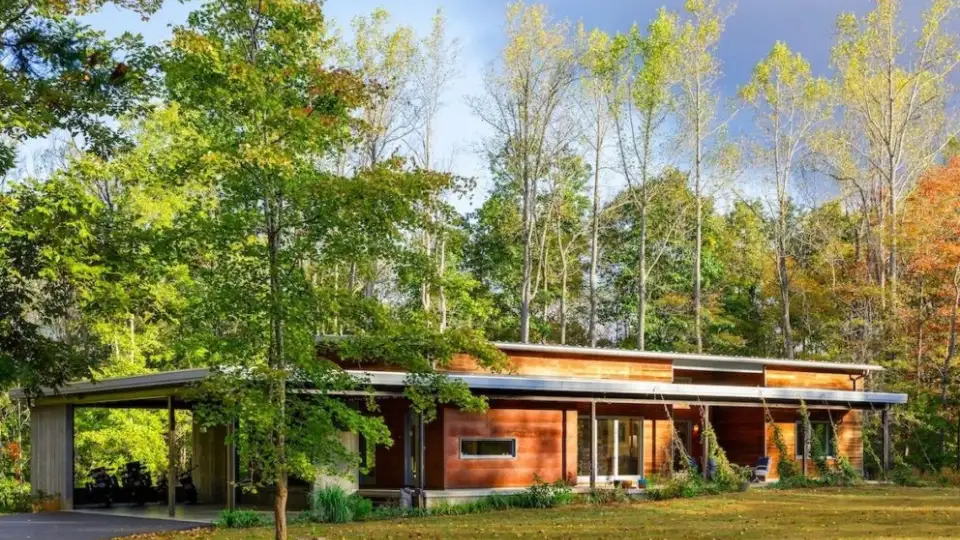
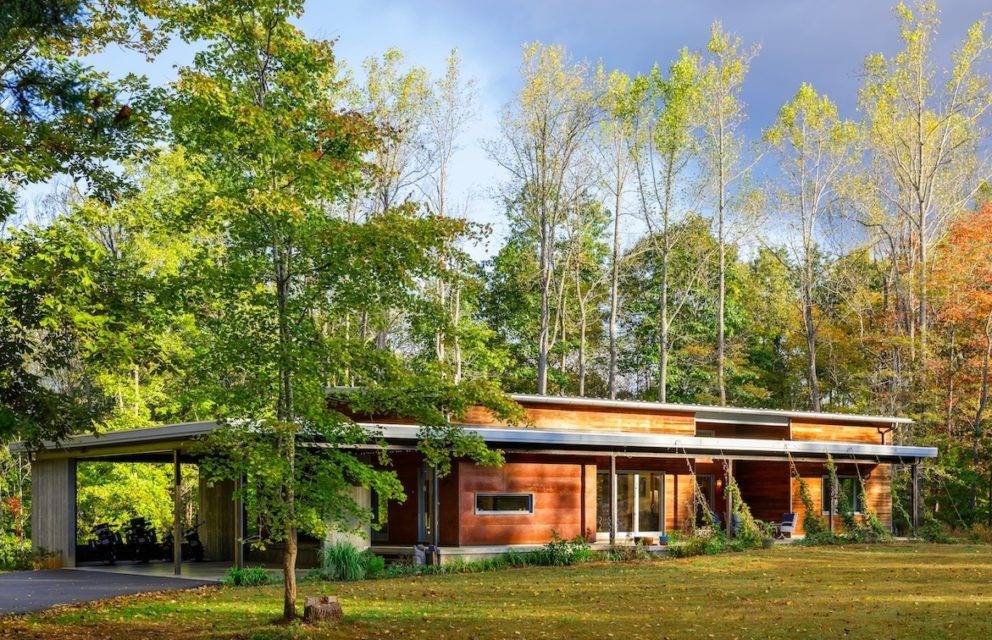
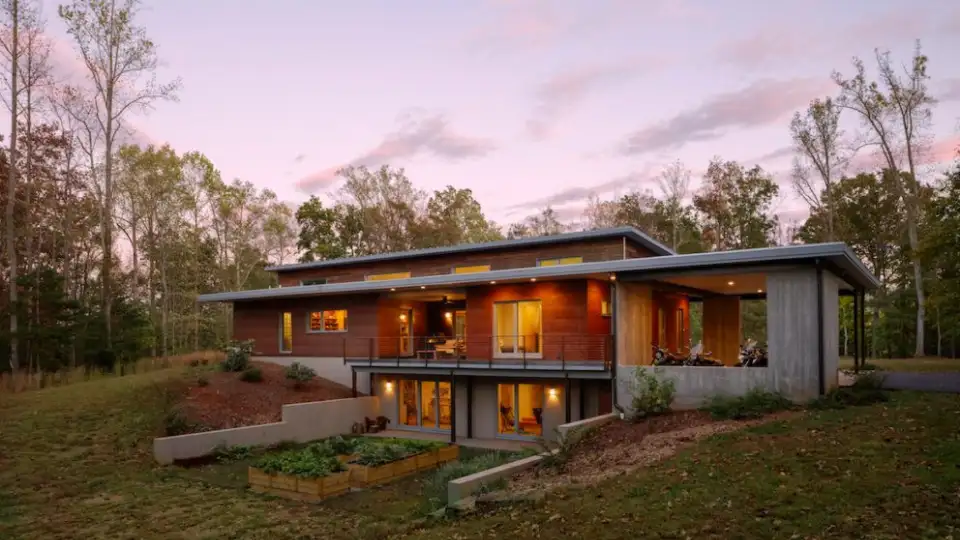
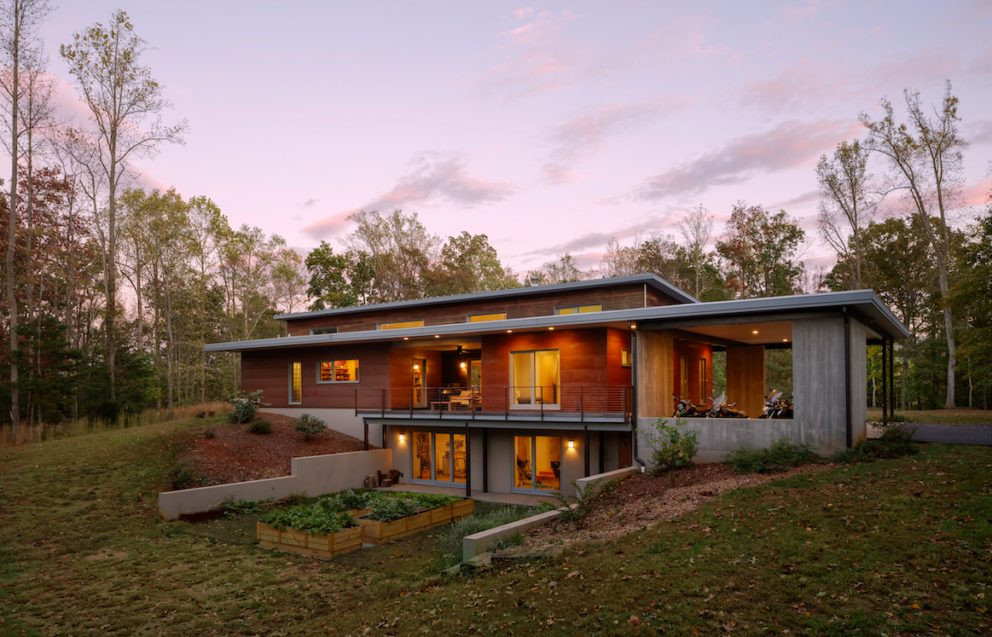
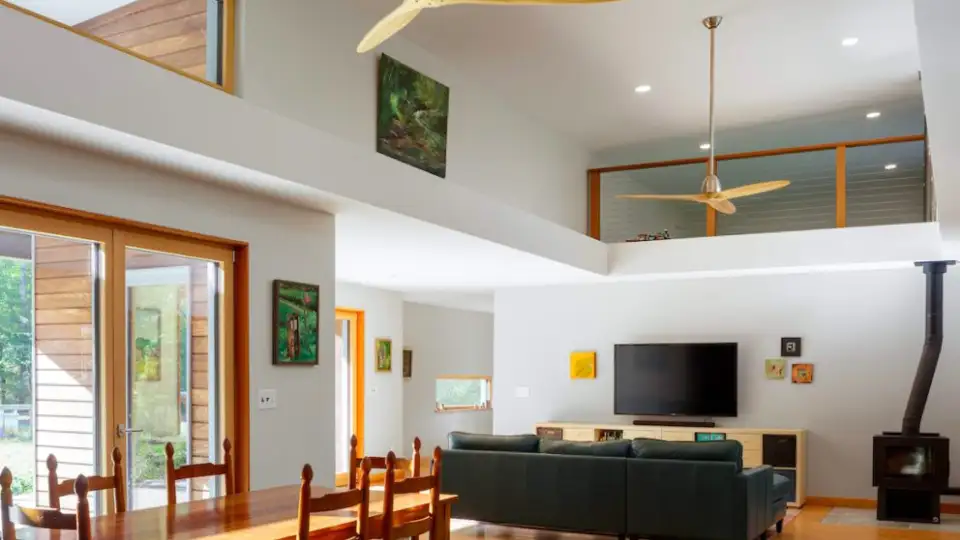
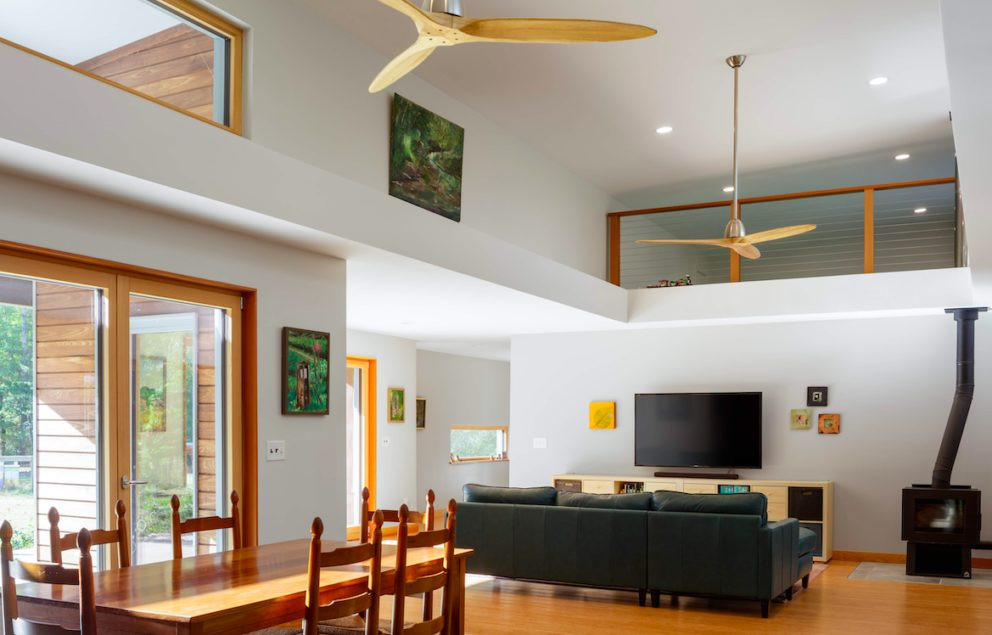
Completed in 2016, the architecture of the Batesville residence was inspired by the client’s love for Frank Lloyd Wright’s Usonian houses, and their wish for a contemporary design that integrated energy-efficiency and sustainable materials with warmth, sensually interesting textures, and variety in spatial experiences. The completed home provides all of the above, coupled with great indoor-outdoor connections and views to the surrounding Virginia Piedmont and Blue Ridge Mountains.
