
To most casual observers in Saugerties, New York, the Burt Street Apartments appeared to be undergoing little more than an installation of new siding. On closer inspection, however, a more expert eye would notice that there was nothing standard about the construction work undertaken on this 12-unit, 4,284-square-foot structure. In fact, the Burt Street Apartments are a test case for what could be a revolutionary new approach to “deep energy retrofits” on smaller multifamily residential buildings that could have wide application for other commercial structures while making many of the principles of Passive House design (like continuous insulation and thermal-bridge-free detailing) the industry standard.
As part of an evaluation of potential cost reductions in retrofit techniques spearheaded by the New York State Energy Research and Development Authority (NYSERDA), the project is an experiment to determine the viability of retrofitting buildings with a prefabricated lightweight panel adding continuous insulation (ci) and air barriers. The panels – a major focus of the study – comprise a cladding of exterior insulation and finish system (EIFS), and are being reviewed by NYSERDA for energy savings, installation costs, and impact on building enclosure tightness.
In this way, NYSERDA can report on the effectiveness of adding substantial amounts of insulation to exterior walls (with targets of about R-24) as part of its efforts to evaluate a variety of techniques for deep energy retrofits, where the effort is meant to significantly reduce the energy use of existing buildings.
The A.R.T. of the reStore™
A: Aesthetics
R: Repair
T: Transformation
The Levy Partnership of New York City, the designer on the project, collaborated with Sto Corp. as a key partner, specifying the Atlanta-based company’s Level 3 Overclad using StoLite Panel for the facade restoration project. The main focus of the project is to evaluate:
Impact on heating and cooling energy use.
Improvements to air tightness of the building envelope.
Effect on project cost.
To make these assessments, The Levy Partnership is comparing pre-retrofit energy bills with utility bills for the 12-month period following the retrofit, with adjustments for differences in weather in both periods. In addition to measuring for energy savings, the team will use blower door testing before and after the new cladding is installed to measure for air infiltration and loss. Last, the construction process is documented – starting at panel manufacturing and going through closeout – both to determine the total costs and to identify ways to streamline the retrofit process.
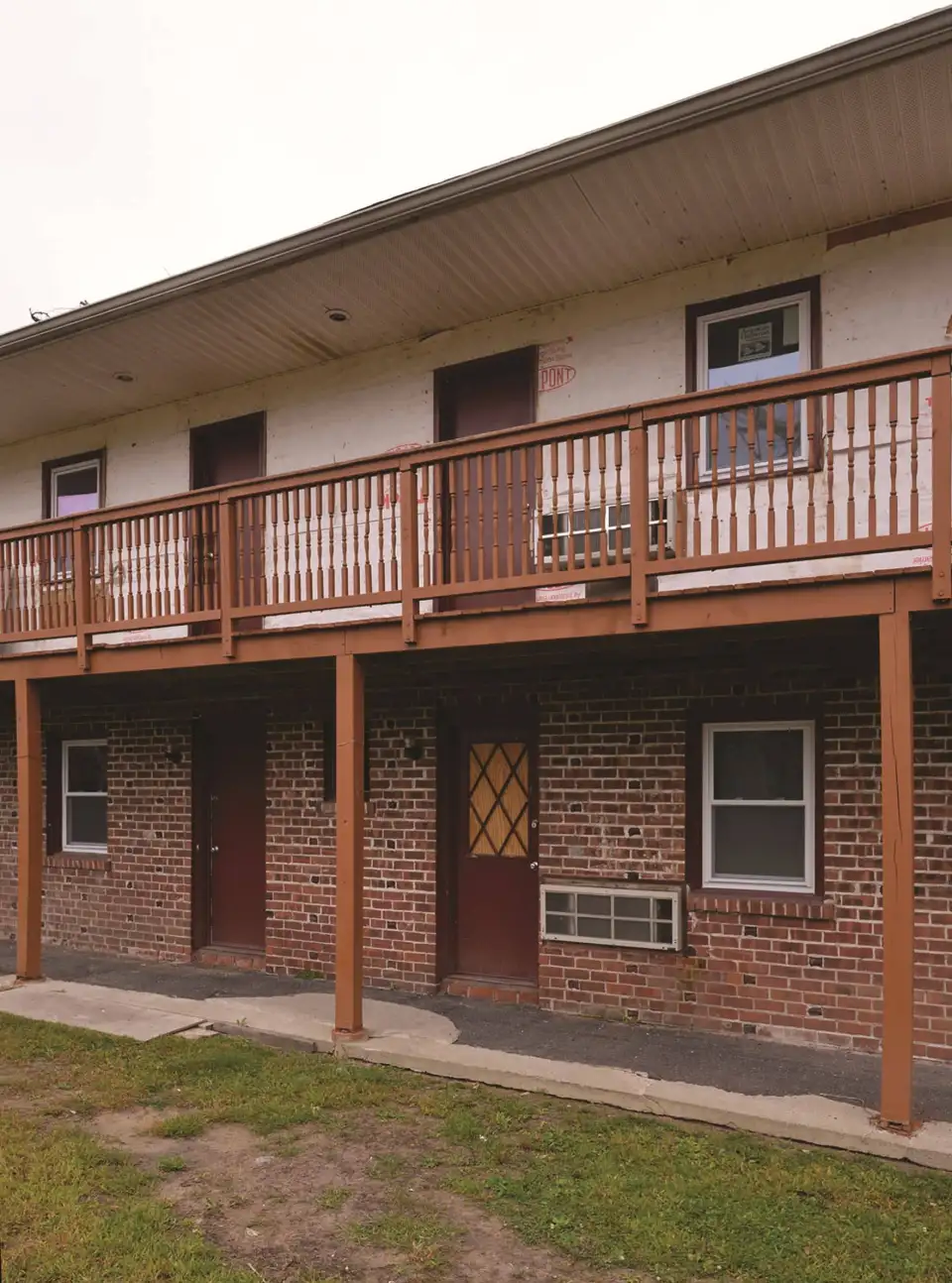
A technology whose time has come
Behind this project – modest in scale, yet groundbreaking in its approach – are decades of work in the building industry to improve energy efficiency. Great strides have been made in the creation of efficient new envelopes and cladding systems, leading to a new generation of energy-efficient green buildings. For existing buildings, which account for most commercial and institutional construction projects, many have now turned their focus toward the retrofitting of existing structures to achieve a comparable level of performance to the new, super-efficient projects.
