In a fortuitous set of circumstances, two families approached Hyperlocal Workshop at around the same time with similar needs. Each wanted a small cabin on land they owned in the mountains of Colorado, one at 7,000 feet elevation and one at 9,000 feet for a place to commune with nature with their young children. They both agreed that we could develop the same building system for each of them so we could focus on getting the most design out of the diminutive spaces. These tandem requests inspired the CABIN_ph project, a series of simple Passive House mass timber modular retreats to explore flexible housing.
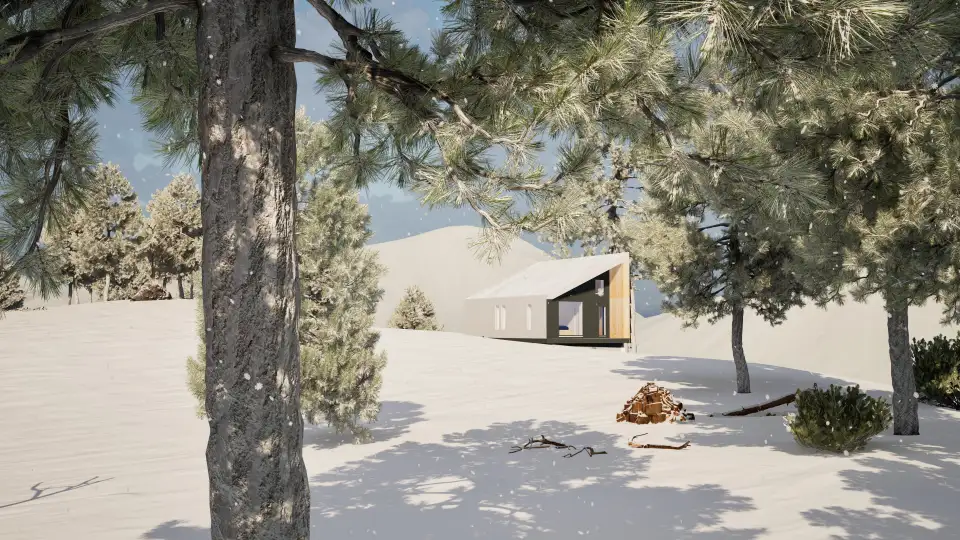
Timber Panelized Approach Supports Flexible Housing Solutions
The design concept is rooted in a simple shed roof structure that can host a loft, separate sleeping area, bath, and kitchen and dining space. The two relatively remote locations led us to decide early in the process to make the structure modular, using 3’6” by 8’0” sections of nail-laminated timber (NLT) panels for the walls. Traditionally, an NLT building system was used in many larger buildings a century ago but has been largely forgotten in modern construction. As a renewable and affordable mass timber system, it eliminates additional finishes and can be used in multiple horizontal and vertical structural applications with only about 30% more wood resources compared to conventional framing. It also is easily fabricated in a small shop with minimal tooling.
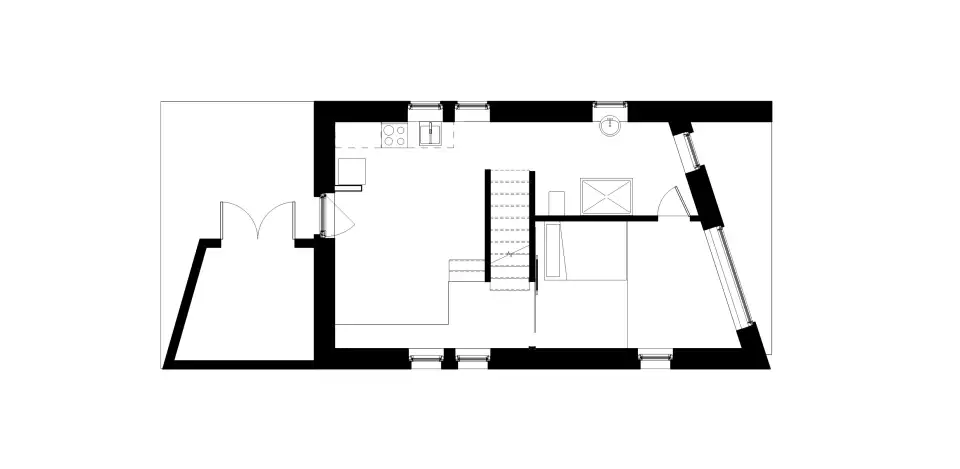
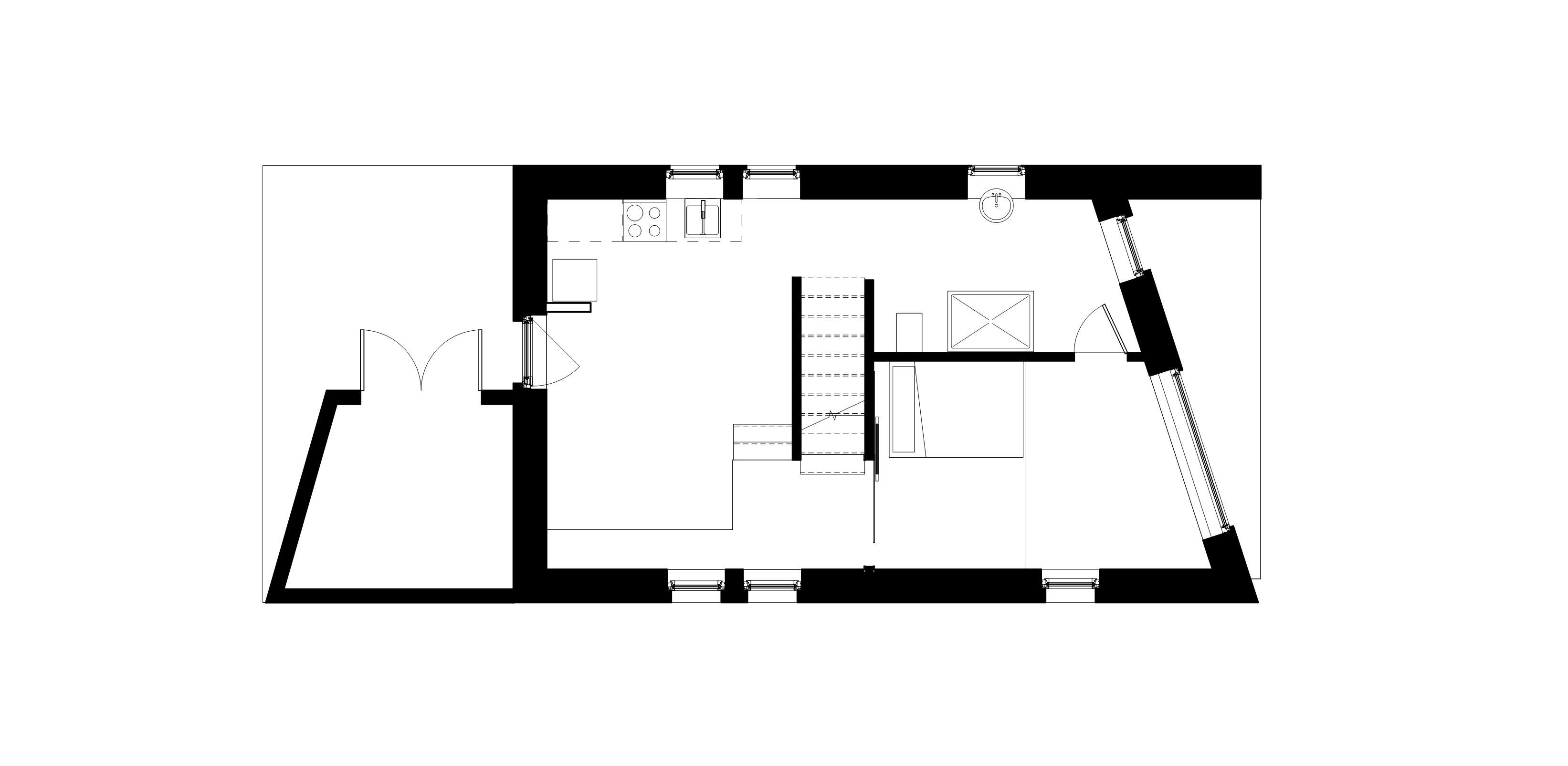
The cabin's first floor layout plan.
