As sustainability becomes a crucial focus in the construction industry worldwide, New Zealand finds itself on the cusp of transformative change. Research in 2023 revealed significant insights into the upfront carbon emissions for New Zealand fenestration systems. However, the results are relevant for any product manufactured internationally and shipped to other shores for consumption. This article explores how these insights can benefit manufacturing businesses within the construction sector seeking to thrive in an era increasingly defined by sustainability.
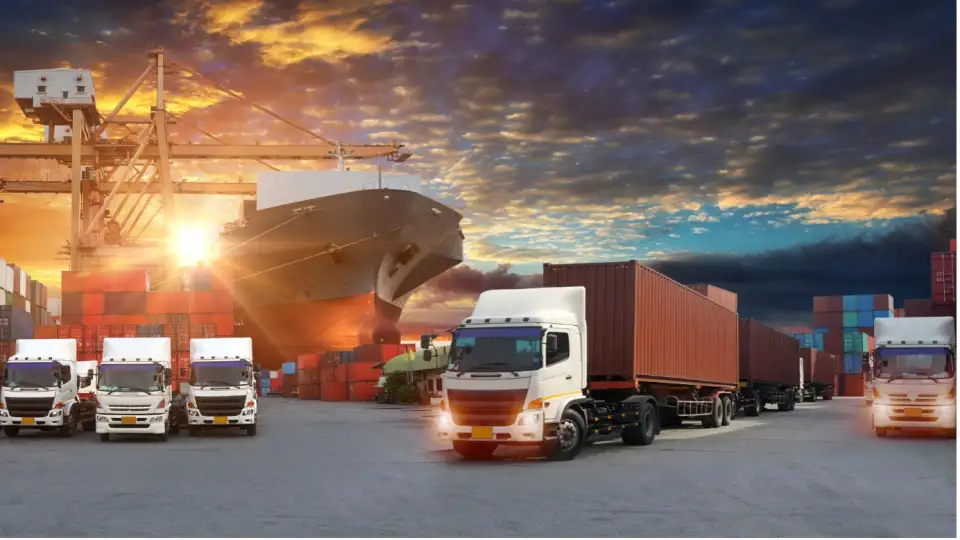
Upfront Carbon Emissions and the Built Environment
Sustainability in Construction
According to the United Nations Environment Program (2023), buildings and the construction sector are responsible for 37 percent of global emissions. New Zealand's built environment accounts for 20 percent of the country's emissions. Although New Zealand’s overall global emissions are relatively small, its per capita emissions are among the highest in the Organization for Economic Co-operation and Development (BRANZ, 2024).
Building and construction emissions encompass everything from extracting raw materials to manufacturing, installing, using, and disposing of building products. One critical aspect often overlooked in the drive to reduce carbon emissions is upfront carbon emissions, which are those embedded in materials throughout their life cycle. The current building code in New Zealand focuses solely on the operational carbon emissions related to heating and cooling a building. A focus on operational carbon fails to consider the carbon footprint produced during raw material extraction, production, manufacturing, installation, and end-of-life phases.
Why Upfront Carbon Matters
In 2022, New Zealand introduced its first emissions reduction plan to decarbonize various sectors (Ministry of Environment, n.d). Despite these efforts, the country is not on track to meet its targets in 2024, necessitating the purchase of international carbon offsets equivalent to 102 megatonnes of CO2, comparable to burning 51 million metric tonnes of coal.
