Michigan Januarys are not known for their clemency. The depths of winter can be particularly brutal on the west side of the state, where bands of lake-effect snow roll off Lake Michigan almost daily and the air temperature can remain below freezing for weeks. On the tiny Leelanau Peninsula—which extends past the 45th parallel and in formal geographical terms sits at the tippy top of the mitten state’s pinkie finger—resilience inevitably means surviving winter power outages and long periods when one is snowed in. Consequently, many homes have generators or, failing that, woodburning fireplaces.
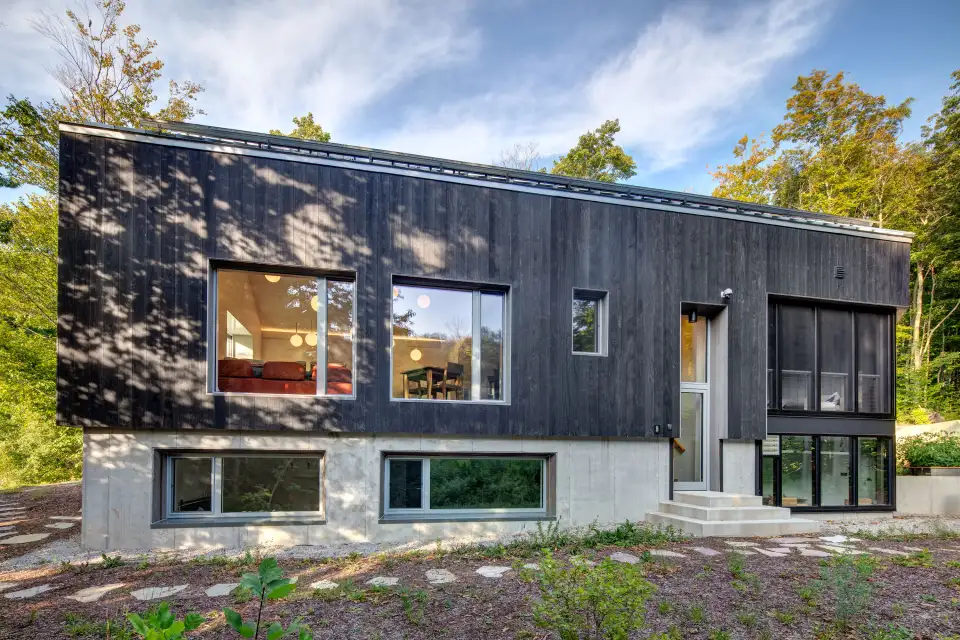
Up North Resiliency in Michigan
Colleen and Doug, two recent additions to the Leelanau, had neither when their heating system picked January to go on the fritz. A freshly retired couple from downstate, the two had moved up north into a newly built home only a few months previously. With temperatures stuck in the teens at the time, they called the person who had installed their heat pump to request he come and fix the problem.
When the repairman arrived to resolve the issue and further inspect the one condenser for the approximately 3,000-ft2Passive House, he was surprised to find that the interior temperature had only fallen from 68°F to 63°F. In code-built homes in this part of the state, houses can become uninhabitable and pipes can freeze in a manner of hours without a heat source.
When he asked them how long they had gone without heat, the owners said they weren’t sure. They told him that they’d called about a week prior. However, as architect Hilary Padget relays, “It had taken them a while to even realize that the heat wasn’t on.”
Health, Comfort, and Data
Colleen and Doug came to Hilary Padget and Anthony Harrington of New York-based pHdesign for several reasons. According to Padget and Harrington, the partners who put the “p” and the “H” in the name of the firm, Harrington had known the couple’s son during grade school. Colleen had also been his pediatrician. Beyond the Michigan connection, the homeowners recognized that pHdesign’s commitment to sustainable design aligned with their values and many of the priorities they had for their home—chiefly, that it had to be resilient, comfortable, energy efficient, and healthy.
Padget notes that the latter interest took priority for Colleen because of her medical background. Meanwhile, Doug has worked on sustainable energy policy for the state of Michigan for years and was primarily interested in efficiency, but also in using data to improve building performance.
Given these priorities, pHdesign and the couple considered a few different options when it came to building standards and certification, including LEED and Energy Star. The more they learned about Passive House, however, the more it seemed like a good fit for the project, even if the firm had yet to take a project through the certification process. Still, Padget and Harrington were not without experience. Harrington had worked on a Passive House project while with another firm, and Padget was in the process of obtaining her certification from the Passive House Institute (PHI) as these initial conversations were taking place. “Ultimately, we came to it together,” Harrington says, of the decision to pursue PHI’s Classic certification.
“We were all drawn to the fact that we were making an energy model that could be tested onsite,” Harrington says.