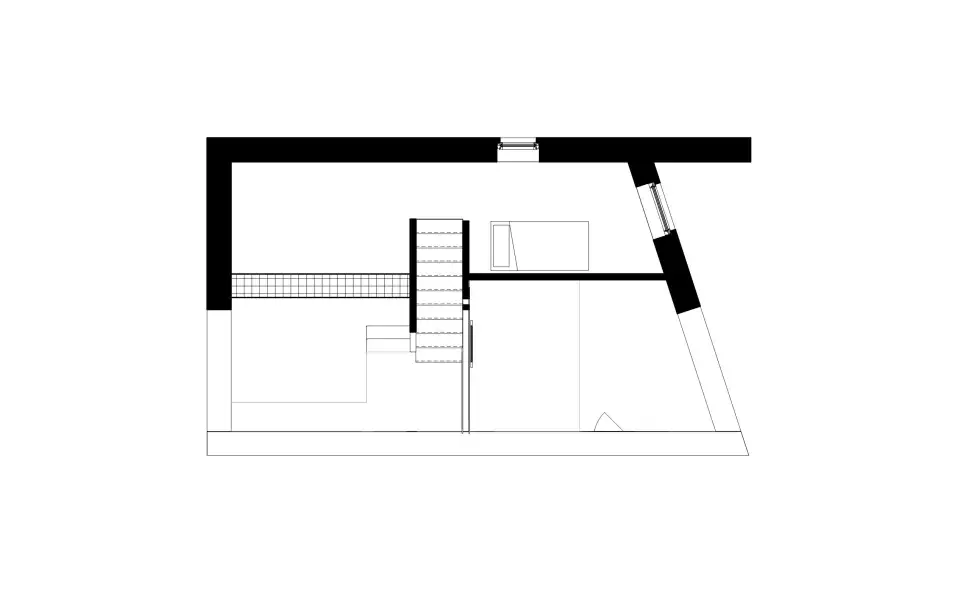
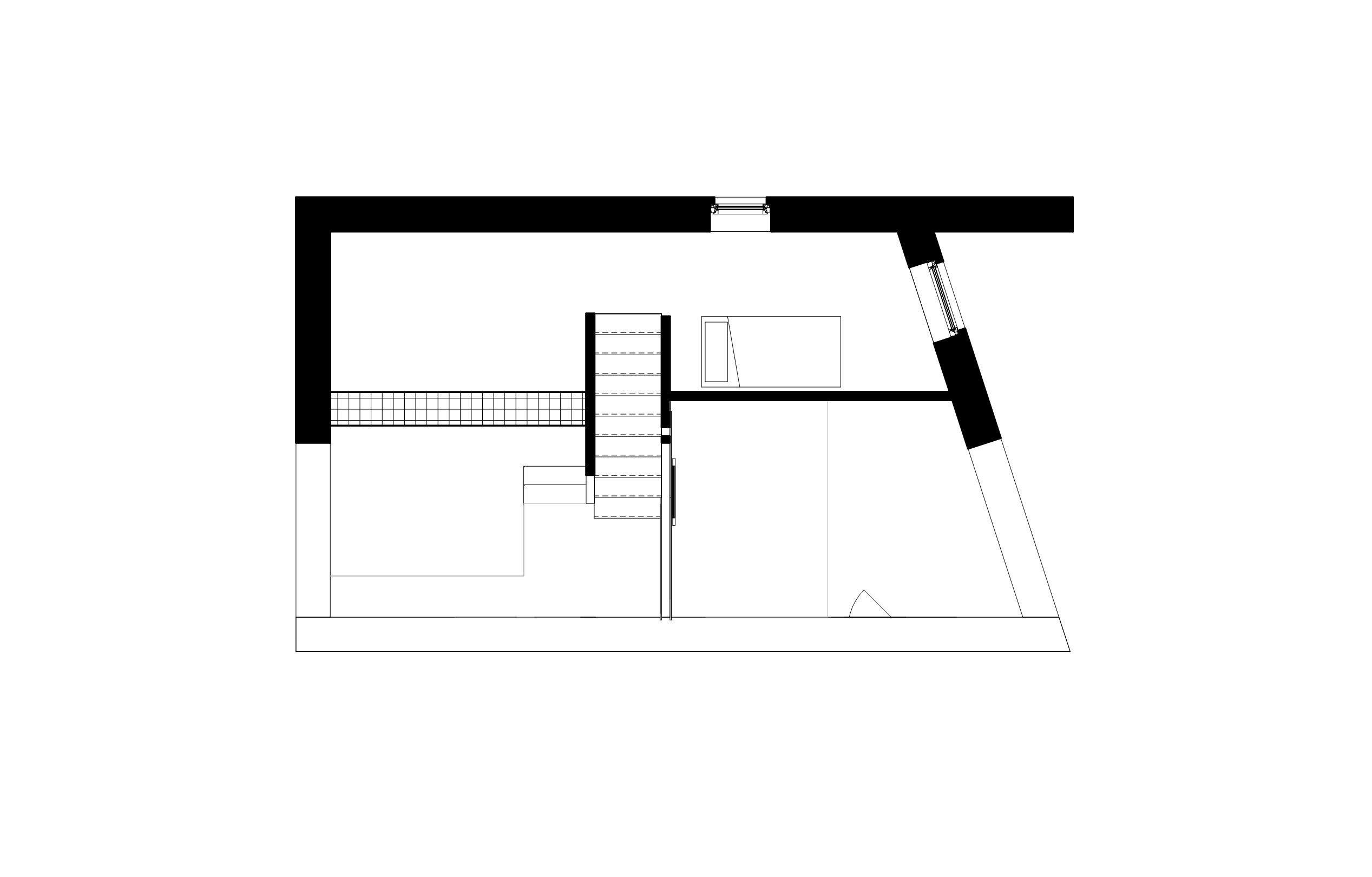
The floor plan of the cabin's loft.
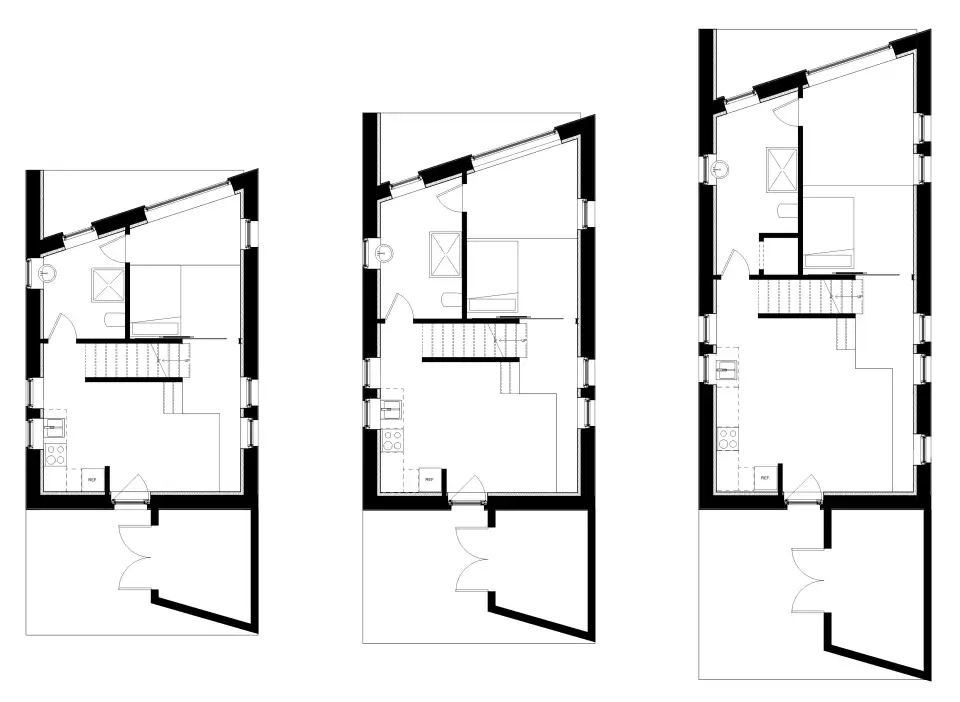
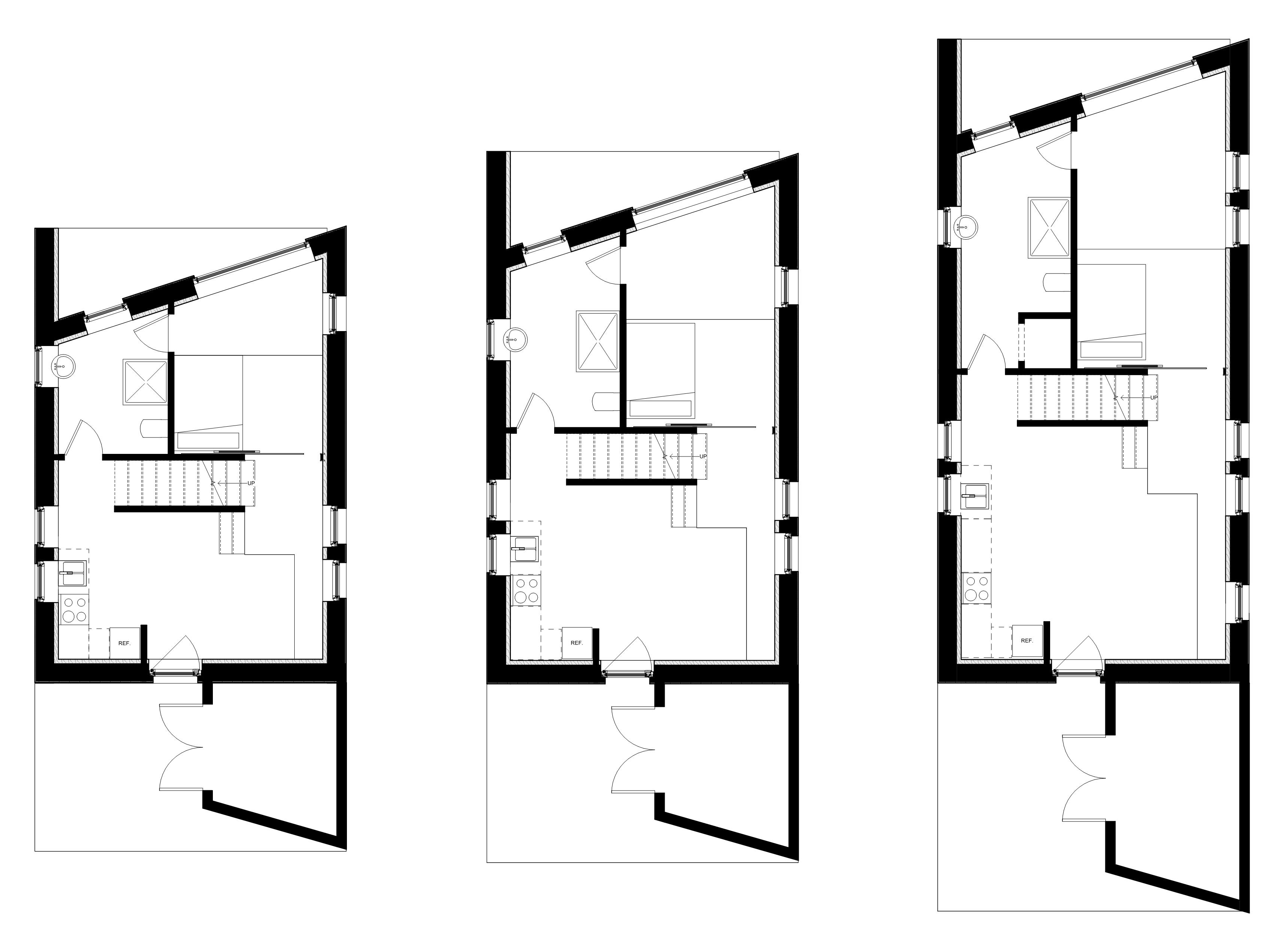
Floor plan variations.
The NLT panels we are using are built off site by First Haus Co in Taos, New Mexico, using common 2x4 framing lumber and the LignoLoc timber nail, which provides the mechanical fastening but still allows for the panels to be cut. Similar to dowel laminated timber (DLT) the system avoids the glues and extensive processing of cross laminated timber (CLT). On the exterior side the wall panels are sheathed in plywood and wrapped with an Intello membrane for vapor control and airtightness. The outboard insulation layer is a full-height Larson Truss system filled with 16 inches of wood fiber insulation. Further structural testing would be valuable to reduce or eliminate the need for plywood.