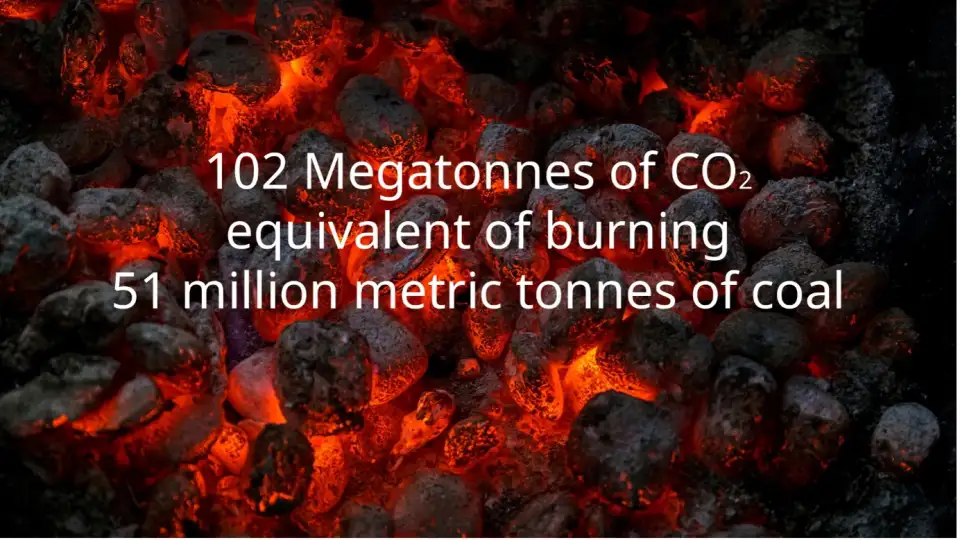
This reliance on volatile international carbon markets underscores the need to address upfront carbon emissions. This is because focusing solely on operational carbon does not address other significant sources of emissions.
The Role of Fenestration Systems
Fenestration systems—windows, doors, and skylights—play a pivotal role in the built environment's overall carbon footprint. As the lowest-performing thermal element in any wall assembly, fenestration frame material choice can impact upfront and operational carbon emissions.
Here's how fenestration systems influence upfront and operational carbon emissions:
Energy Efficiency: Fenestration systems can significantly affect a building's energy performance. Poorly designed or low-performing fenestration allows for excessive heat loss in winter and heat gain in summer, leading to increased reliance on heating and cooling systems. This, in turn, raises operational energy consumption and associated carbon emissions.
Frame Material: The choice of frame materials (such as wood, aluminum, fiberglass or uPVC) influences the thermal performance of windows and the carbon emissions related to their production (upfront carbon). For instance:
Thermally broken aluminum windows and doors offer good energy efficiency and are highly recyclable, making them an environmentally friendly choice. Their durability enables them to last for decades, reducing ongoing maintenance requirements and the frequency of replacements. However, it's important to recognize that aluminum production is energy-intensive and generates significant carbon emissions, particularly if the material is not sourced from recycled inputs or manufactured using fossil fuels. Additionally, these systems can experience thermal bridging, undermining their energy efficiency if not properly designed or installed. Lastly, failing to recycle these products at the end of their life cycle can contribute to unnecessary landfill waste.
Wooden windows and doors can act as a natural carbon sink prior to production by capturing CO2during its growth and can be a renewable resource if sourced sustainably. They offer good energy efficiency, reducing heating and cooling costs, while their production typically requires less energy compared to materials like aluminum or vinyl. However, negative impacts include unsustainable logging, which can lead to deforestation and increased CO2 emissions. Additionally, wooden products are prone to decay and insect damage, leading to waste, and treatments used to enhance durability can have adverse environmental impacts.
Fiberglass windows and doors offer good insulation, reducing energy consumption and greenhouse gas emissions. They are durable but not biodegradable, contributing to landfill waste. Additionally, the manufacturing process can release chemical emissions and volatile organic compounds, posing possible environmental and health concerns.
uPVC windows and doors provide good insulation that reduces the need for heating and cooling, leading to lower energy consumption. However, the manufacturing process of uPVC (unplasticized polyvinyl chloride) involves extracting and processing fossil fuels, which can emit harmful pollutants. Although uPVC can be recycled, not all recycling facilities accept it, and if disposed of in landfills it can take hundreds of years to decompose, contributing to long-term environmental pollution. Moreover, petroleum extraction, the primary raw material for uPVC, can result in habitat destruction and other environmental damage.
Life Cycle Considerations: The carbon impact of fenestration systems must be evaluated across their entire life cycle, including manufacturing, installation, operation, maintenance, and eventual disposal or recycling. Choosing materials with lower upfront embodied carbon from raw material extraction and manufacturing processes is essential for minimizing the overall carbon footprint.
Sustainable Design: Incorporating high-performance fenestration with appropriate U-values, solar heat gain coefficients ("SHGC"), and visible light transmission ("VLT") can reduce energy demands for lighting and climate control, thus decreasing operational carbon emissions. Investing in energy-efficient technologies can enhance performance, such as double-glazing warm-edge spacers combined with advanced soft-coat low-emissivity coatings.