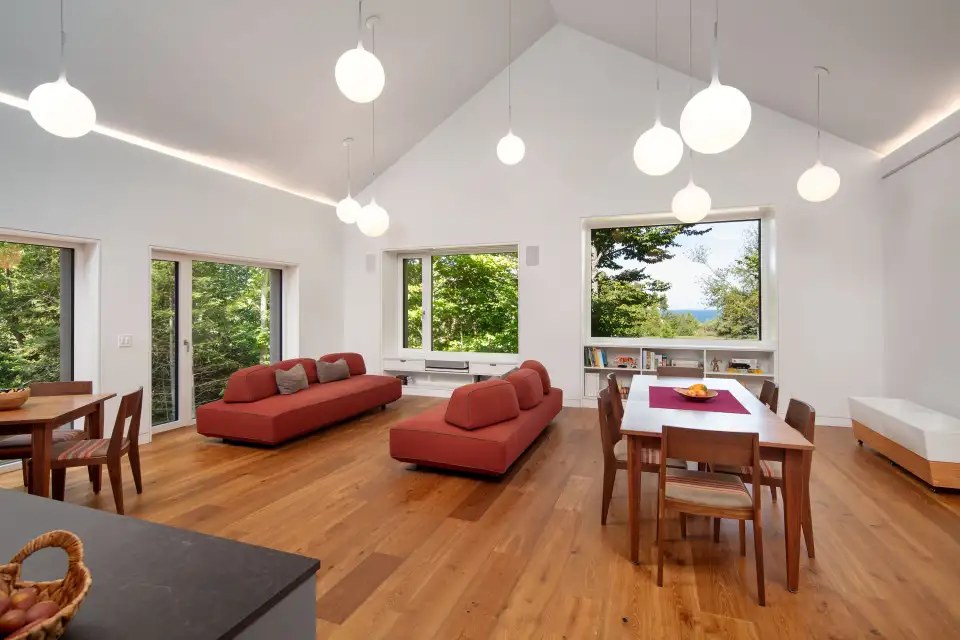
The House Takes Shape
The Burnt Angle House, as it’s known for reasons that evidently sound better in Spanish, is located in a newer subdivision that is a little over two miles from the incorporated village of Northport. The one-acre property is triangle-shaped, with the northwest-facing side following the contours of a quiet, residential street. The house is sited near the southwest corner of the property, overlooking a short, public trail that snakes down a ravine and leads to the sandy shores of Lake Michigan. As illustrated in Figure 1, the public trail ends at the opposite side of the public road from the property but turns into a private walkway that leads to the front door of the home.
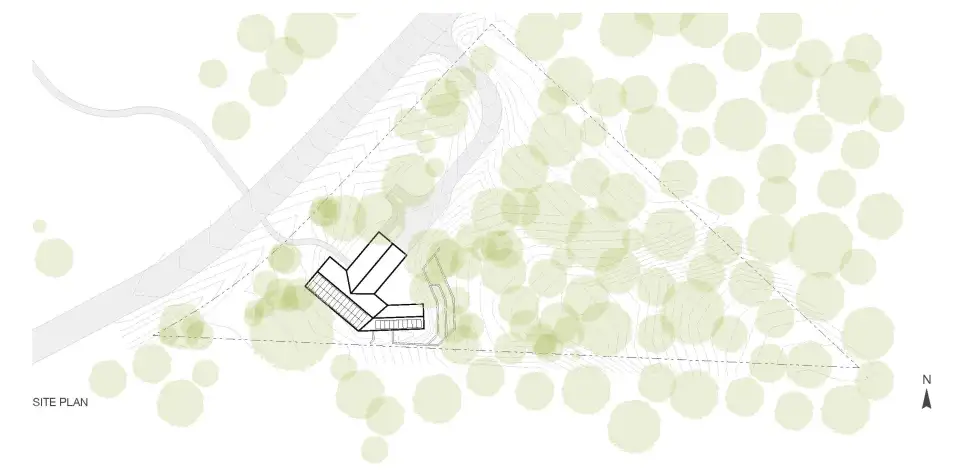
The northern and eastern portions of the property are more densely wooded, while the southwest- and south-facing sides of the home are significantly less shady. This is not likely to change, as the adjacent property to the south is undeveloped and the land on the other side of the property line is a depression where a small lake had once been; it is not a suitable place to build much of anything. Consequently, there were no privacy concerns and Padget and Harrington oriented the home so as to take full advantage of the southern exposure and to maximize solar gains in the winter.
