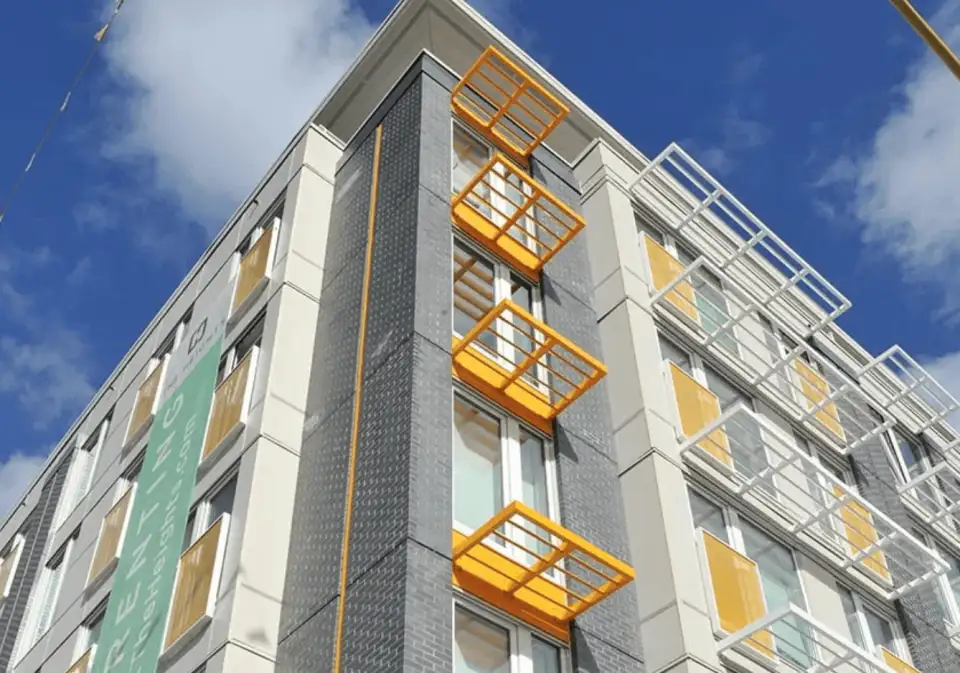
When Scott Kennedy, principal of Cornerstone Architecture, was persuading the developer of The Heights, a mixed-use six-storey building, to build it to meet the Passive House standard, Passive House buildings were a rarity in Vancouver. He was convincing—or maybe it was the numbers.
The city of Vancouver gives incentives for rental housing, which this 85-unit building is, allowing developers to build six storeys rather than four. Taking advantage of this incentive, though, requires that the project meet more-stringent energy standards, which usually entails installing a more-expensive heating system than the typical electric baseboard. Kennedy calculated that a gas-fired heating-and-distribution system would end up costing $450,000. Add in maintenance and fuel costs over 40 years, and you get closer to $600,000. Upgrading The Heights to the Passive House standard, reducing the heating load, would mean getting to use electric baseboard with a capital cost of $25,000. Yes, other Passive House upgrades would add costs, but there would be savings overall.
In designing the Passive House details for this building, Kennedy strove for simplicity. The building is wood frame, with a 2 x 6 wall on the exterior and a 2 x 4 service cavity on the interior. Both are insulated with fibreglass batts. An interior taped, 5‑cm EPS layer serves as the air barrier, and the whole wall assembly delivers an R‑value of 35.
To keep the air barrier continuous, the ends of the floor joists are wrapped with an air barrier membrane that is taped to the EPS. The bricks, stair, and handrails hang off of the exterior wall without interrupting the thermal and air barrier.
The roof also was fairly conventionally constructed, just with batts in the 2 x 10 joist cavity and a little more insulation overall. Tongue-in-groove plywood decking sits atop that cavity, covered by a peel-and-stick membrane that serves as both the air and vapour barrier. Over that is a layer of EPS, sloped for drainage, with 15 cm of polyiso on top and a 2‑ply membrane, adding up to a total R‑value of 56 for this assembly.
On the lowest floor of the building, reserved for parking, an unusual detail was required to minimize the thermal bridging from the concrete columns supporting the structure. The main floor slab connected to the columns is also concrete. It is insulated on top with 15 cm of EPS that has wood battens built into it and anchored into the concrete slab below it. A plywood subfloor rests on the EPS.
With the extra insulation and attention to airtightness, the heating-energy demand is being easily met with the low-cost electric baseboard. Summer comfort is achieved with the HRV’s bypass mode, which brings in cool air at night. Domestic hot water is being supplied by a gas-fired boiler.
Photo by Gordan Dumka