Additionally, the electricity grid mix available at the place of manufacture can also impact upfront carbon emissions. Interestingly, New Zealand's relatively green electricity grid (77% renewable energy) means upfront carbon emissions can significantly outweigh operational emissions (Transpower, n.d). However, each manufacturing region will have a different electricity grid mix, and you could look at your local grid mix to understand the impact of manufacturing activities near you (EIA, n.d). The higher the electricity generation from renewable sources, the lower the impact from upfront carbon emissions.
The Impact of Legislation and Competition
The New Zealand government recently signaled potential changes in building material rules to make the use of overseas products easier and cheaper (Beehive, 2024). While this could increase competition to reduce housing prices, it raises concerns about the quality, resilience, and sustainability of these imported materials.
Local manufacturers must emphasize the unique benefits of locally made products. With New Zealand’s green electricity grid and local aluminum smelter, New Zealand-made products could offer lower upfront carbon emissions. A similar argument could be made in other nations or regions with local aluminum smelters and relatively clean electricity grids (e.g., Iceland, Quebec). Therefore, adequate consideration of embodied carbon—emissions associated with manufacturing, transporting, constructing, and disposing of products—is essential.
The Importance of Environmental Product Declarations (EPDs)
Environmental Product Declarations ("EPDs") offer comprehensive data about a product's carbon footprint, encompassing energy consumption, water usage, and other environmental indicators. An EPD is usually valid for five years and generated according to the relevant standards. Construction EPDs are based on the International Organization for Standardization (ISO) 14040/14044, ISO 14025, or ISO 21930 standards, or on the European Union’s EN 15804 standard. EPDs can provide the transparency needed for architects, designers, builders, and homeowners to make informed decisions.
However, not all EPDs are created equal. Our research highlighted discrepancies in international EPDs where data from multiple suppliers were aggregated, potentially masking significant differences in emissions. In some cases, only a single product (casement window) was evaluated, assuming that the window data would be ascribed to sliding and hinged doors. Our concern with this practice is that sliding and hinged doors have significantly higher kg CO2-eq per m2 of glazing.
Another issue is that most European EPDs used in New Zealand have yet to be converted for use in New Zealand. This means European EPDs fail to account for transport emissions to New Zealand. Additionally, New Zealand's carbon emissions inventory only allocates international shipping emissions as a footnote and does not consider them a contributor to New Zealand emissions (Climate Change Commission, n.d.). Ignoring international shipping emissions suggests that as long as the emissions were produced elsewhere, then the mindset is it's not our problem.
Advocating for More Localized EPDs
New Zealand is a group of small islands in the southern hemisphere, far from most manufacturing hubs. Therefore, New Zealand-specific EPDs can bridge the gap for local manufacturing businesses, thus ensuring accurate representation of emissions data, including packaging and transport impacts. These EPDs can highlight the advantages of New Zealand's green grid products and low upfront carbon materials, such as aluminum from Tiwai Point (NZAS, n.d.) or recycled aluminum from McKechnie Aluminium (McKechnie, n.d.). These advantages hold true within any locality that is far away from major manufacturing hubs and has a relatively clean grid.
Understanding shipping distances can indicate alarmingly high upfront carbon emissions for other countries. However, the 2023 upfront carbon emissions study on the importation of fenestration systems to New Zealand highlighted that more than just the distance travelled can lead to high upfront carbon emissions.
Critical Study: Fenestration Upfront Carbon Emissions
In 2023, the first stage of our comprehensive research project focused on the front end of the life cycle analysis of building materials. We selected two BRANZ model houses, MH1 and MH2—standard New Zealand identifiers for anyone versed in local thermal modeling. BRANZ (Building Research Association of New Zealand) is a prominent organization dedicated to enhancing the quality, performance, and sustainability of buildings in New Zealand. Established in 1960, BRANZ conducts rigorous research and provides valuable insights, tools, and resources for the New Zealand building and construction industry.