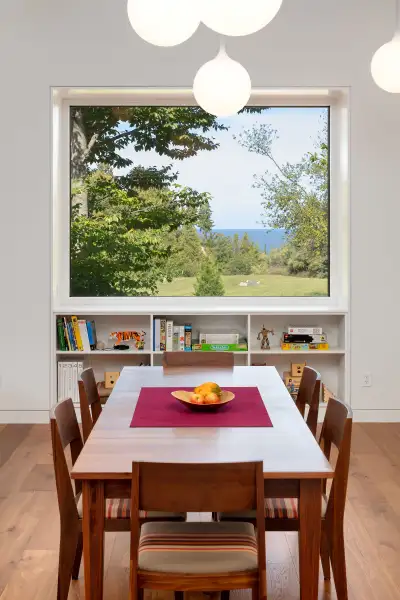
The siting on the property influenced its massing and the delineation between the home’s public and private spaces. As the wing of the home that extends to the east and runs along the southern border of the property is secluded from the public road and other residential properties, it is where the more private sections of the home are located. This wing includes the primary suite, which consists of a bedroom and two walk-through closets that enter into the spacious primary bathroom, as well as the laundry room and a screened-in porch. Keeping in mind future mobility issues, this area is all on the same floor. The attic is used solely for storage and housing the mechanical systems, including a Zehnder Comfoair Q450 for ventilation and a Rheem domestic hot water system. The condenser for the Mitsubishi heat pump system is located on the exterior of the easternmost wall to protect it from the wind and snow off Lake Michigan.
