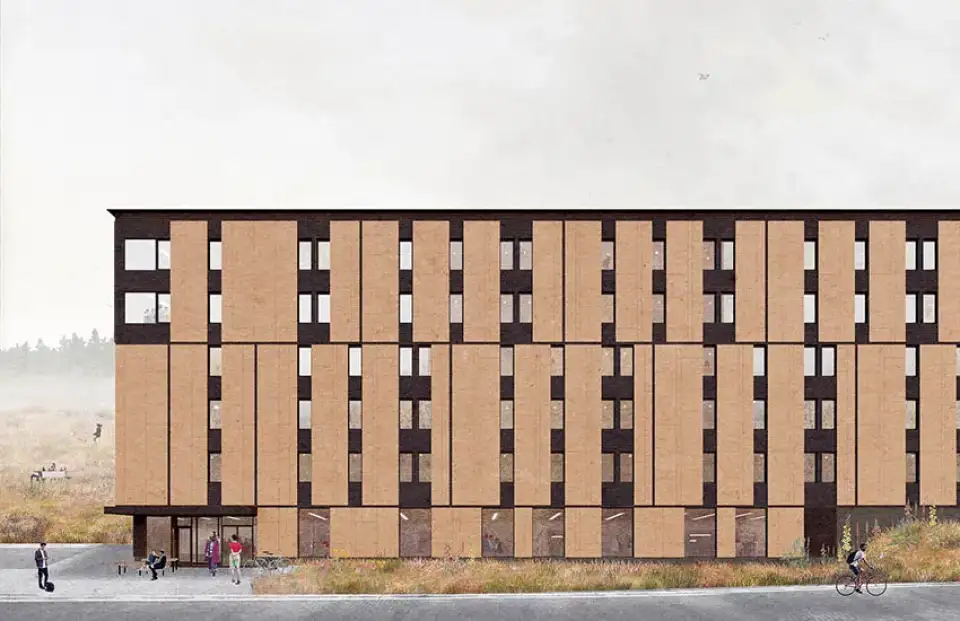
As a global leader in sustainability, the University of British Columbia (UBC), no longer satisfied with minimizing harm, is moving toward net positive contributions to environmental well-being. UBC acts as a living laboratory by integrating its academic—research and teaching—activities with operational mandates.
A major part of UBC infrastructure is student housing. With 12,000 students living at the Point Grey campus and more than 2,100 beds at the Okanagan campus in the near future, the university has become an industry expert in this building typology. Along with this expertise comes the ability to take well-assessed risks such as UBC Okanagan’s new Skeena Residence for students, which is aiming for Passive House certification. Skeena is an expression of applied sustainable building research, and as such will benefit other universities, municipalities, and communities.
Designed by PUBLIC Architecture + Communication, the Skeena Residence will provide 220 bedrooms and amenity space across six floors. Completing an ensemble of residence buildings that encircle a large common green space, the project focuses on student life and support services while synching up with the existing campus. The architecture team understands that student residences aren’t just for sleeping. In the design for this typology, a balance of academic priorities and recreation is important. On the first level, Skeena Residence has a large laundry room in close conversation (a glass wall separates them) with adjacent lounge and social spaces. The relationship between the two spaces encourages chance meetings and happenstance gatherings. Moreover, the transparency offers passive surveillance, or visibility that promotes a sense of security. In short, the design of the building supports community life.
To further maintain safety and privacy, the upper five floors contain the residence apartments, semiprivate living, and study areas. Each of these five floors contains a homey house lounge with views of the surrounding mountains and a kitchenette, dining table, and couches, and—to keep unlike activities acoustically separated—a study room at the other end of the building.
Design Influences
Ultimately, Skeena’s design was driven largely by the programmatic requirements. The neighboring student residence had a proven layout of two bedrooms separated by a shared bathroom. The layout of this module was repeated for Skeena within an optimal building length, width, and number of floors—optimal being determined by the least amount of energy required to heat and cool the building while also delivering the requisite number of beds.
This Passive House goal of minimal energy use for heating and cooling also shaped other design choices. Given that ornamentation is tricky to insulate effectively, a simple form without irregularities such as corners, steps, overhangs, or canopies performs best. Mechanical systems also work best within a narrow, contiguous box. This limits aesthetic parameters to material, color, pattern, and texture. The simpler the building, the more important material choices and detailing become to the design.
To preserve responsiveness to budgetary concerns, the architectural team designed the Passive House wall assembly like a jacket—or, as students might say, a beer coozy —in the sense that it can simply be removed. Structurally the same as a conventional building, Skeena’s skeleton allowed for the potential subtraction of the Passive House elements without hiccups in cost or schedule.
Design decisions are also swayed by other practicalities, such as standard and locally available materials and techniques. The building is 80% wood-framed, with some concrete on the ground floor. A wood structure was chosen for its inherent insulative properties as well as its ready availability and ease of construction.
The Building Envelope
Designing multiunit buildings to the Passive House standard presents a unique set of challenges and opportunities, and PUBLIC Architecture + Communication was grateful to have the assistance of a team of Passive House professionals from RDH Building Science, led by Monte Paulsen. More than with conventional building methodologies, the integrated design process is vitally important to achieving Passive House. Conventionally, a design process begins with broad strokes and with each successive iteration becomes increasingly refined, ending with details. Passive House, however, inverts this process.
The process for Skeena required accelerated decision making and involved a heavier workload during schematic design. For example, understanding thermal bridging implications and other Passive House success factors necessitated front-loading assembly and junction detailing. These details were also critical for determining if Passive House heat recovery units could service the project, or if cooling would be required in the Okanagan climate.
