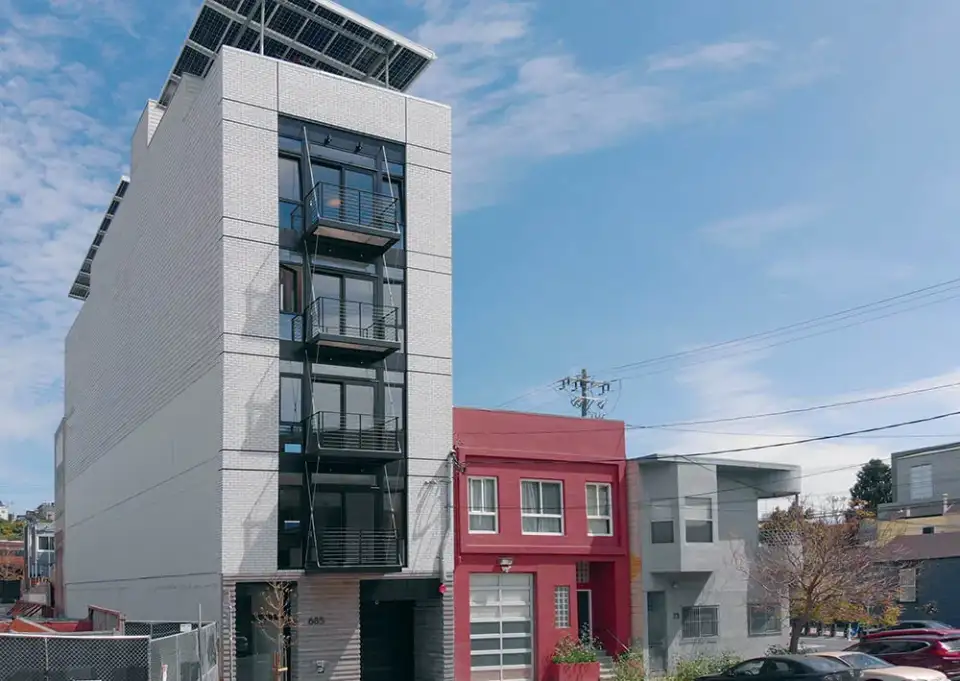
Sol Lux Alpha is the first Passive House certified multiunit nanogrid development in the United States. A nanogrid is a self-contained energy system that is islandable from the grid. Each of Sol Lux Alpha’s four condominiums is 100% powered by renewable energy solely from the PV system over the building’s roof deck. As such, the six-story building pushes the vertical limit for fully site-powered PV building design. The units are actually projected to generate excess power that can be used for electric vehicle (EV) charging, or can be paid back from San Francisco’s Clean Power excess generation tariff of $.089/kWh. Each unit, plus the common area, has three Tesla Powerwall energy storage systems. These systems allow the unit to remain fully functional if the grid goes down, or if the owners simply choose to disconnect. Energy and building science experts and industry professionals have travelled from as far away as Switzerland and Australia to learn more about Sol Lux Alpha.
The initial inspiration for the Sol Lux Alpha nanogrid system came to designer-builder John Sarter in late 2009. Motivated by the Yokohama Smart City project, a citywide consortium dedicated to optimizing energy supply and demand, Sarter looked for such projects in the United States and found nothing comparable. He decided to see what could be accomplished with a single building, while also introducing the idea of distributed solar PV coupled with energy storage systems in policy, energy, and the built-environment sectors. An interconnected group of nanogrid living units, combined with community-distributed energy resources, is the essence of a microgrid community.
The first nanogrid design by Sarter and his firm, Off The Grid Design, was a passive-solar home in Marin County, California. The home was designed to provide two EV charging stations in a semidetached garage. The work he saw in Japan inspired him to reach higher than EV charging. While designing this initial project, Sarter also attended a presentation on Passive House methodology. It seemed logical to him that a larger structure with a lower ratio of internal volume to surface area would be a more economical model for a Passive House certified nanogrid building.
The partnership for Sol Lux Alpha solidified when Sarter convinced first-time developer Lloyd Klein, owner of the project’s 25-foot by 100-foot lot, of the value of carbon-neutral living. Sarter said he believed he could get a 25% rear yard setback requirement waived if they brought to the San Francisco Planning Department a project with a high level of sustainability. Klein said, “If you can do that, I’ll build it with you!” When Sol Lux had its community meeting prior to approval, there was initially some pushback by the local community about the project’s height, the massing, and the full lot coverage. When the team told the neighbors that building would be net zero and carbon neutral, the negativity dissolved. The city was also receptive, granting the setback exception and entitlements in a record six months. By comparison, it took a developer with an adjacent property three and one-half years to receive his entitlements.