The more central portion of the home is sunk into a slope, thereby creating two levels. The lower floor contains semi-private accommodations for guests, as well as an exercise room, bathroom, root cellar, and greenhouse. Meanwhile, the top floor is on the same level as the primary suite and includes the kitchen, dining room, and living room. The open floor plan of this space, combined with the cathedral ceiling of the double-height dining and living rooms, makes it ideal for hosting. The room is also oriented in such a way as to frame a magnificent view of Lake Michigan through the dining room window.
Extending to the northeast from the kitchen is a mudroom that serves as a vestibule from which one can either exit out the front door or go into the garage. Both the mudroom and the garage are unconditioned. The front door leads down the steps to the path leading to the lake, or to a covered exterior porch and walkway that runs the length of the garage and is used for semi-protected access to the driveway.
In total, the treated floor space is just over 2800 ft2, though that excludes some of the most beloved features of the home. The unconditioned root cellar and the greenhouse on the bottom floor are central to the couple on account of the priority they place on eating well and making the most of the thriving artisanal food scene on in this part of the state. The root cellar gives them space where they can store their own canned and fermented foods, as well as cheeses, wines, and ciders from around the Leelanau and Traverse City. “They want to keep their food sources as local as possible,” Padget says. The root cellar takes advantage of being partially below grade and enjoys stable temperatures. It also houses the heat pump for the water heater, which helps moderate the room’s temperature and humidity levels.
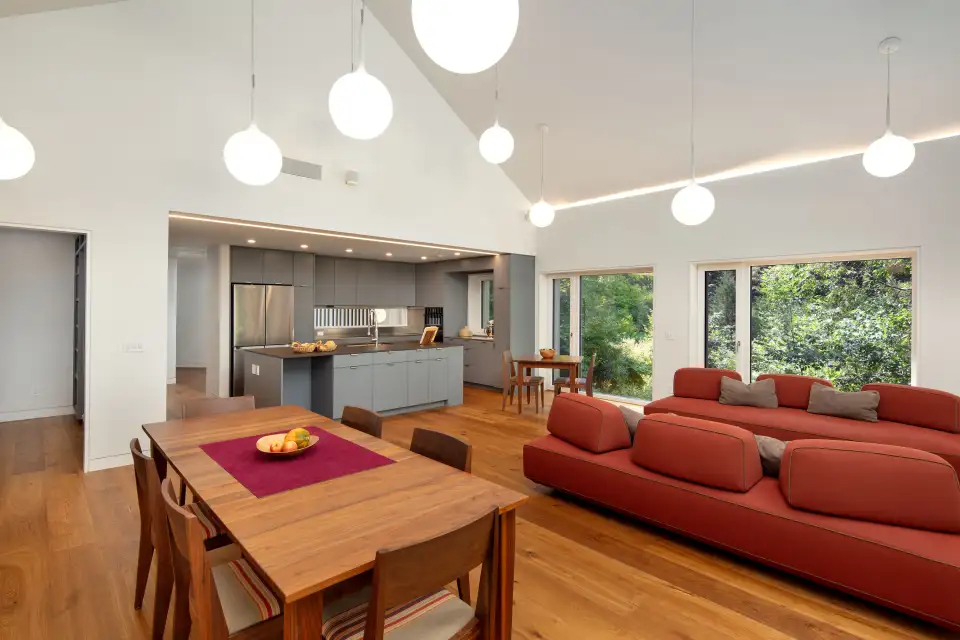
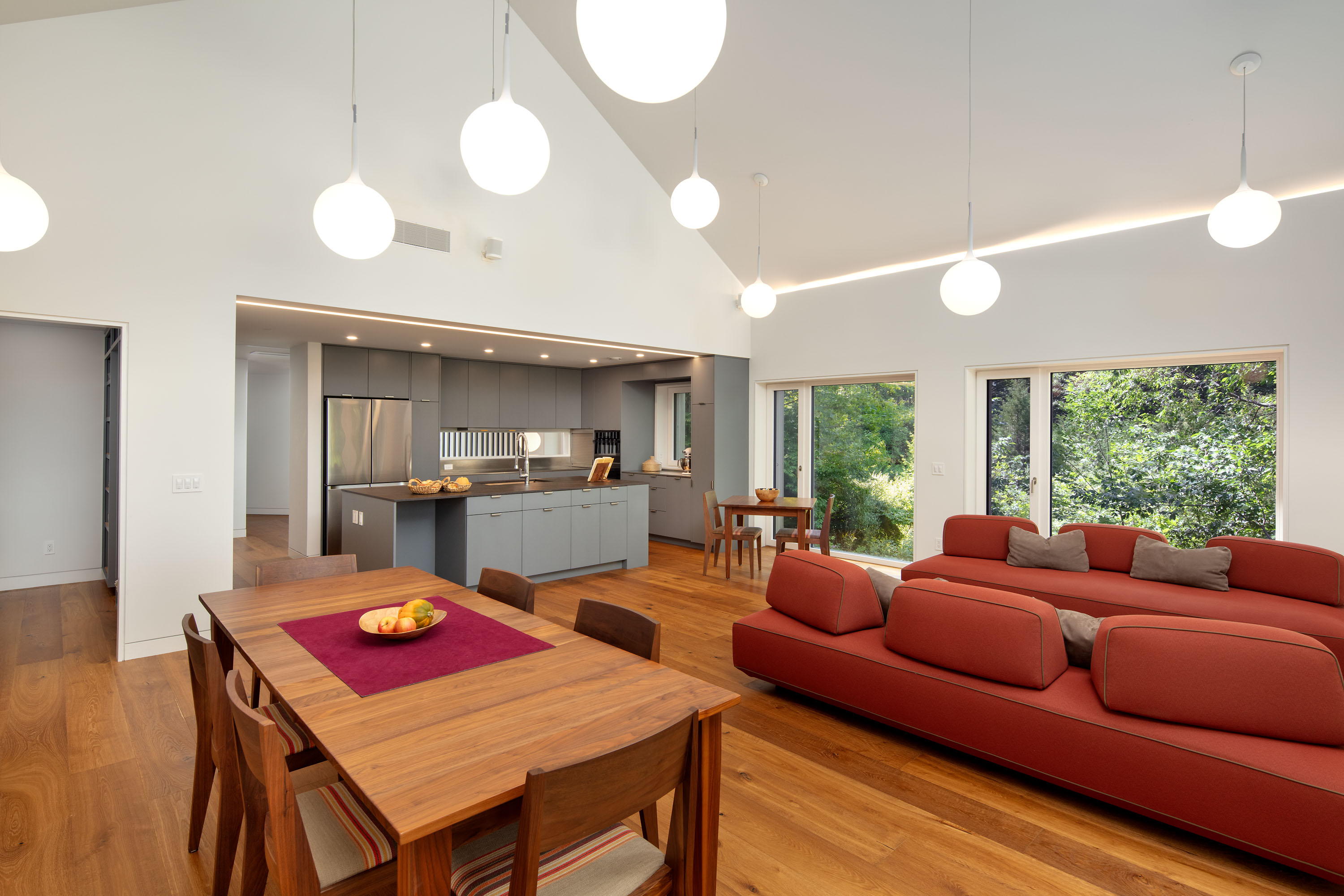
The open living and dining rooms
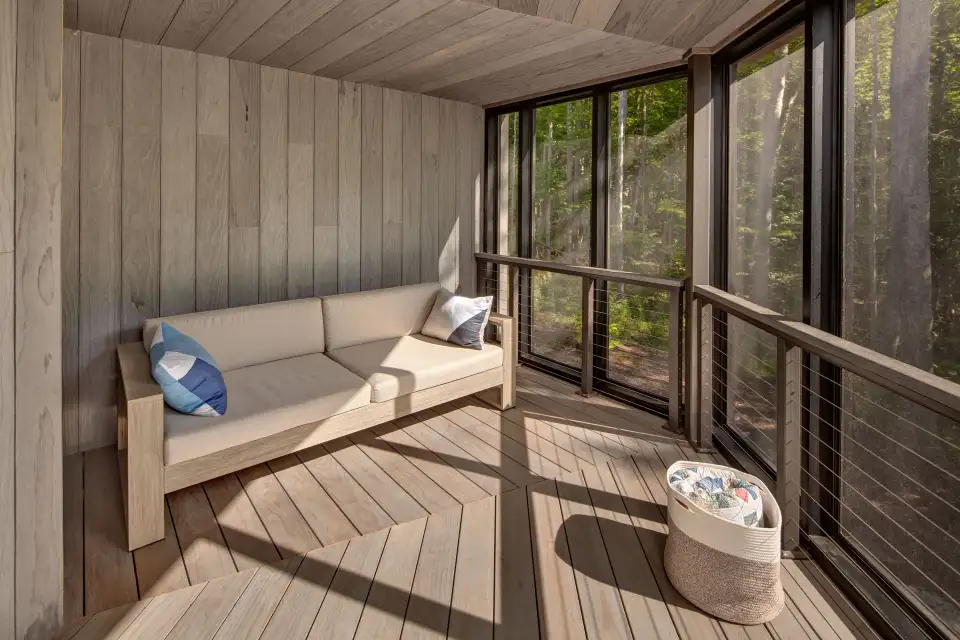
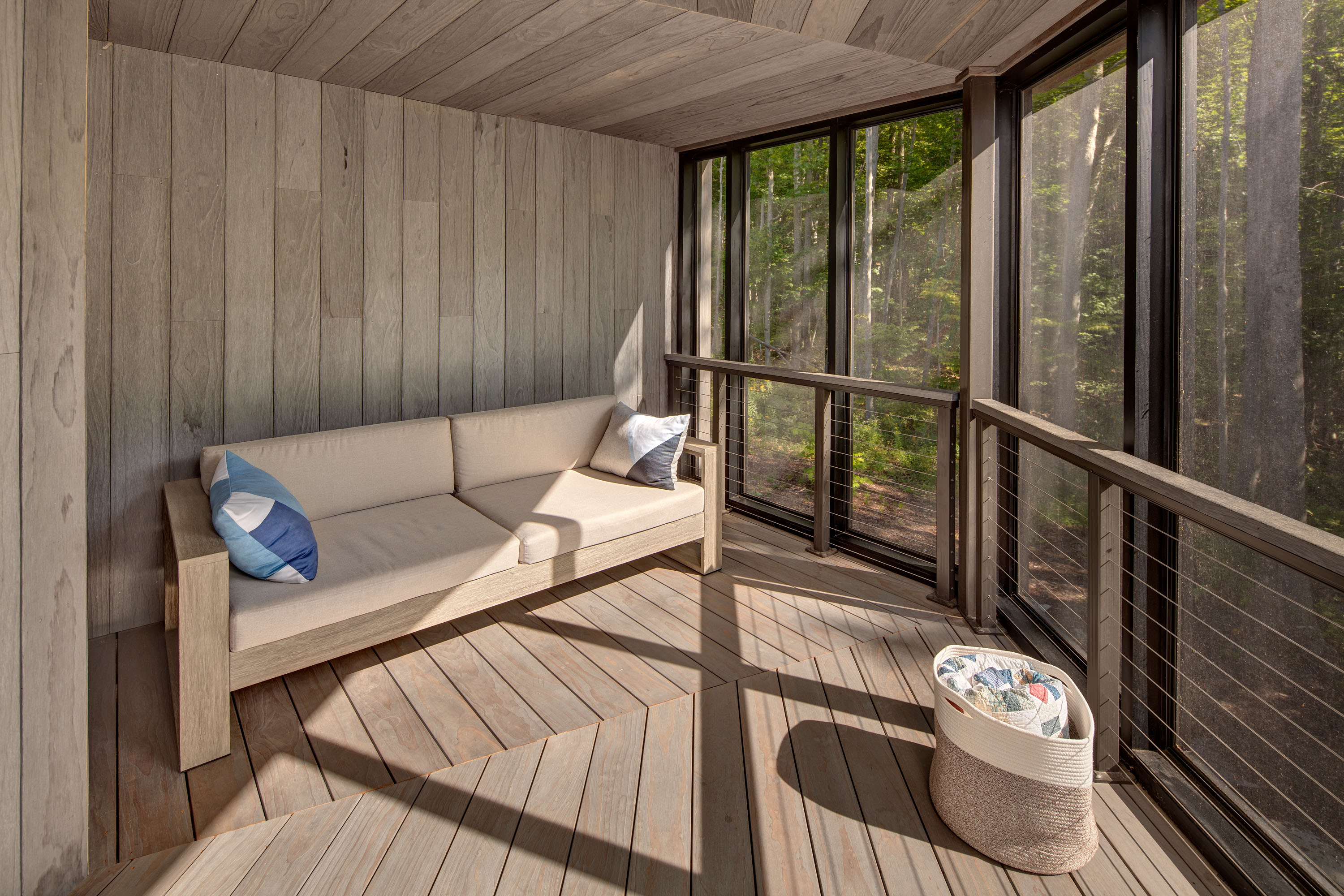
The porch area.