The concept of a deep energy retrofit -- in which integrated design and systems thinking are used to achieve much larger energy savings than conventional energy retrofits -- has taken hold. But as Jordan Dentz, research coordinator for The Levy Partnership, explains, “The difficulty with a deep energy-retrofit process is that it is often fairly labor-intensive and site-specific, which means that while savings can be significant, the cost is equally high.”
A simple example of wall insulation proves his point: construction crews have to remove exterior cladding and interior wall materials, lay in or blow in new insulation, and then apply weather sealing. After this, installation of new, custom-built cladding systems may be required. In most cases, the vital aspect of envelope improvements for the deep energy retrofit may be too cost-prohibitive for many building owners and homeowners.
Not surprisingly, groups like NYSERDA, which has consistently focused on promoting best practices in energy efficiency, have had the goal of changing that relationship between retrofit cost and meaningful achievements in building envelope efficiency.
“The Burt Street project in Saugerties is part of a broader project to demonstrate and document a variety of different and innovative approaches to reducing the costs of exterior insulation retrofits,” says Bob Carver, one of the heads of NYSERDA’s Buildings Research Group. To that end, the agency gave the green light to The Levy Partnership’s recommendation with Sto Corp. to show how to achieve the significant performance benefits of continuous exterior insulation and liquid-applied barrier membranes, with an easy-to-use, panelized system that can be transported to job sites and adhered or hung over (or in place of) existing, sub-par cladding.
The particular system employed for the project exterior (StoLite Panel) is manufactured with an expanded polystyrene (EPS) core covered with a durable, aesthetically pleasing finish. The lightweight panels are manufactured in a controlled facility for uniformity and consistent quality. Each one weighs about 1.5 pounds per square foot, with special shapes such as corners made to specifications. Unlike a similar field-applied system, StoLite Panel does not require tenting or heating in cold weather.
On the jobsite, this complete enclosure system is attached to the building’s sheathing or masonry exterior using a combination of mechanical fasteners and adhesive. The off-site fabrication and nonstructural nature of the StoLite system makes it effective for situations where installation speed, minimal occupant disruption, and construction quality are critical, says The Levy Partnership’s Dentz. “It’s lightweight, easy to carry around, doesn’t impose much load on the building,” he explains. “And it’s prefinished, making installation a one-step process.”