Our approach was to deep dive into the material coefficients of kilograms of CO2 equivalent (kg CO2-eq) for all materials associated with locally and internationally sourced uPVC and thermally broken aluminum systems from China, Germany, and New Zealand. We chose these frame materials because the construction industry in New Zealand has heavily relied on cold aluminum frames for building windows and doors since the 1960s. Aluminum frames were popular because they were durable, lightweight, and corrosion resistant. A building code change in 2008 introduced double glazing as a standard feature. However, it has only been a recent 2022 code change that has shifted the industry towards increased frame energy efficiency for the window and door market. While cold aluminum frames are still available on the market, there has been a significant shift towards thermally broken aluminum frames and an increased use of uPVC windows and doors. Of course, other frame options are available, such as steel and wooden frames. However, the predominant frame material in New Zealand remains aluminum based.
Note: the author of this article is an employee of Technoform Bautec Asia Pacific an international manufacturer and supplier of thermally broken components for windows, doors and facades. At the time of writing the fenestration carbon analysis report the author was an independent consultant who has only recently taken up a position with Technoform Bautec Asia Pacific.
Selection and Sourcing
The study considered house lots of windows and doors (windows and doors packages in North American terminology) manufactured internationally and shipped to New Zealand and containerized long lengths shipped to and manufactured in New Zealand. We calculated the upfront carbon impact, including raw material extraction, manufacturing, and local and international packaging and transport emissions.
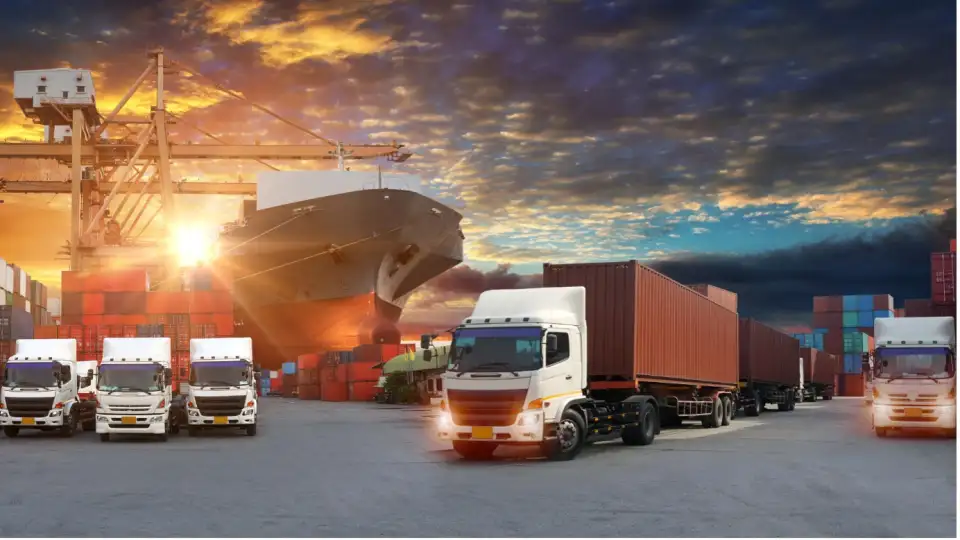
Critical Analysis
We aimed to answer a pivotal question:
"Would window frame material choices change if we considered the upfront carbon impact from international transport and packaging requirements to the remote island of New Zealand?"
Months of data analysis revealed significant insights, which are reflected in the detailed charts of our report. These charts are accessible via a QR code provided below or by clicking this link: Technoform upfront carbon analysis of fenestration systems.
