Articles
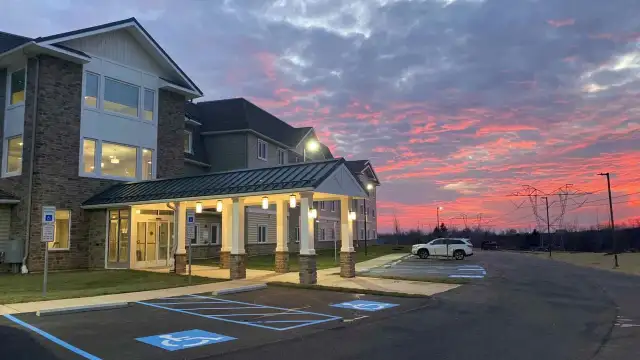
8/15/25
Susie Clemens House: Simplicity Meets Performance in Southeastern Pennsylvania
The modest Susie Clemens House in Hatfield shows that simple forms, proper planning, and the application of passive principles can lead to exceptional performance and comfort for occupants.
Article, Affordable Housing
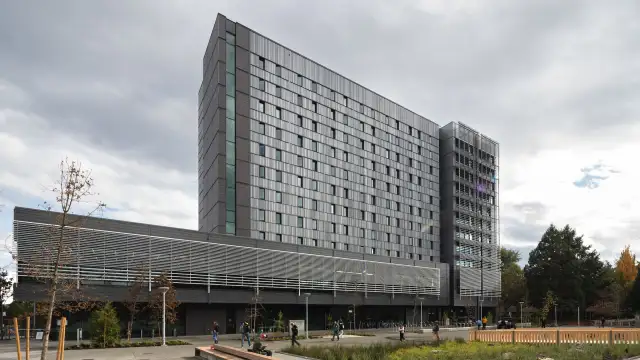
8/15/25
Cascadia Component Spotlight Recap: Versatility and Value in Passive House Windows Systems
We look back on Cascadia's Component Spotlight and dive into case studies for the Ken Soble Tower and Coal Harbor Phase 2.
Article, Fenestration, Sponsored
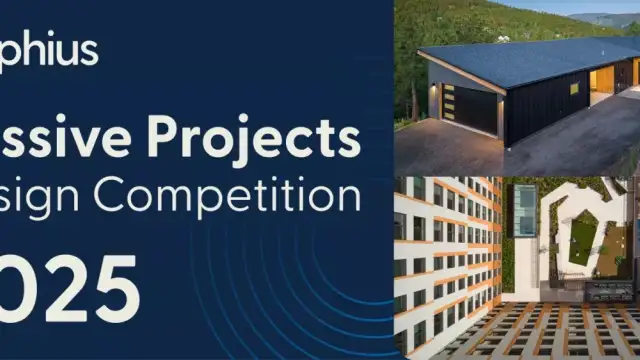
8/13/25
The Phius Passive Projects Design Competition is Back!
A detailed look at the 2025 Phius Passive Building Design Competition, including deadlines, award categories and more.
Article, Phius, News
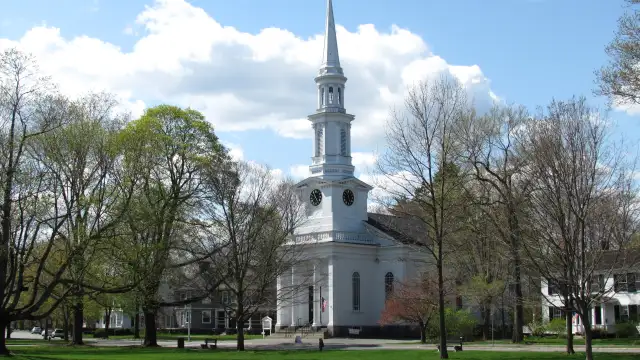
8/8/25
This Massachusetts Town Banned Gas — And Housing Boomed Anyway
Critics say stringent, pro-electrification building codes and restrictions on natural gas will impede housing developers. A Boston suburb is proving them wrong.