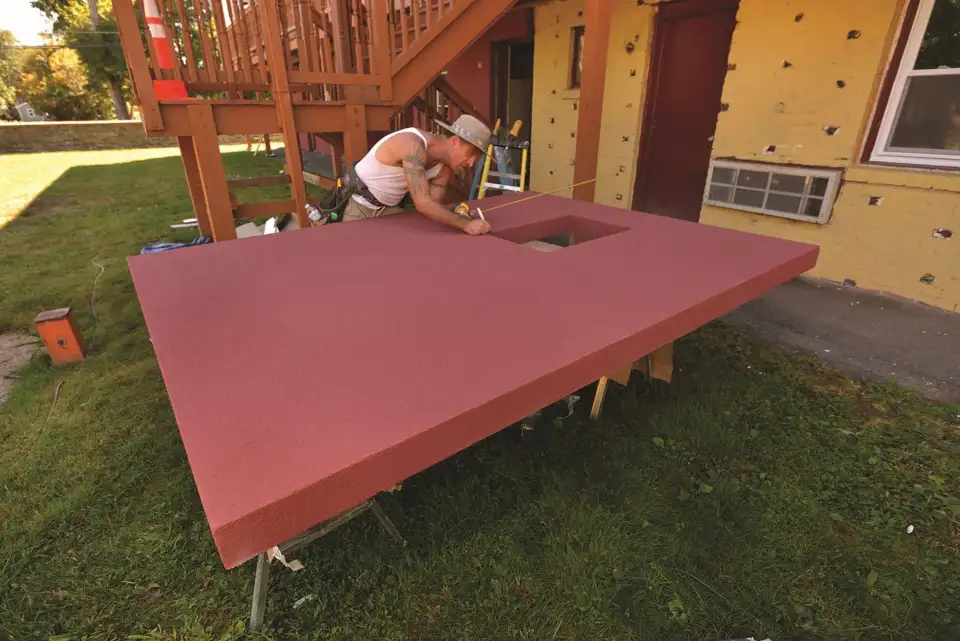
An ideal test case
The Burt Street Apartments seemed ideal to demonstrate the application of a prefabricated, prefinished wall system on an existing residential structure. The low-rise multifamily structure also represents a valuable test case for cost reduction in an exterior insulation retrofit
Containing 12 units of affordable housing, the building required about 4,000 square feet of exterior cladding, with brick cladding on the first floor and vinyl siding on the second, both over a 2 x 4 wood frame with 1.5-inch fiberglass batt. According to the project designers, the original systems were poorly installed – although Nevien Sidarous, AIA, the building’s current owner, has been strongly committed to energy efficiency and had already carried out several retrofit measures. Sidarous had recently replaced the mechanical systems and added floor and ceiling insulation. She even installed a photovoltaic (PV) system to reduce utility bills. However, she had not yet addressed the exterior walls, says Dentz, “the one part the owner and contractors didn’t really have a good solution for. So the walls remained very poorly insulated.”
Given these circumstances, The Levy Partnership saw that the exterior wall retrofit could be carried out as an independent step using the current conditions as a baseline. By analyzing the effects of the facade system -- in isolation -- they could provide a clear view of the envelope retrofit’s energy and cost benefits.

Basic recladding approach
The project design was fairly simple, according to The Levy Partnership: The siding on the second floor was removed, while the brick veneer on the first floor remained in place. The 4-inch-thick system was installed over the plywood sheathing on the second floor and over the brick on the lower floor on all sides. This was followed by caulking.
Performing the work is Malcarne Contracting of Rhinebeck, N.Y., a well-regarded retrofitting contractor in the region and a NYSERDA Multifamily Performance Partner, meaning the company has extensive experience with this type of work. However, it was the first time the contractor had used this particular system. The fabricator of the wall panels was J. E. McLaughlin, Inc., based in Rutland, Vermont, which also made the related facade components.
According to Dentz and Sto Corp., the existing wall characteristics and building design make a good case for study and analysis. “The small multifamily building has a simple building geometry and repeated façade patterns that are highly suitable to off-site panelization of an exterior wall insulation system,” the team reported. “The building is master-metered for electricity, with the building owner paying for all utility costs.” The team added that Sidarous would be the ideal owner – “committed to energy efficiency as demonstrated by the previous retrofit.”