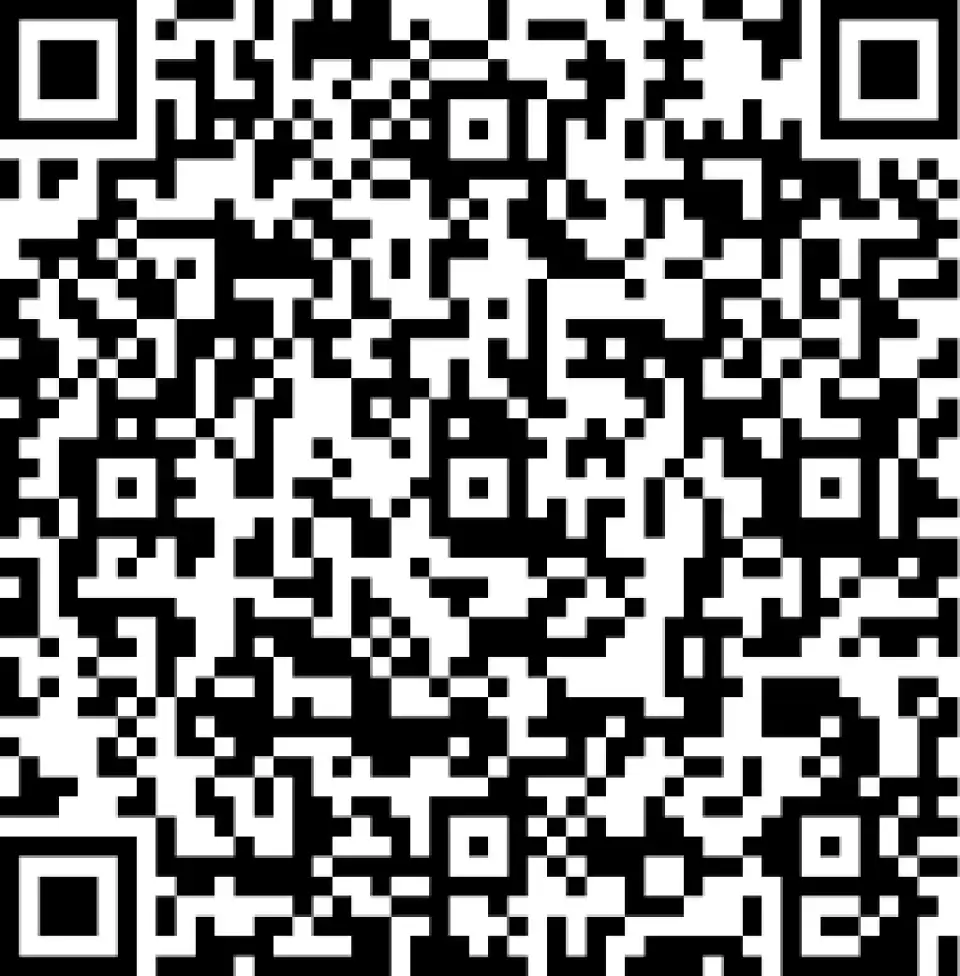
Domestic vs. International Production Emissions
Our top-level results revealed a stark contrast in carbon emissions between locally manufactured and imported materials:
Lowest Emissions: Windows and doors manufactured in New Zealand from New Zealand smelted aluminum had the lowest upfront carbon emissions. This New Zealand manufactured house lot then became the baseline benchmark for further comparisons in the results.
Impact of Shipping Distance: Longer shipping distances and heavier materials significantly increased the upfront carbon emissions for imported house lots.
Impact of high fossil fuel manufacturing: Even with shorter transport distances, raw material production and manufacturing in high fossil fuel manufacturing locations generated the highest upfront carbon emissions.
Case Study: Germany and China
Germany: Shipping a uPVC house lot from Hamburg to Auckland is a 24,697-km journey. This distance added a worst-case scenario of 1,110 kg CO2-eq from packaging and transport alone, equivalent to burning 554 kg of coal. There was a 10.3 percent increase in emissions compared to the baseline house lot manufactured in New Zealand using aluminum smelted in New Zealand. These international transport emissions are unlikely to be included in any EPDs provided for internationally sourced products.
China: With a shorter distance of 9,427 km to reach New Zealand, the emissions impact from transport and packaging created a worst-case scenario of 714 kg CO2-eq for a uPVC house lot. However, China's upfront carbon emissions associated with manufacturing were markedly higher due to coal-powered manufacturing plants. As such, aluminum house lots from China resulted in 10,189 kg CO2-eq, comparable to burning 5,093 kg of coal, making a 139 percent increase compared to the baseline house lot manufactured in New Zealand using aluminum smelted in New Zealand.