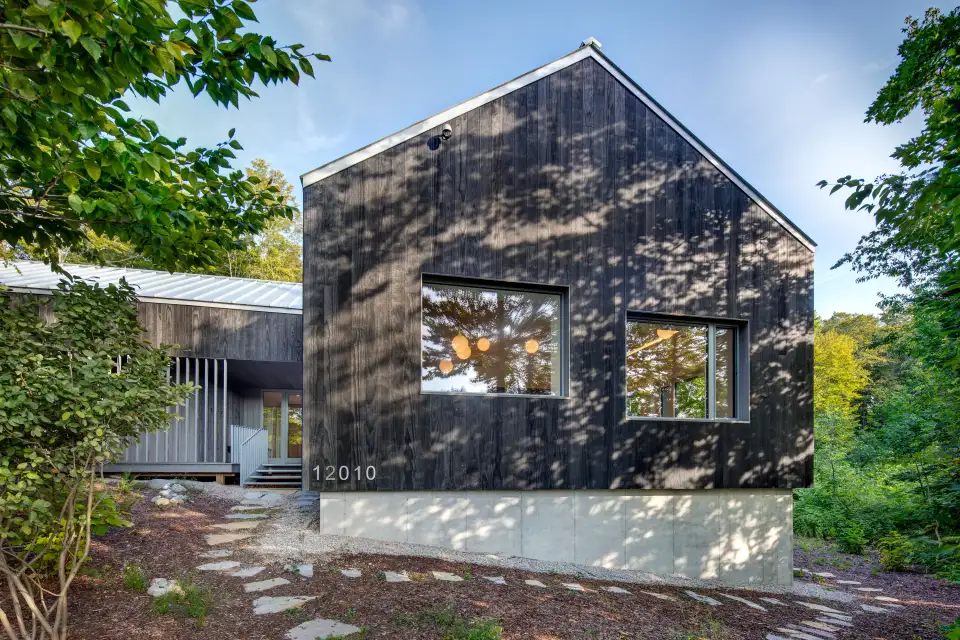
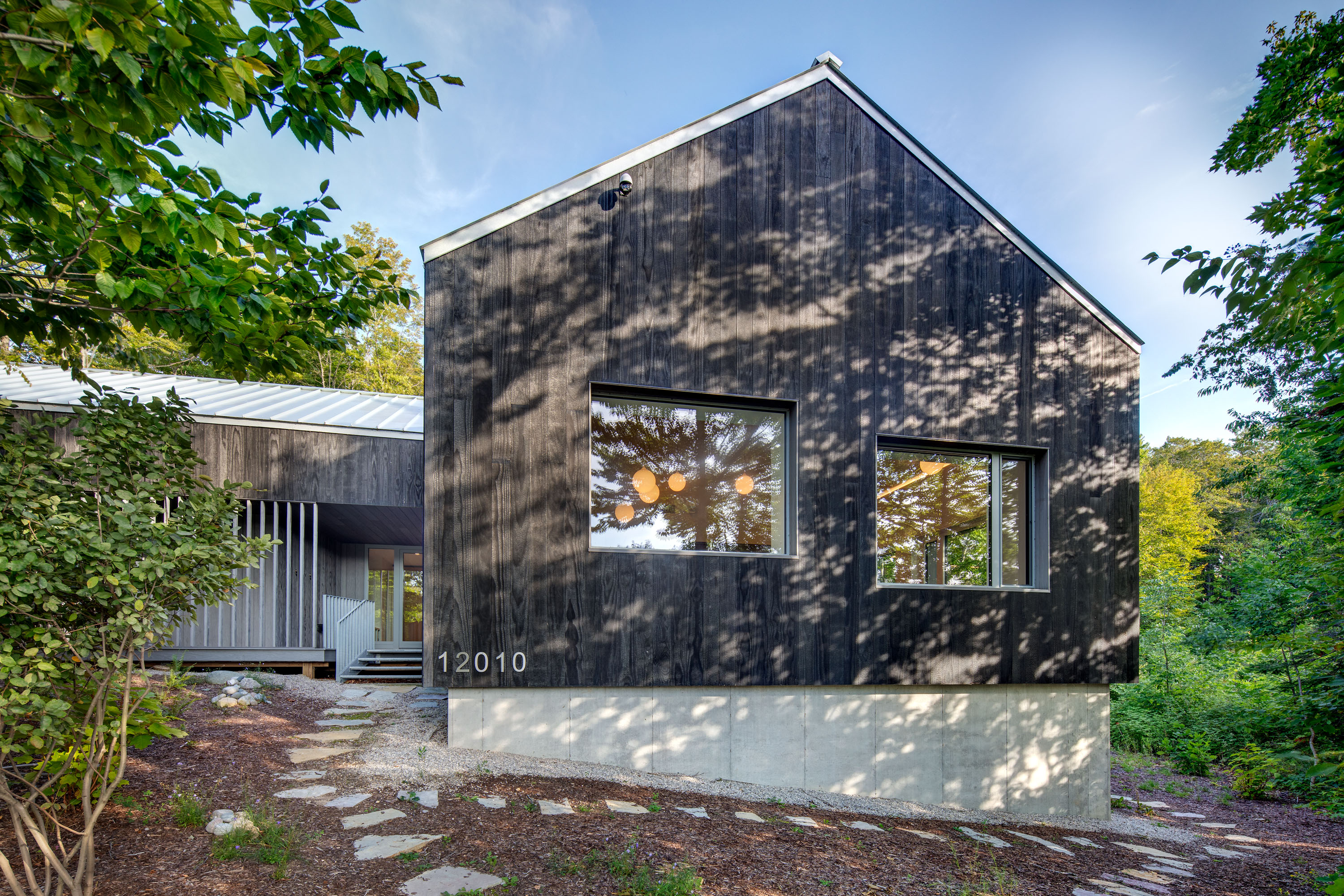
The exterior of the home from the public street.