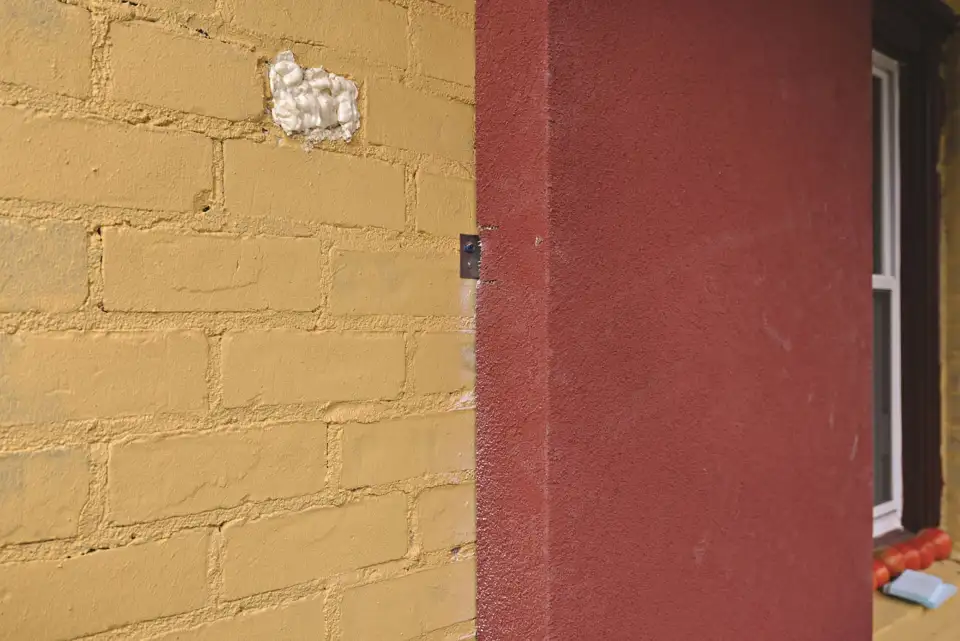
Results and reactions
“What’s appealing to me is the potential for increased energy efficiency, particularly the associated reduction in utilities costs, which we have to pay,” Sidarous says. As an architect who is experienced with retrofit projects, Sidarous also comments positively on the design and construction phases. “It’s been a great process,” she says. “There was a bit of a learning curve, but now that the panels are installed it is really fantastic. We are definitely looking at significant efficiency improvements when all is said and done, and the building’s appearance has also been improved.”
Additionally, Sidarous is optimistic about the awareness this project will create for the increased practicality of retrofitting small residential buildings – something that other architects and contractors should learn.
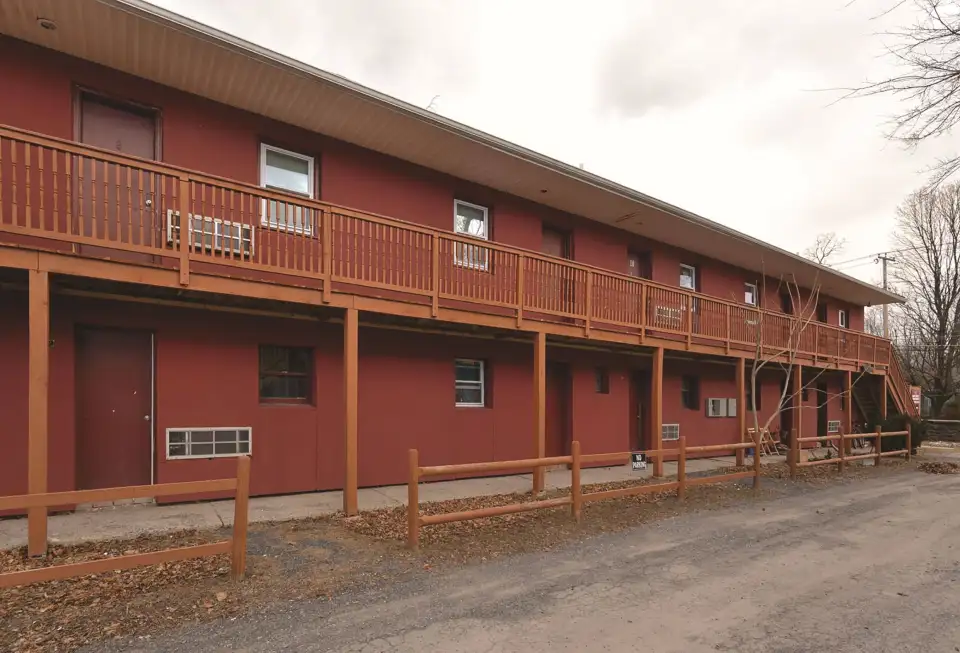
Joseph Malcarne, president of Malcarne Contracting and the project leader for the Burt Street Apartments construction work, is already convinced. Malcarne has worked on numerous NYSERDA projects and found in his first time using the StoLite cladding system that it was not only effective but also straightforward for the construction crews to handle and install. “Despite the challenge we faced with having to remove so much original siding material,” says Malcarne, “the StoLite panels installed easily and now look clean, true and finished.”