Through multiple design, energy-modeling, and budget iterations, it became clear that the clients' priority in respect to energy was to achieve a net-zero or even net-positive energy standard but to forgo full Passive House certification. Therefore, in team with our builder, we settled on a building envelope that is well-insulated, vapor-open and air-tight, but relatively affordable with about 1/3 less in average R-value than would have been needed to meet PHIUS+2015 heating demand criteria.
Beyond the envelope, the architecture integrates basic principles of energy-efficient and sustainable design: overhangs on three sides provide shading in the summer and protection from weather, large openings in the south allow for passive solar heat gains in the winter, and low and high openings in the north provide for passive cooling and glare-free daylight while supporting cross-ventilation. Additionally, insulated, exposed concrete floors in the basement and in the slab-on-grade portion of the house serve as thermal mass to help cool in the summer and to store the warmth of daytime sun in the winter.
These passive measures are complemented by an active system consisting of a 7.2kWp photovoltaic array that feeds the grid if there is an energy surplus. Currently the inverter provides a small amount of power--enough to keep the refrigerator running during an outage--but the clients plan to install lithium-ion batteries in the near future to allow for a larger load and multiple days of off-grid power supply. Supplemental heating and cooling is provided by two 1t ducted mini-split heat pumps and a wood-stove with direct air-supply and a sealed combustion chamber.
