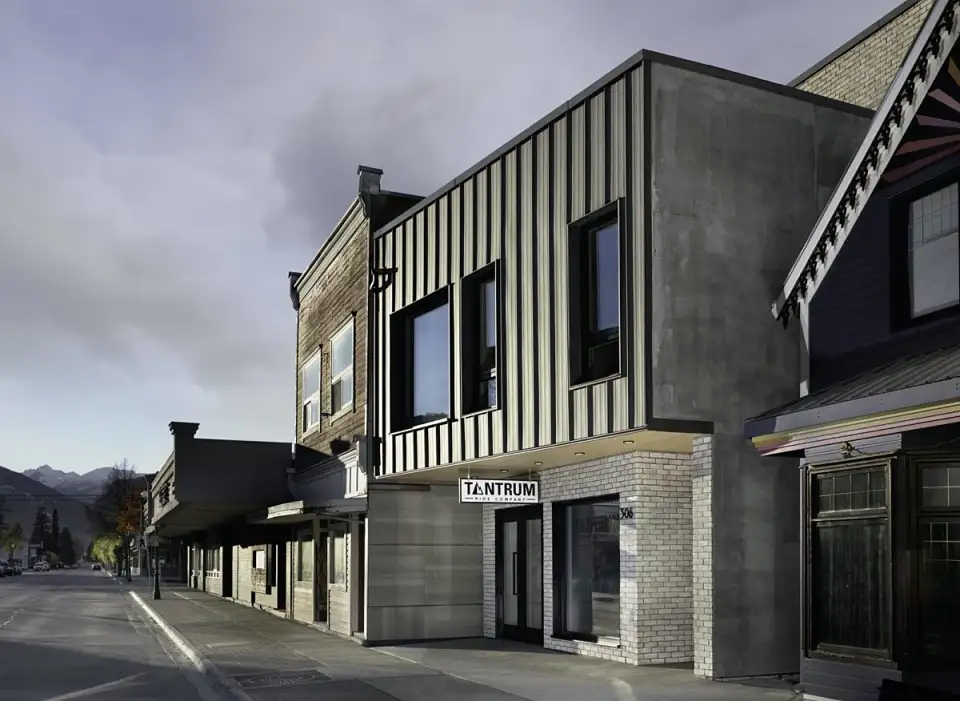
Revelstoke, British Columbia, a nature lovers’ resort town in the Selkirk Mountains, welcomes the Tantrum Bike Shop and office building, an outstandingly sustainable commercial Passive House building.
The owners of the bike sale, service, and rental business on the ground floor named their business and the building after a local mountain biking trail, but builder Greg Hoffart of Tree Construction suggests tantrum also expresses the team’s outrage at the nearly insurmountable permitting challenges this project had to overcome. Hoffart and architect David Arnott of STARK Architecture hope Tantrum inspires developers everywhere to throw a tantrum in the face of traditional commercial development, choosing innovation over business-as-usual mediocre efficiency, conventional high-embodied-emissions building materials, and complacent design.
In 1910, pioneers developed this downtown 25-foot by 100-foot lot with a one-story, wood-framed building squeezed between a similarly sized building and a two-story one, but a 1960s fire left a hole between the surviving flanking buildings. The larger building, meandering over the property line, also leaned well over the vacant lot. The combination of the encroaching neighbor and a depressed economy squelched redevelopment until today’s resurgence of business, fueled by tourists chasing deep powder, rushing rivers, and extreme bike trails. Tantrum’s owners had been eyeing this lot for their new shop, and after Arnott and Hoffart created a beautiful and efficiently comfortable new home for them, they knew they had the right team to conquer the challenge. Arnott and Hoffart promised a Passive House building constructed using the most sustainable materials possible (see Certification Tips).
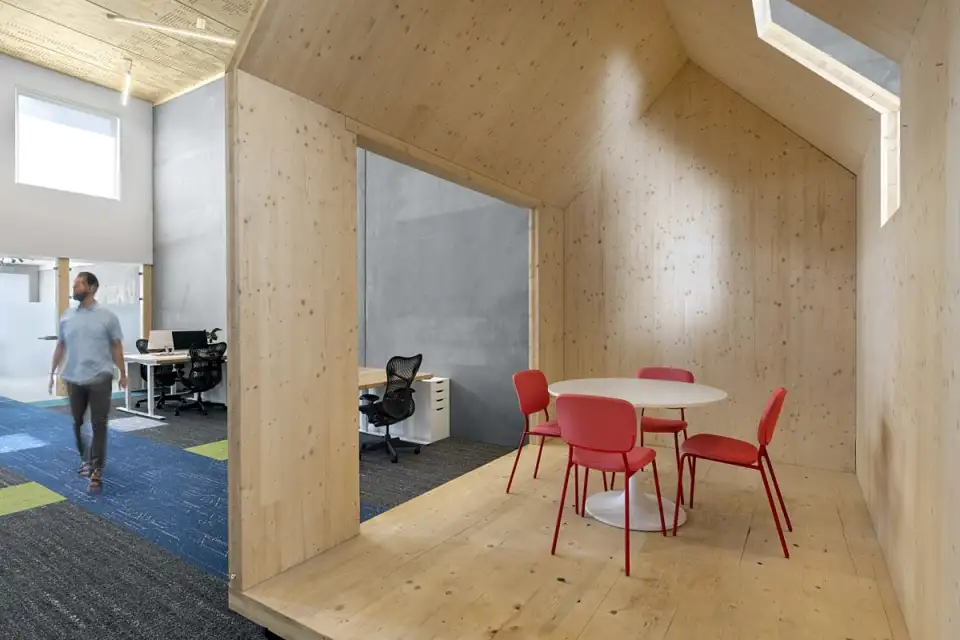
Design
Arnott knew he had to make maximum use of the narrow lot and could go three stories high, but how could he avoid inflicting an unsightly box between two heritage wood structures? The solution was to articulate both ends of the box—outside and inside.
