Green building conferences always serve as a reminder of how many industries are joining the effort to decarbonize our building stock, and last month’s Getting to Zero Forum in Charlotte, North Carolina, was no exception. Put on by the New Buildings Institute, the event was preceded by NBI’s first annual Embodied Carbon Summit, followed by the two-day GTZ Forum, and it brought together policymakers, engineers, developers, workers from the non-profit sector, architects, designers, and others from across the country who are tirelessly working to reduce operational and embodied carbon.
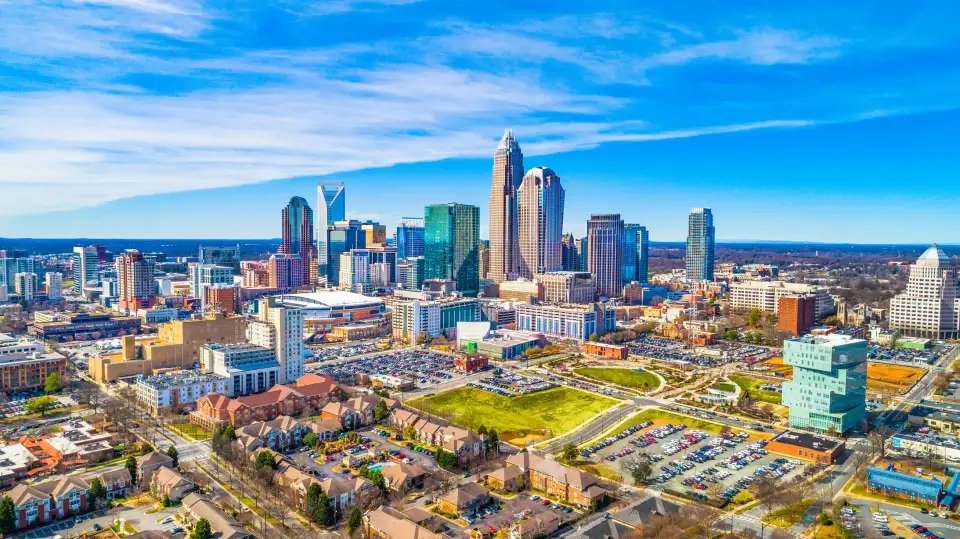
Charting a Path to Decarbonization at the Getting to Zero Forum
Many of the sessions centered on ways to reduce embodied carbon and technologies that can optimize the energy consumption of buildings, but some of most practical takeaway from the event came from individuals who described how they engaged with others to make real progress either implementing local building performance standards or getting private owners to see the value in efficiency improvements.
Local Building Performance Standards: Lessons Learned
Several jurisdictions around the United States have implemented building performance standards that apply to either some or all of their community’s building stock. These standards tend to be far less rigorous than Passive House standards but still create pathways for meaningful improvements that can be realized over the long-term while also generating workable frameworks from which other jurisdictions can borrow and tweak as they see fit.
As two examples, the District of Columbia passed legislation in 2018 designed to reduce energy use 60% across all buildings by 2032, and to become carbon neutral by 2045. Denver implemented a similarly ambitious program in 2021, which aims to reduce energy in all multifamily, commercial, institutional, municipal, industrial, manufacturing, and agricultural buildings in the City and County of Denver that are 25,000 square feet or larger by 2030, and to hit carbon neutrality by 2040.
Representatives from the two jurisdictions—Sharon Jaye, building performance policy manager for Denver’s Office of Climate Action, Sustainability and Resiliency; and Branch Chief for Building Performance and Enforcement in the Energy Administration at the District of Columbia Department of Energy & Environment Katie Bergfield—provided invaluable advice about the process of enacting building performance standards at the local level. For Jaye, one of the more specific pieces of advice that may not seem totally obvious was the importance of speaking with attorneys early on in the process because they will ultimately be responsible for finalizing the language of the policy. While Jaye said it's not necessary to teach them all the nuances of building performance standards, having some familiarity with building science and how standards have been implemented in other communities can help avoid ambiguous phrasing. English that’s been run through the meatgrinder that is Legalese can lead to misunderstandings, and that it’s important to engage with attorneys during the drafting process to ensure both parties agree on the plain English meaning of specific passages. This lesson should be taken to heart by engineers and architects who help draft policy.
Addressing Stakeholder Concerns
Senior Market Transformation Manager Debbie Driscoll of the Northwest Energy Efficiency Alliance spoke next during this session, focusing on the needs and wants of private owners in the Pacific Northwest. What was enlightening about Driscoll’s presentation was not that owners see new performance standards as being disruptive to business as usual or that many firms may simply accept the fines for noncompliance rather than make the necessary upgrades to their building. While unfortunate, it has been widely reported.