In particular, Malcarne responded positively to the cold-weather application. “Since we completed a lot of the installation at the end of last fall and into the early winter, being able to mount the panels quickly was a big help,” says the contractor.
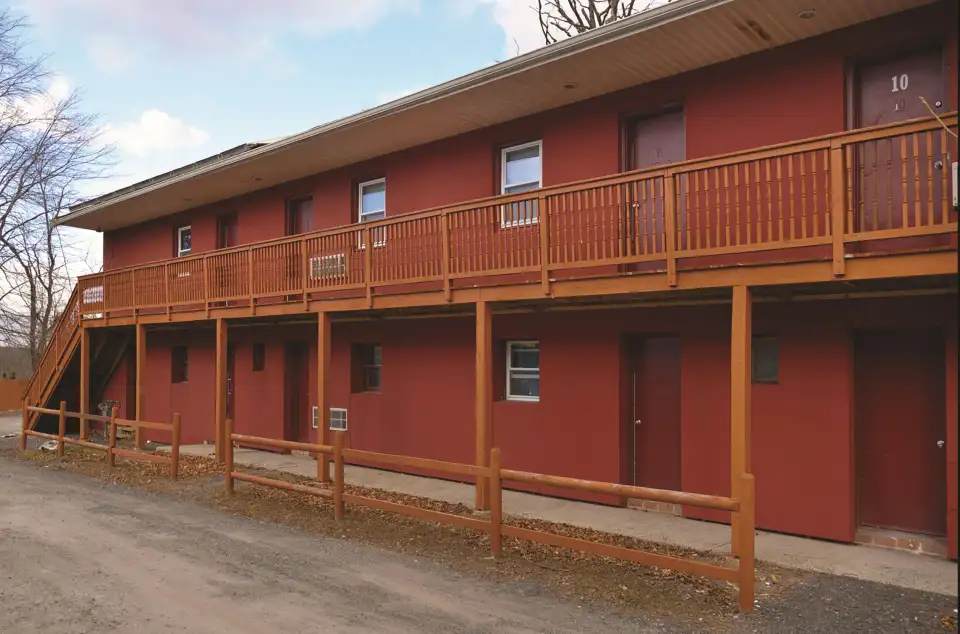
Curb appeal
Up until now, one of the main commercial drawbacks of deep energy retrofits has been their aesthetic challenges, say the project team members. For building owners and homeowners enamored of their façades’ traditional appearance, the exterior finish of many panel systems can leave something to be desired.
Yet, as both Sidarous and Malcarne note aesthetics is one of the additional advantages of the StoLite Panel. The results represent an important aspect of the Burt Street project: Since the system can be prefabricated using a wide variety of finishes to match architect or end-user requirements, the post-retrofit building can appear to have standard siding, a stucco finish, a variety of colors and textures, and even brick-look or other simulated finishes. Behind them all is a fundamentally consistent technology.
The look for the finished building, while certainly of interest to all, was not the key to success for The Levy Partnership, however. Going back to the original goals of the study, Dentz reviews the key metrics in his initial evaluative summary.