Meanwhile, the low-angle greenhouse allows them to capture more solar radiation during shoulder seasons to stave off the ever-present risk of frost. To provide more control over the environment within the greenhouse, it has been outfitted with a Ground Air Heat Transfer (GAHT) system that has been patented by Ceres Greenhouse Solutions, who worked as the greenhouse consultants on the project. The GAHT system operates in a similar manner to a geothermal heat pump by relying on the thermal mass of the earth and uses only a few small fans to push air into pipes installed in the soil below. Hot air is cooled as it goes through the piping, while warmer air can be drawn up from the earth during nights and cold snaps.
Above the greenhouse is a covered but unconditioned porch. The area may not get a lot of use in the winter, but the sound of the waves from Lake Michigan and the cool nighttime air makes it a great place to sleep in the summer. If they want to stay inside, they can also open the windows and doors, allowing for cross-ventilation. Padget notes that leaving the front door and porch doors open provides a pleasant cross breeze that keeps the house comfortable during the warmer months when the owners don’t want or need to use air conditioning.
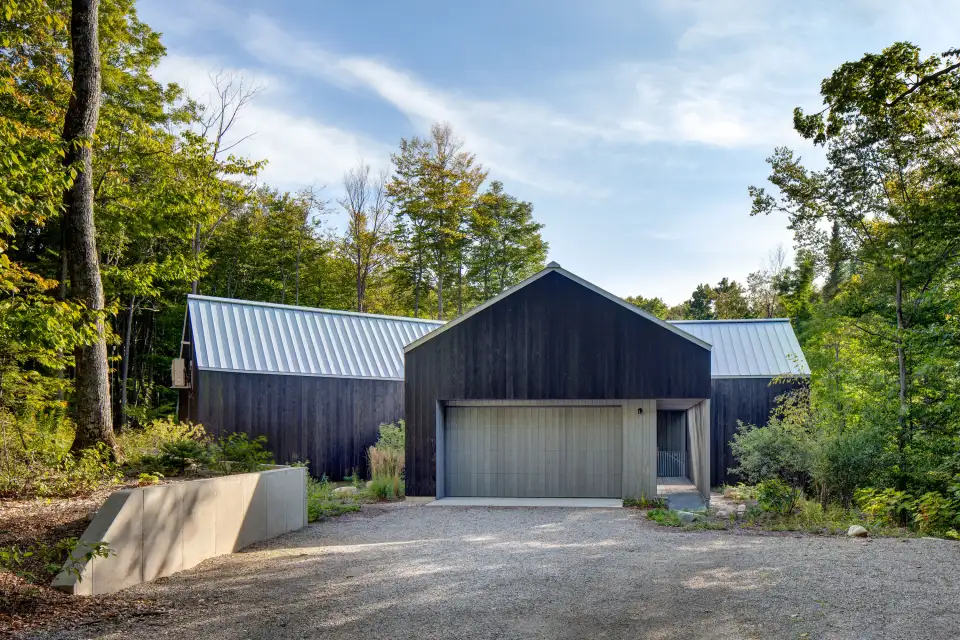
Passive Protection
Though the detailing was not always easy, and the geometry was more complex than is typical in a Passive House home, Harrington and Padget relied on several passive design solutions on the exterior to ensure not only comfort but durability—especially when faced with huge and steady accumulations of snow. The average annual snowfall in Leelanau County is 115 inches!
