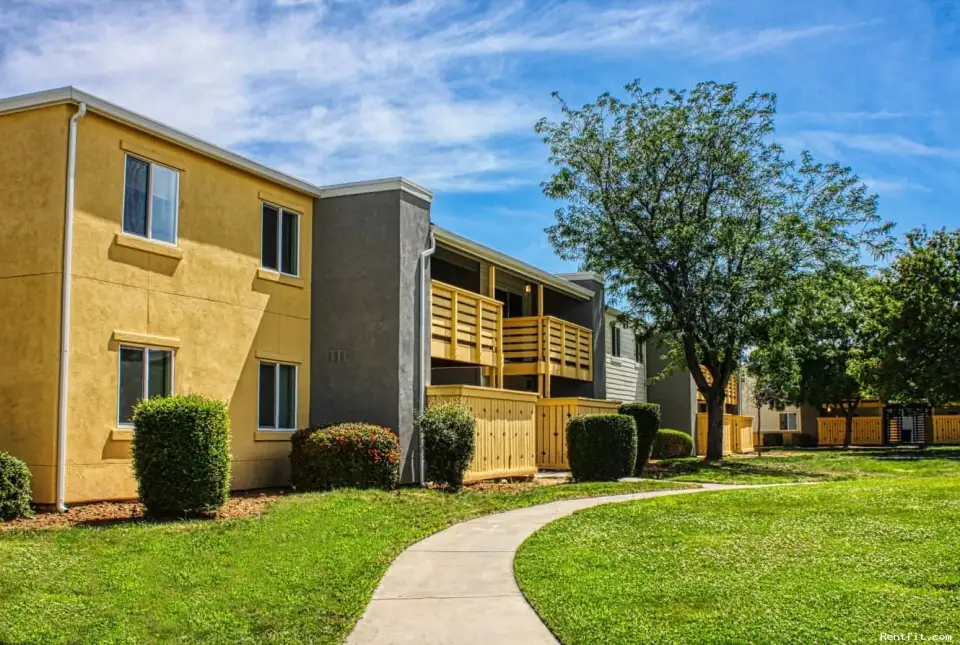
RMI, a long-time proponent of tunneling through efficiency cost barriers, has turned its characteristic expertise toward flattening the market barriers that impede zero-carbon building retrofits. Initiated in 2016, RMI’s REALIZE program has since blossomed into a four-pronged effort, with each branch supporting the other in a self-reinforcing spiral that is speeding the delivery of advanced retrofit solutions.
The four program initiatives—Advanced Building Construction (ABC) Collaborative, technology R&D, Zero Over Time, and scaling of regional efforts—combine supply chain coordination with demand aggregation to ultimately prove out and deploy prefabricated retrofit systems that are climate specific, cost effective, and aligned with limiting global climate change to 1.5°C.
Historically REALIZE’s main scope was its demonstration pilots, which were inspired by Energiesprong’s industrialized zero-energy retrofits in the Netherlands. While those efforts have not abated, they have been added to as the nature and extent of the market barriers in the United States have become clearer. “The ABC Collaborative and RMI’s partnership with the U.S. Department of Energy (DOE) has become a huge focus,” says Martha Campbell, who leads the REALIZE program. The collaborative grew out of the joint efforts on RMI’s Eva White demonstration pilot in Boston, which is still in progress. “DOE worked directly with us on the pilot and saw the growing pains of what we were trying to do, where our market was, and the gaps in that market,” explains Campbell.
DOE brought its resources to bridging that gap. In 2020 DOE awarded $26.3 million to 40 competitively selected projects, led by 29 organizations, in support of its Advanced Building Construction Initiative. The ABC Collaborative, one of those funded projects, has as its mission the coordination of market actors to accelerate the deployment of high-performance building systems. Its founding organizations, in addition to RMI, include the Association for Energy Affordability, PHIUS, ADL Ventures, and VEIC.