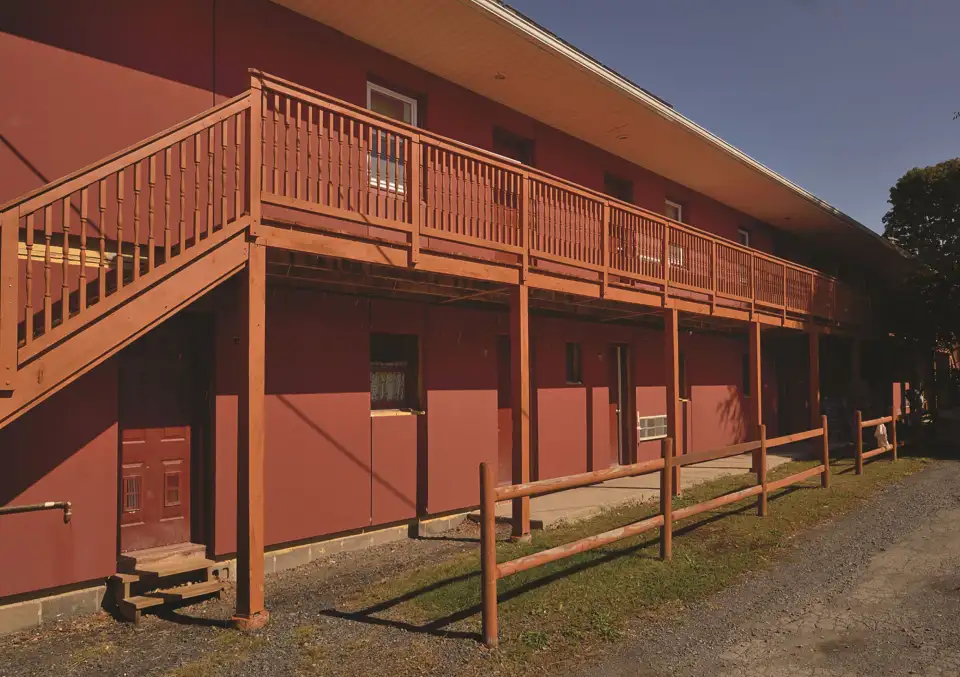
1. Impact on heating and cooling energy use.
Pre- and post-retrofit energy bills have been collected. The post-retrofit monitoring is required by NYSERDA, with all data weather-normalized and included in a final report. A total space conditioning energy savings of 36% or 7,803 kWh demonstrates a significant improvement over performance prior to the retrofit. Furthermore, anecdotal evidence from the owner and tenants report improved comfort levels within the structure. All tenants were asked to rate their thermal comfort level before and after the retrofit from 1 to 5 (1=poor; 5=excellent), the average rating went from 1.7 to 4.8!
The R-24, continuous insulation (ci) provided by the StoLite Panel system eliminates thermal bridging and associated heat loss, creating a more energy-efficient structure.
2. Impact on air tightness of the building envelope.
The system includes a liquid-applied air and moisture barrier that has been independently tested to show they achieve low levels of air intrusion through the exterior wall construction, which helps reduce energy needs in both heating and cooling seasons.
For the Burt Street Apartments, blower door tests have been conducted prior to the retrofit to establish baseline performance. Because the building does not have a common corridor, each apartment is entered separately from an outside walkway on each floor. Therefore, whole building leakage could not be tested easily. A sampling strategy was utilized with blower door tests conducted in half of the units. After testing, it was estimated that the facade restoration provided an air leakage reduction of 11%.
3. Cost.
The process and costs for the project have been documented from production through installation. The total costs demonstrate that this project is not only cost-effective but also significantly less costly than most other deep energy retrofit approaches to building envelope remediation. The final tally include labor costs and materials costs of $10.35/ft² and $9.68/ft², respectively. Opportunities to streamline the process, according to The Levy Partnership, include scheduling installations to avoid cold months and coordinating material delivery more precisely. Overall, the team was very satisfied with the results of the retrofit. Malcarne summarizes, “I would definitely work with StoLite again.”
Still, anything else beyond the project’s mandated findings might only be considered a bonus – great news for the building owner, contractor or architect, but not a requirement for NYSERDA-sponsored evaluations and demonstrations of today’s best deep energy retrofits. Yet cost-effectively adding substantial amounts of insulation should enhance the building, neighborhood, and communities, making it a better place for all while also becoming more sustainable to operate, says The Levy Partnership.
The project’s sponsor agrees. “One of the things we sometimes wrestle with at NYSERDA is the notion of curb appeal,” says NYSERDA’s Carver. “There are all kinds of far-out designs that people have come up with for energy-efficient buildings, but will the average homeowner latch onto them? Many of them want something that looks like a traditional home. So the fact that we can do this retrofit and preserve or even improve the appearance of the building and make it look like it’s any other apartment building -- that’s a huge plus for us.”
A history of turning inspiration into reality.
Inspiration favors the open mind. With Sto, your creative exploration can take you anywhere. Our proven products give you unmatched freedom and the ability to achieve your vision in any color, any form, any texture, any material.
Now, with The A.R.T. of reStore™, Sto provides a comprehensive solution that focuses on maintenance, repair, and energy improvements that safeguard the long-term value of your investment. Whether it requires simple maintenance, or a complete facade restoration, Sto helps you update and repair your building’s exterior with any aesthetic that you desire. Follow your inspiration, and Sto will provide everything your building design needs: products, support, services and surfaces.
Creativity Begins. Sto Finishes.®
All images courtesy of Sto Corp.