The panels come in two types; one is opaque, and the other hosts a window or door. Stacked panels provide a roof pitch that allows for a code-approved set of stairs to the loft. The panels can be placed in any linear configuration to the site to adapt for views, egress, and solar gain. This approach allows the floor plans to stretch from 450 square feet to more than 1,000 square feet with no additional structural development required.
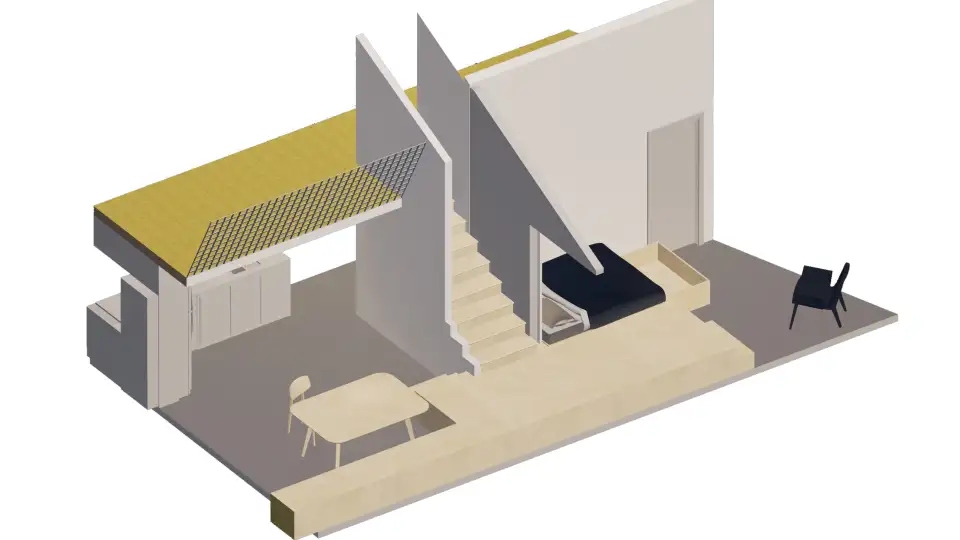
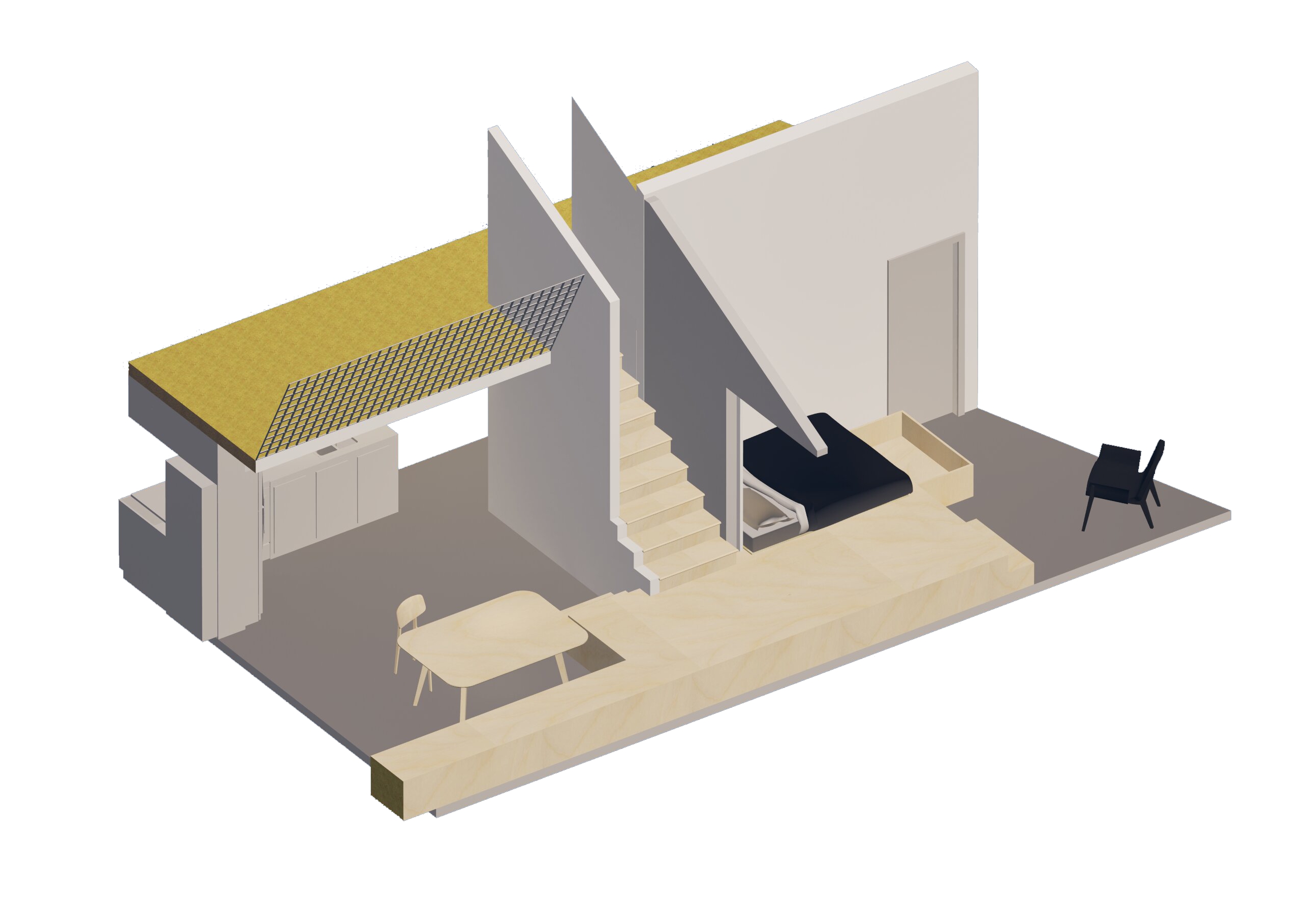
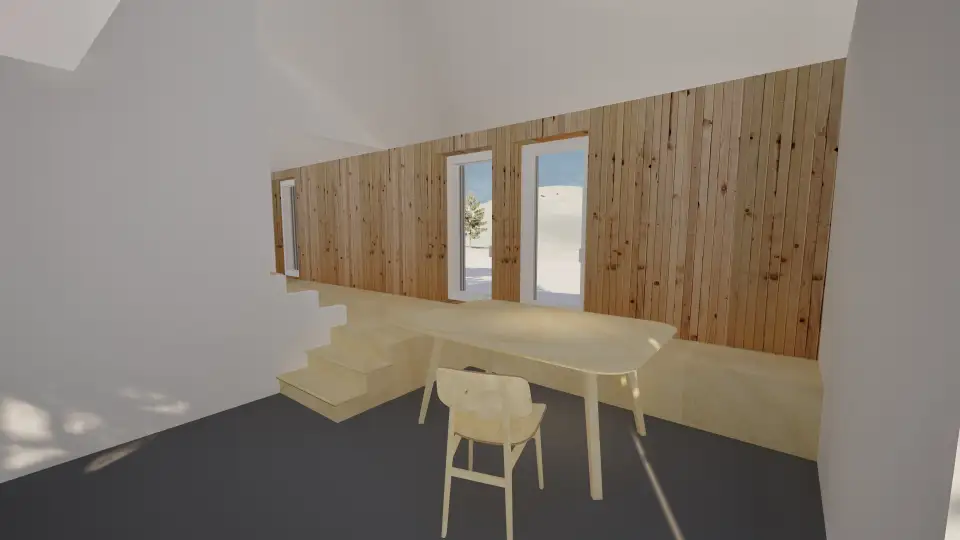
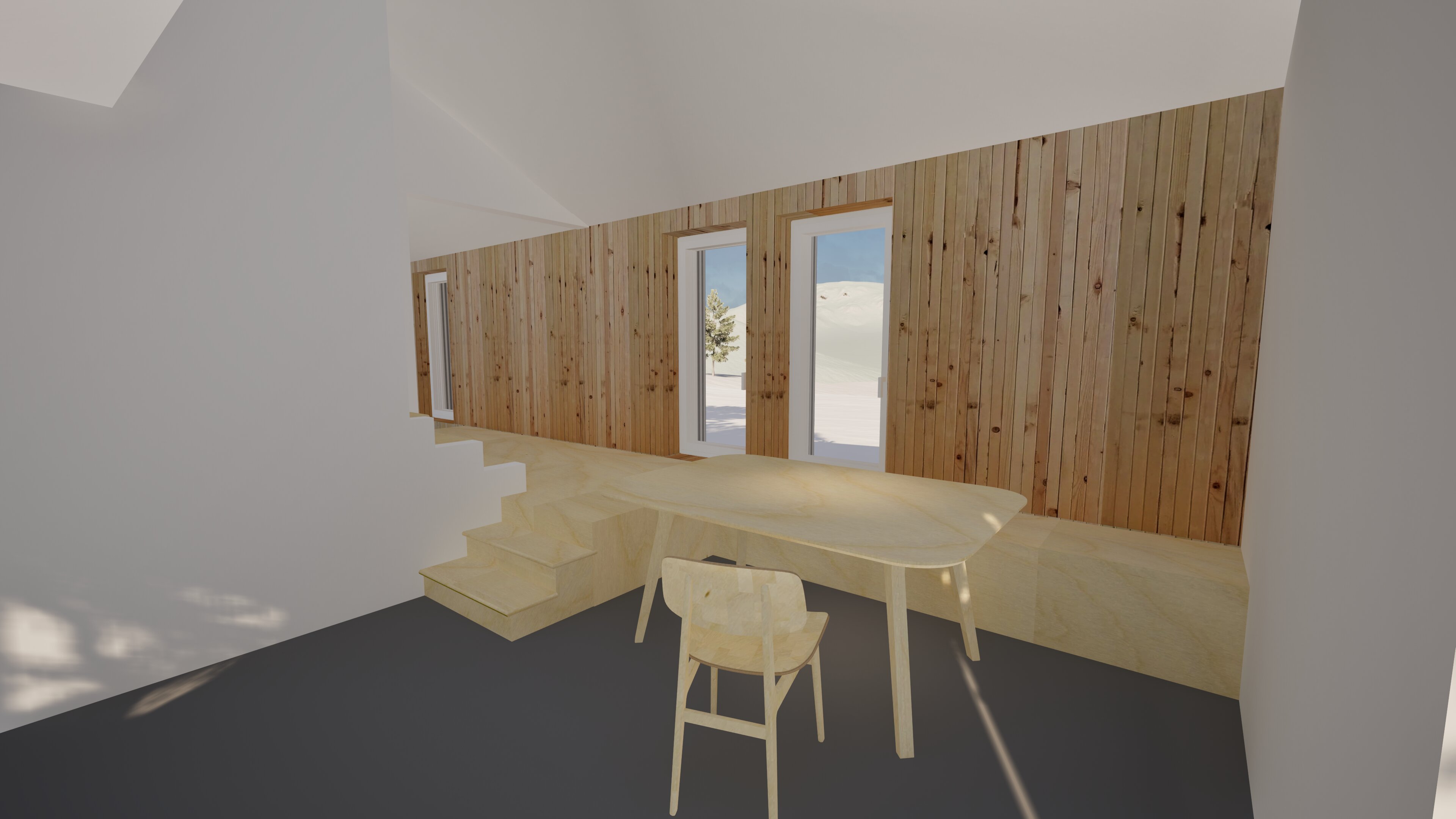

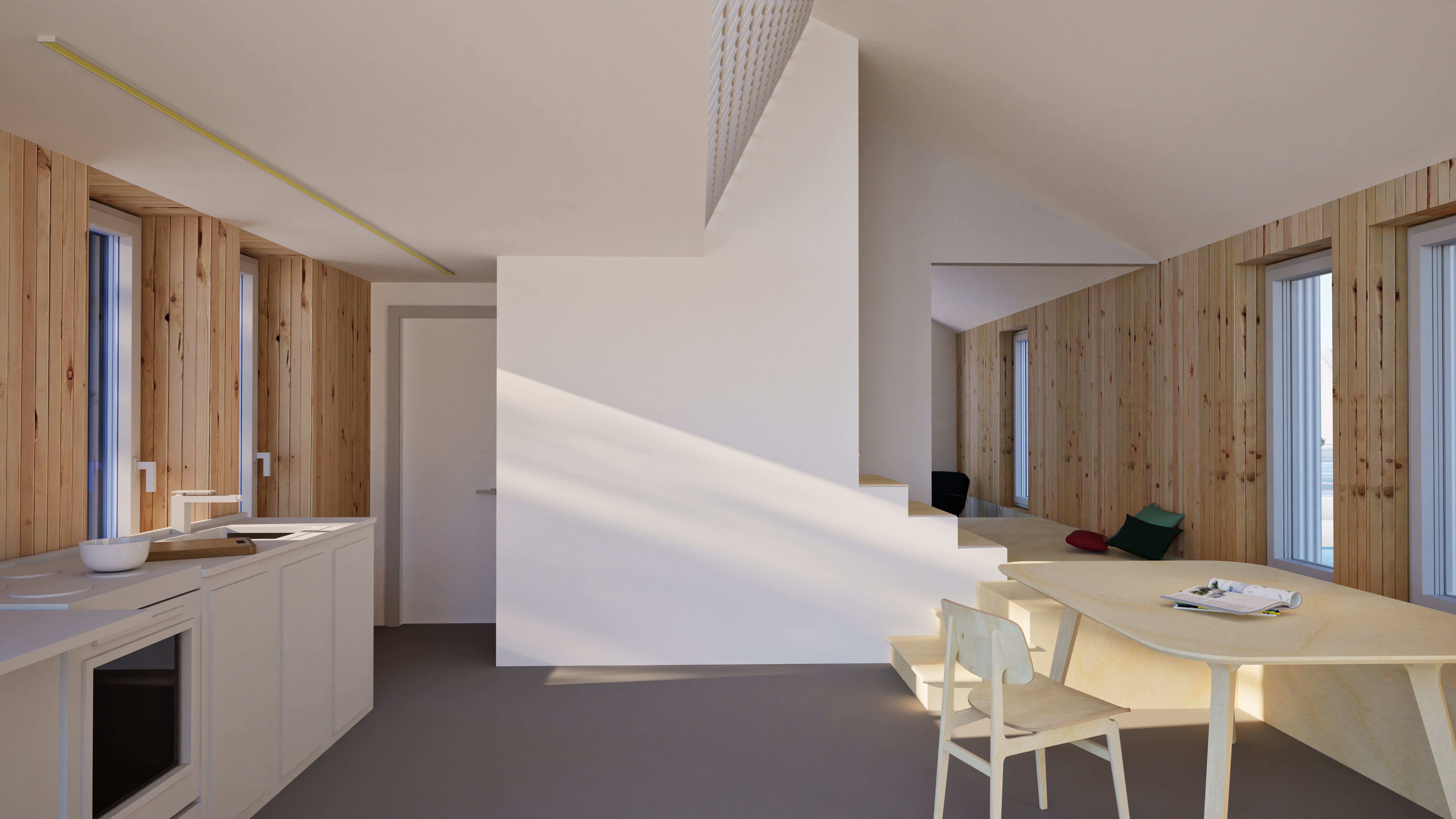
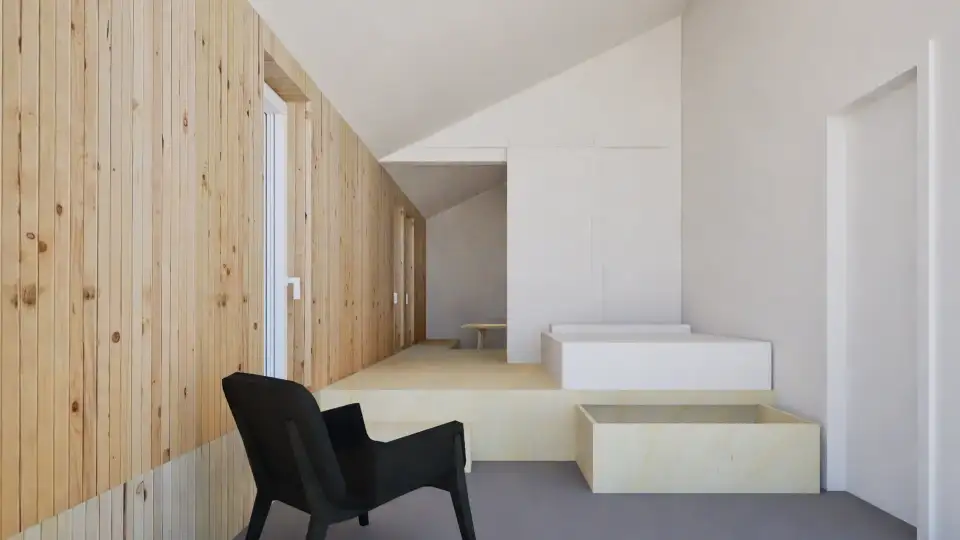
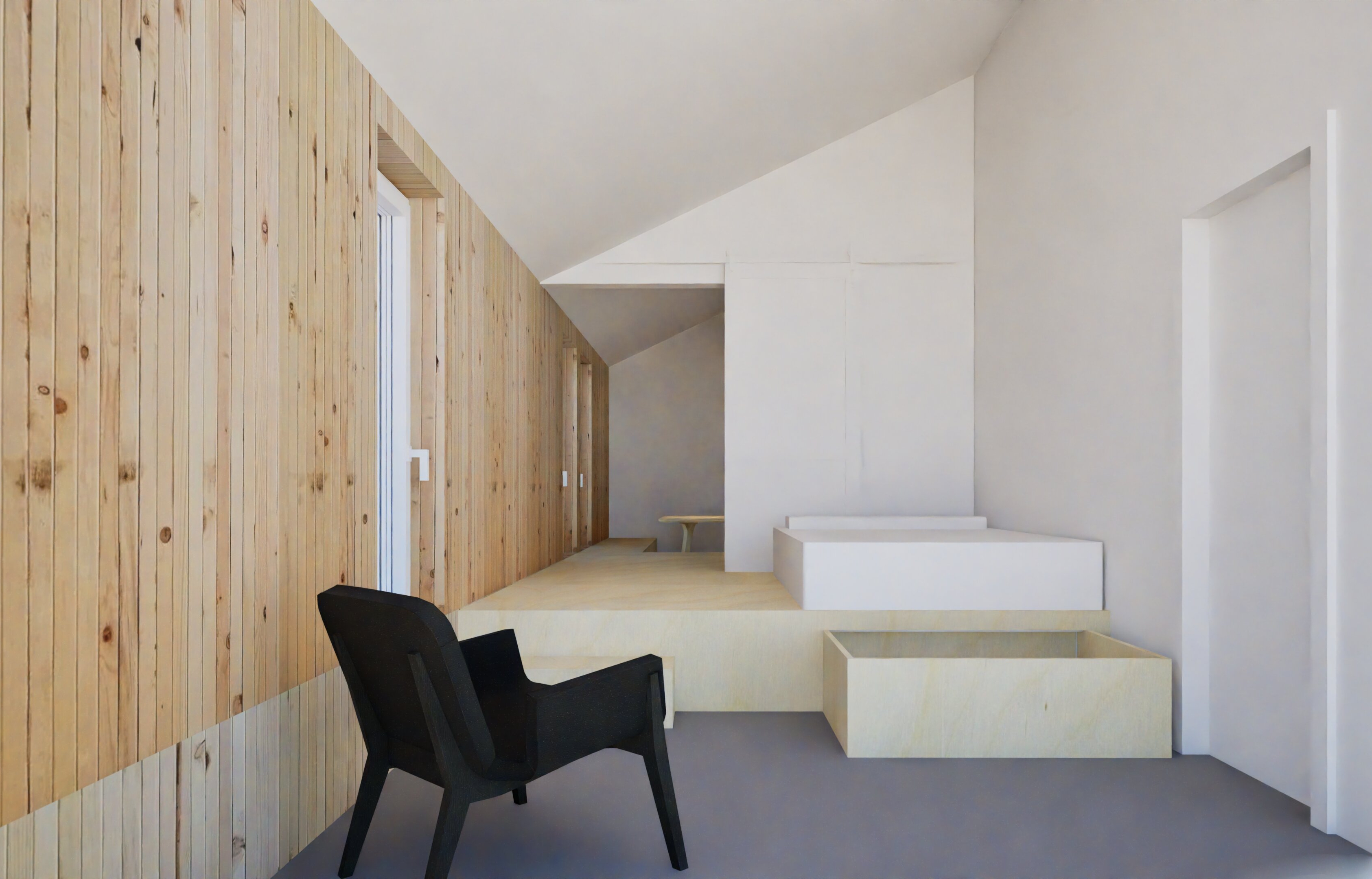
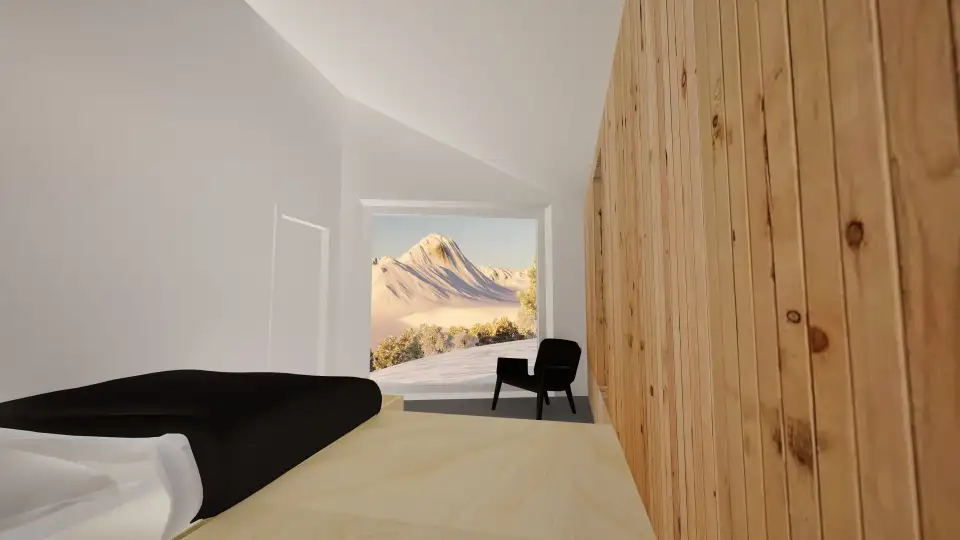