Rather, the main takeaway from Driscoll’s presentation is that many owners, particularly owners of commercial buildings and market-rate multifamily buildings, are not simply rejecting efficiency upgrades as a kneejerk reaction to what they perceive as regulatory overreach, nor are they skeptical that efficiency upgrades and deep energy upgrades will eventually produce a return on their investment. At the end of the day, they are interested in running a profitable business and reducing risk. They want better proof-points that energy-efficient solutions will translate into fewer vacancies, better tenant retention, and higher rents. To allay their concerns and assure them that improvements are not risky investments, it's best to present them with solid evidence that payback will occur in a period that makes financial sense to them.
If you can show that upgrades translate into improvements in the metrics they care about, they will be more receptive to making the upgrades. Somewhat analogous to the point above, it’s important to speak the language of stakeholders when getting them on board.
Con-Edison and Non-Pipes Alternatives
One of the more ambitious programs that was described during the two-day conference came from an unlikely source: Consolidated Edison of New York, a utility company servicing New York City and most of Westchester County. The utility company has designed two programs under their Non-Pipes Alternative Implementation Plan: the Area Load Relief Program and the Electric Advantage Program. The presentation by Mark Brescia, clean energy program manager for Con-Ed, and Julie Liu, president of Centsible House, focused on the latter program.
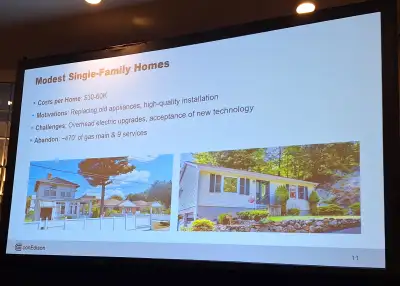
Con-Ed is responsible for nearly 4,500 miles of gas mains in the area. Given that demand for gas will decline in coming years, while the costs associated with maintaining this infrastructure will remain the same (or possibly even increase), the utility company has realized that it is more cost-effective to identify leak-prone pipes that can be eliminated, pay for the full electrification of buildings connected to the pipe, and then proceed with the elimination of the gas main. In other words, Con-Ed is literally paying to electrify and retrofit entire buildings to eliminate parts of their gas distribution system. Firms like Liu’s are then responsible for performing the conversions, which often involve not only the installation of electric appliances, domestic hot water systems, and heat pumps, but also upgrades to building envelopes and wiring. When appropriate, they will even remove oil tanks.
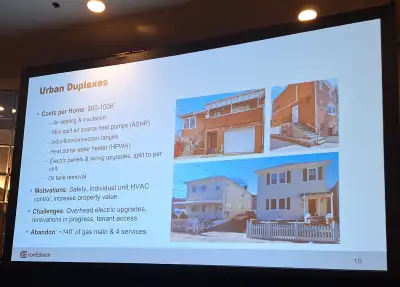
The cost of these upgrades runs from $60,000 to $100,000 for duplexes in Queens and the Bronx, and they can be as low as $30,000 for modest single-family homes, according to Liu. Again, the costs for these improvements are covered by the utility company.
At this point in time, the program is extremely small and only offered to customers who are connected to the most remote parts of the distribution system (oftentimes on dead end streets). Moreover, all customers connected to any specific main must agree to the conversion before the main can be removed, requiring intensive outreach to individual customers. If it proves successful, however, other utilities may recognize the financial prudence of eliminating gas infrastructure rather than maintaining it, which may accelerate all-electric conversions.
Producing a 21st Century Labor Force
One of the issues that was perhaps not formally addressed but was the subject of many conversations between sessions was the need for upskilling across industries. As the standards to which buildings are constructed become stricter, those who model, design, and build these structures will need to learn best practices in their field. Unfortunately, workers across the AEC industry are lagging behind in training, resulting in added delays and costs of projects, especially outside of major metropolitan areas. While Boston and New York City may have no shortage of people capable of building to even the most rigorous standards, the number of qualified individuals drops precipitously once one leaves these markets, frustrating efforts to normalize the construction of high-performance buildings. Without proper engagement and efforts to provide affordable or even free training to workers, many stakeholders may decide that non-compliance is a better business decision than upskilling or finding qualified people to do the job.
It doesn't have to be this way. There are numerous federal funding streams via the Inflation Reduction Act and the Bipartisan Infrastructure Law that are opening to help create a 21st century workforce capable of constructing healthy and efficient housing, and these sources of funding will be routed through state programs that are still being developed. What will be interesting to see is if the decarbonization movement will be able to take the training programs that were successful in places like New York or Boston or Chicago and recreate them in places like New Orleans, Boise, and Charlotte.
If conferences can serve as a reminder of how many industries are joining the effort to decarbonize our building stock, they also serve as reminder of how many people have invested their time and energy to transforming what we build and, more importantly, how we build it. There is no doubt that we have a wealth of knowledge and expertise; what remains to be seen is if we can spread it and create a decarbonization movement that is truly nationwide.