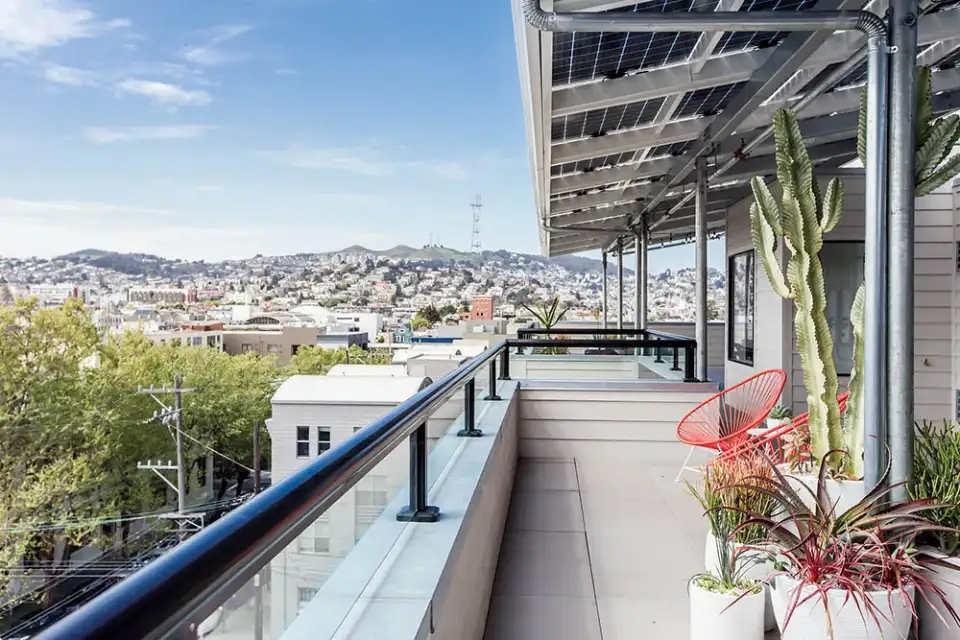
The Sol Lux Alpha team decided on Passive House certification through PHIUS, drawn by its partnership with the U.S. Department of Energy’s Zero Energy Ready Home certification. The four condominiums are certified by both organizations, and the building is the first PHIUS+ Source Zero multiunit development in California. This combination of certifications enabled Sol Lux Alpha to achieve an Alternate Path of Compliance to San Francisco’s rigorous Green Building Code, the only one granted to date.
Having decided on Passive House certification, the project team had to select a construction method. It ended up choosing prefabricated panels, because of the anticipated precision, schedule, and cost reductions, and because it would be difficult to build with stick framing on the relatively narrow zero lot line site. As it turned out, finding a reliable prefabrication supplier was a challenge. After two false starts, the team settled on an Oregon supplier that partially stick framed the panels on a warehouse floor, which didn’t initially provide the precision the team was expecting.
The panels had to have a two-hour fire rating inside and out. From the outside in, they consist of cementitious siding, a liquid air barrier, two layers of 5⁄8-inch fire-rated board, ½-inch plywood, and 2 x 6 studs. They were finished on-site with dense-packed cellulose and two layers of 5⁄8-inch drywall. The rim joists also had to be included in the prefabricated walls. All exterior wall lumber had to be treated with liquid borate and then air dried for fire prevention. With a maximum length of 16 feet, a panel could weigh as much as 1½ tons, creating challenges when stacking panels on the floors prior to lifting and placing them with a crane.
During assembly, silicone gaskets were placed under the bottom plates and vertically between panels. A continuous bead of subfloor glue sealed the perimeter plywood edges to the envelope boundaries. Because the concrete podium was not precisely leveled and the panels were not fully constructed with precision milling equipment, some of the first panels didn’t fit as precisely together as planned, creating some interesting air-sealing challenges. Sarter spent time at the facility in Oregon training the crews, which improved the precision and air sealing on the upper floors.
Because of the weight and the building height, the panels had to be placed by crane. Since the building essentially covered the site and had no side or rear access, a very large mobile crane had to be placed in the street, requiring a special permit and shutting down the street for each floor lift. In retrospect, according to Sarter, the team probably did save some time and money as intended by using prefabricated panels, but it lost those savings in the complexities of having to assemble them by crane in a dense urban environment.