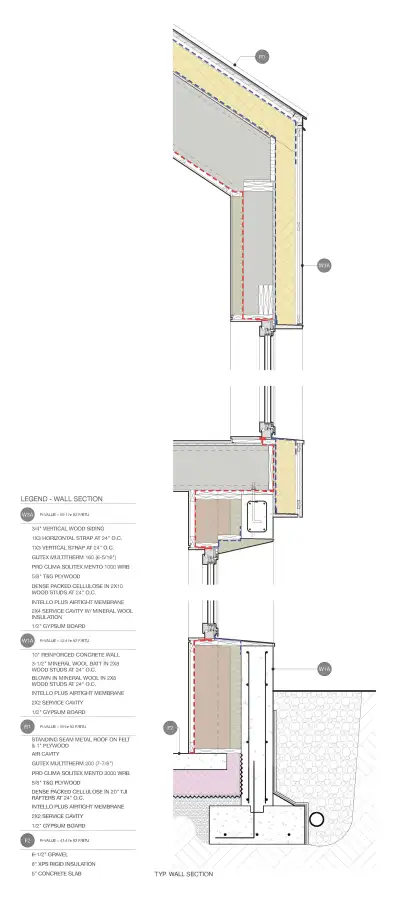
To start, the team was conscientious about preserving the existing trees on the western perimeter of the property to shield against lake-effect snow. Secondly, the house was topped with steep-pitched metal roofing without gutters to easily shed snow. Third, the concrete foundation and exterior on the ground floor is recessed to further distance it from the shedding snow. It is also surrounded by gravel to encourage drainage and avoid pooling when the snow melts. Finally, the additive, Xypex, was added to the exposed concrete, which Harrington notes makes the concrete become more water resistant as time goes on. Though Padget and Harrington were reluctant to use so much concrete on account of its relatively high embodied carbon (and considered using natural stone as an alternative), they recognized that its low cost and superior durability, especially when combined with the properties of the Xypex, made concrete the most practical option. “We could have snow sitting against this wall all season, and it will not become an issue,” Padget says.
Diving into the assemblies, the foundations for the two wings that extend from the central portion of the home are slab on grade, while the foundation for the central portion is a decoupled slab (see Figure 2) with limited XPS insulation beneath the slab. The average R-value for the foundation is 42.
The wall assembly for the lower level was also designed for weather extremes. The interior insulation layer is composed of Thermafiber INSUL-FILL Blown-In Attic Mineral Wool Insulation within an 11-inch cavity and a 3.5-inch layer of Thermafiber ULTRABATT insulation installed next to the concrete wall. Both types of insulation are hydrophobic. The exterior insulation layer from the upper level extends past the floor joist to over-insulate the top portion of the wall. Padget notes that the floor joist also contains blown-in cellulose.
For the upper floor and the two wings (see Figure 3), the wall assembly is composed of cladding from reSAWN Timber Co, which sits exterior to the Pro Clima Solitex Mento 1000 WRB with TESCON Vana tape, an insulation layer of Gutex, plywood sheathing, blown-in cellulose between the studs, and then an Intello air barrier. The average R-values for the lower and upper floors are 52.43 and 69.13, respectively. The roof is approximately 24 inches thick and has an average R-value of 98.98. They achieved this by filling in the joists with cellulose and adding a layer of Gutex on top of the Solitex Mento 3000 WRB. On the roof itself sits a PV array consisting of 38 panels that is modeled to produce 17,254 kWh/yr.
The triple-pane windows and doors were manufactured by Zola Windows and include models that are both tilt and turn (U-value 0.15) and fixed (U-value 0.12). The door models, also from Zola, include ThermoWood (U-value 0.11) and ThermoPlus Clad (U-value 0.16 – 0.20).
Building in Michigan
Construction was neither easy nor quick. Ultimately, it lasted four years. As was the case with many projects around the world, there were significant delays associated with the COVID-19 pandemic, but there were also several obstacles that arose because of the novelty of Passive House construction in Michigan. Harrington notes that sourcing high-performance components, as well as many low embodied carbon materials, took a lot of additional effort. One notable exception was cellulose, which has become a standard insulating material in the state.
The general contractor, Endura Performance Homes, was another positive exception, as he had received his Passive House certified tradesperson training through Phius. Additionally, he had worked with Habitat for Humanity and private owners around the Traverse City area on sustainable and low-energy projects. The same could not be said for the subcontractors and tradespeople, who had very limited familiarity with Passive House design and were at times incredulous about the level of care that was needed when air sealing or installing such an enormous amount of insulation. Conversely, they did appreciate how warm and quiet the house was during construction and how working with natural materials led to far less irritation than other types of insulation—particularly fiberglass.
It can be a difficult concept to fully appreciate until you’re inside a Passive House, Padget explains. “You’re experiencing the absence of annoying things,” including noise, dust, and allergens. Despite the challenges of building during the pandemic and learning the nuances of Passive House while on the site, “They were happy with the space they created.”
Project Team
Architect: pHdesign
MEP: Baucraft Engineering
Structural/Civil Engineer: Erin W. Parker, PE
Greenhouse Consultant: Ceres Greenhouse Solutions
Passive House Certifier: Passive House Academy
Passive House Metrics
Heating demand |
4.54 |
kBTU/ft2/yr |
Cooling demand |
2.43 |
kBTU/ft2/yr |
PER |
26.87 |
kBTU/ft2/yr |
Air tightness |
0.6 |
ACH50 |