MATERIALS
Building Envelope Assemblies
Slab-On-Grade: 6” EPS continuous insulation, Polyethylene Vapor Barrier, 6” exposed concrete slab
Basement: Insulated Concrete Foundation - EIFS Stucco, 2.75” Expanded Polystyrene (EPS), 10” Concrete, 2.75” EPS, Drywall
Main Floor: Rustwall Corten Steel or Cambia Wood Thermally Treated Poplar Siding, 0.75” wood batten vent cavity, 2” Roxul Rockboard 80 Mineral Wool Rigid Insulation, Solitex Mento Adhero Weather-Resistive Air-Barrier Membrane/Tescon Vanaa Tape 3/4”, plywood sheathing (primary air-tight-layer), 2x6 Wood Studs - 24” o.c. with densepacked Cellulose Insulation, Drywall
Flat Roof: EPDM Membrane, 4” Polyiscynene Rigid Insulation, Solitex Mento Adhero Weather-Resistive Air-Barrier Membrane 3/4”, Plywood Decking (Air-Barrier), Truss Joists with Dense-Pack Cellulose Insulation, Drywall
Sloped Roof: Galvalume Standing Seam Metal Roof, 3/4” Plywood Decking, 3” Vent Cavity, Solitex Mento Plus Weather-Resistive Air-Barrier and Roofing Membrane, Truss Joists with Dense-Pack Cellulose Insulation, Drywall
PERFORMANCE
Passive Performance, Measured Against the PHIUS+2015 Standard
Airtightness: 0.34 ACH50 / 0.023 ELA50 (PH Cert: <0.6 ACH50 / 0.05 ELA50)
PHPP Annual Heating Demand: 6.48 kBtu/sqft*year (Cert: <4.75)
PHPP Annual Sensible Cooling Demand: 0.21 kBtu/sqft*year (Cert: <4.75)
PHPP Primary Energy Demand: 22.2 kBtu/sqft*year (Cert: <38)
Envelope Assembly R-Values: Basement Slab-On-Grade R26, Basement Walls R24, Exterior Stud Walls R28, Flat Roof R56, Sloped Roof R54
Window & Door R-Values: Zola ThermoClad European Frames R7, Triple Pane Glazing, SHGC 0.50 R11
Active Performance
Manual J: Peak Heating Load 20996 Btu, Peak Cooling Load (sensible) 18859 Btu, Peak Cooling Load (latent) 1791 Btu
HVAC: 2 slim duct Mitsubishi Minisplits, 12000 Btu / SEER 20 Heat Pumps, RenewAire EV90P ERV, Wood Stove with direct air-supply, PE Geospring Heat Pump Hot Water Heater
Electric Energy: PV Array - 7,200 watts SolarWorld (made in USA) 300 Watt Mono-Crystalline Panels, Inverter - SMA 6000 Watt inverter with 2000 watt batteryless backup
Statistics After Two Years of Continuous Occupation
The residence achieves 19,435 kWh total production from PV system - 14,991 kWh used on site and 4,444 kWh excess production sent to the grid
The average annual energy use over the first 2 years is
7,500kWh/year (not accounting for light woodstove use), an extremely low number for a luxury3,000 sf houseEnergy Use Intensity (EUI) is ~8.5kBtu/sf - 73% less than the Architecture 2030 Challenge baseline EUI for detached, single family homes
The PV system has produced about 30% more energy than has been used on site, resulting in a house that in fact meets a positive net-energy standard.
AWARDS
In 2018, the Batesville Net-Zero Residence was awarded a First Place Leadership Award in the Residential category by the Virginia Energy Efficiency Council.