Article, Electrification
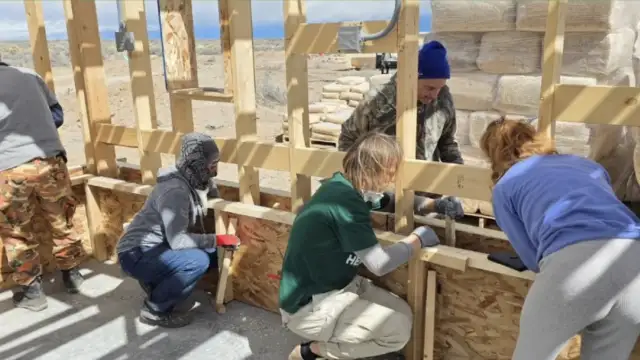
8/4/25
2025 Rocky Mountain Natural Building Conference Is Heading to Bozeman in September
Hosted by the Natural Building Alliance from Sept 18-20, the conference will explore the use of natural materials in high-performance construction.
Article, News, Natural Materials

8/1/25
Majority of Americans Believe Climate Change Affecting Mental Health, APA Poll Finds
The American Psychiatric Association's Healthy Minds poll found that a majority of Americans are either very anxious or somewhat anxious about a host of topics, including climate change.
Article, News
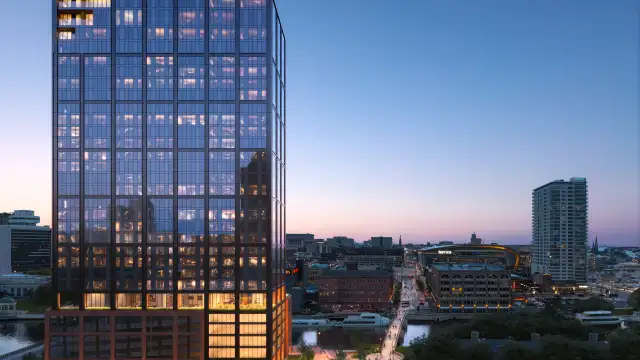
7/25/25
Milwaukee’s Edison Pushes Mass Timber to New Heights
Neutral 1005 N Edison St is pursuing Phius Core 2024 standards and set to become the tallest mass timber building in the U.S.
Article, Mass Timber, Multifamily, Phius
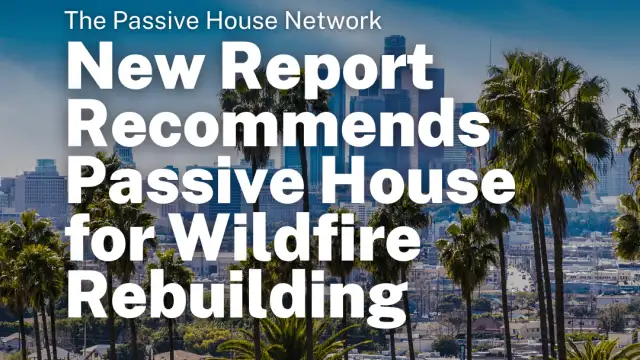
7/24/25
New Report Recommends Passive House for Wildfire Rebuilding
The Blue Ribbon Commission on Climate Action and Fire-Safe Recovery recently published a study finding that Passive House is the best way to rebuild following a major climate disaster.
Article, Resilience
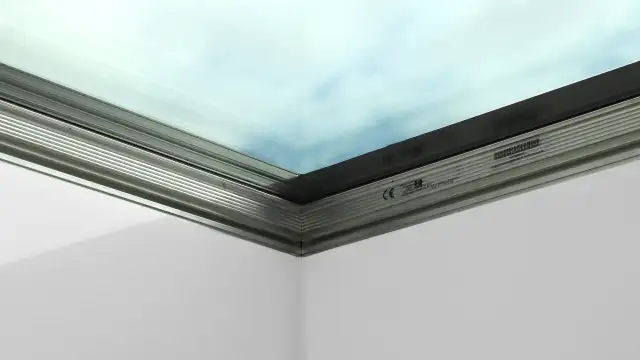
7/23/25
Lamilux FE Skylights: Four Features That Lead to Flawless Isotherm Lines
The Lamilux FE unit skylight is designed for flat roofs and combines sleek design with rigorous engineering to create an elegant skylight with outstanding performance.
Article, Fenestration, Sponsored