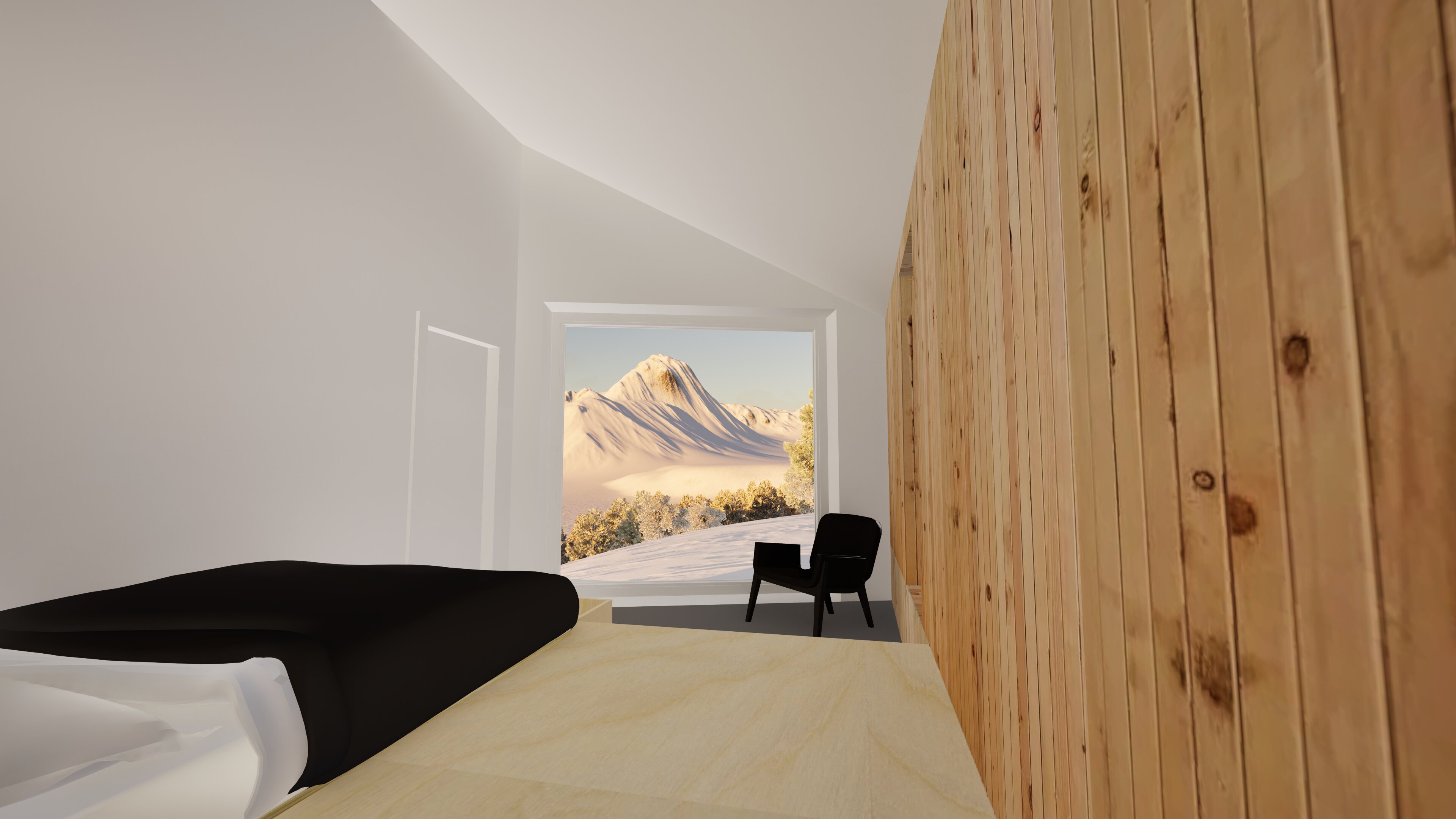
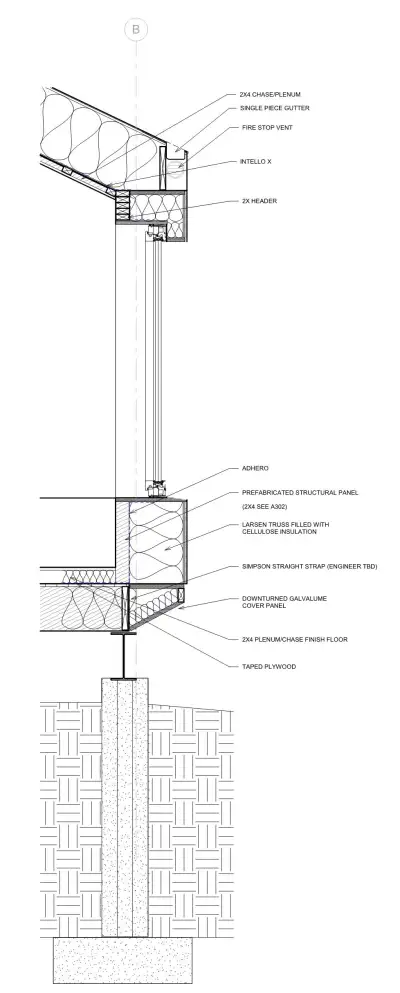
The roof and floor consist of 16-inch I-joists with an Intello air tightness layer concealed under an electrical mechanical chase in the ceiling. The platform floor is the airtightness boundary by taping ¾-inch ply, which is protected by the 2x4 mechanical finish floor system.
The interior is anchored by a built-in plywood structure that acts as the staircase, seating for dining, bed platform, and storage. It is a visual anchor for the interior to reduce the sense of clutter. The bedroom hosts a significant 8-foot by 8-foot window to help immerse the occupants in their surroundings.
To preserve living space, the energy recovery ventilation system is located in the unconditioned storage just outside the cabin. Hot water is point-of-use electric for a cabin