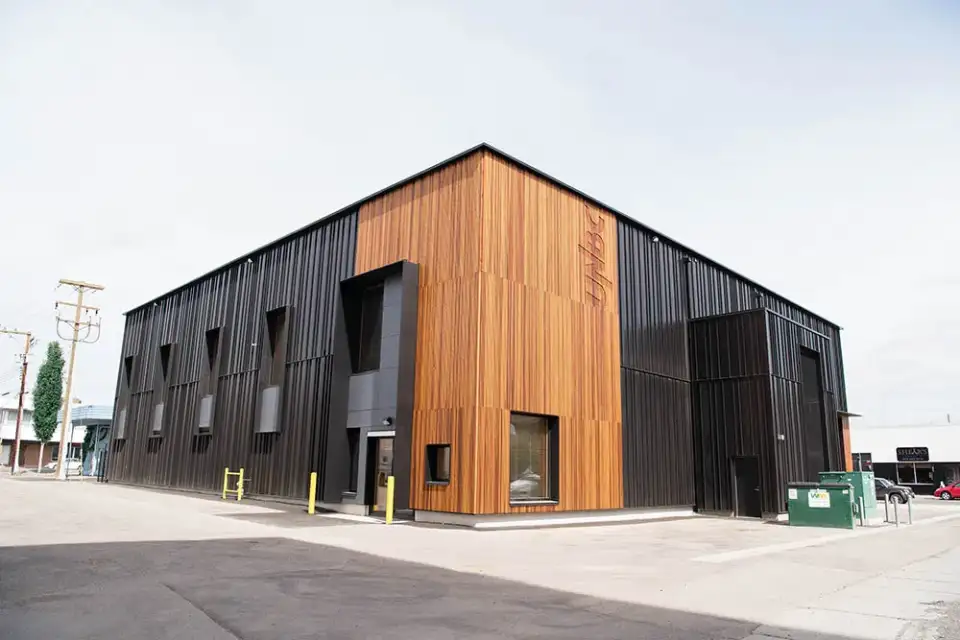
The Masters of Engineering in Integrated Wood Design program at the University of Northern British Columbia (UNBC) equips design and construction professionals with the knowledge needed to apply wood use, building science, and sustainable- design principles to future projects. The program is hosted in Prince George, British Columbia, at the Wood Innovation Design Center (WIDC), an eight-story glulam post-and-beam mixed-use building with a cross-laminated timber core that was at the cutting edge of industry when it was first constructed.
As the program grew, so did the need for increased capabilities within the laboratory. First conceived of in spring 2016, UNBC’s new Wood Innovation Research Lab (WIRL) opened its doors in April 2018. The lab building is constructed with engineered-wood products and received Passive House certification in July 2018.
The WIRL is a 10-meter (33-foot) -tall single-story mixed-use building with a large two-bay lab space as well as a separate classroom and office spaces. The superstructure is composed of mass timber glulam columns and beams on a 6-m (20-foot) grid, and the walls are framed with wood trusses in order to achieve a high thermal performance.
The lab and classroom space is being used by UNBC faculty and students for research and testing related to wood construction and Passive House. The lab is equipped with a concrete strong wall and floor complete with anchors and hold- downs for three-dimensional testing of wooden structures. An overhead crane runs the length of one of the two bays, which allows for the safe maneuvering of large test structures or wood specimens. The shop also includes three universal testing machines, a computer numerical controlled (CNC) cutting machine, and a 34-m2 (366-ft2) wood-conditioning room that is equipped with ventilation and humidification in order to create an ideal environment for normalizing wood specimens to a consistent moisture content.
Meeting the Passive House standard was particularly challenging for this project for three reasons. First, Prince George has a harsh climate that swings from 30°C to –30°C during the year and has 234 heating or cooling days per year. Second, because of the need for a very tall lab space, the building envelope area is rather large compared to the small thermally treated floor area—the denominator in all Passive House energy consumption calculations. Third, the building’s program requirements created some very complex challenges. A large bay door was needed to afford access for semitrucks. The cutting machinery throws off significant dust volumes, which in turn require a large dust extraction system, posing significant airtightness challenges. And the hydraulic pumps for the structural testing equipment generate massive interior heat gains when operating.