Arnott cantilevered the second floor to cover entries for both the front of the bike store and the back where bike rental/service customers come and go. Pulling the third story back hides it from pedestrian view to match the scale of its neighbors. And this design also brings windows closer to the people working in the center of the second-floor offices.
The final touch? Angle the front so that it juts out to meet the larger two-story building’s façade but gracefully recedes to meet the front of the charming historic single-story coffee shop next door. As an added bonus, pedestrians can now see the front and windows as they walk from the center of downtown. And the windows are now oriented closer to due south.
Arnott’s clever articulation of both ends of the envelope solved exterior challenges, but fire protection requirements for a three-story building were too expensive to meet. The key this time was to create an 18-foot-tall ceiling for the office space in the middle of the second floor by pulling the third floor almost to the back of the building. The third floor, now that it is a mere mezzanine, doesn’t trigger expensive fire protection requirements, and also serves as a more private office area.
The exterior and interior articulation created four different kinds of space: (1) a large volume for the storefront retail store and alley-accessed rental/repair shop, (2) traditional office spaces with windows at both ends of the second floor, (3) a large open office area in the middle of the second floor with plenty of natural light, and (4) private and semiprivate mezzanine offices. Tree Construction, now a Tantrum tenant, enjoys the 20-foot-height open office area, which currently hosts a model building of cross-laminated timber (CLT) panels.
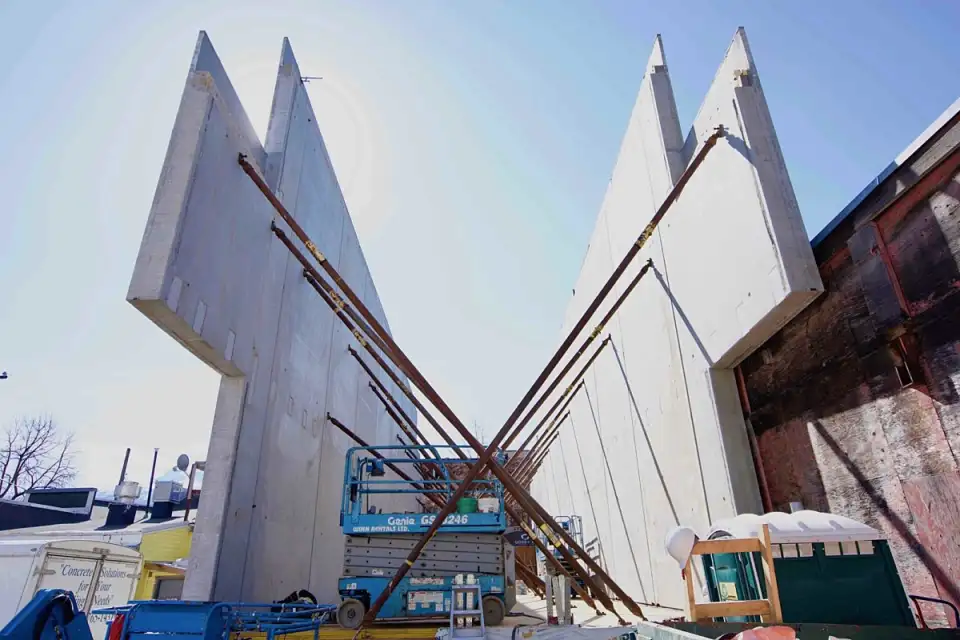
Construction Challenges
Building in Revelstoke is not for the faint of heart. Limited labor, short summers, and 40 feet of snow in a long, cold winter are common afflictions for Canadian builders. The first construction obstacle coincided with the initial excavation.
Racing to meet the owner’s May 2019 opening deadline, the Tree team discovered during excavation that the overbearing two-story building, like many in its era, was built on heavy timbers instead of concrete. Remove too much lateral supporting soil, and they’d be in litigation and potentially buying expensive renovation of an arguably obsolete building. Driving pin piles for the entire 70 feet to support the neighbor would have been too slow and expensive.
Solution? Hoffart limited the excavation; all that Tantrum really needed was a 6‑foot-tall basement sufficient for storing bicycles. The back end of the basement had to be full height, so pin piles on the side of the slouching neighbor allowed full-depth excavation for the grade beams that support the ICF basement walls. Forming and pouring the concrete grade beams and basement slab over a corduroy of EPS foam varying from 2 inches to 16 inches thick during the Revelstoke winter was cold, wet, and miserable. The Tree team added 4 inches of EPS to the outside of the ICF basement walls atop the slab for a total of 9 inches of EPS. Finally, the ground floor was ready to be decked.