that will only be used seasonally, and a 40-gallon heat pump water heater for longer term occupancy. The mechanical distribution of air, power, and water is tucked in the chase floor on top of the insulated timber platform to provide accessibility.
Because of the significant fire risks in the cabins’ location, as is the case generally throughout the West, the cladding system is a simple corrugated metal on the roof and lower side. The taller wall utilizes 3x5 fiber cement panels placed like oversized shingles. Underneath the steel roof is a ventilation screen and Polystick XFR, a fire-resilient, but vapor open, self-adhesive bulk water barrier.
The site conditions for the 712-ft2 (TFA) cabin are challenging enough, sitting as it does at 9,000 feet on an exposed site in Colorado’s Rocky Mountain, that we had not intended for it to necessarily meet PHI’s certification criteria, but to our surprise the Passive House Planning Package annual heating demand results fall in just below 4.75 kBTU/ft2 as a result of the favorable synergy of the glazing and view corridor. The cabin’s paltry peak load of 4,000 BTUs means that it can easily be heated with a mini-split unit.
Because the length and perforations of the structure can be easily configured, and the wall system R-value can be optimized on a case-by-case basis, the project’s adaptability allows it to also serve as a viable urban use case for a backyard accessory dwelling unit. The adaptability surmounts what has been a core hurdle for many predesigned schemes, which often require significant modification to work in varied conditions, especially when accounting for the nuances of Passive House performance methodology.
