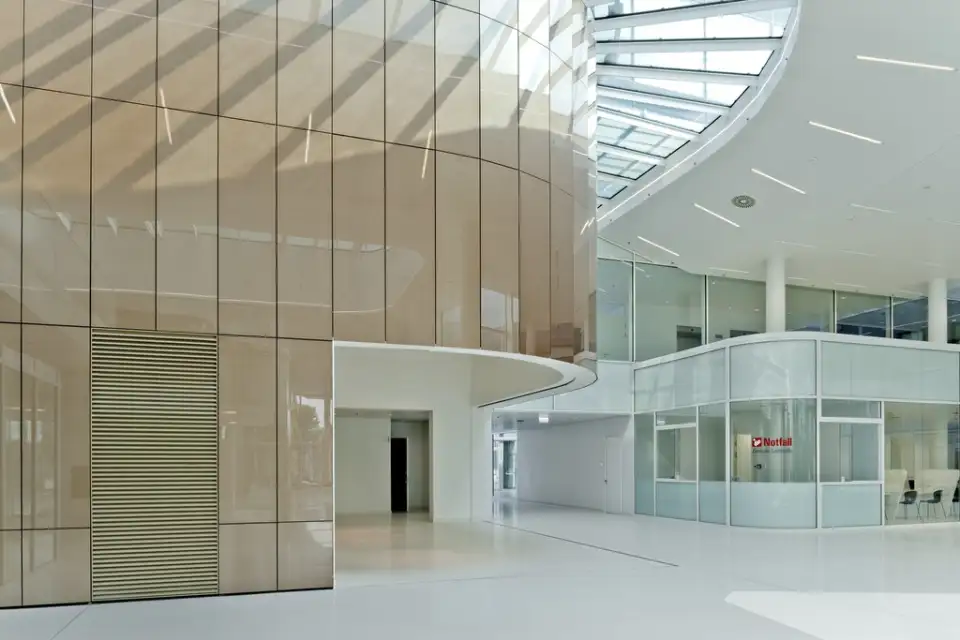
Delivering on All Fronts
No matter the structure, installing the optimal building envelope solution requires an integrated approach that also takes aesthetics into account. The components must work together to manage air, water, thermal, mechanical, and fire performance while simultaneously delivering visual appeal for building owners.
Based on the latest advancements and emerging trends, ventilated rainscreen systems combine durability and functionality with beauty and visual impact. Their inclusion in a project can drive greater energy efficiency for years to come. Their versatility opens up avenues to make the external wall memorable and striking.
Fully tested, integrated systems—installed in the field or in a factory setting—can also drive greater efficiency and cost savings, contributing favorably to a project’s overall bottom line. Taken together, a rainscreen’s value proposition becomes apparent, demonstrating that it can do quite a bit more than simply provide protection from the elements.
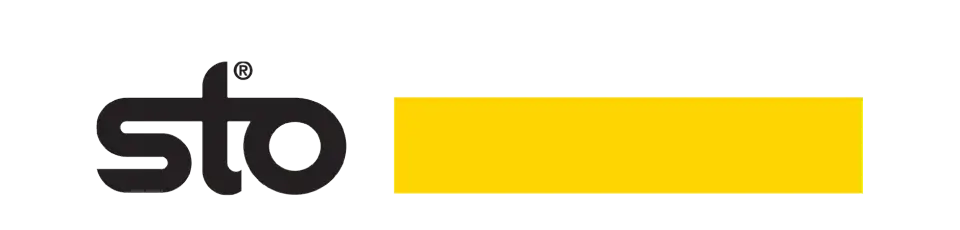