The building envelope was framed using dimensional-lumber trusses that were prefabricated into one-side-open wall panels. Due to the thermal performance requirements, the 10-m (33-foot) -tall wall panels were required to be over 500 millimeters (19.7 inches) thick. Framing the panels with upright trusses rather than studs accommodated this thickness in a cost-efficient way and reduced the resulting thermal bridges.
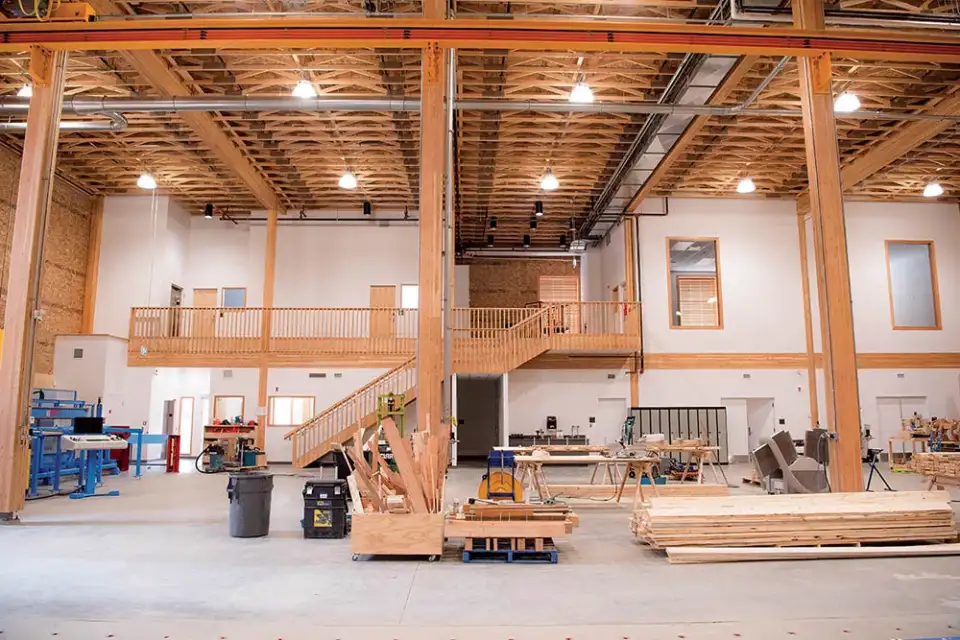
The wall panels were designed with prefabrication in mind, but the local industry—in this case, Winton Homes Ltd., a Prince George-based company that procures the raw materials from a local sawmill—was not yet capable of producing complete panels. Instead, the shipped panels consisted of OSB on the inside, followed by a smart air and vapor barrier membrane for airtightness and vapor diffusion control, and then the 500-mm-thick truss structure. The outside of the panels remained completely open when lifted by crane into place. The builder was able to then seal the seams of the airtight layer by reaching through the wall to the membrane. Once sealed, the panels were closed from the bottom up with another layer of OSB on the outside and simultaneously filled with blown-in mineral fiber.
Exterior to this OSB was a layer of building wrap, then strapping to form a rain screen gap, and the siding. The siding is mostly painted metal with cedar accents. The interior layer of OSB was left exposed as the finishing for the lab portion of the building.
The majority of the windows are located on the south-facing wall, and the window area was optimized to allow for sufficient daylight and views while limiting the overall frame length, as the frames represent the biggest thermal weakness. The aluminum-clad wood-framed, triple-pane windows were placed strategically—about midway through the panels—to minimize thermal losses. Because of the cold climate, the windows selected had a U-value for the installed window of between 0.70 and 0.87 W/(m²K), depending on the size.
Heat losses through the roof were managed by applying an average thickness of approximately 610 mm (2 feet) of sloping EPS insulation. EPS was chosen over the initially designed polyurethane because it has a significantly lower embodied carbon impact.
Reducing thermal losses through the 30-m by 30-m (98-foot by 98-foot) concrete raft slab foundation was quite challenging , because a portion of the foundation is a strong floor: a high-capacity 1-m (3.3-foot) -thick section of reinforced concrete that will be used for structural testing. A high-strength and -density EPS insulation had to be special ordered for installation below this portion of the building, which would be experiencing higher than normal forces. Underneath the foundation 215 mm (8.5 inches) of EPS was applied continuously.