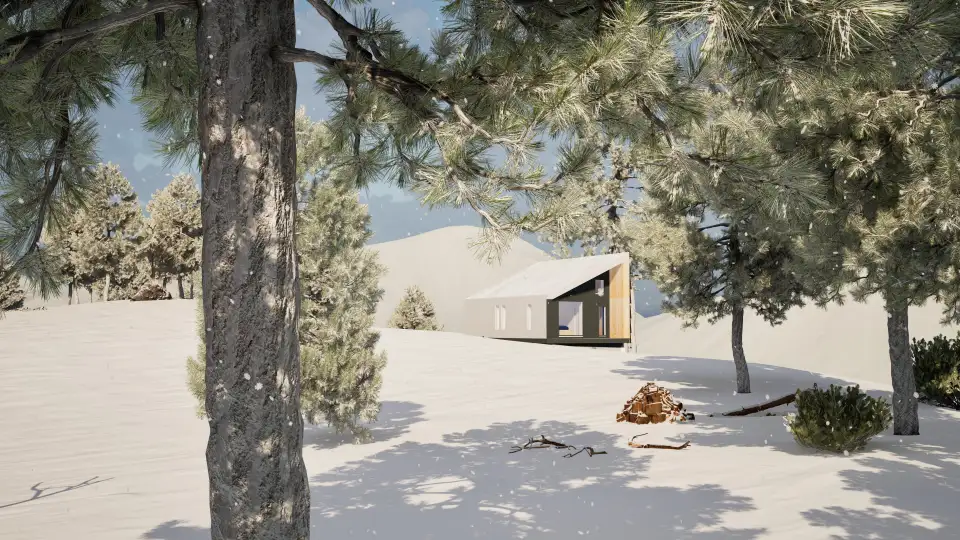
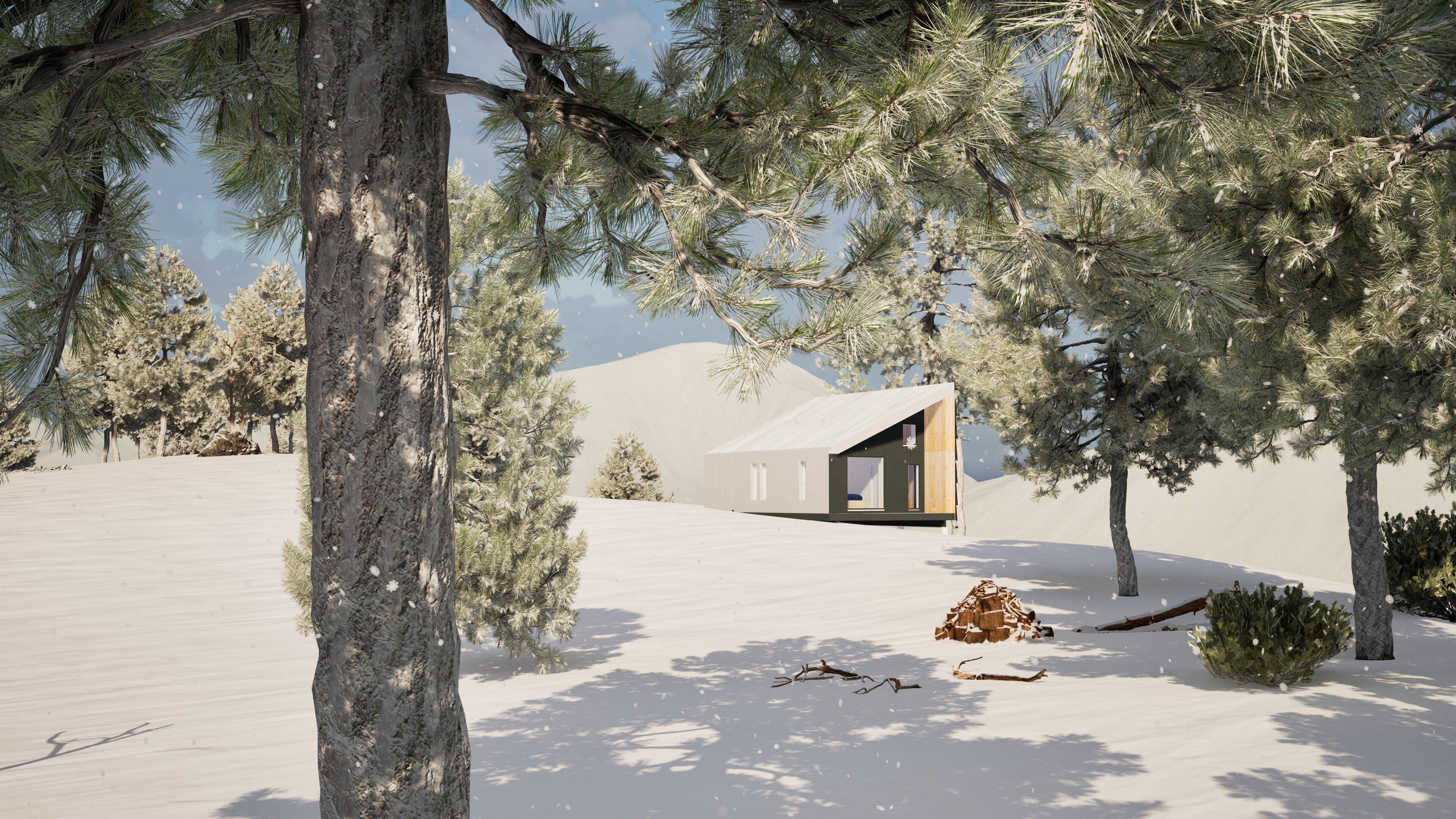
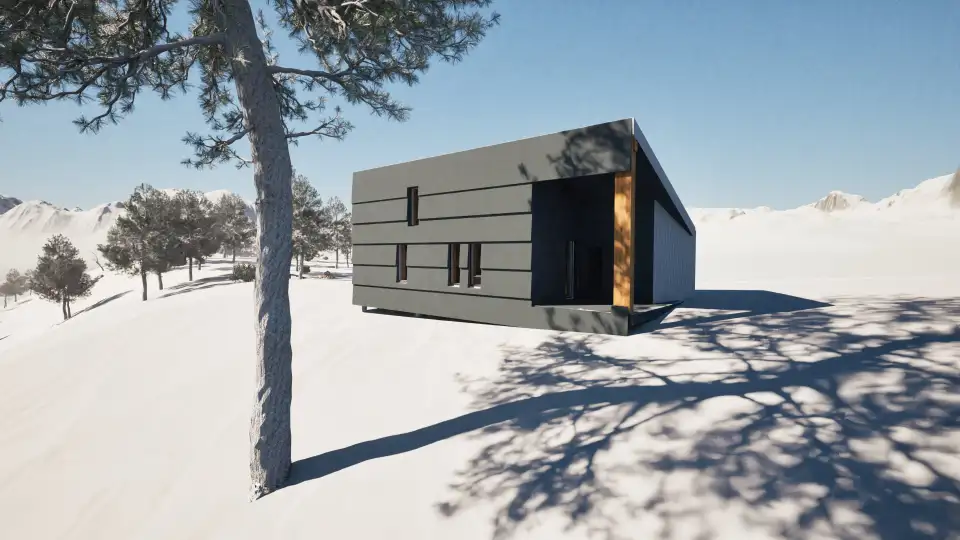