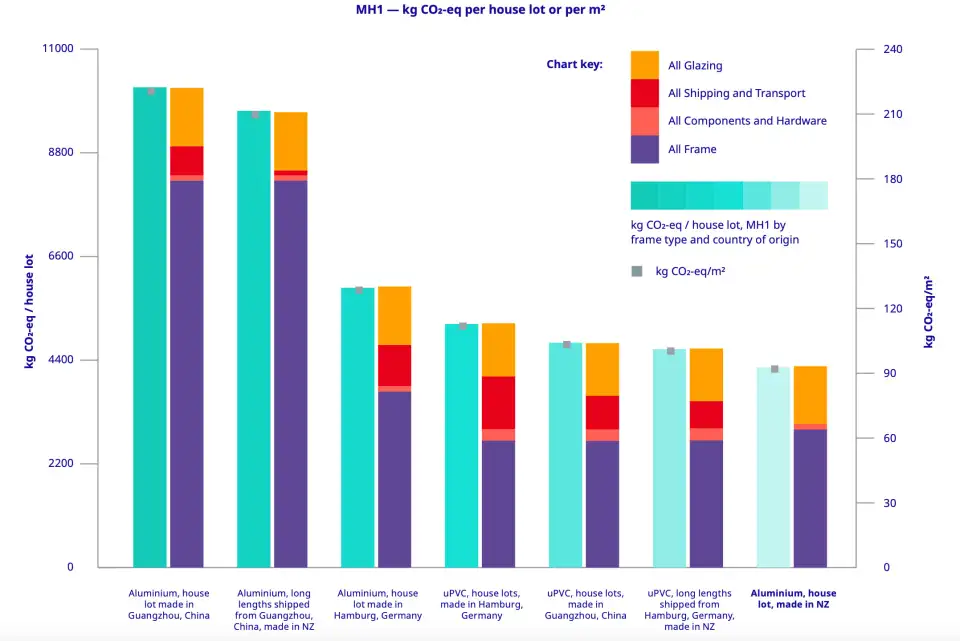
Supporting Local Manufacturing
The report's findings underscore the importance of supporting local manufacturing to avoid the high upfront carbon emissions associated with international supply chains. This narrative is not unique to any country; it applies globally, wherever local manufacturers compete against international imports.
For too long, local manufacturers have been under immense price pressure due to the high production volumes of international competitors. These competitors often operate under less stringent legislative constraints, particularly those concerning people-centric labor laws and anti-slavery requirements.
The fashion industry has been grappling with similar challenges for many years, and many companies have been criticized for utilizing international manufacturing options that frequently circumvent stringent labor laws, resulting in lower costs, fostering poor working conditions, and contributing to severe human rights violations. It is high time the construction industry also recognizes that cheaper imports come at a significant cost—both ethically and environmentally.
Just as the fashion industry has begun to take steps towards more ethical and sustainable practices, the construction industry must also confront the harsh reality that lower-priced imports are not a solution. By supporting local manufacturing, industries can ensure fair labor practices, reduce environmental impact, and promote sustainable economic development.
Recommendations for manufacturers and distributors
Develop a local Environmental Product Declaration for each country your product is sold into.
If using international suppliers, include an addendum detailing packaging and transport emissions to the country of resale.
Recommendations for architects and specifiers
Insist on local EPDs for locally produced and imported products.
Make your suppliers responsible for correctly identifying current hidden upfront carbon emissions from international transport and packaging.
Recommendations for legislators
Keep up the effort to reduce carbon emissions in the construction industry.
Suppliers will likely only take the steps necessary to make upfront carbon emissions more transparent to consumers through legislative measures.
What Happens if Imports Increase?
The influence of imported fenestration systems on New Zealand's carbon footprint could be significant. At the current rate of building activity, the increased importation could add up to 213 million kg CO2-eq per year, akin to burning 106,000 metric tonnes of coal. And that can be exponentially higher if we consider all the products imported into New Zealand to build just one house.
New Zealand must prioritize reducing reliance on offshore carbon credits and focus on internal improvements, maximizing local resources, and making incremental, meaningful changes towards a sustainable built environment.