TEAM AND TRADES
Architecture & Passive House Energy Consulting: bg design & consulting, Charlottesville, VA (now Gehrung + Graham)
General Contractor & Daniel Ernst, Promethean Homes, Steeles Tavern, VA,
Energy Rating & HVAC Specs: John Semmelhack, Think Little, Charlottesville, VA
Site Work: Arnold Excavation and Hauling, Batesville, VA
Concrete Flatwork: Manny Herring, Scottsville, VA
Cavity Insulation: Weatherseal Insulation Company, Charlottesville, VA
Electric Installation: Dave Brooks Electric, Mint Spring, VA,
HVAC Installation: Charlottesville Heating & Air, Scottsville, VA
Plumbing: Hord's Plumbing and Backhoe, Ruckersville, VA,
Roofing: Martin Roofing, Charlottesville, VA
PV System Design & Installation: Randall Peltola, Genesis Home & Energy, Waynesboro, VA
Manufacturer(s)
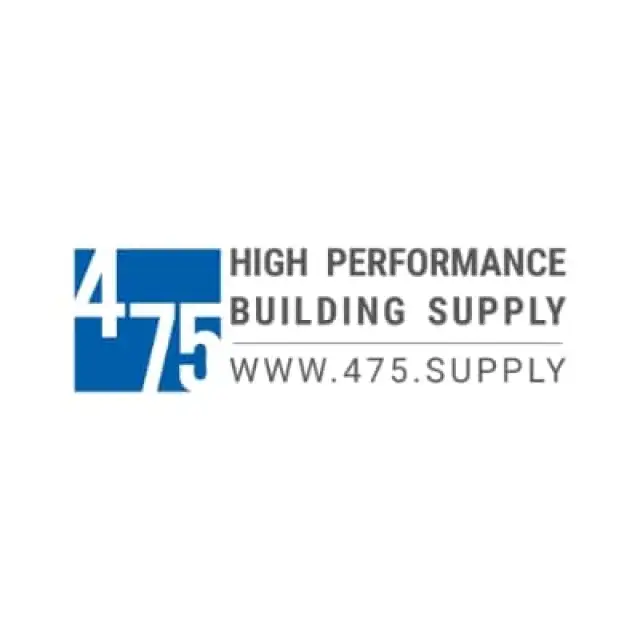
475 High Performance Building Supply
475 High Performance Building Supply is a Passive House supplier and educator. Selling Passive House essentials like air-sealing tape and more for low energy building.
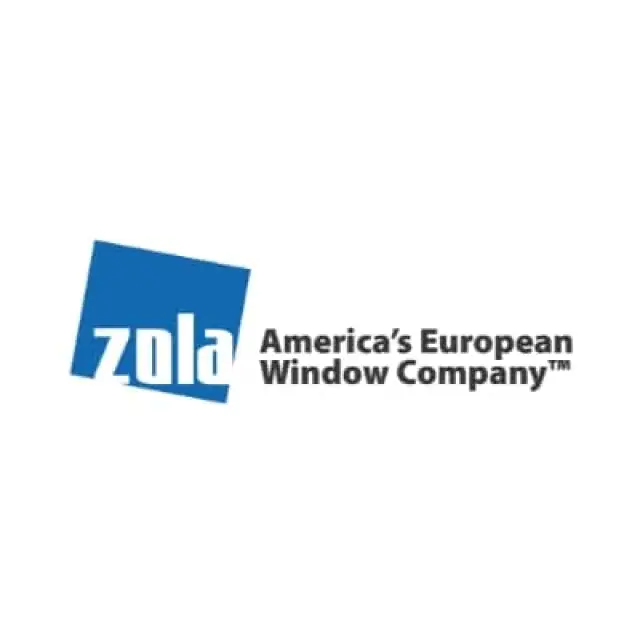
Zola Windows
Zola provides European manufactured, high-performance windows & doors for North American Passive House buildings.
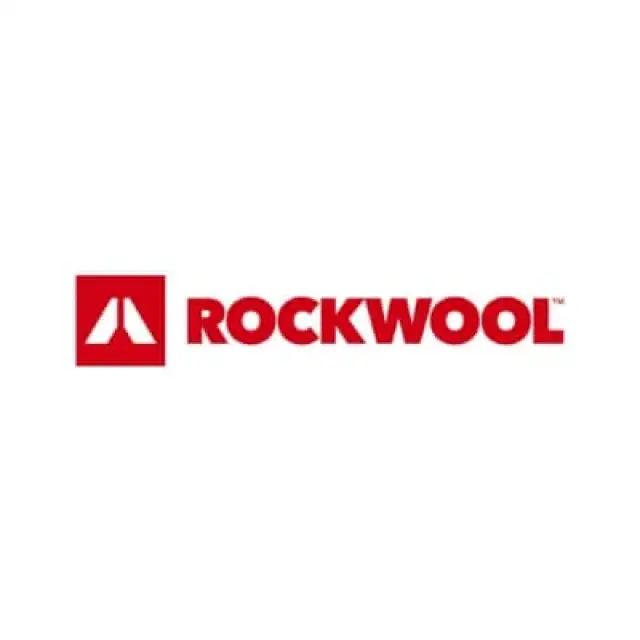
ROCKWOOL
Rockwool offers a full range of high-performing and sustainable insulation products for the construction industry and Passive House.