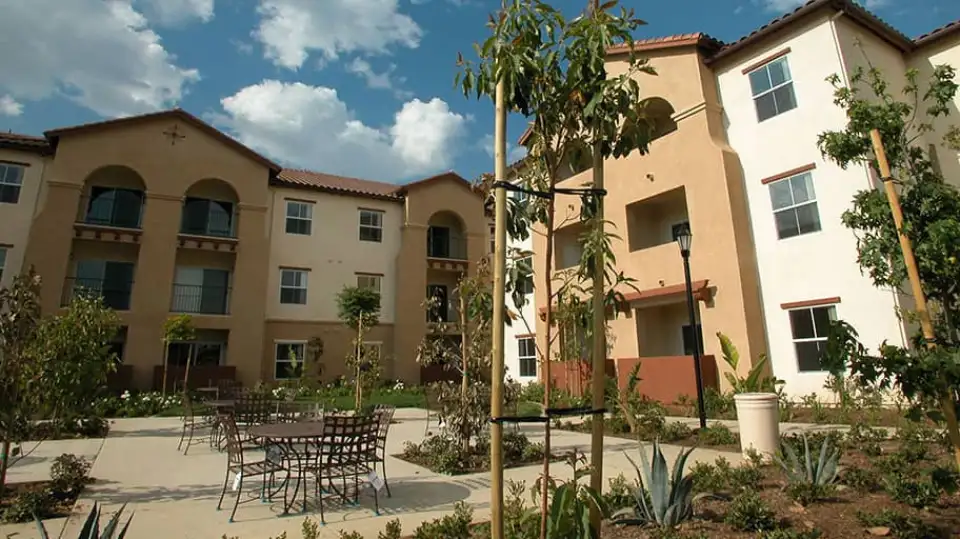
Additional funding through the ABC Initiative is also helping RMI support the development and fabrication of a critical retrofit technology—a mechanical system pod that integrates water heating, cooling, heating, heat-recovery ventilation, and an economizer to maintain comfort during the shoulder seasons. The pod is currently in fabrication and will be undergoing testing this summer with field validation and commissioning starting possibly late this year or early 2022.
In a parallel effort, thanks to funding from the California Energy Commission (CEC), RMI has partnered with a European manufacturer of an integrated mechanical pod to modify its product for the California market. The manufacturer already has a distribution network in the United States but has been hesitant to invest in making the leap to the U.S. market with this type of unfamiliar, integrated product until the demand is clearer. “My understanding is that even in Europe these products are quite niche,” states Brett Webster, an RMI manager supporting REALIZE. To help with overcoming the market hurdles here, the REALIZE team is working with the manufacturer to get the appropriate certification and line up demonstration sites. By spring 2022 the pods will be in at least four units in a 40-building site in California.
Simultaneous with these R&D efforts, the Zero over Time initiative is working to scale demand by helping building portfolio owners more quickly assess the optimal timing of zero-emission (ZE) retrofits across their entire portfolio. The cost effectiveness of ZE retrofits can be optimized when upgrades are timed to coincide with such trigger events as equipment replacements, major rehabs, refinancing, and building acquisitions. Working with large building portfolio owners, RMI is helping them plot out strategic timelines to fully decarbonize their portfolios by a given date.
Thus far, the portfolio owners that RMI is consulting with are those that are also involved in REALIZE’s demonstration pilots—WinnCompanies, National CORE, Self-Help Enterprises, and Eden Housing. WinnCompanies owns the Eva White building in Boston (see "Northeast Multifamily Retrofit," p. 31, for more on this pilot), while the others are involved in REALIZE’s California pilots (see "REALIZE-CA," p. 26). “We have five demonstration sites in California that total 300,000 ft2,” says Amy Egerter, technical lead for REALIZE. On both coasts RMI is working with panel manufacturers to fill the other big hole in the deep energy retrofit supply market—cost-effective climate-specific panelized solutions. “So much of our work is engaging manufacturers and contractors to understand the scale we need to reach to get cost compression for these systems, so that we don’t have to rely on incentives, which are not always available at the levels required for these projects to pencil,” says Campbell in discussing another thorny problem of scaling up retrofits: how to pay for them.
In working toward cost-effective solutions, the REALIZE team, in partnership with PHIUS, used the PHIUS standards as guideposts to develop a unique set of guidelines for more industrialized ZE retrofit solutions—such as unitized wall panels, pre-integrated mechanical pods, and so on—by typology. To keep within budget constraints, the California pilots are using double-pane windows to replace older window units. When asked about the missed opportunity to renovate using the best available technologies, Lucas Toffoli, a manager in RMI’s Carbon-Free Buildings Practice, pointed out that reaching for the highest performance available can result in not as many projects getting completed and consequently more carbon being put into the atmosphere. ”From a system-level perspective, practical and budgetary feasibility is something to keep in mind to facilitate reducing emissions now, when the ‘net present value’ of those emissions is highest—even if, from a philosophical perspective, it’s true that when you are doing the work, in an ideal case, you should reach as high as you can,” he notes.
With its many arms, the REALIZE program is loosening all the pinch points that exist in the deep energy retrofit market and hopefully sweeping us all—industry and building owners alike—toward healthier, zero-carbon housing in the process.