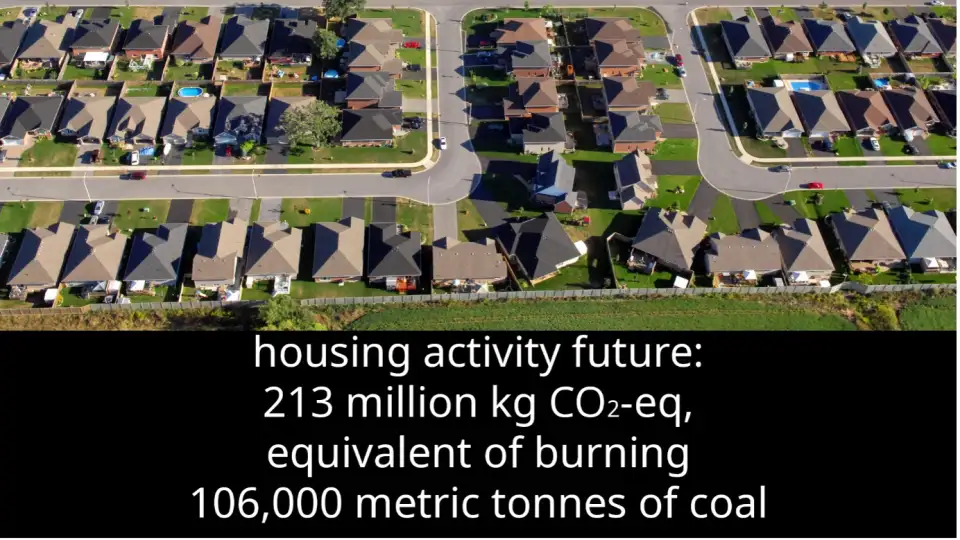
What Does the Future Hold?
The construction industry in New Zealand is poised for significant shifts towards greater sustainability. By acknowledging and addressing upfront carbon emissions in fenestration systems, local businesses can comply with emerging policies and showcase the unique advantages of New Zealand-manufactured products. Emphasizing accurate, transparent data through locally prepared EPDs can position these businesses as leaders in sustainable construction, ensuring long-term growth and resilience in a competitive market. This statement holds true not only for New Zealand, but for any market where locally manufactured products can offer a more ethical or sustainable product than international competitors.
As we move forward, the importance of sustainability in the construction industry cannot be overstated. Reducing upfront carbon emissions represents a critical opportunity for businesses to contribute to a greener planet and thrive in a market that increasingly values sustainability. By leveraging transparent and insightful data, New Zealand's construction industry can move towards a more sustainable future, benefiting the environment and economy.
References:
Beehive. 2024. Building products shakeup to lower prices. Retrieved 31 July 2024. https://www.beehive.govt.nz/release/building-products-shakeup-lower-prices
BRANZ. 2024. Reducing greenhouse gas emissions in the construction industry. Retrieved 31 July 2024. https://www.branz.co.nz/sustainable-building/climate-change/reducing-greenhouse-gas-emissions-construction-industry/
Climate change commission. n.d. Review of whether emissions from international shipping and aviation should be included in the 2050 target. Retrieved 31 July 2024. https://www.climatecommission.govt.nz/our-work/advice-to-government-topic/review-on-whether-emissions-from-international-aviation-and-shipping-should-be-included-in-the-2050-target/
Stewart, D. 2023. Upfront carbon footprint analysis of New Zealand fenestration systems. Retrieved 6 August 2024. https://www.eboss.co.nz/assets/EBOSSNOWFiles-2/Technoform_UCFAnalysis_231212.pdf
EIA. N.d. Electricity explained, electricity generation, capacity, and sales in the United States. Retrieved 31 July 2024. Electricity generation, capacity, and sales in the United States - U.S. Energy Information Administration (EIA)
Ministry of Environment. n.d. Emissions reductions. Retrieved 31 July 2024. https://environment.govt.nz/what-government-is-doing/areas-of-work/climate-change/emissions-reductions/
McKechnie. n.d. Sustainability. Retrieved 2 August 2024. Sustainability | McKechnie Aluminium Solutions Ltd
NZAS. n.d. Sustainability. Retrieved 31 July 2024. https://nzas.co.nz/sustainability
Transpower. n.d. Empowering our energy future. Retrieved 31 July 2024. https://www.transpower.co.nz/
United Nations Environment Programme. 2023. Building Materials And The Climate: Constructing A New Future. Retrieved 31 July 2024. https://www.unep.org/resources/report/building-materials-and-climate-constructing-new-future