As for airtightness, careful design and planning and meticulous implementation during construction resulted in an impressive achievement that was well above expectations: 0.07 ACH50. The compactness of the building and the simplicity of the envelope worked in our favor, but there were also significant pitfalls.
An overhead shop door was a lab requirement in order to receive materials via a flatbed truck, but it presented a logistical challenge, as these doors aren’t typically airtight or well insulated. The solution was a German-manufactured door that fully seals, thanks to rubber gaskets pressed airtight between each panel and the surface where the door meets the floor, and to an ultra-high-molecular-weight polyethylene profile and track that reduces friction when the door is being opened or closed. The door was tightened against the track after installation to ensure a tight seal while maintaining minimal resistance for raising the door.
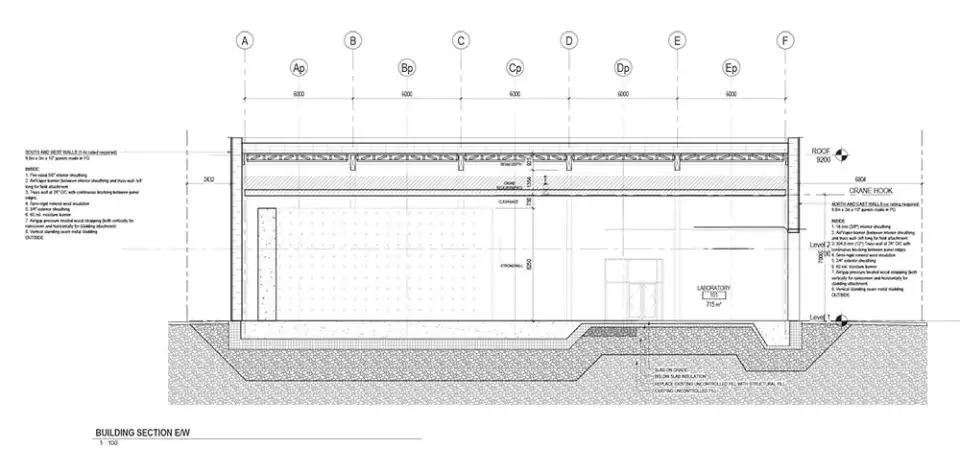
Wood dust is an unavoidable by-product of working with wood and can represent a significant health and safety risk if not properly cleaned up, as the dust can be small enough to irritate the respiratory system. Removing it involves moving large volumes of air, leading to unavoidable heat losses. To reduce those heat losses as much as possible, a dust extraction system with a recirculating function was installed. The air is transported out of the building and the dust is removed through a large cyclone filter. Then the air comes back into the building, passes through very large 1-micron pocket filters, and is eventually distributed back into the laboratory. The system can be operated in bypass mode, in which case the exhaust air is not recirculated. This mode is only used when cedar or hardwoods are processed. As the extracted air volume is very large, a door has to be opened to allow for enough airflow. These wood species are rarely used in the laboratory, and a limitation to process them only during the summer months was acceptable to the user and the certification team.
For continuous ventilation the WIRL relies on an HRV with a heat recovery efficiency of 80%. The building’s small heating requirement of only 9.8 W/m² is met using a 35-kW gas-powered furnace, which is roughly the same capacity as a furnace serving a code-compliant single-family house. The heating power needed according to the modeling and the current measuring results suggests that a furnace with a power of 10 kW would have been sufficient, but availability and safety margins made the builder opt for the installed system. The expected energy costs for the heating system are around $1,000 per year, leading to expected savings on energy costs alone of more than $10,000 per year. For an incremental increase in the operating budget, the natural gas will be replaced by renewable biogas, which will reduce the already very low emissions associated with the building heating by another few percent to about 10% compared to a code- compliant building. The heat is distributed using in-floor radiant heating with a highly efficient, low flow temperature of approximately 22°C.
Heating energy |
Cooling energy |
Total source energy |
Peak cooling load |
Air leakage |
---|---|---|---|---|
3.8 kBtu/ft²/yr |
36.8 |
8 3.2 Btu/hr/ft² |
0.3 |
0.1 ACH50 |
1.1 kWh/ft²/yr |
10.8 |
10.9 Watts/ft² |
0.1 |
|
12.0 kWh/m²a |
116.0 |
10.0 Watts/m² |
1.0 |
Image courtesy of Bree-Ann Orser