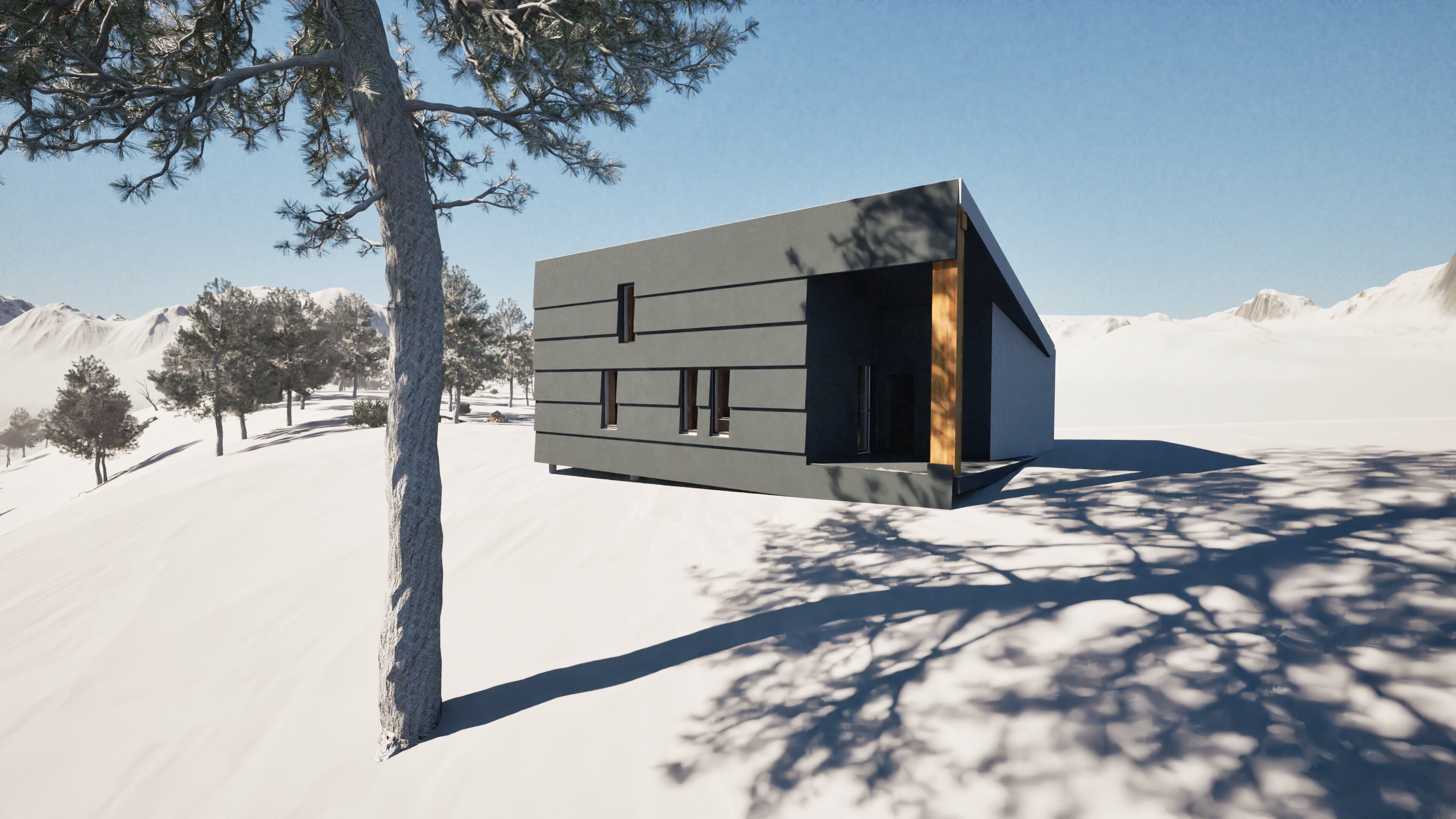
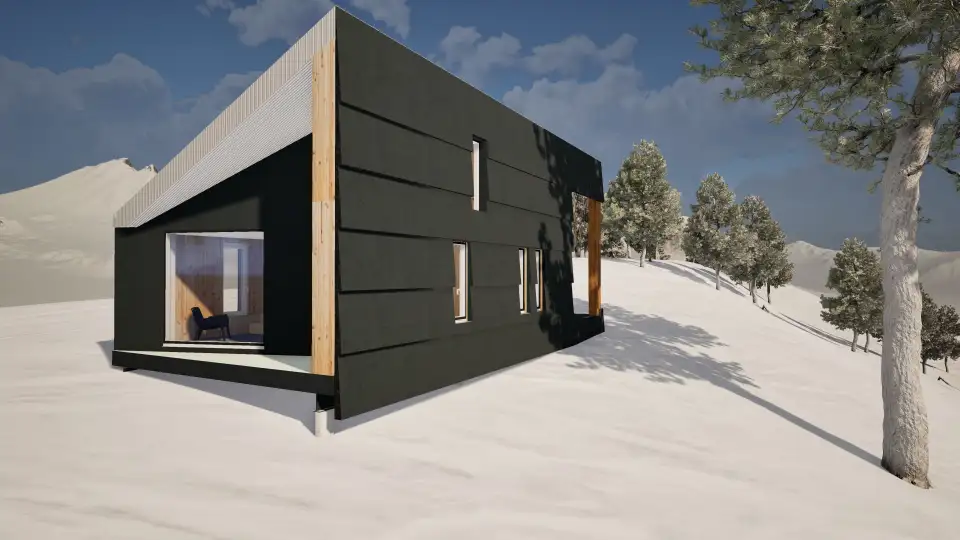
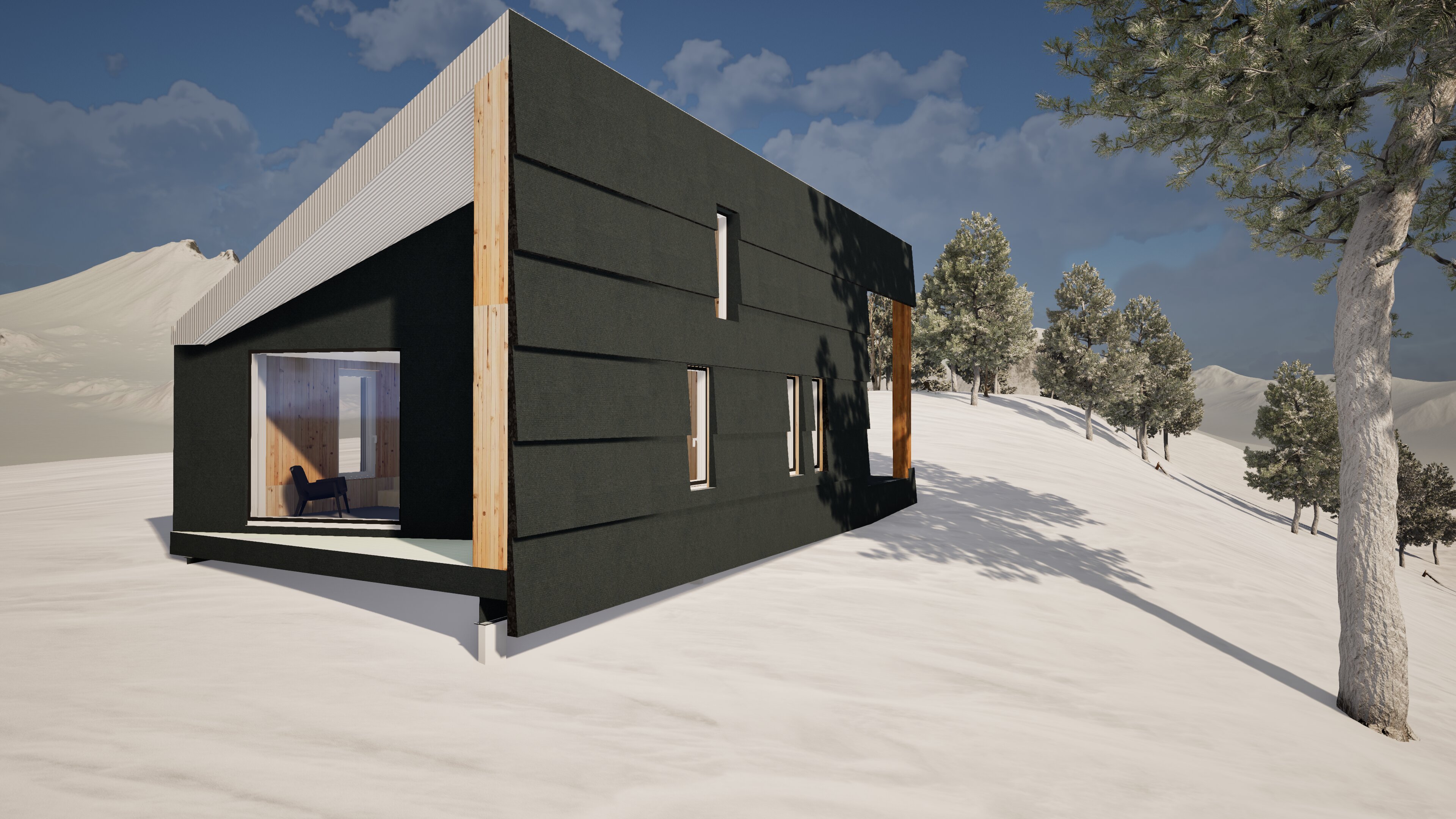
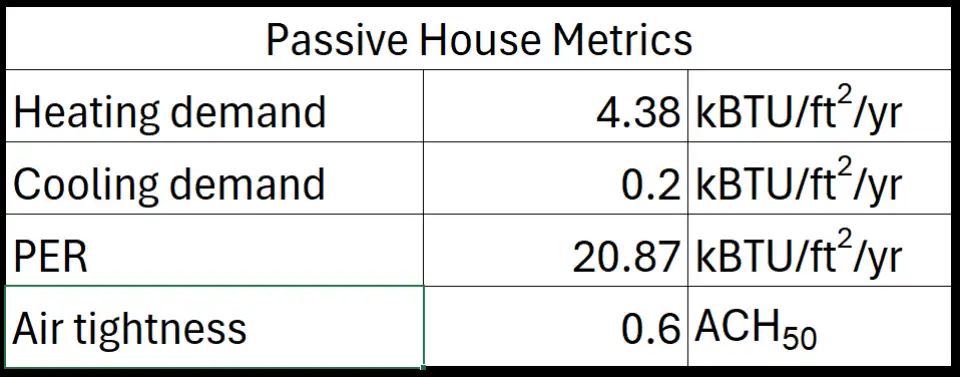