The next construction conundrum was, how do you use all 25 feet of your lot’s width and also create finished, fireproof sidewalls? Concrete masonry unit blocks would be too labor intensive, slow, and impossible to finish because of the encroaching neighbor.
Factory-built, full-height, concrete structurally engineered panels (SEPs) solved the problem. The 3‑inch outside layer of high-strength, low-moisture concrete provides a durable, fireproof exterior. And SEP panels sandwich 7 inches of polyiso foam between the outer concrete panel and the inner 4‑inch concrete, so it stays warm in winter and cool in summer. Structural ties of resin-filled fiberglass bond inside and outside concrete layers without thermal bridging. Though largely hidden from pedestrian view by the flanking buildings, the tall, dark panels have a clean, geometric aesthetic. Installation takes only two weeks, and neither the indoor nor the outdoor surface requires any finishing treatment. Speedy installation of the SEPs made up for the excavation and basement nightmare.
The SEPs also helped Tantrum reclaim its space from the slouching neighbor. Although some SEPs had to be made thinner where the meandering property line encroached, installing the SEPS enabled Tantrum to lever its listing neighbor back to vertical at the property line. The design and construction nightmares from the encroachment had a bit of a silver lining, as a small portion of this sidewall is adiabatic, helping the thermal performance.
Floor and Roof Panels
With the foundation and long sidewalls created, Tree employed another time-saving assembly. Angle iron was quickly welded to the inside of the SEPs to support the floors and roof, and then factory-manufactured Swiss Lignatur floor and roof panels, precisely milled to the exact distance between the sidewalls, were craned into place. As each panel was lowered into place, the crew would pound it tight to the neighboring panels, and call for the next panel.
These factory-crafted panels are made up of box beams of dimensional spruce lumber biscuit jointed and glued together into cassettes averaging 4 feet wide. The benefits they offer include speed of installation; a variety of insulating, fire-retarding, and/or sound-absorbing fills; and geometric designs for a finished ceiling. In both the roof assembly and the cantilever floors, the core of Tantrum’s thermal protection is the wood-fiber insulation built into these panels. Atop the 11-inch-thick roof cassettes are another 13–3/8 inches of wood-fiber insulation panels, as well as mineral wool averaging 4 inches thick in 2 x 8 sleepers ripped to slope to 2 inches thick for drainage.
The cassettes in the cantilevered second floor are also 11 inches thick, but to avoid penetrations in the panels that would compromise their fire rating, the finished floor is on 2 x 4 sleepers atop the cassettes. This assembly created not only a chase for plumbing, ventilation ducts, and electric, but also space for mineral wool batts where the floor cantilevers. Under the cassettes is 6 inches of wood fiber, strapping, and ¾‑inch tongue-and-groove softwood for a total cantilevered floor thickness of 24 inches.
CLT and Wood-Fiber Insulation
With the sidewalls, floors, and roof completed, Greg’s team built the end and interior walls. Although some of these walls are 2 x 6 conventional stud framing, some are strategically located CLT panels. Along with some CLT interior walls, they withstand shear in this long, narrow building. Lower-density wood-fiber insulation is covered by thinner, higher-density finish wood-fiber panels held in place by polymer fasteners to reduce thermal bridging, completing the 14-inch-thick end walls.
Finishes
Strapping supports dark steel cladding, which, in combination with the SEP concrete sides, provides a dark, durable exterior for a commercial building. Inside, the honey-colored Lignatur ceilings complement the light-gray concrete. Flooring is carpet panels made from recycled polyethylene fishing nets with the occasional bright yellow, orange, and red strands providing a fun, light, and warm feeling.
Ventilation, Plumbing, and Mechanical Systems
With the building’s airtight envelope, super insulation, and retail/office-occupant-density lighting and electrical equipment, heating loads can be met by ventilation post heaters and electric-resistance spot wall and ceiling panels. In summer, the concrete thermal mass along with the extensive wood-fiber insulation add up to deliver a high specific heat buffer even on hot days. Night flush cooling and large ceiling fans help on the hottest days.
Given separate retail and office tenants and operating hours, the bike shop and the offices have their own electric-resistance hot water tank and ERV in the basement utility room. A dedicated utility chase from basement to roof is insulated, but the 43-foot-long ducts between the ERVs and roof reduced the efficiency of the ERVs from 76% to 68% and increased the specific heat demand by 0.6 kilowatt-hours per square meter per year.
Not only did Arnott and Hoffart create robust, sustainable assemblies, but they were careful to avoid thermal bridges. They carefully covered the windows and door frames with wood-fiber insulation for low installation psi values, attached cladding with thermally isolating polymer anchors, and minimized plumbing thermal bridges.
Tantrum’s clever design, painstaking construction, and advanced materials emphasize function in a beautiful form.
—Tad Everhart certified Tantrum and is a member of CertiPHIers Cooperative.
Read more Passive House Buildings Magazine