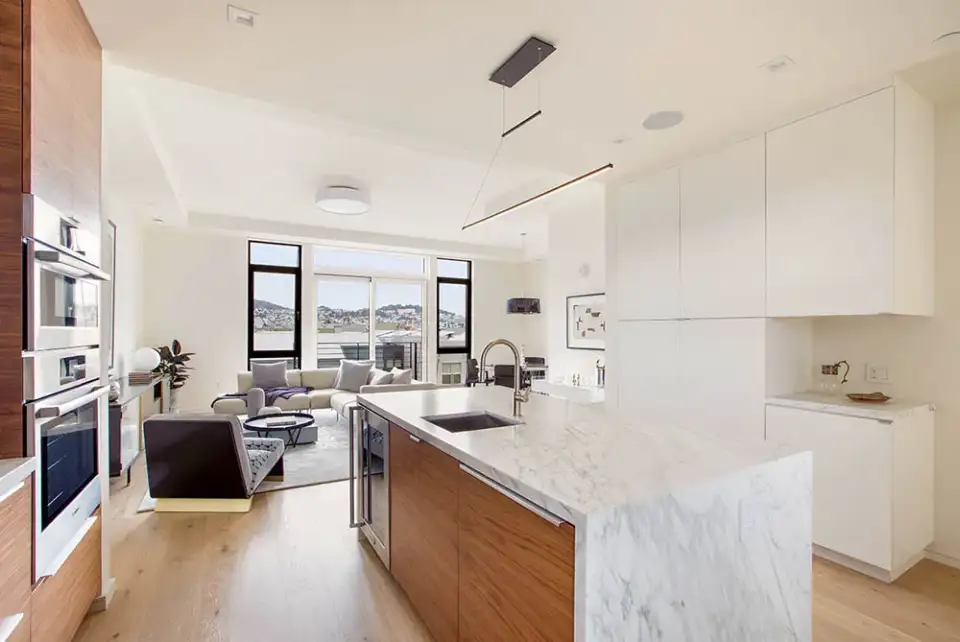
The remainder of the project is a fairly typical Passive House building, configured as four stacked condominiums over a garage. The efficiency created by a lower interior volume- surface area ratio, plus the mild California climate, helped the project reach Passive House certification using standard platform framing. Additional benefits included double-pane Passive House certified European windows and an absence of exterior insulation. The kitchens are all-electric, including an induction cooktop. Each unit has two ducted mini-split coils for heating and cooling and a heat pump water heater. The building and power systems are simple and reliable. You can set it and forget it, or customize the way the energy storage system interacts with the grid. Owners can take advantage of time-of-use rates and EV tariffs to generate income from the excess generation or use it for nighttime EV charging. The elevator and stairs are outside the conditioned space. This presented some challenges locating airtight ADA- and fire-rated doors that didn’t complicate the blower door testing.
A major goal of the project is to show off the multiple advantages of a carbon-neutral lifestyle. The units are very quiet and have excellent indoor air quality, due to Passive House-level air sealing and energy recovery ventilation. All have the accouterments of a luxury San Francisco condominium, in an 1,800-ft2, three bedroom, three-bath unit. The elevators open directly into each unit with an electronic fob, creating a very private feeling.
The roof deck, which includes kitchen, dining, and lounge areas, is bathed in filtered sunlight from a bifacial solar array. Bifacial technology boosts the 380W nominal output by up to 30%, to almost 500 watts per panel. Each unit’s batteries store up to 41.5 kWh, which can power a condominium for two to three days without recharging, due to the efficiency of the building’s systems. Since the PV is recharging the batteries daily, the units can potentially run off-grid indefinitely. As a test, the entire unoccupied building ran off-grid for over three weeks, generating a substantial excess of energy every day. It will be interesting to see the yearly results of a fully occupied structure. The common areas and elevator are powered by a separate set of batteries capable of storing 24 kWh. They provide commercial-grade three-phase power for the elevator through a triple-inverter configuration.
This ambitious project realized a series of firsts: the first multifamily building and Certified Passive House for Sarter, who had been designing and building single-family homes for years; the first ground-up construction project for codeveloper Klein; the first Passive House project for the architect; the first Passive House certified multifamily nanogrid project in the United States; the first San Francisco project allowed to use an Alternate Path of Compliance Passive House certification; and the first PHIUS+ Source Zero multiunit development in California. Having faced and solved significant design and construction challenges, all the team members are gearing up to work on new Passive House and nanogrid projects in the Bay Area and beyond.
Now that the world is witnessing devastation due to global climate-related events, the value of combining renewable energy and storage is becoming more evident. The vision of the Sol Lux Alpha team and others is slowly becoming a global reality. Adoption in the United States is lagging behind many other parts of the world, but there are now many projects in development across the country. Sarter’s goal is to help the United States become more of an innovative and technological leader, moving the ball forward in the areas of building efficiency and microgrid development.
Heating energy |
Cooling energy |
Total source energy |
Peak heating load |
Peak cooling load |
Air leakage |
---|---|---|---|---|---|
4.1 kBtu/ft²/yr |
0.6 |
31.4 |
2.5 Btu/hr/ft² |
0.3 |
0.5 ACH50 |
Courtesy of Compass, Joseph Schell Photography