However, the good news was that working through these problems in the beginning achieved significant time and cost savings in the long run, most importantly by preemptively avoiding changes late in the process. Late changes are more consequential with Passive House, due to its holistic design approach. Any change of a component will alter the energy performance of the entire building. In initial phases, any increased energy demand caused by, for example, swapping out a window could be made up for by increasing insulation or by making other alterations to balance efficiency. However, a proposed window change during construction would have taken up to five weeks for research, evaluation, and sign-off of all consultants. Additionally, as the components are more specialized and the supply chain is more spread out, getting Passive House-quality products usually requires longer lead times, especially for products that are shipped from abroad.
Working out the detailing of the mechanical systems early on was also vital to preserving the schedule and budget. All of the pipes for mechanical servicing required more insulation than is the case in a conventional building. Adding just a few inches of insulation to pipes can require custom wall and floor assemblies at a significant expense. Instead, because of the integrated design approach that we used, we were able to maximize the amount of insulation possible for the pipes while still fitting within typical assemblies, adjusting other building components to achieve the project’s energy goals.

Mechanical Approach – AME Consulting Group
For the mechanical engineers, aiming for Passive House certification also means engaging in the integrated design process much earlier than is typically the case in a conventional construction process, as well as additional coordination with the other team members throughout the project. That extra insulation on the hot water pipes affected more than just the floor assemblies. The Passive House emphasis on maximum efficiency from all sources and details translated into reduced heat loss from the pipes and, not incidentally, minimized the need for air-conditioning. Domestic hot water is being supplied by heat pump water heaters, a relatively new technology for some that required extra planning.
The most obvious difference when designing the mechanical equipment for a Passive House building lies in its much lower peak heating demand than a typical building would have, which makes conventional heating equipment inappropriate. A less- obvious consequence is that specifying and ordering right-sized equipment brings a project to a mechanical point of no return—in terms of committing the project to achieving its Passive House targets—much earlier than other design aspects might.
Further Complexities
The density of students in a Passive House student residence necessarily presents further challenges. With a student population comes a far greater number of fridges, hair dryers, and computers per square meter than are found in a typical midrange residential building. These appliances create an enormous plug load, or electrical draw.
To further the complexity of student residences, when students aren’t chilling drinks, drying wet hair, or researching on their laptops, they are conducting humidity-intensive activities such as showering. To combat the excess moisture, air circulation is completely renewed every three hours via highly efficient mechanical systems, thus warding off the threat of mold. Ventilation air is provided by heat-recovery ventilation units. Despite its high energy demand, the Skeena Residence has not required hookup to the available gas connection or to the roughed-in connections for a PV array.
The Victory Lap
The Skeena Residence is a victory, particularly given the extreme seasonal temperatures at this UBC campus. Not only is the project expected to achieve Passive House targets when complete, but the building systems are expected to perform within the anticipated conditions of climate change.
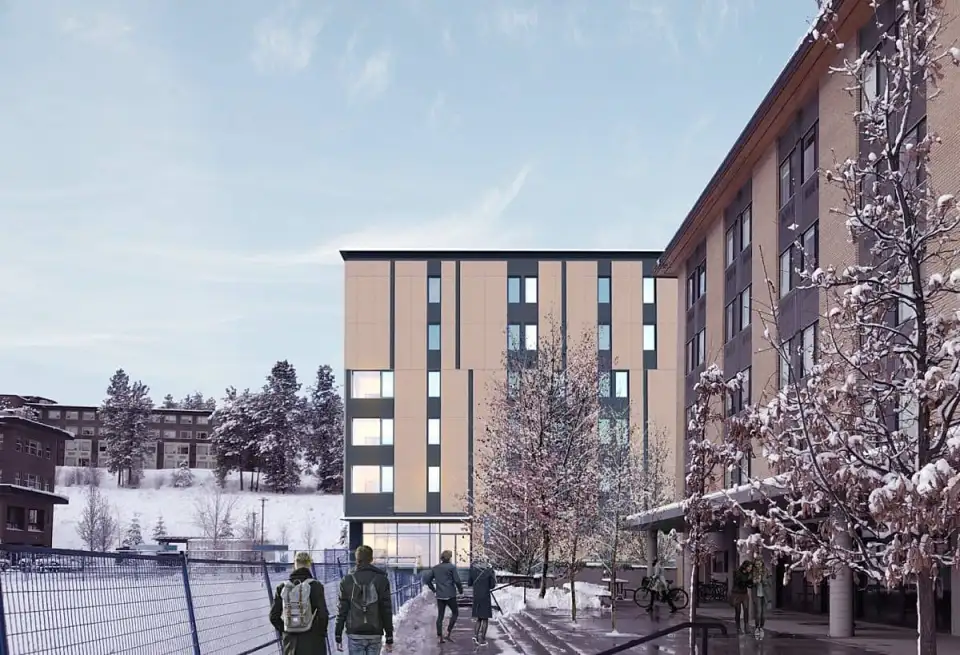
Box: Lessons Learned
Skeena is built into an existing context that did not have the same parameters as those required by Passive House. This sets up unrealistic design expectations. To counter these expectations, our team allowed for time to educate and inform the client and user groups.
Construction of the wall assembly is new—and therefore challenging—to many tradespeople. To offset this learning curve, RDH Building Science, the envelope consultant, offered on-site workshops focused on Passive House construction.
Some key components of Passive House building have long lead times. To avoid schedule delays, it is advisable to pre-tender key components such as HRV units and triple-glazed windows.